Вступ
Вид материала | Документы |
- Вступ, 323.48kb.
- Програма дисципліни кредитний модуль " основи радіоелектроніки" (для груп фф) Вступ, 153.44kb.
- Питания з Програми з курсу «Механіка», що виноситься на зм 1 вступ, 86.8kb.
- Робоча навчальна програма здисципліни: Принципи І методи аналізу художнього твору Спеціальність, 222.75kb.
- План, вступ, викладення змісту теми (як правило, 2 глави), висновок, а також список, 24.79kb.
- Вступ України до Світової огранізації торгівлі. Законодавчі зміни. Галузеві стратегії”, 72.41kb.
- Робоча навчальна програма Модуля Вступ до спеціальності Для студентів спеціальності, 404.17kb.
- Вступ до історії україни 5-й клас (35 годин), 86.86kb.
- Вступ до історії україни 5-й клас (35 годин), 104.36kb.
- М. В. Ломоносов; [вступ ст., сост., примеч. А. А. Морозова]. Ленинград : Сов писатель,, 249.18kb.
Технологічний процес добування шламу селену у виробництві сірчане кислоти зображено на мал. 19.
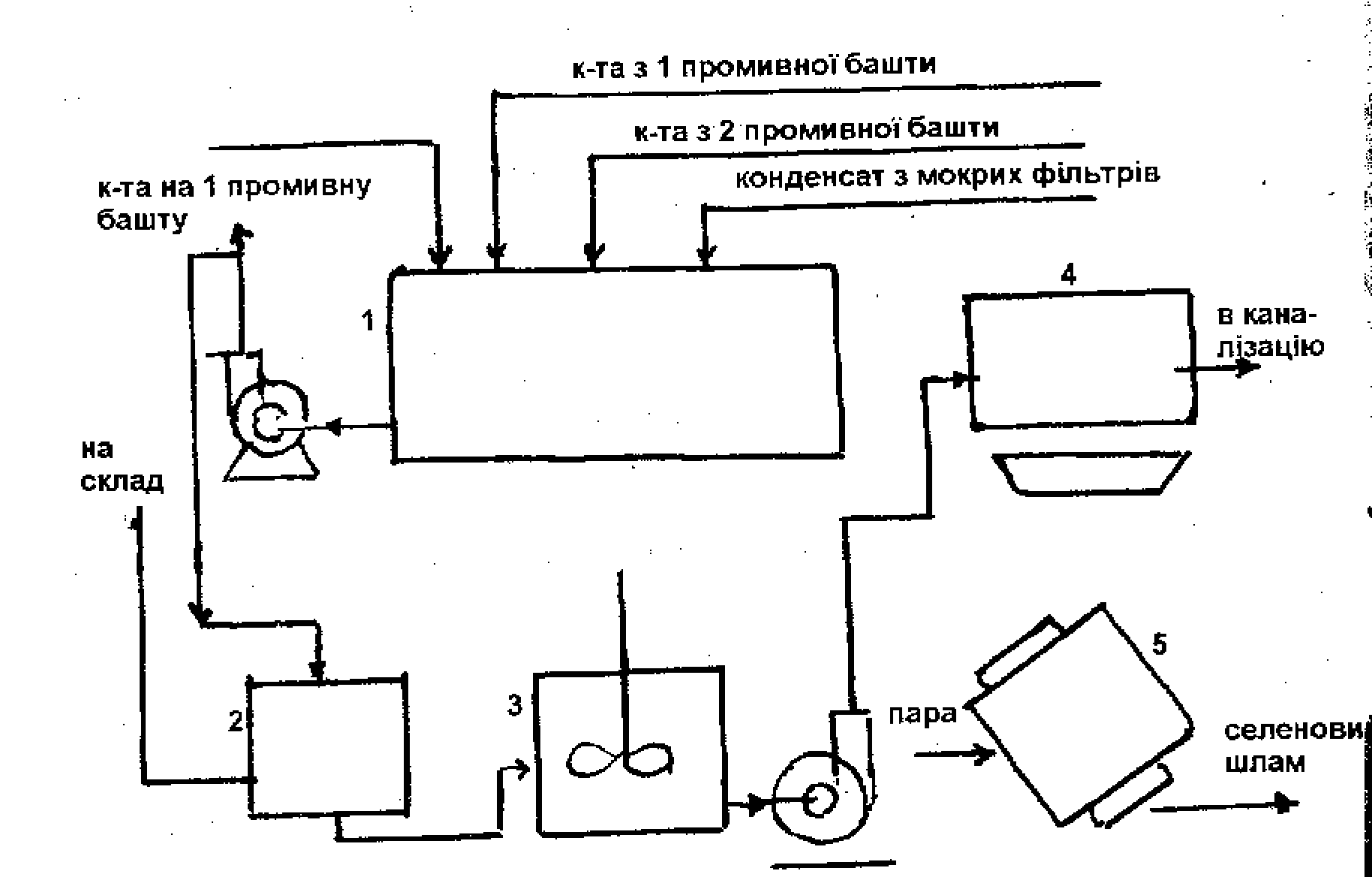
Мал. 19. Схема процесу добування селену у виробництві сірчаної кислоти
1 — збірник кислоти; 2 — фільтр; 3 — змішувач 4 — фільтрпрес для шламу; 5 — сушильня.
6.6. Використання відходів при переробці фосфатів: фо» сфогіпсу і фтористих сполук.
Виробництво екстракційної фосфорної кислоти складається з дозування фосфатної сировини і сірчаної кислоти; розкладу фосфатів сумішшю сірчаної і ортофосфорною кислотами (екстракція); охолодження пульпи; адсорбції вторинних газів і концентрації (упарювання) фосфорної киcлоти. При цих операціях утворюється багато відходів у вигляді фосфогіпсу. Встановлено, що при отриманні 1 т ортофосфорної кислоти утворюється до 5,6 т фосфогіпсу. Він містить до 94% сірчанокислого кальцію і зараз не використовується, але може застосовуватися для гіпсування солончакових грунтів, виробництва портландцементу, як замінник гіпсу, при отриманні вапна сірчаної кислоти.
На мал. 20 зображена принципова схема переробки фосфогіпсу. Від ділення і промивання фосфогіпсу проводять на стрічкових конвейєрно- лоткових і карусельних вакуум-фільтрах.
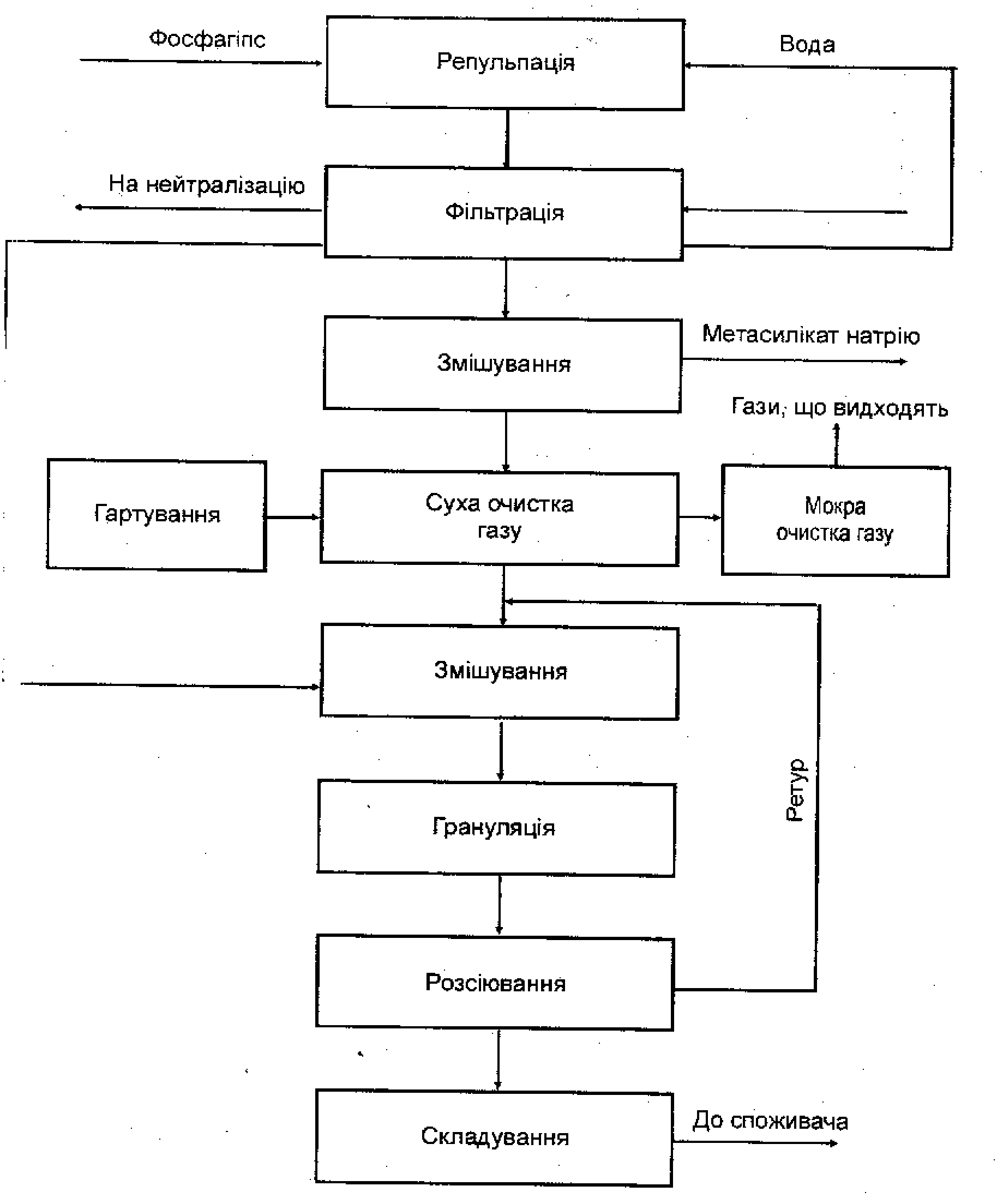
Мал. 20. Схема переробки фосфогіпсу
В деяких випадках відмитий від фосфорної кислоти фосфогіпс використовують для отримання інших в'яжучих речовин, крім цементу, вироблення різних будівельних деталей. Є спроби отримувати з нього сульфат амонію і вапно.
