Вступ
Вид материала | Документы |
СодержаниеДо першої групи відносяться До другої групи відносяться Мал. 13. Схема процесу вилучення золота і срібла із шахтної породи або подрібненої руди з використанням пересувних установок |
- Вступ, 323.48kb.
- Програма дисципліни кредитний модуль " основи радіоелектроніки" (для груп фф) Вступ, 153.44kb.
- Питания з Програми з курсу «Механіка», що виноситься на зм 1 вступ, 86.8kb.
- Робоча навчальна програма здисципліни: Принципи І методи аналізу художнього твору Спеціальність, 222.75kb.
- План, вступ, викладення змісту теми (як правило, 2 глави), висновок, а також список, 24.79kb.
- Вступ України до Світової огранізації торгівлі. Законодавчі зміни. Галузеві стратегії”, 72.41kb.
- Робоча навчальна програма Модуля Вступ до спеціальності Для студентів спеціальності, 404.17kb.
- Вступ до історії україни 5-й клас (35 годин), 86.86kb.
- Вступ до історії україни 5-й клас (35 годин), 104.36kb.
- М. В. Ломоносов; [вступ ст., сост., примеч. А. А. Морозова]. Ленинград : Сов писатель,, 249.18kb.
Таблиця 12
Склади компонентів для отримання чорного і білого шлакоситалів
Компонент | Білий | Чорний | |
1 | 2 | ||
Шлак Кварцовий пісок Кремнефтористий натрій Сульфат натрію | 58,5 36,8 1,0 3,7 | 62,0 38,0 - - | 55,6 34,3 - - |
Шлакоситали випускаються у вигляді стрічки шириною 1500 мм і товщиною 6-9 мм. На тильній стороні стрічки є квадратні нарізи висотою 1,5-2,0 мм, а зовнішня сторона стрічки гладка і сяюча. З шлакоситалів випускають плитки розміром 300х500х10мм, 250х250х18 і 200х300х20 мм з нарізною лицевою стороною.
Шлакоситали різного кольору отримують шляхом нанесення на їх поверхню керамічних фарб. В таблиці 13 дані фізико-хімічні властивості шлакоситалів, які вироблені з металургійних шлаків.
Таблиця 13
Фізико-хімічні властивості шлакоситалів
Властивість | Одиниці виміру | Показник величина |
Об'ємна маса Коефіцієнт теплопровідності Температура плавлення Межа міцності при згині Межа міцності при розтягуванні Ударна в'язкість Твердість Модуль пружності | кг/см3 Вт/м°С оС МПа МПа Дж/см3 НВ МПа | 2700 1,32 850-900 90 37 0,34 5,7-7,5 900 - 102 |
Кислотостійкість в сірчаній кислоті Кислотостійкість в соляній кислоті Лужна стійкість Питома теплоємкість Коефіцієнт лінійного розширення Водопоглинання Межа міцності при стиску Коефіцієнт однорідності по міцності Опір плиток на удар Коефіцієнт стирання Коефіцієнт Пуансона | % % % КДж/кг°С см/град % МПа - Дж/см3 кг/см2 кг/см2 | не менше 98,5 не менше 90,0 не менше 85 0,84 7 •10-6 0,0 110 0,4 1.1 0,05- 10-5 0,21-0,23 |
Як видно з таблиці 13, шлакоситали мають щільну будову, володіють великою міцністю, твердістю, зносостійкістю, водонепроникністю, вогнепроникністю і корозійною стійкістю. Вони витримують 100 циклів змінного заморожування і розтоплення. Однак, крихкість шлакоситалів обмежує їх застосування. Шлакоситали доцільно застосовувати у випадку хімічно-агресивного середовища і високої вологості, для утеплення шарових панелей, зовнішніх стін. Шлакоситали склеюють рідким склом і використовують для виготовлення санітарно-технічних виробів - умивальників, ванн, унітазів, зливних бачків і труб.
Піношлакоситали використовують як тепло- і звукоізоляційний матеріал при виготовленні панелей, стін, плит, покриття, а також як конструкційний матеріал. Шлакоситали виробляють об'ємною масою від 300 до 1300 кг/м3.
3.5. Залізо і цемент з киснево-конверторних шлаків.
Киснево-конверторний шлак на відміну від доменних шлаків не володіє гідравлічними якостями і тому не має великої цінності.
Склад киснево-конверторного шлаку, %: оксиду заліза 15-40; кремнезему 7-18; оксиду магнію 2,6-6,0; оксиду марганцю 2,0-6,5; фосфорного ангідриду 1,0-2,5 і глинозему (0,3- 2,0).
