Научно-производственное содружество «альянс – цемен т»
Вид материала | Документы |
- Статут всеукраїнської громадська організації "Український фінансово-кредитний альянс", 135.88kb.
- Информационный центр всеукраинского объединения «русское содружество», 461.4kb.
- С. И. Мозжерин Федеральное Государственное Унитарное Предприятие «Научно-Исследовательский, 268.73kb.
- rn org/resources/summary/Russian doc, 125.05kb.
- Заочная межгуманитарная олимпиада Раздел: Иностранный язык (английский), 54.89kb.
- Vii международная научно-практическая Интернет-конференция «альянс наук: ученый ученому», 89.6kb.
- Никуличев Ю. В. Содружество независимых государств. Очерк современной истории, 1646.81kb.
- Франсез-Казань 5 лет, 49.99kb.
- С. В. Климашевская, М. В. Гладышева, В. Ф. Пузырев, Т. И. Уланова,, 75.4kb.
- М. М. Бутаев ОАО «Научно-производственное предприятие «Рубин», 41.2kb.
3.2. ОБЖИГ СЫРЬЕВОЙ ШИХТЫ
3.2.1. Процессы, протекающие в шихте при нагревании.
100 … 150 0С. Испаряется физическая вода.
400 … 600 0С. Дегидратация (отщепление гидратной воды) глин, Са(ОН)2.
700 … 1000 0С. Диссоциация (отщепление СО2 у карбонатов) MgCO3, СаCO3.
900 … 1100 0С. Образование твердых низкоосновных растворов, СаО Fe2О3,
2 СаО Fe2О3, СаОАl2О3.
1100 … 1300 0С. Зарождение высокоосновных твердых растворов 3СаОАl2О3, 2СаОSiO2, 3СаОSiO2 (образование расплава).
1300 … 1450 0С. Идет интенсивное насыщение известью низкоосновных твердых растворов, увеличивается доля расплава.
1450 0С … 100 0С. Охлаждение. В зависимости от скорости жидкая фаза либо кристаллизуется, либо остекловывается, идёт кристаллизация С3S, С2S, С3А, С4АF.
3.2.2. Механизм синтеза твердых растворов клинкера.
В твердых телах по мере нагревания усиливаются тепловые колебательные движения элементов кристаллической решетки. При определенном уровне нагревания амплитуда колебаний элементов становится настолько значительной, что они вырываются из своих узлов и начинают движение в кристалле, подгоняемые силами электрических разноименных зарядов. Это движение называется диффузией. Наиболее энергично элементы перемещаются на поверхности кристалла и по его ребрам. Это обусловлено меньшей энергией связи элементов и малым сопротивлением в сравнении с внутренним пространством кристалла. При некоторой температуре свободно блуждающие элементы отрываются от поверхности кристалла, создавая своеобразное облако вокруг твердой частицы, что способствует физико-механическому взаимодействию частиц находятся на некотором расстоянии друг от друга.
Когда в тесном контакте находятся частицы СаО и кислых оксидов, и эти частицы достаточно активны, происходит внедрение элементов СаО в SiO2, Аl2О3, Fe2О3. Несмотря на то, что масса СаО в шихте вдвое больше массы кислых оксидов, именно СаО внедряется, «раздувая», если можно так выразиться, кислые оксиды. Почему это происходит? Главная причина в размерах элементарной ячейки СаО. Ребро элементарной кубической ячейки СаО составляет 4,79 ангстрем, в то время как в тригональных SiO2 и Аl2О3 параметры элементарной ячейки соответственно 5,01 х 5,47 ангстрем и 4,75 х 12,97 ангстрем. В связи с этим коэффициент диффузии СаО в SiO2, Аl2О3, Fe2О3 на несколько порядков ниже коэффициента диффузии кислых оксидов в СаО.
3.2.3. Твердофазовое и жидкостное взаимодействие частиц при формировании твердых растворов.
При формировании клинкера имеют место процессы, протекающие только с участием твердых фаз, и процессы, протекающие с участием смешанных твердых и жидких фаз.