Процес переробки фосфогіпсу полягає в тому, що фосфогіпс з карусельного фільтру надходить на репульпацію при відношенні твердої фази до рідкої 1:3, а потім гідротранспортером подається в приймач фосфогіпсу цеху грануляції і сушіння. Пульпу фільтрують на барабанних вакуум-фільтрах. Фільтрат частково повертається на репульпацію, а частково на нейтралізацію. Для підживлення системи гідротранспорту використовують конденсат з відділення випаровування. Далі фосфогіпс змішують з розчином метасилікату натрію і направляють в обертову піч для дегідратації:

Остання стадія до безводного гіпсу проходить при температурі 9000С. Більша частина відхідних газів являє собою пари води і 55% продукту, який осідає в циклонах і абсорберах.
Дегідратований фосфогіпс змішують з вологим продуктом, фільтрують і надають на грануляцію, а потім розсівають на фракції 3-50 мм і менше. Остання фракція у вигляді ретура надходить на стадію змішування, а перша-на склад готової продукція для споживання.
Встановлено, що використання фосфогіпсу в якості мінералізатора в процесі випалювання клінкера замість природного гіпсу економить 1,95 крб. на 1 т(в цінах 1989р).
Стічні води спочатку нейтралізують вапняковим молоком і коагулюють за допомогою полі акриламіду. В шламі, який при цьому утворюється, вміщується вже 10-15% фосфорного ангідриду і 8-10% фтору.
Стічні води фосфорних підприємств вміщують фосфорний, ангідрид, фтористі сполуки у вигляді кремнефтористоводневої кислоти.
Стічні води мають такий склад, мг/л: фосфорного ангідриду 8000; солей заліза 4880; кремнезему 3400, Водневий показник або РН 1,2.
Шлам обробляють сумішшю фосфорної і сірчаної кислот протягом 1 г при температурі 50°С і фільтрують. Пульпа обробляється газоподібним аміаком до РН 4-4,5; змішується з хлоридом калію, карбамідом. До суміші додають розчин-ретур і масу гранулюють. Процес закінчується сушінням продукту при 70-100°С. В результаті амонізації фосфорна кислота (з ангідриду) перетворюється в солі - моно-, діамонійфосфат, а сірчана кислота -в сульфат амонію.
Склад продукту, %: фосфорного ангідриду 9-13; азоту 3-4; вологи 20-35. '
Збір фтористих з'єднань і їх переробка. Фтористі з'єднання утворюються при переробці природних фосфатів, які містять фтор, і отриманні фосфорних добрив. Так, при отриманні суперфосфату біля 40% вміщеного в природних фосфатах фтору виділяється в газову фазу у вигляді фтористого водню і туманоподібної кремнефтористоводневої кислоти, де їх концентрація сягає 15-35 г/м3. Ці гази надходять в адсорбційну установку для вловлювання з них фтору. При сушінні гранульованого суперфосфату також виділяється фтор (10-17%), який залишився в продукті. Ступінь виділення фтористих сполук зростає з піднесенням температури сушіння і її довготривалості.
При екстракції фосфорної кислоти в ній залишається 78-80% фтору, що вноситься з сировиною-апатитом; 15-17% його переходить в фосфогіпс, а з газами вилучається лише 3-5% фтору. При випаровуванні екстракційної фосфорної кислоти в газову фазу виділяється 80-90% вміщеного в ній фтору.
При виробництві подвійного суперфосфату камерним способом з суміші виділяється 1-3% фтору, а при сушінні подвійного суперфосфату, що отримується поточним способом, виділяється 50-60% фтору від загального його складу у вихідних фосфатах і фосфорній кислоті.
При гідротермічному обезфторюванні природних фосфатів фтор виділяється з них майже повністю (на 93-97%).
Газ, який надходить на адсорбцію з апаратів виробництва простого суперфосфату, повинен мати температуру не нижче 65°С, бо при більш низькій температурі чотирифтористий кремній гідролізується вологою, що знаходиться в газі, згідно з рівнянням:

Виділяється гелеподібна кремнієва кислота, яка буде осідати в газоходах у вигляді шламу. А це приведе до частої очистки газоходів і простою обладнання. Водяна абсорбція фтористих газів практично зводиться до поглинання туманоподібної кремнефтористоводневої кислоти, що утворилась в результаті гідролізу чотирифтористого кремнію.
Газ спочатку промивають в механічних абсорберах-камерах з розбризкуючими валками, де вловлюється 80-90% фтору, потім в порожніх баштах, які зрошуються водою, де поглинається решта частин фтористих з'єднань.
Зовнішні габарити башти-камери: довжина 10-18 м, висота 5-6 м і ширина 1,5-2,0 м. Об'єм 36 м3. Башта в середині розділена перегородками на відділення, через котрі газ послідовно проходить і промивається рідиною, яка розпилюється дрібними бризками за допомогою розпилювача, що обертається. Газ для кращого вловлювання кремнефтористоводневої кислоти пропускають через кілька абсорберів (2-3), що працюють з протиточною схемою зрошення. З першого абсорбера витікає кислота, що вміщує 8-10% вилученого продукту. Об'єм абсорбційної системи визначається продуктивністю суперфосфатного заводу з розрахунку 0,5 м3 на 1 т суперфосфату в годину.
Ступінь вловлювання кремнефтористоводневої кислоти сягає 98-99%. Вихідні з абсорбційної установки гази вміщують 0,1-0,2 г/м2 фтору ,і викидаються в атмосферу.
На суперфосфатних заводах на кожну тонну суперфосфату вентилятор повинен відсмоктувати 250-300 м3 фтористих газів.
Далі кремнефтористоводневу кислоту обробляють водним розчином хлористого натрію в сталевих реакторах з мішалками, футерованими гумою, і отримують кремнефтористий натрій. Він використовується як інсектицид або дефоліант. Хлористий натрій беруть в надлишку згідно з реакцією:

Кристали кремнефтористоводневого натрію відділяються від маточного розчину і гелю кремнієвої кислоти відстоюванням на протязі 30 хв. Так як швидкість осідання кремнефтористоводневого натрію в 10 разів більша за швидкість осідання гелю кремнієвої кислоти, то це дозволяє їх відділити один від одного. Кристали першої солі відфуговують, промивають в гумовій центрифузі від хлористого натрію і хлороводню, а потім висушують до вологості в 1%.