Великий вміст заліза в шлаці робить доцільним його вилучення. Технологія цього процесу була розроблена А.Г.Вольфсом і Л.Х. Гесенсом (Пат США 4174961 10 листопада 1979 року фірма "Ерсто Нидерландс і Цемент Індастрі Ейс ІПВ") Нідерланди, СВР. Цементбейдрійбен НВ Бельгія. Оксиди заліза і марганцю, які є в шлаці, піддають відновленню вуглецем або його сумішшю з відходами вугільних шахт і глиноземом, який містить силікатні добавки. На мал. 12 зображено цей процес.
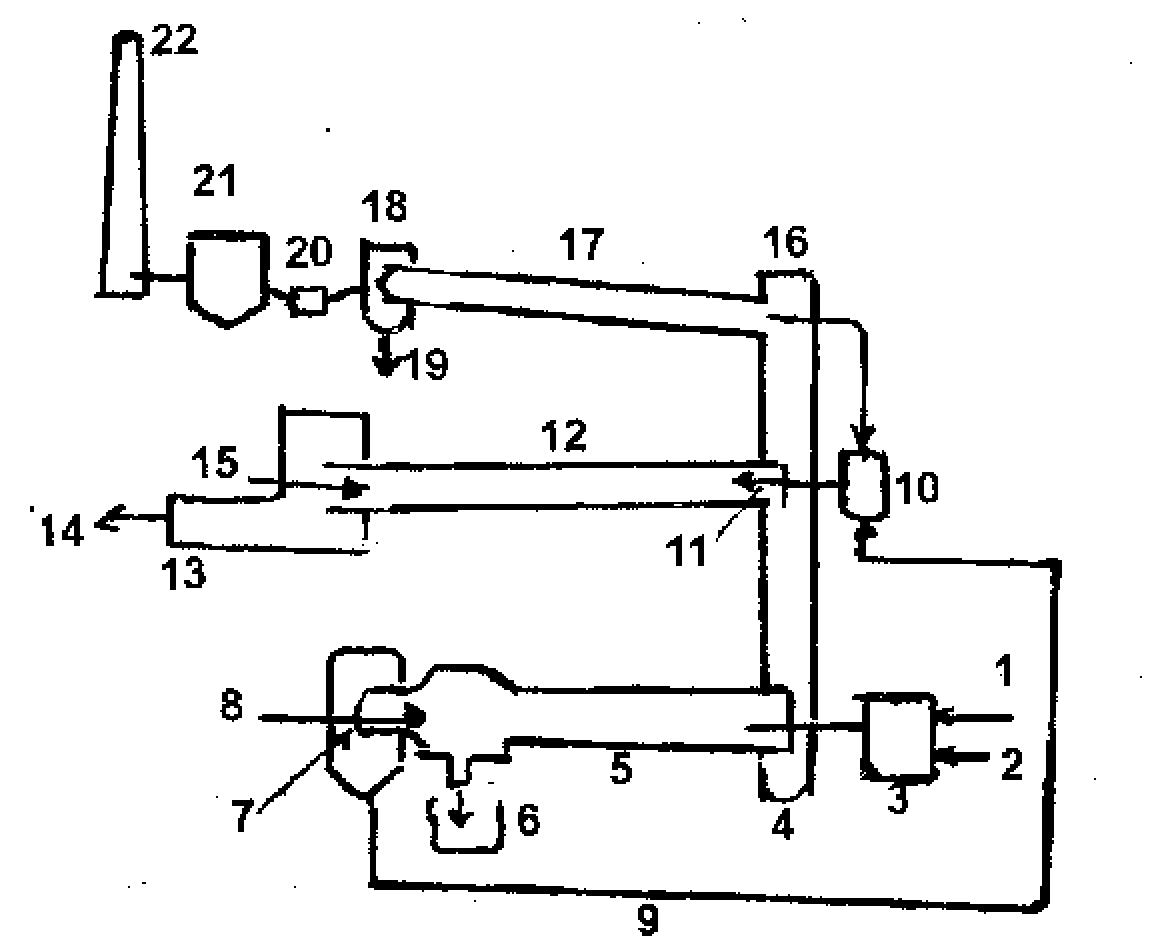
Man. 12. Технологічна схема процесу одержання заліза і цементного клінкеру із шлаків кисневого конвертора (опис в тексті)
Шлак подається по лінії 1, відходи вугільних шахт - по лінії 2 в пристрій для подрібнення 3. Сировина по лінії 4 потрапляє в обертову піч 5, де проходить відновлення оксидів металів. Нагрів печі здійснюється газом, який подається по лінії 8. При досягненні температури в 1400°С проходить плавлення сировини і виділення заліза, яке виводиться з печі по лінії 6. Шлак, який залишився в печі, після відділення заліза зливається через отвір 7, по лінії 9 подається в змішувач 10.