Твердофазовое взаимодействие как процесс диффузионного переноса вещества также есть функция температуры и времени. Например, если взять два тонкодисперсных порошка СаО и SiO2, смешать их и нагревать при температуре 1000…1100 0С в течение 100 часов, то получим твердый раствор 2СаОSiO2, содержание которого в исходной композиции не превышает 30 %. Обжиг при этих температурах в течение 1000 часов позволяет получить 50 % 2 СаО SiO2.
Однако если установить температуру обжига 1400 0С, то через 10 часов обжига вся сырьевая композиция СаО + SiO2 превратится в смесь 2 СаО SiO2 + 3 СаО SiO2.
Картина кардинально меняется, если в нагреваемой композиции возникает жидкая фаза. Так, например, если к рассматриваемой композиции СаО + SiO2 подшихтовать 15 % хлорида кальция, то уже при температуре 1200 0С через 5 часов нагрева вся сырьевая масса перейдет в твердые клинкерные растворы.
Почему так происходит? Коэффициент диффузии СаО в расплаве на несколько порядков выше, чем в твердой среде. Поэтому присутствие жидкой фазы в обжигаемом клинкере желательный энергосберегающий фактор. Однако «лишняя» жидкая фаза может негативно отразиться на технологическом процессе: не исключается «козление» массы, т.е. слипание обжигаемого массива. Из практики эксплуатации обжиговых агрегатов известно: доля расплава в клинкере при обжиге во вращающихся печах должна быть в пределах 20…30 %, в шахтных печах 15…25 %, в туннельных печах 25…40 %.
3.2.4. Теплообмен в обжиговых агрегатах.
Вращающиеся печи – 90…95 % энергии передается к обжигаемому клинкеру за счет теплового излучения факела и стенок печи, 5…10 % энергии передается конвекцией и теплопроводностью.
Шахтные печи – практически 100 % энергии передается конвекцией.
Туннельные и камерные печи – теплообмен смешанный, 60 % энергии передается конвекцией, 40 % излучением.
Важным технологическим обстоятельством при обжиге является время, поскольку этот фактор определяет производительность обжигового агрегата.
Теоретически для обжига смеси тонкодисперсного известняка и глины при значительном коэффициенте теплоотдачи много времени не требуется, 10…15 минут. Однако в реальных условиях это время существенно больше. Время обжига клинкера во вращающихся печах лежит в пределах 1,5…2,0 часа, в шахтных печах (в зависимости от размера гранул) 4…8 часов, в туннельных и камерных печах 6…12 часов.
3.2.5. Охлаждение клинкера.
Максимальная температура, которой достигает клинкер 1450…1480 0С. Для выгрузки готового продукта на склад клинкера его температура снижается до 100…150 0С.
Интервал изменения температуры клинкера в 1300…1380 0С не может не оказывать влияния на качество клинкера. Особенно важным обстоятельством является время изменения температуры, т.е. скорость охлаждения.
При быстром охлаждении клинкера минералы не успевают сформировать качественные крупные кристаллы, а расплав полностью выкристаллизоваться. В результате минералы клинкера мелкокристаллические с большим количеством дефектов, в клинкере присутствует значительная масса стеклофазы.
Медленное охлаждение клинкера позволяет протекать кристаллизации более качественно. Минералы клинкера представлены крупными, упорядоченными кристаллами, а количество стеклофазы в клинкере невелико.
Быстроохлажденный, слабозакристаллизованный клинкер характеризуется быстрым реагированием с водой и быстрым твердением, однако прочность цементного камня ниже, чем у медленно охлажденных клинкеров.
Медленноохлажденные клинкеры с водой реагируют достаточно медленно.
Режим охлаждения в каждом конкретном технологическом процессе подбирается индивидуально с учетом требований к будущему вяжущему и с учетом качества сырья. Например, если в сырье содержится значительное количество MgO, то охлаждать клинкер следует медленно для того чтобы кристаллы MgO максимально выросли. Крупные кристаллы MgO практически не реагируют с водой, что исключает нежелательный эффект расширения при твердении цементного теста.
При производстве быстротвердеющих и особо быстротвердеющих цементов стремятся максимально сократить время охлаждение клинкера быстрое.
3.2.6. Альтернативные энергоносители для обжига клинкера.
В качестве альтернативных энергоносителей для обжига клинкера могут использоваться любые твердые горючие вещества. Однако перед использованием целесообразно перевести твердое топливо в газообразное, т.е. твердое топливо следует газифицировать.