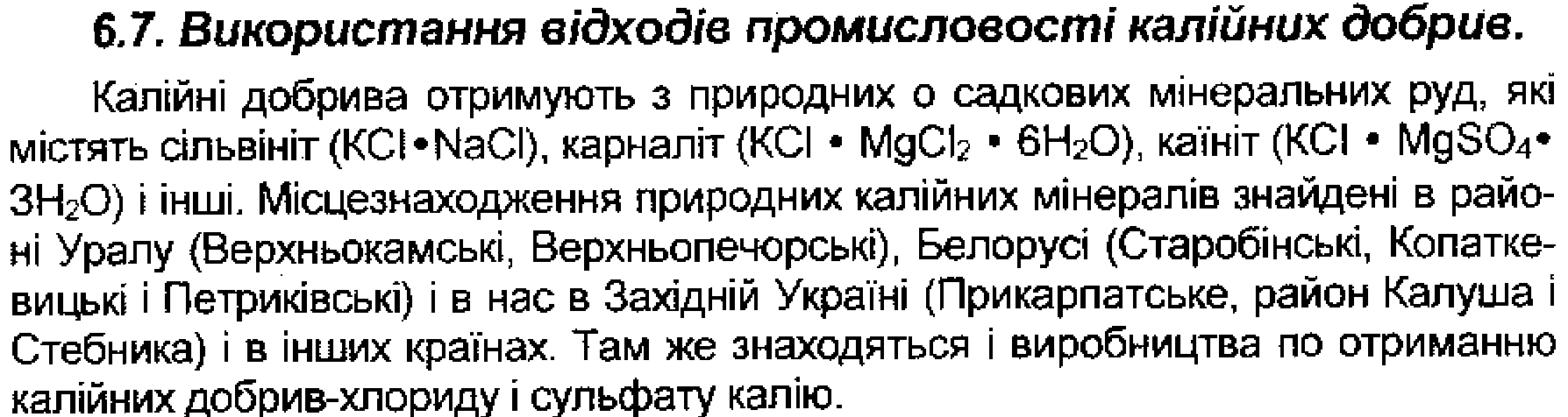
Існує три технології отримання хлориду калію: флотаційний або термомеханічний, галургічний, який заснований на різній розчинності і подальшій кристалізації хлористих солей калію і натрію, і комбінований, який поєднує два перших. При переробці і збагаченні сировини в калійній промисловості кожного року утворюються сотні тисяч тонн галітових відходів, які містять хлористий натрій і мільйони тонн глинисто-солевих шлаків, що складаються із хлористого натрію (91%), хлористого калію (1,7%). глинистого залишку, вологи (6%), а також невеликої частини солей кальцію і магнію. Тому на калійних підприємствах впроваджують методи комплексного використання сировини: одержання разом з калійними солями розсолів для виробництва харчового хлористого натрію, кормового хлористого натрію, сульфату нагрію, а також сировини для виробництва магнію і деяких інших речовин.
Значна частина галітових і глинисто-солевих шламів повертається в калійні виробки на заповнення відпрацьованих камер або порожніх просторів (пустот).
"Хвости" після проведення основної флотації направляються в згущувач. Шлам, який відбирається із згущувача і містить 2,5-1,7% хлористого калію, відфільтровують на барабанному вакуум-фільтрі, змішують з іншими шламами та перекачують у відвали.
Маточний розчин із центрифуг, згущувача і фільтра повертається у виробництво.
6.8. Виробництво сірчистого газу з відпрацьованої сірчаної кислоти.
Апаратура, що застосовується для цього технологічного процесу, зображена на мал. 21. Вона складається з реактора 2, конденсатора сірки 6, вентилів для регулювання тиску 12. 12а, сушильної башти 13, колони 16 для вилучення сірчистого газу зі зворотним холодильником 19, додаткового реактора 21, циркуляційного насоса 22, нагрівача сірки 24, пальника для спалювання сірки 28, а також відповідних трубопроводів і додаткового обладнання.
Реактор 2 - закрита посудина з мішалкою і внутрішніми перегородками, яка вміщує розплавлену сірку при температурі 370°С.
Відпрацьована сірчана кислота з процесу алкилювання органічних сполук або з інших виробництв подається в реактор 2 по лінії 1, туди ж подається вода і розплавлена сірка при тиску 0,7 МПа. При цих умовах сірчана кислота розкладається, виділяючи сірчистий газ, вуглець з органічних сполук, які попадають в реактор з відпрацьованою сірчаною кислотою
і водою.
Гази з реактора 2 по лінії 4 потрапляють в конденсатор сірки 5 -трубчатий теплообмінник. Газовий потік охолоджується до 140°С, і сірка конденсується. Її відділяють від газового потоку в сепараторі 6, після чого повертають в реактор 2 по лінії 7.
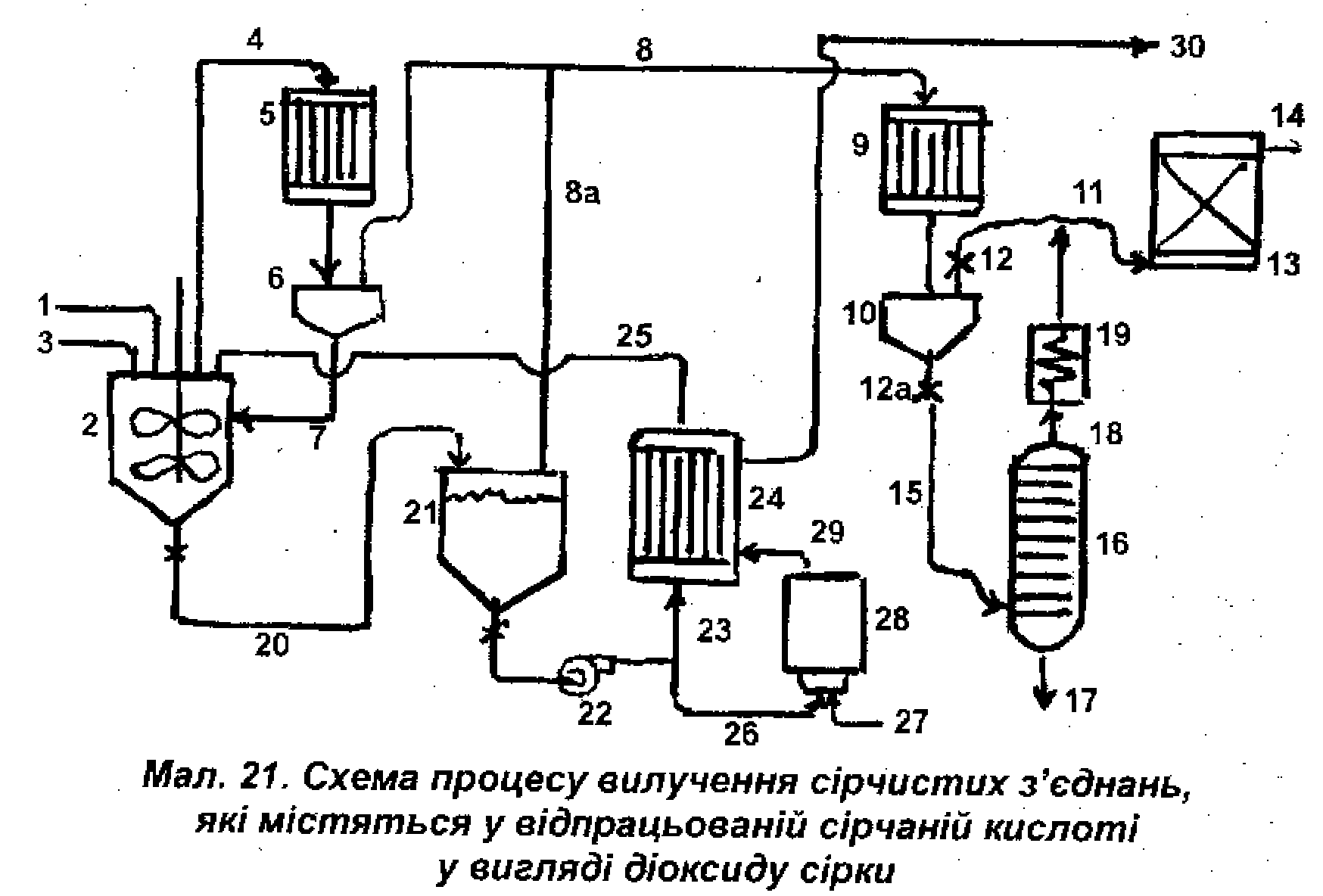
Сепаратор-порожня посудина, з нижньої частини якої. виводиться сірка, а газ виходить зверху і по лінії 8 потрапляє у водяний конденсатор і де охолоджується до 35°С. Вода конденсується разом з сірчистим газом.