Вапняк або крейда по лінії 18 подаються в теплообмінник 17 для попереднього нагріву. Теплообмінник нагрівається газами, які виходять з випалювальної і агломераційних печей по лінії 11 і 12. Ці гази подаються по лінії 16. Теплообмінник 17 має пристрій для виходу пилу 19 за допомогою вентилятора 20 і електрофільтра 21 для вловлених найдрібніших частинок пилу. Відхідні гази викидаються в атмосферу через димову трубу 22. Передчасно нагріта подрібнена сировина із теплообмінника 17 також подається в змішувач 10, де змішується зі шлаком, який подається по лінії 9 і далі прямує в агломераційну піч 12 по лінії 11. В печі суміш нагрівається до 1400°С газом, який подається по лінії 15. Отриманий агломерат охолоджують в холодильнику 13 і по лінії 14 клінкер портландцементу виводять для подальшої переробки в цемент. ;
3.6. Технології переробки відходів кольорової металургії.
4.6.1. Утилізація сірчистого газу при отриманні міді і інших кольорових металів із сульфідних руд.
На заводах виробництва міді із сульфідних руд «плавкою на штейн” згідно наведених нижче реакцій:
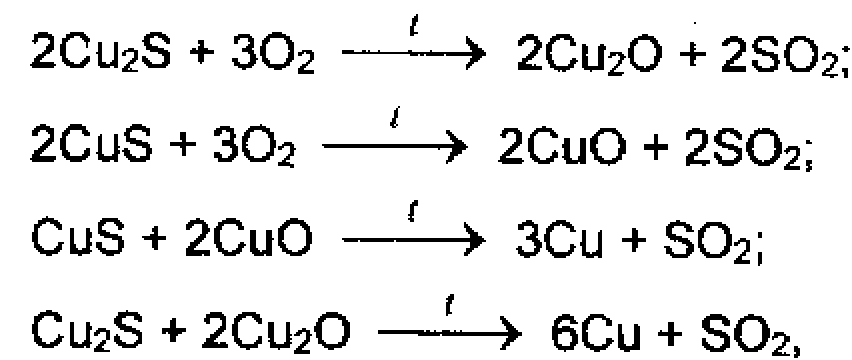
а також свинцю, цинку отримується в якості відходів велика кількість сірчистого газу. Тому на цих заводах є цехи виробництва сірчаної кислоти. Сірчистий газ висушують, очищують і концентрують. А потім іде відома технологія.
Якщо концентрація сірчистого газу мала, то іноді використовують технологію так званого "нестаціонарного каталізу", яка розроблена в інституті каталізу Сибірського відділення РАН д.т.н. Ю.Матросовим. Цю технологію більше використовують за кордоном.
Так, японська фірма "Хитачи Зоссен" на своєму заводі кольорової металургії біля м.Осака пустила в експлуатацію установку по одержанню сірчаної кислоти із відхідного сірчистого газу такої низької концентрації. Установка виготовлена по ліцензії, яку фірма придбала у вищезгаданому інституті.
В установці є новий апарат, який і діє "нестаціонарним каталітичним процесом". Установка автотермічна і сама виробляє високу температуру, яка придатна для опалювальних або технологічних цілей. Подібні установці змонтовані також в Пловдиві [Болгарія), індії фірма "Зенета минерария", Німеччині (фірма "Лургі"), США (фірма "Монсанто").
В колишньому СРСР такі установки були змонтовані на "Печенганікель", на Усть-Кам'яногірському свинцево-цинковому на Мідно-гірському, мідно-сірчаному та на Червоно-уральському металургійних комбінатах.
3.6.2. Шлаки кольорової металургії.
В залежності від виду переробленої сировини вихід шлаків у кольоровій металургії сягає від 10 до 200т на 1т отриманого металу. Ці шлаки містять значну кількість цінних компонентів.
Так, у шламах мідних заводів міститься залізо, мідь, цинк, золото, срібло і інші. У цинкових - залізо, цинк, свинець, кадмій та інші. Вміст окремих металів в ряді шлаків більше, ніж у видобувних рудах, тому такі шлаки повинні перероблятися.
Шпаки кольорової металургії за хімічним складом об'єднують в три групи.
До першої групи відносяться шлаки нікелевих і мідних підприємств, які відрізняються малим вмістом кольорових металів і заліза, їх переробка економічно не доцільна. Ці шлаки краще використовувати для виробництва будівельних матеріалів.
До другої групи відносяться мідні шлаки, які відрізняються малим вмістом міді і більш вагомим вмістом цинку і свинцю. Такі шлаки доцільно
переробляти для вилучення з них цинку, свинцю і заліза з одночасною утилізацією силікатної частини для виробництва будівельних матеріалів.
До третьої групи відносяться олов'яні і свинцеві шлаки, а також мідні, які відрізняються значним вмістом цинку, свинцю і олова, їх також доцільно переробляти для видобутку цих металів.