Наибольший интерес в этом плане представляют ископаемые угли.
Ископаемые угли состоят из трех продуктов: воды, минерального компонента (золы) и горючей массы.
В газификации участвуют горючая масса и частично вода. Золошлак всегда балласт. Чем больше в угле минерального компонента, тем меньше выход генераторного газа из единицы массы твердого топлива. Вода хотя и участвует в синтезе генераторного газа, но полученный при этом газ по суммарному показателю энергоемкости (теплотворность плюс теплосодержание) ниже безводного. Поэтому если в ископаемом угле значительное содержание воды, то целесообразно ее удалять, всю или частично, методом бертинирования (термическая обработка твердых топлив при t = 250…280 0С).
Балансы процесса газификации твердых топлив показаны на рис. 3.1.
В идеальном случае, когда потери тепловой энергии равны нулю, для газификации 1 кг угля с влажностью WО = 20 %, АС = 10 %, горючей массой 70 %, низшей теплотворной способностью 4775 ккал/кг требуется 1,98 кг воздуха, при этом образуется 2,88 кг генераторного газа с теплотворностью QН = 1365 ккал/кг и теплосодержанием i = 843ккал, и 0,1 кг золы.
Если теплотворность генгаза равна 1365 ккал/кг, а его теплосодержание равно 843 ккал, то в идеальном случае сумма произведения массы генгаза на его теплотворность и теплосодержания должна равняться исходной теплотворности угля.
МГГ х QГГ + i = QНУ
2,88 х 1,365 + 843 = 4774,2 ккал
Как видим, в идеальном случае энергетический потенциал исходного топлива равен энергетическому потенциалу продуктов его газификации.
В реальной действительности существуют потери, которые влияют на выход генгаза, его калорийность и теплосодержание. Однако материальный и тепловой баланс между исходным углем и продуктами газификации по-прежнему остается неизменным.
На рис.3.2. показан результат реальной газификации того же угля (рис.3.1.). Снижение теплотворности генгаза до 1293 ккал/кг и возрастание теплосодержания генгаза до 898 ккал баланс газификации не нарушили.
Приход: 4775 + 6 + 10 = 4791 ккал
Расход: (2,93 х 1293) + 898 + 47 + 5 = 4791 ккал
В таблице 3.7. даны показатели для процесса газификации ископаемых углей. Результаты получены в НИИСтромкомпозит. Из таблицы 3.7. видно, что, несмотря на различное содержание в углях балластного вещества (зола, вода) и различный выход генераторного
Материальный и тепловой баланс газификации твердого топлива (идеальный случай)
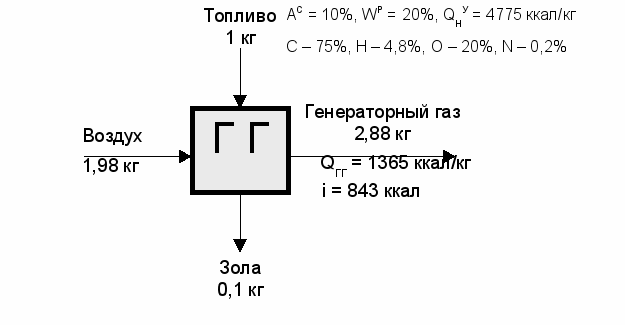
Рис. 3.1.
Реальный материальный и тепловой баланс газификации твердого топлива

Рис.3.2.
Таблица 3.7.