Цю суміш з конденсатора 9 подають в сепаратор 10, де відбувається розділення рідкої і газової фракцій. Газова фракція виводиться з сепаратора 10 через вентиль 12. З нею виходять оксиди вуглецю і водяна пара. Цю фракцію обезволожують в башті 13 зрошуванням концентрованою сірчаною кислотою, а потім виводять з системи по лінії 14. Воду із сепаратора 10 виводять через вентиль 12 а і по лінії 15 подають в колону 16 для вилучення сірчистого газу. Колона з'єднана лінією 18 зі зворотним холодильником 19. Після відділення сірчистого газу воду з колони 16 по лінії 1| скидають в каналізацію.
Розплавлена сірка безперервно виводиться з реактора 2 по лінії 20 додатковий реактор 21. Сірка в реакторі 21 знаходиться 2 години. Сірчистий газ, що утворився в реакторі 21, по лінії 8а потрапляє в лінію 8, де змішується з потоком газу, що виходить з реактора 2 у водяний конденсатор 9. Сірка з реактора 21 виводиться за допомогою циркуляційного насоса 22. Далі маса сірки поділяється на два потоки. Перший по лінії 23 подають в нагрівач сірки 24-трубчастий теплообмінник, де сірка нагрівається розжареними газами. Вони утворюються при згорянні сірки в пальнику 28 до температури 425°С, а потім повертаються в реактор 2 по лінії 25. Другий потік сірки по лінії 26 подають до пальника 28, де відбувається згорання сірки в струмені повітря, який поступає по лінії 27.
В продуктах згоряння міститься сірчистий газ, який по лінії 29 поступає в теплообмінник 24, де він використовується для нагрівання сірки.
Газ із теплообмінника по лінії 30 виходить і використовується як сировина для виробництва сірчаної кислоти.
6.9. Добрива з відпрацьованої сірчаної кислоти.
Процес одержання добрив з відпрацьованої сірчаної кислоти розроблений С.Д.Шарле (Пат. США 3888653, 10 червня 1975, Фірма "Шамрак Кемікал ліміт", Канада). Апаратура складається з великої опалювальної печі довжиною 10 м, діаметром 180 см, що обертається, гранулятора і ротаційного холодильника, Вода, відпрацьована сірчана кислота та хлористий калій подаються в піч, яка обігрівається природним газом 12,5-І 17,ОкДж/кг. В печі утворюється сульфат калію, який потрапляє в гранулятор. Газоподібний хлористий водень виходить з печі на очищення.
Добриво являє собою сухий дрібнокристалічний порошок. Порошок і грануляторі змішується з водою, гранулюючим агентом і проводить процес грануляції по відомій технології. Гранули вивантажуються із гранулятора розмірами 6-10 меш. Вони вміщують вологу, тому їх пропускают через барабанну сушарку і охолоджують в обертальному барабані. Після цього гранульоване добриво подається в спеціальну ємкість. Відкіля добриво відправляють як готову продукцію.
6.10. Утилізація тепла при виробництві сірчаної кислоти.
Нагріте повітря, що виходить з валів мішалок механічних печей для згоряння колчедану, використовують для опалення приміщень, підігрівання води і інших господарських потреб, а також для отримання пари в котлах-утилізаторах.
В печах "киплячого шару" отримують більше 1 т пари на 1 т виробленої кислоти. В той же час на 1 т виробленої кислоти потрібно 50-100 кВт/г і електроенергії.
Використовуючи енергію пари в парових турбінах можна значно знизити витратний коефіцієнт електроенергії, а також відповідно знизити собівартість сірчаної кислоти.
Нижче в таблиці 16 наведена кількість теплоти, що виділяється при і отриманні 1 т сірчаної кислоти в МДж/Мкал.
Таблиця 16
Кількість тепла, що виділяється при одержанні сірчаної кислоти МДж/Мкал.
Розділ 6. Технології переробки і використання від ходів промисловості полімерних матеріалів
6.1. Загальна характеристика полімерних відходів.
Особливістю відходів полімерних матеріалів є те, що вони не підлягають природним процесам очищення - гниттю, вивітрюванню, окисленню, розчиненню у воді, а також природному розкладу. Тому примусове знищення їх проводиться за допомогою згоряння, затоплення або захоронення, але всі ці способи ведуть до забруднення довкілля і тому не допустимі.
Найкращий спосіб їх використання - застосування як додаткового джерела сировини. Полімерні відходи можна брикетувати з в'яжучими речовинами і у вигляді блоків осушувати територію біля моря, як це робиться у Японії для отримання додаткової земельної площі.
Технологічний процес використання полімерних матеріалів в якості додаткової сировини включає наступні операції: подрібнення, сепарації по розмірах і дозування, як додаток до основної синтетичної смоли.
Важливою ланкою в цьому процесі є ідентифікація полімерного відходу, яка проводиться по визначенню щільності, розчинності, характеру горіння, запаху від полум'я та інших ознаках.
Нижче наводиться методика визначення відходів полімерних матеріалів за характером горіння.
6.2. Методика якісного визначення полімерних відходів за характером горіння.
Смужкою або шматочком досліджуваного полімеру доторкаються до зовнішньої сторони полум'я горілки чи спиртівки. Якщо речовина легко загоряється, то вона швидко забирається від полум'я. Якщо вона плавиться і скручується, тоді її продовжують тримати в полум'ї до згоряння. При цьому визначають запах, який виникає при горінні, користуючись наступними ознаками:
1. Якщо пластмаса, або полімер, не загоряються, зберігають свою форму, але виділяється запах формаліну, який роз'їдає очі, то матеріал являє собою фенолформальдегідну або фенолкарбамідну основу.
2. Якщо при загорянні відчувається запах фенолу, то досліджуваний зразок фенолформальдегідна смола.
3. Якщо при загорянні відчувається запах паленої гуми і з'являється зелена смужка, перекрита жовтим кольором, то це - неопреновий каучук або хлоропрен.
4. Якщо матеріал не загоряється, і відчувається риб'ячий запах, то полімер - меламіноформальдегідна смола.
5. Якщо при горінні речовини відчувається солодкуватий запах і є залишки чорної сажі, то це - хлористий вініліден.
6. Якщо при горінні відчувається різкий запах, але непаленої гуми, то це - хлористий вініл або полівінілхлорид.
7. Якщо при горінні відчувається запах підгорілого молока, то речовина являє собою казеїн.
8. Якщо при горінні відчувається запах оцтової кислоти, то полімер-ацетил целюлоза.
9. Якщо речовина продовжує горіти при її витягуванні із полум'я і відчувається запах камфори., то це – целулоїд.
10. Якщо відсутній запах камфори, але речовина активно горить і навіть спалахує, то це може бути нітроцелюлоза або піроксилін.
11 .Якщо при горінні спостерігається голубувате полум'я з білою верхівкою і солодкуватим квітковим запахом, то це може бути поліметакрилат.
12. Якщо відчувається запах зіпсутих овочів з голубуватим кольором полум'я, а речовина розчиняється в соляній кислоті, то це - нейлон.
13. Якщо від полум'я відчувається запах пригорілої олії або сиру і виділяються іскри, то це - бутилцелюлоза.
14. Якщо горіння тихе, спокійне, не утворюються іскри, то це – полівінілбутираль.
15. Якщо полум'я не яскраво-червоного кольору у вигляді кайми, утворюються іскри і відчувається запах кислоти, то це - полівінілзцеталь.
16. Якщо полум'я має яскраво жовто-білий колір і відчувається запах масляної кислоти, то це - ацетобутиратцелюлози.
17. Якщо запах полум'я солодкуватий квітковий, а полум'я коптить, то це - полістирол.
18- Якщо полум'я має запах горілого паперу, то дослідна речовина -целюлоза.
19. Якщо при горінні речовини утворюється полум'я, обмежене жовто-зеленою крихтою, крихта дає іскри і запах оцту, горить погано, плавиться, і частинки, падаючи у воду, утворюють чорно-коричневі зерна, то ця речовина - ацетилцелюлоза.
20. Якщо речовина горить легко, утворюючи солодкуватий запах, при плавленні шматочки, падаючи у воду, утворюють плоскі диски коричневого кольору, то цей полімер - етилцелюлоза.
7.3. Переробка відходів полімеризаційних полімерів.
Ці відходи одержуються із синтетичних смол або полімерів, які отримуються шляхом полімеризації, тобто за рахунок розкриття подвійних або потрійних зв'язків. До них відносяться аналоги поліетилену, полістиролу, полівінілхлориду і т.п.