Технологія переробки груп шлаків вибирається в залежності від їх складу і фізико-хімічних властивостей. Наприклад, процес флюмінгування застосовується для технології переробки шлаку, який вміщує цинк. В цьому випадку через шар розплавленого шлаку, який знаходиться в шахтній печі, продувають під тиском суміш повітря з вугільним пилом. Причому повітря подають в кількості, недостатній для повного згоряння вугілля, щем приводить до утворення окису вуглецю, який відновлює метали з їх оксидів. Пари металів далі окислюються над розплавленим шлаком повітрям до оксидів. Останні виносяться з печі газовим потоком і відділяються від оксидів в циклонах. Шлак випускається із печі і в неї завантажується нова порція сировини. Шлак, що випускається із печі, гранулюють безпосередньо або після його відстоювання з метою виділення штейну при наявності в ньому міді і срібла.
Переробка шлаків вальцуванням проводиться в горизонтально нахилених трубчатих печах, які обертаються, в присутності відновника при температурі 1100-1200°С. Шихта готується із шлаку, коксу і безперервно подається в піч. Пари металів, які при цьому утворюються над шихтою, окислюються, виводяться з газами з печі і вловлюються циклонами.
Наявний у шихті сульфід свинцю сплавляється з сульфідами інших металів і утворює штейн-сплав. Він стікає до розвантажувального кінця печі. Наявні в шихті благородні метали і мідь практично залишаються в твердому стані і поступають на переробку для їх вилучення.
Штейн поступає на плавильні установки і конвертори для вилучення міді. Свинець відділяють від цинку внаслідок різних температур плавлення і кипіння.
Всі місця завантажування шихти, вивантажування металу і інші, які пов'язані з виділенням пилу, пару та газів, а також система евакуації металу, газів або пилу обладнані очисними спорудами для вловлювання матеріалів і повторного їх використання.
3.6.3. Золото з відвалів шахт кольорової металургії.
Процес вилучення золота з відвалів шахт, розроблений
P.M. Дарра (Пат. США 4056261, 1 листопада 1977 p.), поданий на мал. 13

Мал. 13. Схема процесу вилучення золота і срібла із шахтної породи або подрібненої руди з використанням пересувних установок
Установка включає в собі пристрій для розбризкування розбавленого розчину ціаністого калію і каустичної соди на поверхню відвальної породи або на подрібнену руду. Розчини проходять через шари руди до твердої поверхні землі 3. Природний нахил грунту направляє отриманий розчин комплексної солі золота в жолоб 4, який обтягнутий гумою 5. Розчин під дією сили тяжіння стікає в резервуар 6, який має непроникливу поверхню. Золото і срібло знаходяться у вигляді розчинених комплексних солей калію. Далі цей розчин перекачують до іонообмінних установок, які заповнені активованим вугіллям. Вони встановлені на трьох пересувних платформах 7, 8, 9. Кожна з ємкостей 10-14, які встановлені на платформах 7 і 8, мають в нижній частині розподільну плиту з отворами 15. Розчин подається в нижню частину першої колони, яка заповнена гранульованим активованим вугіллям і надходить вверх, а потім поступає знизу в другу колону, послідовно проходячи усі колони. При цьому вугілля вбирає в себе, тобто адсорбує, золото і Срібло. Ця процедура проводиться до насичення вугілля золотом і сріблом. З останньої колони розчин поступає на сито для відділення захоплених потоком частинок вугілля і попадає у вирівнювальний резервуар 16.
Нові порції розчинів каустику і ціаніду калію додаються до відпрацьованого розчину в ємкості 17 і 18. При цьому використовується дозатор. Отриманий, тобто збагачений компонентами, розчин знову потрапляє по трубопроводу 20 для розбризкування на шар нової порції породи. При цьому нова порція води додається в ємкість 19, яка розміщена на платформі 9.
3.6.4. Селен із анодного шламу процесу рафінування міді.
Селен із шламів процесу рафінування міді вилучається трьома способами: обпалом з содою, обпалом з кислотою і плавленням з содою і селітрою. Технологічний процес останнього способу зображений на мал. 14.
Процес, розроблений К.Н.Субраманяном, А.Іллісом і Н.К.Ніссеном (Пат. США 4165046, 1 липня 1979 року; фірма "Зеінтернштейн Нікель Компані", МНК) і призначений для гідрометалургійної переробки анодних шламів процесу рафінування міді. Анодні шлами містять селен, свинець, телур благородні метали. При цьому процес і ступінь виділення селену складає 95%, а його чистота 99.7%. Анодний шлам після виділення міді і телуру має такий склад, %: селену 35; глинозему ЗО; срібла ЗО; паладію 11; міді 3; телуру 1; нікелю 2 і золота 0,5.