Теплотехнические параметры получения генгаза из различных углей
Месторождение | Вид угля, теплотворность, ккал/кг | Производство Генгаза | Энергетика генгаза | Сжигание генгаза | ||||||
Расход воздуха, кг/кг | Выход генгаза, кг/кг | Выход золы, кг/кг | Кало- рийность генгаза, ккал/кг | Темпе-ратура генгаза, 0С | Расход воздуха на сжигание 1 кг генгаза, кг | Полезная энергия 1 кг угля, ккал | Темпера-тура продуктов сгорания, 0С | КПД гази-фика-ции | ||
Кузнецкий Кузнецкий Интинский Подмосковный Егоршинский Челябинская область Бородинский Красноярский край Черемховский Иркутская область Гусиноозерский Экибастузский Казахстан Сучанский Приморский край Древесный уголь | газовый Q = 6350 тощий Q = 5400 длиннопламенный Q = 4370 бурый Q = 2490 паровичный Q = 5570 бурый Q = 3740 длиннопламенный Q = 4850 бурый Q = 4200 слабоспекающийся Q = 4000 жирный Q = 4900 Q = 7900 | 2,52 2,82 1,88 0,85 2,86 1,545 1,72 1,7 2,04 2,16 4,28 | 3,375 3,61 2,58 1,47 3,61 2,445 2,455 2,52 2,615 2,81 5,25 | 0,145 0,21 0,3 0,38 0,25 0,1 0,265 0,18 0,425 0,35 0,03 | 1050 1020 1170 1280 1050 1110 1490 1210 985 1240 1010 | 1000 1030 1000 840 1060 920 1000 980 1200 1050 1150 | 1,4 1,0 1,0 1,3 1,0 1,1 1,5 1,2 1,0 1,26 1,0 | 5430 4620 3710 2130 4770 3190 4150 3590 3420 4190 6750 | 1760 1730 1780 1700 1760 1710 1770 1770 1750 1730 1700 | 0,85 0,85 0,85 0,85 0,85 0,85 0,85 0,85 0,85 0,85 0,85 |
газа из единицы массы угля, температура продуктов сгорания различных генераторных газов практически идентична, и она удовлетворяет требованиям обжига клинкера.
Вместе с тем генераторные газы различных углей характеризуются различным энергетическим потенциалом (полезной энергией отнесенной к единице исходного топлива) – чем выше доля горючей массы в топливе, тем выше энергетический потенциал, но это не значит, что угли, содержащие большое количество балласта (подмосковные, бородинские и др.) непригодны для использования при обжиге клинкера. Газификация этих углей характеризуется бóльшим выходом зольного продукта на единицу выработанной энергии, но никак не отражается на качестве энергии.
Представляется весьма перспективным применение для обжига клинкера генераторного газа из древесного угля. Древесный уголь может быть получен из древесных отходов в одном комплексном аппарате совместно с газогенератором.
Древесный уголь отличается наивысшим энергетическим потенциалом среди всех углесодержащих топлив.
Пригодна для газификации горючая масса твердых бытовых отходов, представляющая собой смесь бумаги, древесины, текстиля, кожи, пластмасс и резины. Энергетический потенциал генгаза из ТБО вполне удовлетворяет требованиям обжига клинкера.
3.3. ПРОИЗВОДСТВО ПОРТЛАНДЦЕМЕНТА
3.3.1. Помол клинкера и сепарирование.
Заключительная фаза в производстве портландцемента – это совместный помол клинкера с гипсовым камнем и другими добавками, предусмотренными рецептурой.
Помол осуществляется в шаровых, трубных мельницах. Это самый энергоемкий процесс в производстве цемента. Тонкость помола портландцемента марки 400 обычно измеряется удельной поверхностью частиц и лежит в интервале 2300…2800 см2/г, что соответствует остатку на сите 008 – 7…10 %. Максимальная крупность частиц цемента до 80 мкм.
Шаровые мельницы не способны обеспечить требуемую тонину помола в открытом цикле, поэтому шаровые мельницы при помоле клинкера всегда работают в комплексе с воздушным сепаратором, поскольку никакое сито не решит проблему отсева требуемой фракции.
Воздушный сепаратор настраивается таким образом, чтобы отделить частицы тоньше 80 мкм от прочих частиц. То, что не проходит воздушный сепаратор, возвращается в мельницу на домол.
3.3.2. Марка портландцемента.
Марка цемента – это механическая прочность на сжатие образца из 1 части цемента и 3 частей стандартного (Вольского) песка, затворенных водой до нормальной густоты, твердеющего 28 суток в естественных условиях.
Обычная, наиболее распространенная марка портландцемента – 400. Это значит, что образец выдержал нагрузку в 400 кг/см2 (400 атмосфер) без разрушения.
Можно ли из клинкера одного состава получить более высокие марки портландцемента? Из любого клинкера возможно получить цементы марок 400, 500, 600.