Поліетилен у вигляді зношеної плівки сільськогосподарського застосування, пакети, мішки, сумки і залишки інших виробів переробляються на підприємствах Держпостачу колишнього СРСР в Кишиневі, Кемерові, Ташкенті, Пензі, Вузловій (станція Південно-Східної залізниці), Києві, де працюють лінії для отримання агломератів або гранул з цих відходів.
Технологічний процес отримання цього грануляту (або агломерату) складається з наступних операцій: транспортування відходів під ножиці на ланцюговому транспортері і подавання їх в миючу, ріжучу машину: завантаження січки віходів на вібросито для промивання водним розчином; флотації січки для відділення забруднень, які мають щільність більше 1 г/см3; відсмоктування січки з поверхні ванни і подавання її на вібросито і пароповітряну сушарку, а потім в бункер-накоплювач і завантаження січки і агломератор.
Продуктивність установки 500 кг січки за годину. Агломерат має насипну масу 0,35-0,40 кг/дм3, розмір частинок - до 8 мм (80%). Процес показаний на мал. 22.
Обладнання і технологія виробництва грануляту із полімеризаційних відходів складається з завантаження сировини в контейнер скіповим підйомником, який подає контейнер на приймальний стіл 2. Сировина завантажується вручну в бак агломератора 3, де проходить безперервний цикл послідовної різки, промивання, сушіння агломерації.
Сировина далі пневмотранспортером подасться в бункер-змішувач 4, і потім в заглиблення екструдера 5. З екструдера відходи полімерів виходить у вигляді джгутів і надходять у ванну охолодження 6. Грануляція матеріалу проходить в грануляторі 7, звідки гранулят надходить в бункер-нагромаджувач 8 і упаковується для відправки на завод-виробник деталей.

Мал. 22. Схема технологічної лінїї виробництва полімеризаційного грануляту 1 - сниповий підйомник; 2 - прийомний стіл; 3 - агломератор;
4 - змішувач; 5 - екструдер; 6 - ванна охолодження; 7 - гранулятор;
8 - бункер-нагромаджувач
Час агломерації 15-17 хв. при одногодинному завантаженні в агломератор 65-70 кг сировини.
Насипна маса грануляту 0,4-0,5 кг/дм3 при розмірі гранул 3,5х5 мм.
Лінії переробки полімеризаційних відходів виробляються в м. Кузнецьку Пензенської області заводом "Кузполімермаш".
Вторинний поліетиленовий гранулят використовується у виробництві дренажних труб, плівок для потреб сільського господарства (компостування, теплиць, мульчирування, виготовлення сховищ), литих труб, виробів для сантехніки, електромонтажу, виготовлення транспортної тари у вигляді ящиків для пляшок, фруктів, молока, овочів і таке інше.
Іноді вторинна поліетиленова сировина подрібнюється в крихту на роторних подрібнювачах пластмас типу ІПР-100-ІА (завод-виробник "Кузполімермаш") або на обладнанні італійської фірми "40 ЛМАС-300".
Полі стирольна вторинна сировина застосовується для виготовлення облицювальних листів, товарів широкого вжитку, радіодеталей і т.п. Полістирольна крихта переробляється у вироби звичайними методами, які застосовуються для термопластів - екструзією, литтям під тиском і пневмо-вакуумним формуванням.
Створено дослідно-експериментальне підприємство "Київвторполімер", де із спрацьованої поліолефінової тари, поліетиленової плівки і полівинілхлоридних і інших промислових полімерних відходів випускають нову поліетиленову плівку, труби, комплекти для крапельного зрошення будівельні матеріали, поліхлорвінілову плитку, різну тару тощо. Труби поліетиленову плівку одержують методом екструзії, а різна тара промислового призначення виготовляється з допомогою лиття під тиском. Це один з найпрогресивніших сучасних способів переробки пластмас, який дає змогу формувати вироби в автоматичному режимі. На "Київвторполімері" використання тонни вторинної полімерної сировини дає змогу економити 400 крб. порівняно із застосуванням такої ж кількості первинної сировини, і собівартість виробів значно нижча.
7.4. Використання відходів термореактивних пластмас.
В процесі переробки нагромаджуються значні кількості відходів пресматеріалів у вигляді задирок і лому бракованих виробів, які сягають більше 15% від вихідної сировини. Внаслідок того, що відходи термореактивних матеріалів в процесі переробки втратили здатність до розм'якшення і розчинення використання їх являє важку проблему. Тому відходи підлягають розмелу при температурі не вище 30°С, а потім повертаються у виробництво у вигляді добавок від 6 до 15% до нового прес-порошку.
Використання грубоподрібнених відходів термореактивних пластмас включає можливість одержання високоякісних виробів. При достатньо гінкому подрібненні і рівномірному розподілі молотих відходів в середовищі нового прес-порошку значно підвищується якість продукції із вторинних прес-матеріалів.
Для переробки відходів фенопластів і амінопластів на заводах переробки пластмас застосовуються спеціальні комплексні установки.
Там відходи подрібнюються на зубчастій дробарці і ударно-дисковому млині до частинок менше 3 мм, а потім підлягають подрібненню на вібромлені в замкнутому циклі з повітряною сепарацією крізь вібросито. Із дробарки відходи потрапляють в контейнер, який у верхньому положенні вивантажується крізь завантажену лійку у вібромлин, де подрібнюється, а потім елеватором потрапляють на ситовий сепаратор. Готовий помел поступає в бункер, а "хвости" у вібромлин, звідти через елеватор знову на вібросито.
Отримані порошки являють собою суміш частинок розміром 0,5мм (33,5%), 0,25 мм (21,3%) і менше 0,25 мм (11,4%). їх змішують з свіжими прес порошками у віброкульовому змішувачі, гранулюють і пресують у вироби,
7.5. Утилізація вторинної поліамідної сировини.
Переробка вторинної поліамідної сировини-капрону, нейлону і інших включає наступні операції: нарізку, відмивку, віджим води, сушіння, подрібнення, кінцеве сушіння, гранулювання і вловлювання низькомолекулярних сполук. Виробництво виробів з поліамідних смол проводять литтям під тиском.
Найвищий рівень переробки промислових відходів полімерних вторинних матеріалів був досягнутий у ФРН, де він склав біля 90%.
В деяких зарубіжних країнах після подрібнення і промивання поліамідних залишків їх розплавляють, а потім лише гранулюють.
Іноді переробка змішаних і забруднених полімерних відходів розплавленням проходить без їх попереднього розподілу по видах. При цьому користуються спеціально сконструйованим литим обладнанням, в якому проходить повна пластифікація і гомогенізація всіх видів полімерів.
7.6. Використання вторинних ресурсів гумотехнічних виробів.
Автомобільні і тракторні покришки в процесі експлуатації стають придатними для подальшого використання і йдуть у відходи. Після відновлювального ремонту вони можуть бути направлені для отримання регенерату або для виробництва будівельних та технічних матеріалів, а також використані в шляховому будівництві, для хімічної переробки шляхом піролізу чи спалювання в цементних печах і в котлах електростанцій в якості палива.
Рівень використання зношених покришок в 1985 році в колишньою СРСР складав 30%. До 1995 року цю цифру було намічено довести до 75%, а до 2000 року - до 100%.
Технологічний процес переробки зношених покришок проходить за такими операціями: миття, відділення бортових кілець, грубого подрібнення на шипорізах і дробильних вальцях, попереднє подрібнення на розмолюючих вальцях і дробарках ножевого або дискового типу, вилучення текстильного та металічного корду за допомогою повітряних сепараторів і вібраційних сит, а також за допомогою магнітного сепаратора.
Ще одне подрібнення призначається для отримання гумової крихта Вона йде на одержання гумового регенерату, який має властивості каучук - пластичність і м'якість. Гумовий регенерат отримують водонейтральним термомеханічним і дисперсійним способами. Гумовий регенерат вводять нові гумові суміші.
Виробництво будівельних матеріалів з гумової крихти проводять для покрівельних і гідроізоляційних елементів, які випускаються у вигляді мастик рулонів і плит. Так, мастика "ІЗОЛ" - багатокомпонентна однорідна маса, яка складається з нафтового бітуму 7%, азбесту 7 сорту 15%, гумової крихти 18| інденкумаронової смоли 4%, каніфолі 4% і антисептика 1%.
Температура розм'якшення мастики 100-165°С, а температура стійкості від 70 до 1400С. Гнучкість залишається при температурі від -10 , 15°С. Температура крихкості - 25°С.