Технологія: шлам змішують з каустичною содою, з вапном (5%) і вилужують при температурі 180-220°С протягом 3-7г при порціальному тиску кисню 0,03-0,1 МПа. При цьому проходить окислення селену до шестивалентного стану і виділення телуру. Добавки вапна на стадії видужування полегшують наступне фільтрування отриманої суспензії. Внаслідок окислювальної лужної обробки вилучається більша частина селену (994 мг/л) телуру (6 мг/л). Основні процеси, які тут проходять, описуються наступними рівнями:
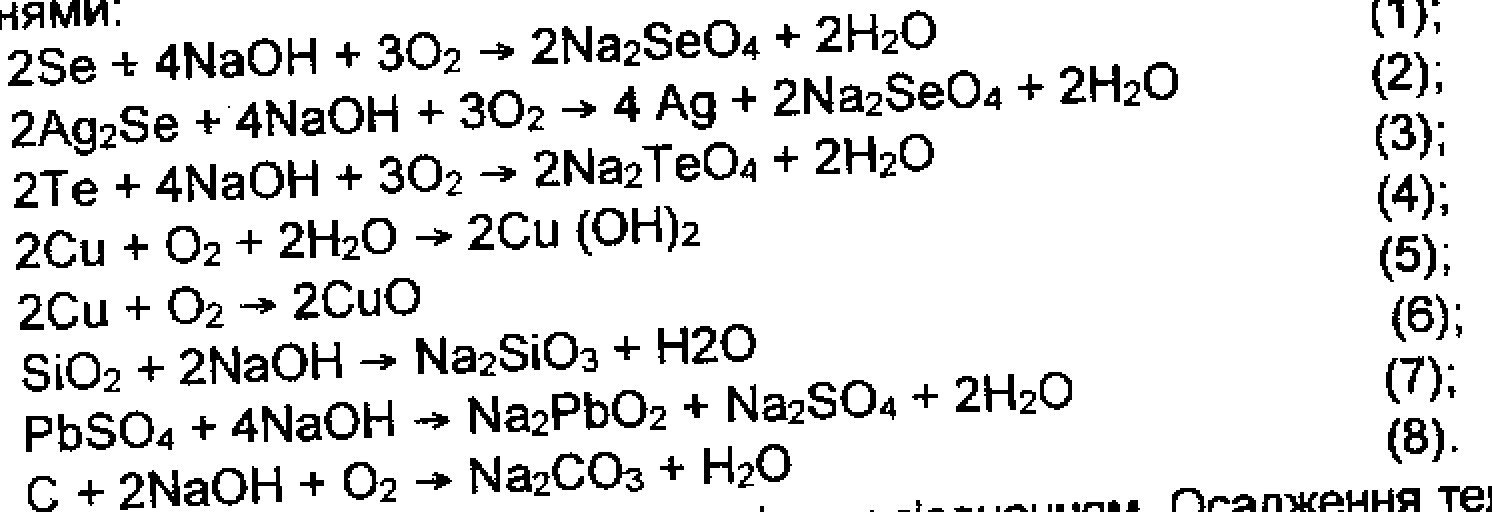
В реакції (8) літера С відповідає органічним з’єднанням. Осадження телуру (реакція 3) проходить майже кількісно. Розчин, який отримується внаспідок лужної обробки, нейтралізують при 30-70оС сірчаною кислотою до РН 7-9, і потім додають гідросульфід натрію в кількості 1-7% від маси шламу. При цьому проходить осадження з'єднань свинцю і діоксиду кремнію, платини і паладію.