Увеличение марки в указанном диапазоне достигается углублением тонины помола клинкера:
Марка 400 SУД = 2300 … 2800
Марка 500 SУД = 3200 … 3600
Марка 600 SУД = 4000 … 4500
Если изменить технологию формования образца: вместо виброуплотнения массы нормальной густоты применить вибропрессование или трамбование полусухой массы, а клинкер измельчить до тонкости 6000…6300 см2/г, то возможно получить образец RСЖ = 800 кг/см2.
В НИИСтромкомпозит в экспериментальном порядке получен портландцемент марок 1000 и 1200. Однако для этого потребовалось изменить минералогический состав клинкера, удалив алюминаты и ферриты.
Для понимания сути синтеза высокопрочного цемента обратимся к рис.3.3. На рисунке представлены кривые, характеризующие нарастание прочности цементного камня, составленного из мономинералов. Из рис.3.3. следует, что прочность С3S и С2S несопоставимо выше прочности С3А и С4АF. По сути два последних минерала «портят» портландцемент, ограничивая его марку. С этими минералами «мирятся» только потому, что все применяемые алюмосиликаты содержат Аl2О3 и Fe2О3, кроме того, оба – плавни, снижают температуру клинкерообразования.
Нами была предпринята попытка получить портландцемент только из кварцевого песка и высококачественного известкового компонента с добавкой хлорида кальция. Синтез клинкера осуществили при температуре 1400 0С в течение 5 часов. Измельченный до тонкости 6200 см2/г, смешанный с Вольским песком (3 части) и затворенный водой В/Ц = 0,25, цемент показал на 28 сутки; отформованный трамбованием 1000 кг/см2, отформованный прессованием при Руд = 200 кг/см2 – 1200 кг/м2. Образцы этого цемента, хранившиеся во влажной среде 1 год, показали прирост прочности до 1500 кг/см2.
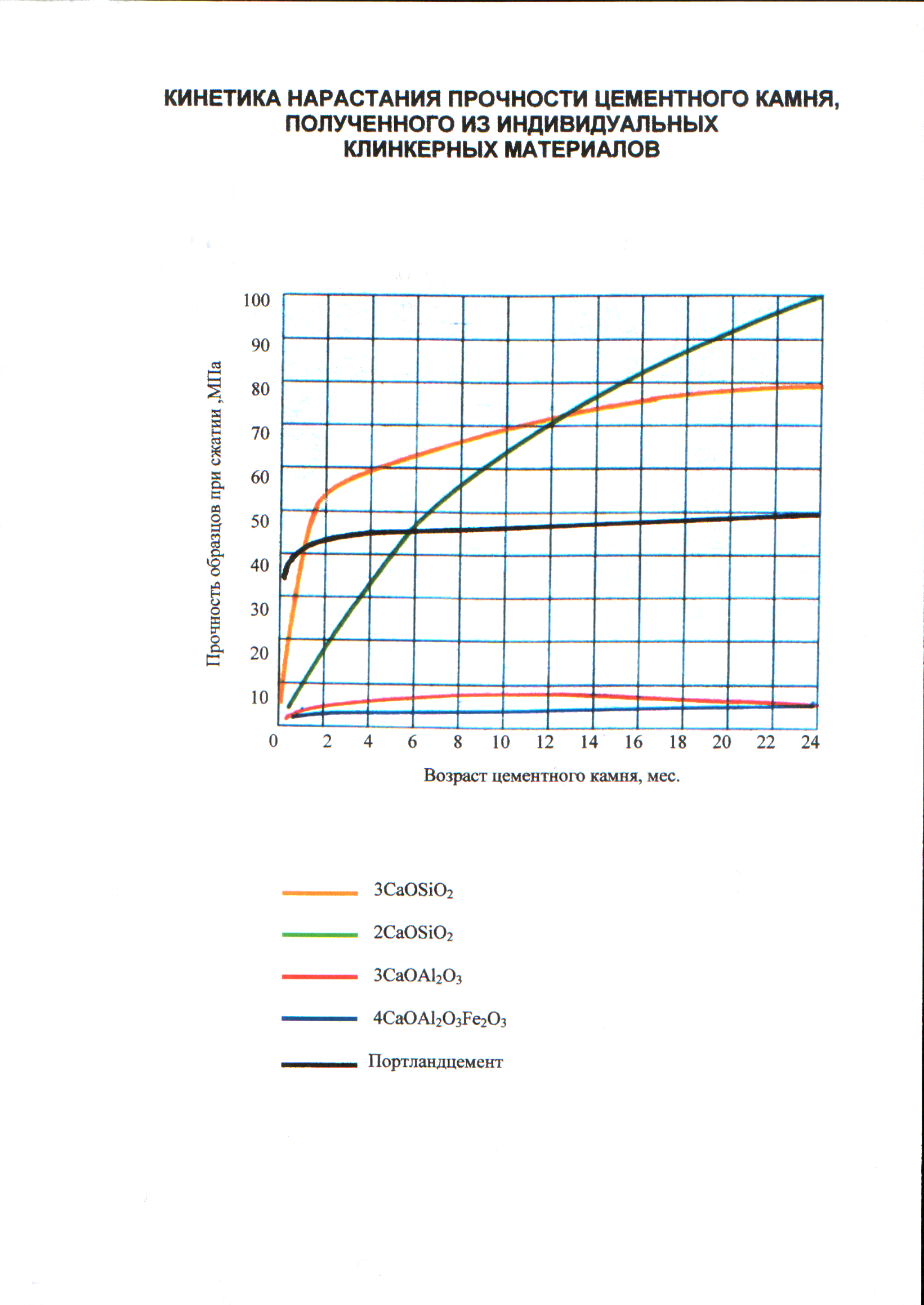
Рис. 3.3.
3.4. ЭКОЛОГИЧЕСКАЯ БЕЗОПАСНОСТЬ ПРОИЗВОДСТВА ПОРТЛАНДЦЕМЕНТА
Основными видами вредных выбросов цементных заводов являются минеральные аэрозоли и оксиды серы и азота продуктов сгорания, отходящих от обжиговых агрегатов.
Подавление аэрозолей на современных заводах осуществляется комплексом аспирационных аппаратов, в основе которых электрофильтры, осадительные циклоны, рукавные фильтры. Указанная аспирационная система работает эффективно, снижая выбросы аэрозоли на 99,9 % при условии соблюдения строгой герметизации всех газоходов.
