«Магнитогорский государственный технический университет им. Г. И. Носова»
Вид материала | Автореферат |
- «Магнитогорский государственный технический университет им. Г. И. Носова», 302.73kb.
- Методика применения методов программной инженерии на этапах разработки информационной, 111.59kb.
- Нп «сибирская ассоциация консультантов», 132.23kb.
- Конференция состоится 11-12 мая 2012г, 58.92kb.
- Разработка механизма формирования конкурентной стратегии в отраслях олигополии, 220.25kb.
- Разработка метода диагностирования ад на основе конечно-элементной модели, 198.53kb.
- Электропривод насосного агрегата на основе энергосберегающего асинхронного двигателя, 268.94kb.
- Методика диагностирования силовых трансформаторов на основе оперативного контроля частичных, 286.02kb.
- Великий Андрей Борисович совершенствование технологии разливки стали на высокопроизводительных, 288.42kb.
- Разработка методики анализа надежности автоматизированных электроприводов прокатных, 289.64kb.
На правах рукописи
Малофеев
Алексей Евгеньевич
СОВЕРШЕНСТВОВАНИЕ ТЕХНОЛОГИИ ВЫПЛАВКИ СТАЛИ В СОВРЕМЕННОЙ ДУГОВОЙ ЭЛЕКТРОПЕЧИ С ИСПОЛЬЗОВАНИЕМ МАТЕМАТИЧЕСКОГО МОДЕЛИРОВАНИЯ
Специальность 05.16.02 –
Металлургия чёрных, цветных и редких металлов
АВТОРЕФЕРАТ
диссертации на соискание учёной степени
кандидата технических наук
Магнитогорск – 2010
Работа выполнена в Государственном образовательном учреждении высшего профессионального образования «Магнитогорский государственный технический университет им. Г.И. Носова».
Научный руководитель – доктор технических наук, профессор
Бигеев Вахит Абдрашитович.
Официальные оппоненты: доктор технических наук
Бабенко Анатолий Алексеевич;
кандидат технических наук
Сарычев Александр Валентинович.
Ведущая организация – Институт металлургии Уральского
отделения Российской академии наук.
Защита состоится 30 июня 2010 г. в 14-00 на заседании диссертационного совета Д 212.111.01 при ГОУ ВПО «Магнитогорский государственный технический университет им. Г.И. Носова» по адресу: 455000, г.Магнитогорск, пр. Ленина, 38, малый актовый зал.
С диссертацией можно ознакомиться в библиотеке ГОУ ВПО «Магнитогорский государственный технический университет им. Г.И. Носова».
Автореферат разослан 27 мая 2010 г.
Учёный секретарь
диссертационного совета Селиванов В.Н.
ОБЩАЯ ХАРАКТЕРИСТИКА РАБОТЫ
Актуальность работы. Доля мирового объёма производства стали в дуговых электропечах в 2009 году составляла около 38 %. Прогнозы указывают на рост доли электростали в течение последующего десятилетия со скоростью до 4 – 5 % в год. Современные дуговые электропечи используются для расплавления шихты и получения жидкого полупродукта, превращение которого в сталь заданного химического состава и качества осуществляется методами ковшовой металлургии.
Технология выплавки полупродукта в современных электродуговых печах развивается в направлении интенсификации плавки. Основными способами интенсификации плавки являются применение топливо-кислородных горелок, кислородных фурм, вдувание углеродсодержащего материала, применение в металлической шихте жидкого чугуна, работа с «болотом» на вспененном шлаке, продувка ванны инертным газом. Современные способы интенсификации плавки позволили сократить цикл плавки до 30 – 50 мин., а удельный расход электроэнергии до 300 – 400 кВтч/т.
Важную роль в современной технологии электроплавки имеет шлак, который помимо рафинирующих свойств должен обладать необходимой способностью к вспениванию для экранирования электрических дуг и повышения эффективности использования электрической энергии. Интенсификация плавки применением больших объёмов газообразного кислорода приводит к образованию высокоокисленного шлака с разной склонностью к вспениванию.
В настоящее время усиливается дефицит традиционных компонентов металлошихты: стального лома и чугуна, поэтому возрастает роль металлизованного сырья при выплавке электростали. Различные виды такого сырья заметно отличаются друг от друга по химическому и фракционному составам, для их успешного применения требуются дополнительные исследования.
В связи с этим, актуальной задачей для электросталеплавильного производства является разработка методов предварительного прогнозирования различных вариантов технологии плавки в дуговой электропечи.
Целью работы является совершенствование технологии выплавки стали и расширение сырьевой базы современной дуговой электропечи для улучшения технико-экономических показателей с помощью уточнения ряда параметров плавки, математического моделирования, лабораторных и производственных экспериментов.
Для достижения этой цели потребовалось провести совместно с работниками Центральной лабораторией комбината и Центром энергосберегающих технологий ОАО «ММК» промышленные исследования в условиях действующего производства на ДСП-180 ОАО «ММК» и определить неизвестные ранее параметры:
- соотношение оксидов железа (FeO) и (Fe2O3) в шлаке;
- состав и температуру отходящих газов.
Кроме того, требовалось оценить эффективность вдувания углеродсодержащего материала для вспенивания шлака, а также изучить поведение разных видов металлизованного сырья при плавке стали в ДСП-180 ЭСПЦ ОАО «ММК».