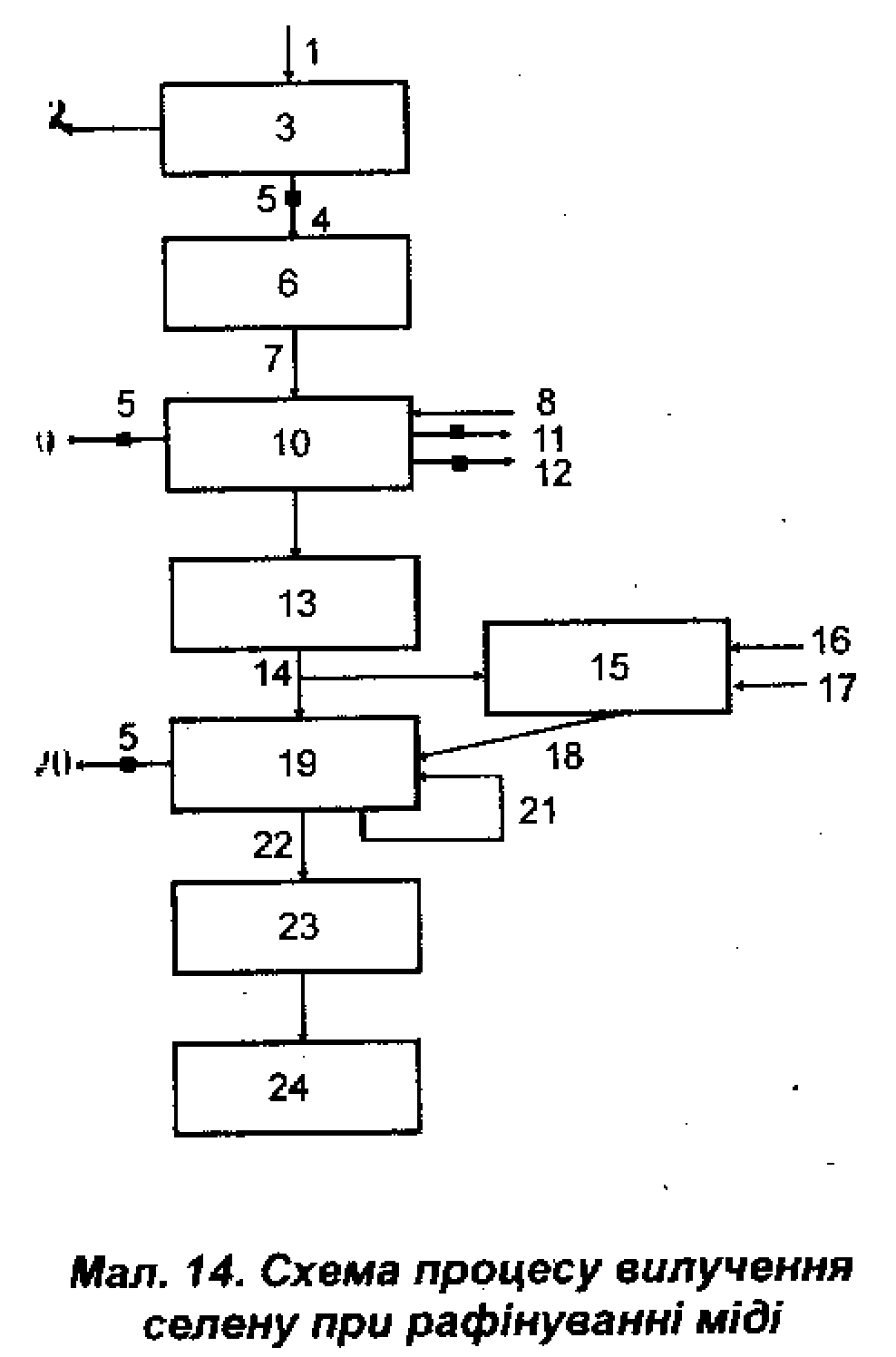
1 - анодний шлам; 2 - повернення міді на рафінування: 3 - видужування шламу для вилучення міді; 4 - анодний шлам, який містить срібло; 5 - крапка виділення побічних продуктів; 6 -промивання, сушіння, змішування, упаковка, транспортування; 7 - бруд і шлам; 8 - флюси (залізо, кремнезем, вапно); 9 - гази і пил при виділенні селену і телуру; 10 - тигельна піч; 11 - перший свинцевий шлам, який містить вісмут, срібло, золото і сурму; 12 - содовий шлам, містить селен, телур, срібло і золото; 13 - відливка анодів; 14 - аноди які містять золото і срібло; 15 - виготовлення електроліту; 16 - азотна кислота; 17 - мідь: 18 - розчин нітратів срібла і міді; 19 - електролізери для вилучення золота і срібла; 20 - пісок, який містить коштовні метали; 21 - брухт срібних анодів; 22 - кристали срібла; 23 - промивання, плавлення, відливка, зважування і штампування; 24 -срібні стержні (готова продукція).
Основні реакції, які проходять на стадії нейтралізації, можуть бути виражені наступними рівняннями:

Після нейтралізації в розчин додають вапно і фільтрують. Залишок на фільтрі промивають водою. Фільтрат містить свинець, телур і мідь. Залишок підкисляють сірчаною кислотою до 100 г/л при 50-60оС. При цьому додатково осаджується свинець у вигляді сульфату, який відділяється від розчину фільтруванням.