Традиционные технологические производства портландцемента рассчитаны на использование в качестве энергоносителей углей. Среднестатистический выброс SО2 –3 кг на 1 т цемента, NОх – 1,2 кг на 1 т цемента.
Подавление вредных оксидов наиболее эффективно достигается путем промывки газов щелочными водами в аппаратах «мокрой» промывки – скрубберах.
Уловленные аэрозоли и обезвоженные шламы «мокрой» очистки газов возвращаются в технологический процесс.
4. ПРОИЗВОДСТВО ПОРТЛАНДЦЕМЕНТА ИЗ ТЕХНОГЕННЫХ ПРОДУКТОВ ПО УНИВЕРСАЛЬНОЙ ТЕХНОЛОГИИ НИИСК
4.1. Особенности универсальной технологии НИИСК
Впервые разработана и предлагается к широкому внедрению универсальная модульная технология производства портландцемента из техногенных продуктов в широком диапазоне мощностей, названная сокращенно «технология НИИСК», по имени научной организации НИИСтромкомпозит, в которой данная технология разработана.
Универсальность технологии НИИСК заключается в том, что она формируется из различных функциональных модулей в зависимости от мощности производства, исходного сырья и энергоносителей, при этом оборудование модулей отечественное, выпускаемое сырейное.
Технология НИИСК при комплектации технологического оборудования предполагает максимальную сборку узлов и технологических блоков на заводе с минимальными монтажными затратами на строительной площадке.
Технология НИИСК рассчитана на использование техногенных продуктов – промышленных отходов производств различного технического назначения, что позволяет существенно снизить производственные затраты, увеличивая доходность мини-завода.
Технология НИИСК – чистое, экологически безопасное производство, гарантирующее уровень выбросов цементной пыли ниже норм, установленных Евростандартом, все уловленные аэрозоли возвращаются в технологический процесс.
В технологии НИИСК предусмотрена система утилизации тепла с генерированием электрической энергии и тепловой для внутренних хозяйственно-технологических нужд.
В технологии НИИСК все процессы высокомеханизированы, при желании Заказчика любая серия мини-завода может быть автоматизирована до уровня завода-автомата.