Технологічний процес отримання мастики "ІЗОЛ" полягає в тому, що змішувач при температурі 80-90°С подається половина розігрітого до 180°С бітуму марки 4; туди ж вводиться інденкумаронова смола і каніфоль. Все перемішується протягом 10-15 хв.
В одержану суміш вводять гумову крихту і температуру суміші підвищую до 180-200°С. Загальний час приготування суміші складає 1 г 50 хв.
Друга мастика "ІЗОЛ" виробляється без розчинника в гарячому стані розчинником в холодному. Їх розрізняють лише галузі застосування.
Покрівельний матеріал "ІЗОЛ" випускається у вигляді плит і рулонів для плоских покрівель.
Гідроізоляційний матеріал "БРИЗОЛ" застосовується для ізоляції циліндричних металевих поверхонь, які працюють в грунті.
Технологічний процес виготовлення "БРИЗОЛУ" починається з виготовлення гумобітумної суміші . В змішувач через дозатори одночасно додають розплавлений бітум і інші інградієнти - гумову крихту, азбест, пластифікатор і адгезів в кількісному співвідношенні 56:28:15:1 при температурі 1700С Після додатковій гомогенізації на вальцях суміш профілюється в даних геометричних розмірах з використанням каландра з охолодженими валками Маса пропускається через ванну з емульсією антиадгезіонної речовини. Гумові плити для тваринницьких ферм являють собою будівельний матеріал із суміші гуми, кордного волокна і бітуму. Ними покривають підлоги із легких бетонів. Плити випускаються розмірами 2000х1000х15 мм.
Склад інградієнтів для отримання плит, в т.ч.: гумова крихта 50; кордні відходи 10; бітум 51-54; азбест сорту 7-20; парафіну 1; сірки 3,6 і тіураму 0,4,
Технологічний процес виготовлення гумових плит складається з підготовки сировини (додаткове подрібнення шинного корду в подрібнювачах ІПР-300, плавлення бітуму при 180°С), змішування компонентів в змішувачі періодичної дії СРШ-400 при 170°С протягом 60 хв., введення вулканізатора після вальців, додаткової гомогенізації протягом 15 хв, профілювання суміші на тривалковому каландрі з одержанням полотна шириною 1000 мм товщиною 7-8мм. Отримані заготовки пресуються і вулканізуються в двоповерховому пресі Д-7444 при 170°С протягом 40 хв. Далі йде обрізання готових виробів, їх маркування і упаковка.
Гумові плити для підлоги промислових будов розміром 500х500х20 мм виробляються також методом гарячої вулканізації.
Покриття "РЕГУПОЛ" виготовляються із гумової крихти для спортивних майданів, підрейкових прокладок для амортизації залізобетонних рейок і шпал, а також тепло-звукоізоляції підлоги кабін тракторів, комбайнів, автомашин. Вихідний склад цих виробів, %: гумова крихта 567 масових на 1000 масових частин сухої речовини латексу; латексної суміші б0%-ної концентрації - 113,5; дисперсії желатинного агента 2,75-3,7 масових частин.
Технологічний процес виготовлення "РЕГУПОЛУ" складається з того, що гумова крихта обробляється 2%-ним розчином парафінату калію і готується латексна суміш при перемішуванні латексу з дисперсією вулканізатора і парафінату калію протягом 30 хв. на вспінюючому апараті ВЕ-1, змішування гумової крихти з латексною сумішшю протягом 1 хв. нанесення і суміші на рухому основу і формування пористого шару, ущільнення його і і підпресовкою на вулканізаторі барабанного типу.
Гумову крихту використовують також у шляховому будівництві в якості наповнювача при створенні верхнього асфальтного шару шляхів і нижнього шару в якості пружної підкладки під асфальтове покриття, а також при будівництві основ шляхів при високих ґрунтових водах.
Застосування гумової крихти в шляховому будівництві підвищує довговічність шляхів, їх еластичність, стійкість до змін температури, силу щеплення автомашин з поверхнею шляху, знижує необхідність обслуговування поверхні і чуттєвість до розтріскування і механічного руйнування.
Південнокорейський дослідник побудував будинок із відпрацьовані автобусних автопокришок. Для цього він їх розрізав, випрямляв і отримував гумову полосу довжиною біля 3-х метрів. На дім площею 83 м2 потрібно 150 таких полос. Будівництво будинку займає 25-30 діб. Спочатку споруджується каркас будинку, потім його покривають зовні гумовими полосами. Їх можна вкладати як горизонтально, так і вертикально. Всередині і гумові полоси покривають полівініловою плівкою, щоб не пахло гумою. Потім іде шар поліпеностиролу - для теплоізоляції. Сухою штукатуркою і обклеюванням шпалерами закінчують будівництво. Ціна будівлі - 260 доларів за 1м2.
В Південній Кореї тепер накопичилось біля 15 млн. непотрібних покришок і їх кількість постійно зростає. Власники звалищ ще платять досліднику за те, що він забирає сміття. Побудована вже дюжина гумових будинків.
Піроліз зношених покришок в останній час все більше привертає увагу, як потенційне джерело одержання нафтової сировини і палива. В результаті термічної переробки зношених покришок одержують паливні мастила, гази і вуглець. Цей метод реалізований на Ярославському заводі технічного вуглецю.
Спалювання зношених покришок супроводжується високою температурою, тому покришки часто застосовують в якості палива, як це робиться на Каліфорнійській ТЕЦ і на цементних заводах Кам'янець-Подільська,! Хмельницької області України.
Теплота згоряння мазуту 40612 кДж/кг, вугілля 29308, природного газу 36356, а зношених покришок 30000 кДж/кг, тобто достатньо висока. Перша в Англії і у всій Європі електростанція, яка в якості палива використовує зношені автопокришки і на якій працює 60 чоловік, утилізує 23% старих покришок, забезпечує електроенергією 25 тис. будинків в окрузі.
На вищезгаданому Кам'янець-Подільському цементному заводі 18%| палива економиться за рахунок спалювання зношених покришок. Річний економічний ефект від цього починання складає 180 тис. крб. на рік (в цінах 1989 року).
Зношені покришки, які завантажували в доменну піч, утворюють 55% твердої речовини, аналогічної за складом і властивостями коксу, 30% газів і 15% рідких продуктів.
Встановлено, що 200 кг зношених покришок замінюють 50 кг коксу.
Фінська фірма "Вяртала Дизель Інтернейшнл" запатентувала спосіб виробництва дизельного палива із старих зношених покришок автомобілів. Процес полягає в тому, що спочатку покришки подрібнюють на спеціальних різальних машинах або струменями води під великим тиском.
Отримана крихта заморожується в рідкому повітрі. Гума відстає від корду і відходить у вигляді шматочків. Крихту змішують з відпрацьованими і мастилами і при високий температурі пропускають крізь насадку з нікелевим каталізатором (або з молібденовим). Внаслідок цього процесу полімерні молекули каучуку розкладаються на короткі, і гума перетворюється в рідину типу дизельного палива, яким можна заправляти автомашини.
Інші напрямки використаний зношених покришок. Новітні дослідження довели, що з покришок можна отримувати адсорбент типу активованого вугілля, а також іоннообмінної смоли, які застосовуються для очищення стічних вод від іонів важких металів з 99,5% ефективністю.
Подрібнені зношені автопокришки можна використовувати для очищення морської води від розлитих нафтопродуктів, а також для рафінування відпрацьованих мастил.
Подрібнена гумова крихта використовується в якості штучного грунту в теплицях у вигляді підстилочного шару або в суміші з грунтом для підвищення його родючості.
Цілі зношені автопокришки застосовують для створення штучних рифів для устриць, риб, мідій, молюсків і інших істот моря при їх розведенні 11.1 морських фермах.
Автопокришками укріплюють береги річок, каналів, озер, морів з метою запобігання від руйнування, ерозії, створення амортизуючих бар'єрів на небезпечних ділянках, а також укріплення відвалів у шахтах.
Ресурси зношених покришок величезні. В Японії їх збирається 475-570тис.т, в Німеччині - 340-370 тис. т, у Франції - 300 тис. т, в США -.90млн. штук на рік. Рівень їх використання різний: в Японії - 44,7%, Німеччині - 16%, в США-9%.
За кордоном гумова крихта використовується також у виробництві кольорового покриття для відкритих і зачинених спортивних ігрових площадок, підлог, покриття для сільськогосподарських забудов, експериментальних асфальтових шляхів. Гумова крихта в цих конструкціях скріпляється полі уретановим зв'язуючим.