Потім на розчин діють сірчистим газом в присутності галогенідів і іонів двовалентного заліза, при цьому іони селену відновлюються до елементарного селену. Для цього суміш нагрівають до 90°С і пропускають крізь розчин сірчистий газ зі швидкістю 0,1-0,3 л на хвилину в розрахунку на літр розчину. За 4 години досягається практично повне осадження селену. Процеси, які при цьому проходять, можуть бути виражені наступними рівняннями:
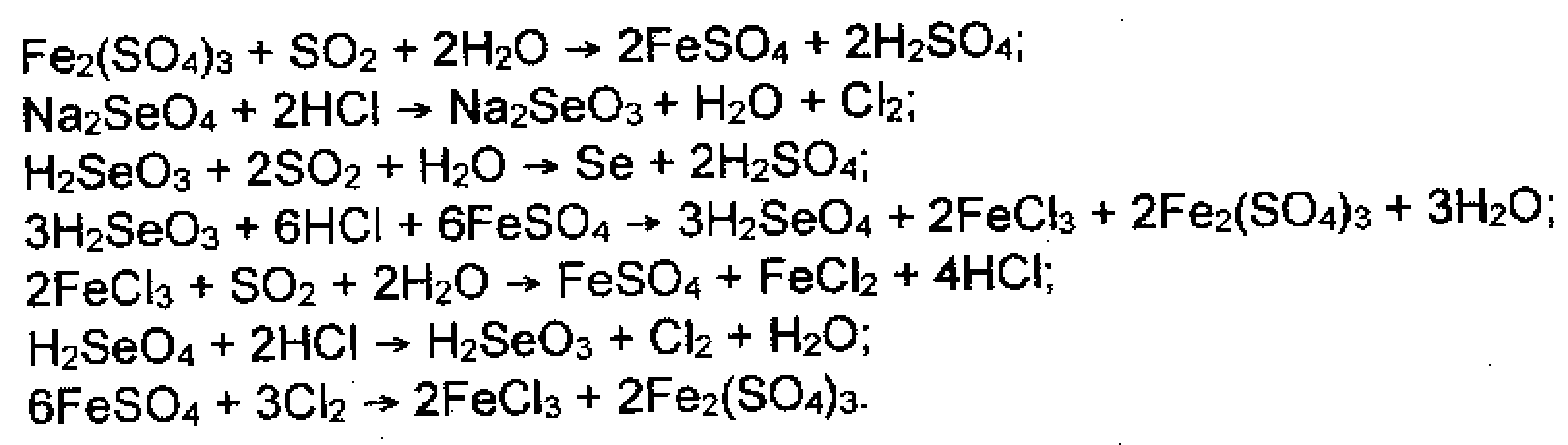
В цих процесах залізо поперемінно міняє свою валентність, переходячи з двовалентного в тривалентний стан і навпаки. Селен відфільтровують, розчин нейтралізують вапном до РН 8-9. Нейтралізований і оброблений сульфідом натрію залишок від вилужування вміщує практично всю кількість міді і телуру, які містились в первинній сировині. Частину цих елементів екстрагують сірчаною кислотою при 40-70°С і РН 1, 5-3. При, цьому екстрагується 50-80% міді і телуру. Розчин відфільтровують і направляють на вилучення телуру. Осад, який містить благородні метали, І потрапляє в піч ДОРЕ для їх вилучення. В осаді знаходиться 30-45% срібла, 1-2% міді, 1% телуру, 4% селену і 5% нікелю.
3.6.5. Срібло з анодних шламів процесу рафінування міді.
Технологічний ланцюг такого процесу відображений на мал. 15, Послідовність операцій: шлам промивають, висушують, перемішують і в упакованому вигляді подають на установку для вилучення благородних металів і в першу чергу срібла. Шлам завантажують в тигельну піч зі флюсами. Тигель являє собою піч відбиваючого типу зі сталевими стінками, футерованими основними вогнетривкими матеріалами. Верх пічки футерований оксидом алюмінію. Паливо-нафта або газ.
Процес обпалювання проходить періодично і триває 5-8 г. Плавлення і рафінування проводиться в одній і тій же пічці. Спочатку отримується сплав, з якого виробляють електроди, і проводять процес електролізу, внаслідок чого отримують чисте срібло і золото. Ступінь вилучення срібла сягає 95%.
Електролізер представляє собою резервуар Із скловолокна. Плоскі металічні аноди розміщуються паралельно підлозі апарата на відстані 7,5-10 см. Підлога електролізера виконує роль катоду, електролітом є суміш розчинів солей міді і срібла (нітрати).
Анодна сітка являє собою оболонку із фільтруючого матеріалу. При електролізі кристали срібла осідають на катоді, їх очищують з нього через кожні 3-4 г. Виділені кристали срібла промивають водою, висушують і плавлять в індукційній печі в срібні бруски.