7.7. Переробка вторинної сировини фторопластів.
Відходи фторопластів подрібнюють при низькій температурі в середовищі рідкого азоту, а потім пресують і спікають. Обладнання подрібнення-ножові подрібнювачі (до 15 мм), вібромлини і спеціальне устаткування з молотковими і дискмембранними робочими органами.
Порошок фторопласту, який отримують після подрібнення, пресують при тиску 300-500 кг/см2 з витримкою в 1-2 хв. Пресовані вироби повільно нагрівають в печі і витримують при температурі 375°С. Тривалість спікання 1 г на 3 мм товщини виробу.
Економічна ефективність використання вторинного фторопласту в перерахунку на 1 т відходів складала 10,5 тис. крб. (в цінах 1989 p.).
7.8. Черепиця із піску і полімерних відходів.
Псковська фірма "Сервіскомплект" випускає черепицю на основі піску і барвника, де зв'язуючим служать полімерні відходи - шматки, плівки, флакони , котушки, одноразові шприци, тобто, все те, що викидається на звалище.
Черепиця, яка отримується із такої сировини, вигідно відрізняється від тієї, яку виробляють з глини і піску та бетону: вона здатна служити не менше 50 років, морозостійка; має добрий зовнішній вигляд і у два рази легша глиняної черепиці. Це дозволяє різко зменшити витрати деревини при побудові стропил та обрешітки. Черепиця міцна, добре з'єднується водонепроникпивим замком, витримує будь-які вітрові навантаження. Виробництво цієї черепиці обходиться без каналізації, паро- і водопостачання. Використовується лише електроенергія. Лінія виробництва черепиці обслуговується трьома робітниками в одну зміну і може давати на рік 25тис. м2 продукції, витрачаючи на 1 м2 25 кг піску, 0,029 кг барвника 7,14кг поліетиленових відходів і 25 кВт/г електроенергії. Площа цеху 80 м2при висоті приміщення 6,5 м.
7.9. Інші способи використання полімерних відходів.
Московське об'єднання «Полімерпобут» виготовляє З тис. т полотнища з відпрацьованого вторинного поліетилену. Такий же матеріал виробляє пензенський завод "Полімер". Ці полотнища застосовуються для силосування кормів. На цих же підприємствах, а також в Одесі і Полтаві виготовляють гофровані труби з обмоткою і фільтрозахисним шаром. Маса 1 :
погонного метра такої труби 230-250 г. Газовики охоче використовують ці труби для газифікації міст, сіл. Вони корозостійкі, добре вкладаються і більш економічні. Ці труби міцніше і набагато легше керамічних та металевих, а строк їх дії на багато більший. Ці труби використовують також робітники тепличних та парникових господарств.
7.10. Регенерація солей міді у виробництві штучного волокна.
При виробництві мідноаміачного штапельного волокна на 1 кг його витрачається 0,5-0,6 кг мідного купоросу. 60% міді повертається із волокна при відділенних операціях у вигляді розчину сірчанокислої міді або мідного купоросу. Цей розчин використовується для виготовлення необхідних солей і гідроксиду міді. Одна третина цієї солі потрапляє в каналізацію з розчинами прядильної і інших ванн.
Регенерація солей міді і аміаку із відпрацьованих мідноаміачних розчинів може проводитись двома способами: кип'ятінням під вакуумом (при цьому мідь виділяється у вигляді оксиду міді, утворюючи мідний шлам) і пропусканням розчину через Н-катіонітний фільтр, коли внаслідок іонного обміну іони міді осідають на смолі замість іонів водню, які відходять у фільтрат. Останній потрапляє на відгонку аміаку.
Перший спосіб, який дозволяє одночасно регенерувати мідь і аміак, найбільш ефективний при переробці розчинів з прядильних ванн, а другий -при виділенні міді із стічних і промивних вод.
Є ще одна пропозиція виділяти мідь з відпрацьованих мідно-аміачних розчинів осадженням міді у вигляді основного сульфату міді після підкислення розчину сірчаною кислотою до РН 6-7.
7.11. Використання відходів інших підприємств.
Госсиполова смола {або бавовняний гудрон} - побічний продукт переробки бавовняного насіння при отриманні бавовняної олії. Це - в'язка рідина темно-коричневого кольору. Госсиполову смолу використовують в якості поверхнево-активної добавки при будівництві шляхового покриття з одночасним застосуванням бітумів.
Міськасфальттрести використовують госсиполову смолу, як додаток, який покращує якість асфальто-бетонних сумішей гарячого типу. Госсиполову смолу вводять в бітум порційне в два прийоми, але спочатку її піді-' і ивають до 40-50°С. Потім суміш бітуму зі смолою перекачують по бітумо-проводу "котел-змішувач-котел" і суміш стає однорідною. Крім того, 3% добавка госсиполової смоли знижує температуру розм'якшення бітуму на 20оС і збільшує глибину його проникнення.
Полімеризат - продукт переробки кубових залишків синтетичних жирних кислот (СЖК). Це - суміш високомолекулярних жирних (парафінового .або насиченого ряду) кислот темно-коричневого кольору. Полімерізат по зовнішньому вигляду і основних властивостях наближається до нафтових .гум марок БН-ІУ і БН-У. Він має достатньо високу адгезію до кам'яних і тих матеріалів.
Полімеризат в нагрітому стані добре змішується з бітумами, нафто-продуктами, розчиняється в органічних розчинниках. Він має водо- і тепло-якість. Висока в'язкість і мала пластичність полімеризату не дозволяє використовувати його в якості самостійного в'яжучого. Але він ефективний добавка до бітумів.
Асфальтобетон, який виготовляють на бітумі з добавками полімеризату, володіє, підвищеними водо- і теплостійкістю, деформуючою здатністю .при від'ємних температурах. Такі суміші більш рухливі, краще ущільнюються, ніж звичайні суміші без добавок полімеризату. При цьому витрати основного в'яжучого при використанні полімеризату скорочуються на 10-15%.
Полістиропьний порох - звичайний відхід виробництва блочного і суспензійного полістиролу. Цей порох додають до бітумів з метою зниження в'язкості останніх в 1,2-3 рази. При цьому знижується трохи і температура розм'якшення, а здовження бітуму зростає в два рази.
Асфальтобетонні суміші, які містять бітум з добавкою полістирольного пороху, зручні для укладання, мають деформаційну здатність при від'ємних температурах. Застосування полістирольного пороху не ускладнює технологічний процес виготовлення асфальтобетонних сумішей: полістирольний порох можна подавати як в бітум, так і прямо в змішувач одночасно з мінеральним компонентом.
Кубові залишки ректифікації-стиролу (КЗРС) отримуються в процесі. очищення стиролу перегонкою. Це однорідна каучукоподібна речовина брудно-коричневого кольору з запахом соляної кислоти. КЗРС містять стирол полістирол, нафталін, дифеніл і інші сполуки,
Практика показала, що КЗРС покращують якість бітумів, збільшують його розтягнутість, знижують температуру крихкості на 25% при незначному зменшенні температури розм'якшення (на 2°С),
Асфальтобетон, який готують на бітумі з добавкою КЗРС, має підвищену морозостійкість.
Вуглеводнево-формапьдегідна смола - основний відхід фенольних виробництв, кубові залишки від ректифікації нафталіну при його формальдегідній очистці Це в'язка рідина коричневого кольору, густиною 1,14 г/см. Смола містить 65% не летучого залишку чистої смоли, 15-20% нафталіну, тіонафтен і деякі інші сполуки. Застосування цього відходу шукається.
Відходи пенополістиролу є матеріалом для побудови теплоізоляційних шарів шляхового одягу, складова частина полістиролбетону - різновид легкого бетону. Цей цемент готується на цементі, воді, пенополістирольному щебені, який отримують подрібненням відходів пенополістиролу - шматків різної довжини і поперечного перерізу. Об'ємна маса пенополістиролу 105-140 кг/м3.
Крупність і гранулометричний склад цього щебеню піддається регулюванню. Об'ємна маса щебеню при стандартному ущільненні складає 35-50кг/м3, міцність при стиску - 0,1-0,3 кгс/см2.
Найбільш придатне в'яжуче для пенополістиролу є портландцементі марки 300 і 400. На 1 м3 бетону витрачається 180 кг портландцементу марки 400 100 кг пенополістирольного щебеню і 120 л води.