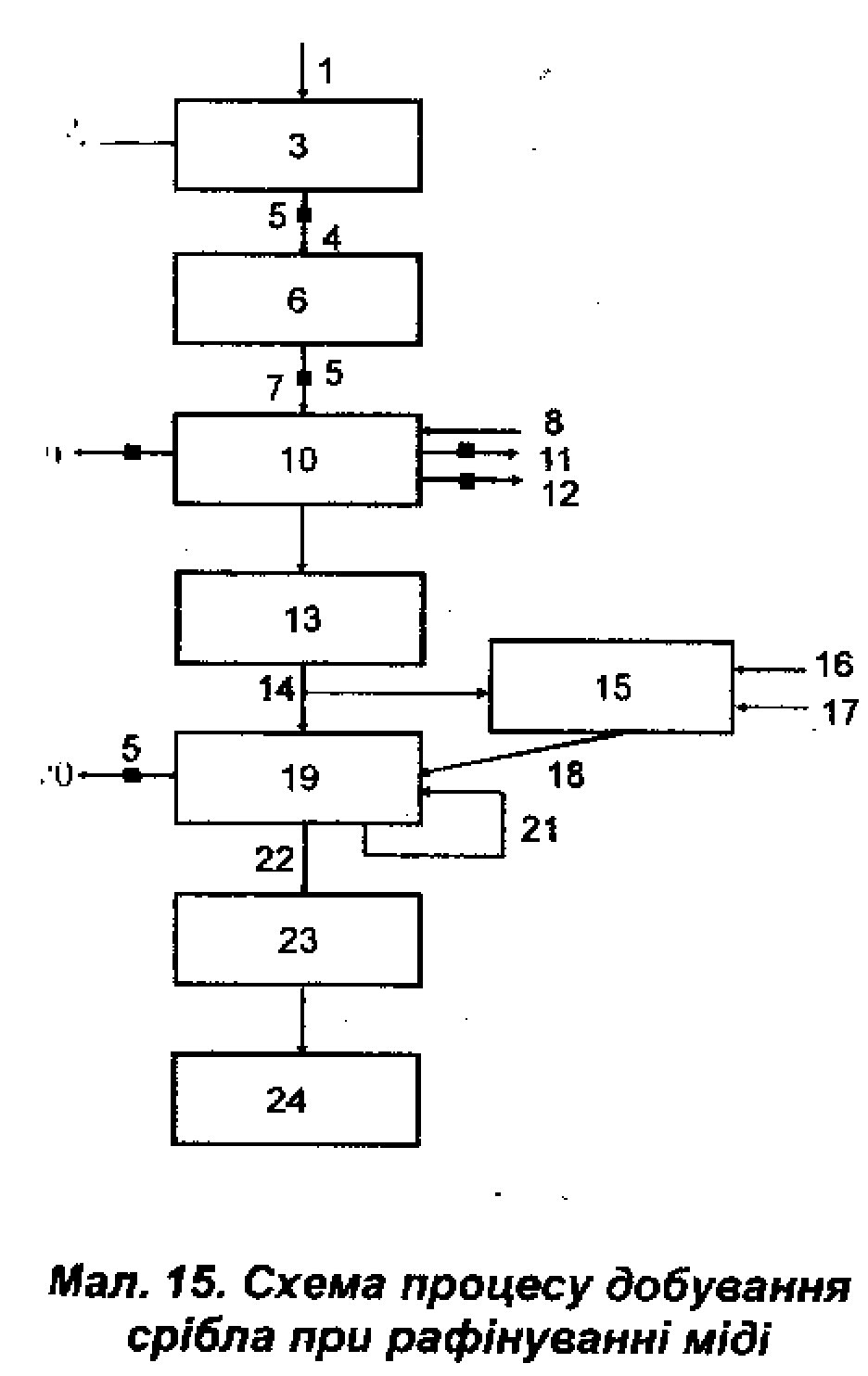
1 - анодний шлам; 2 - повернення міді на рафінування; 3 - вилужування шламу для вилучення міді; 4 - анодний шлам, який містить срібло; 5 - крапка виділення побічних продуктів; 6 - промивання, сушіння, зміщування, упаковка, транспортування;
7 - бруд і шлам: 8 - флюси (залізо, кремнезем, вапно); 9 - гази і пил при виділенні селену і телуру; 10 - тигельна піч; 11 - перший свинцевий шлам, який містить вісмут, срібло, золото і сурму; 12 - содовий шлам, містить селен, телур, срібло і золото; 13 - відливка анодів; 14 - аноди які містять золото і срібло; 15 - виготовлення електроліту; 16 - азотна кислота:
17 - мідь; 18 - розчин нітратів срібла і міді; 19 - електролізери для вилучення золота і срібла;
20 - пісок, який містить коштовні метали; 21 - брухт срібних анодів; 22 - кристали срібла; 23 - промивання, плавлення, відливка, зважування і штампування;
24 - срібні стержні (готова продукція).
Шлам, який збирається на фільтрувальній тканині на анодній сітці, в процесі електролізу срібла включає в собі золото і платину, їх вилучають з фільтра і піддають подальшій переробці. Ступінь виділення срібла оцінюється в 99%.