Бетонна суміш готується в бетономішалках примусового перемішування або лопатевих розчиномішалках. Суміш ущільнювати можна вібруванням або ручними катками, сновні властивості пінополістиролбетону: об ємна маса 250-400г/см3 межа міцності при стиску в 28 добовому старінні 0,35-0,7 МПа, (3,5-7 кгс/см2); коефіцієнт теплопровідності 0,1 Вт/°С/ 0,087 кКал/м град.
Теплоізоляція із пінополістиролбетону краща і дешевша, ніж з будь-якого іншого матеріалу.
6. Матеріали із відходів паливно-енергетичного комплексу.
6.1.Використання відходів вугільної промисловості.
Світове видобування кам'яного вугілля перевищило 2,5, а нафти - З млрд. т. За попередніми підрахунками в найближчий час загальне споживання кам'яного вугілля підніметься до 3,6 млрд. т.
На території України е 1259 териконів, тобто відходів вугледобування. До початку 1974 року на шахтах нашої держави було вже накопичено більше 4 млрд. т відходів вугільної галузі.
Для розміщення породи, яка видається шахтами, необхідно кожний рік виділяти більше 190 га сільськогосподарських угідь. Площа териконів складає більше 5 тис. га корисної землі. Враховуючи, що 1 га сільськогосподарських угідь дає дохід в 4-6 тис. крб. (в цінах 1989 року), то народне господарство України не доодержує до 20-30 млн. крб. доходу щорічно. Крім того, терикони і звалища забруднюють атмосферу і ґрунти. Так, з горючих териконів Львівсько-волинського вугільного басейну з 1 м2 площі териконів за добу виділяється 10,8 кг оксиду вуглецю, тобто чадного газу, 5,3 кг сірчистого ангідриду, 10,6 кг сірководню 1 оксиду азоту. Тому використання відходів видобутку 1 збагачення вугілля є одним із важливих завдань, які визначають шляхи раціонального розвитку всієї вугільної промисловості на Україні і особливо в даний час енергетичної кризи.
Горючі породи і їх застосування в будівництві. Горючі породи - продукт самообпалу пустих порід, які містять залишки вугілля. Відвальні горючі породи отримуються при окислювальному самообпалі шахтних порід при доступі кисню повітря. В них знаходиться до 3 % вугілля. Вони мають щільну шарувату будову. До них входить також мінеральна обгоріла піщано-глиниста частина, горючі сланці, сірка і вапняки. Під дією кисню повітря вугілля і сірка окислюються і самозагоряються. Під впливом високих температур (до 1000°С) порода піддається обпалу, а органічні домішки при цьому вигоряють. Причому обпал проходить вкрай не рівномірно, незважаючи на високу температуру в териконі.
Хімічний склад горілих порід, %: кремнезему 49-62; глинозему 2-13;
сірчистого ангідриду 0,3-1,5; оксиду кальцію 1,5-3,0; оксиду магнію 0,3-1,0;
оксиду марганцю (II) 0,4-1,22 і інших з'єднань 0,3-1, 5.
Фізико-механічні властивості горілих порід: об'ємна маса від 1 04-1,45 до 2,4-2,6 г/см3; міцність при стисканні 40-100 МПа (400-1000 кг/см ); водо-поглинання 1,3-4,4%.
Гранулометричний склад: фракція 0,5 мм - 23 %; Д 5 до 20 мм - 25%; від 20 до 60 мм - 27%; 260 мм - 25 %. Морозостійкість менше 15 циклів. Фізико-хімічні властивості горілих порід дозволяють їх використати для обладнання автошляхів, тротуарів і т.п.
Горілі породи також використовуються в якості заповнювачів звичайних бетонів, які після автоклавної обробки набувають міцності до ЗО МПа (300 кгс/см2). Автоклавна обробка бетонів з наповнювачами з гірських порід дає можливість виготовляти з них блоки і панелі.
В шахтарських містах Копейську і Коркині створені потужності по виробництву цегли із відходів вуглезбагачення за італійською технологією. Тут всі технологічні і транспортні операції здійснюються високопродуктивними механізмами-автоматами, вагонетками з електроприводами і іншими механізмами, які працюють під контролем електроніки.
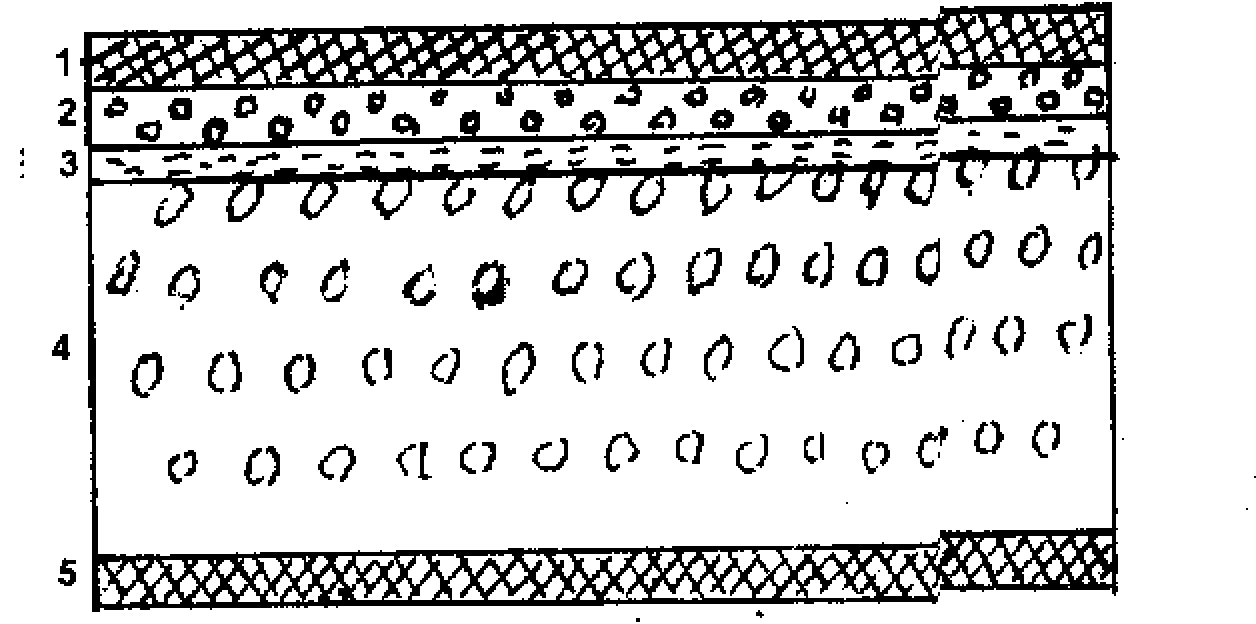
Мал. 3. Конструкція шляхового одягу
1 — асфальто-бетон; 2 — щебінь; 3 — горіла порода;
4 — гірська порода, оброблена дьогтем; 5 — дьогте-грунт (товщина в мм)
Сланцеві породи деяких териконів Донбасу являють собою сировину для отримання з них добрив. Експерименти показали, що ці добрива дозволяють підвищити врожайність вишні на 23%, полуниць - на 40%, люцерни - на 41%, пшениці - на 21%, огірків - на 29% і сіна – на 38%.
3.2. Використання шахтного метану.
Підрахунки спеціалістів показали, що в Донецькому вугільному басейні міститься більше 1,3 трл, м3 газу метану, який є причиною багатьох вибухів, пожеж та загибелі людей. В той же час його можна утилізувати, як це робиться в деяких країнах світу.
Так, в 1992 році в США було вилучено більше 10 млн. м метану з вугільних шахт за розробленою технологією вилучення підземного газу Із вугільних родовищ до розкриття вугільних пластів, а також в процесі Їх експлуатації.
На Україні на шахті «Торезька» проводились промислові досліди використання вугільного метану, який викачувався з вугільних пластів. Цим газом обігрівали два житлових будинки, теплицю, а також адміністративний корпус шахти. Там тим же теплом могли б забезпечити весь житловий масив. І навіть продавати його іншим. Але справа затримувалась відсутністю спеціального обладнання і труб. Крім того, в той час економічно не було доведено, що вигідніше добувати - "чорне" чи "голубе" золото Тим більше, що 1000 м3 підземного газу-метану по теплоті згоряння співставні з 1т найбільш калорійного вугілля.
Зараз на Україні прийнята програма створення і розвитку спеціалізованої метанодобувної галузі енергетичного комплексу.
За даними інституту газу США видобуток вугільного метану до 2010 року повинен зрости в світі до 470-610 млрд. м3 на рік, тобто до 15-20% всього видобутку природного газу і в тому числі в самих США до 60-80 млрд.