Научная новизна работы заключается в следующем:
- получены эмпирические зависимости содержания в шлаке оксидов железа (FeO) и (Fe2O3) при изменении общей окисленности шлака современной ДСП;
- выявлена рациональная область окисленности шлака. Общая окисленность шлака должна быть не более 40 %, а содержание (Fe2O3) не более 10 %;
- определён состав отходящих газов по ходу современной электроплавки;
- определена температура отходящих газов по ходу плавки.
Практическая значимость работы состоит в том, что
1. Разработана математическая модель, позволяющая рассчитывать основные параметры различных вариантов технологии плавки современной электропечи.
2. Сделаны рекомендации по совершенствованию процесса вдувания углеродсодержащих материалов в ДСП-180 ОАО «ММК».
3. Произведена оценка возможности применения различных видов железосодержащих материалов с разной степенью металлизации в электродуговой плавке.
4. Разработанная математическая модель технологии выплавки стали в современной ДСП стала основой для создания мультимедийной обучающей системы «Сталевар ДСП», успешно внедрённой в процесс обучения производственного персонала ОАО «ММК» и студентов металлургических специальностей ГОУ ВПО «МГТУ им.Г.И. Носова».
Апробация работы. Основные результаты работы докладывались и обсуждались на научно-технической конференции молодых специалистов ОАО «ММК» (Магнитогорск, 2006 и 2008); третьем конгрессе металлургов Урала (Челябинск, 2008г.); десятом международном конгрессе сталеплавильщиков (Магнитогорск, 2009г.); втором международном промышленном форуме «Реконструкция промышленных предприятий – прорывные технологии в металлургии и машиностроении» (Челябинск, 2009г.); на ежегодных конференциях МГТУ по итогам научно-исследовательских работ в 2007…2010 годах.
Публикации. По материалам диссертации опубликовано 12 статей в журналах и сборниках научных трудов, в том числе 3 статьи в изданиях, рекомендованных ВАК РФ.
Структура и объём работы. Диссертация состоит из введения, 4 глав, общих выводов, списка использованных источников и приложений. Она изложена на 130 страницах машинописного текста, включая 19 таблиц, 28 рисунков и 102 источника.
ОСНОВНОЕ СОДЕРЖАНИЕ РАБОТЫ
Во введении обоснована актуальность темы диссертационной работы, определены ее цель, решаемые задачи, научная новизна и практическая значимость.
В первой главе на основе анализа литературных данных рассмотрена выплавка стали в современных электродуговых печах. Особое внимание уделено особенностям вспенивания шлака. Выявлены недостаточно исследованные элементы технологии (соотношение оксидов железа (FeO) и (Fe2O3) в шлаке, состав и температура отходящих газов) и недостатки математических моделей, описывающих процесс.
Во второй главе приведены результаты исследований в условиях действующего производства на ДСП-180 ЭСПЦ ОАО «ММК». Анализ специально отобранных проб шлака по ходу плавки показал, в основном, его чрезмерную окисленность (общее содержание оксидов железа иногда превышало 50 %), и повышенную долю оксидов трёхвалентного железа (рисунок 1).
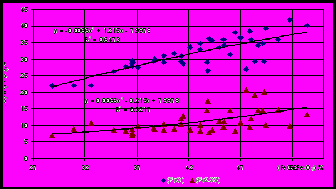
Рисунок 1 – Зависимость содержания оксидов железа от общей окисленности шлака ДСП:
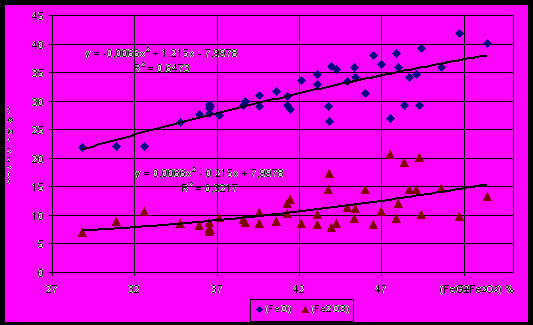
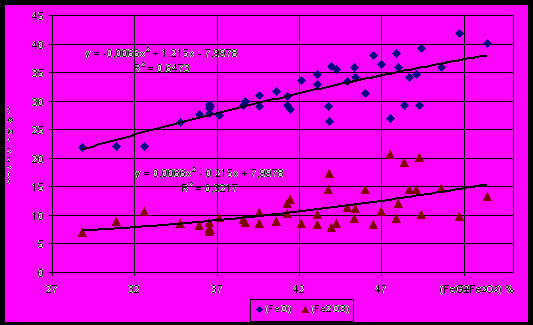
Обработав результаты, представленные на рисунке 1, получили зависимость отношения (FeO)/(Fe2O3) от общей окисленности шлака (рисунок 2).
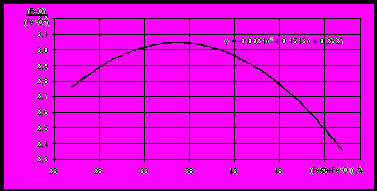
Рисунок 2 – Зависимость отношения оксидов железа (FeO)/(Fe2O3) от общей окисленности шлака ДСП
Из рисунков 1 и 2 видно, что при увеличении общей окисленности шлака более 35 %, наблюдается резкий рост доли высшего оксида железа (Fe2O3).
Получена зависимость отношения оксидов железа (FeO)/(Fe2O3) от окисленности шлака ДСП-180:

Решив систему уравнений

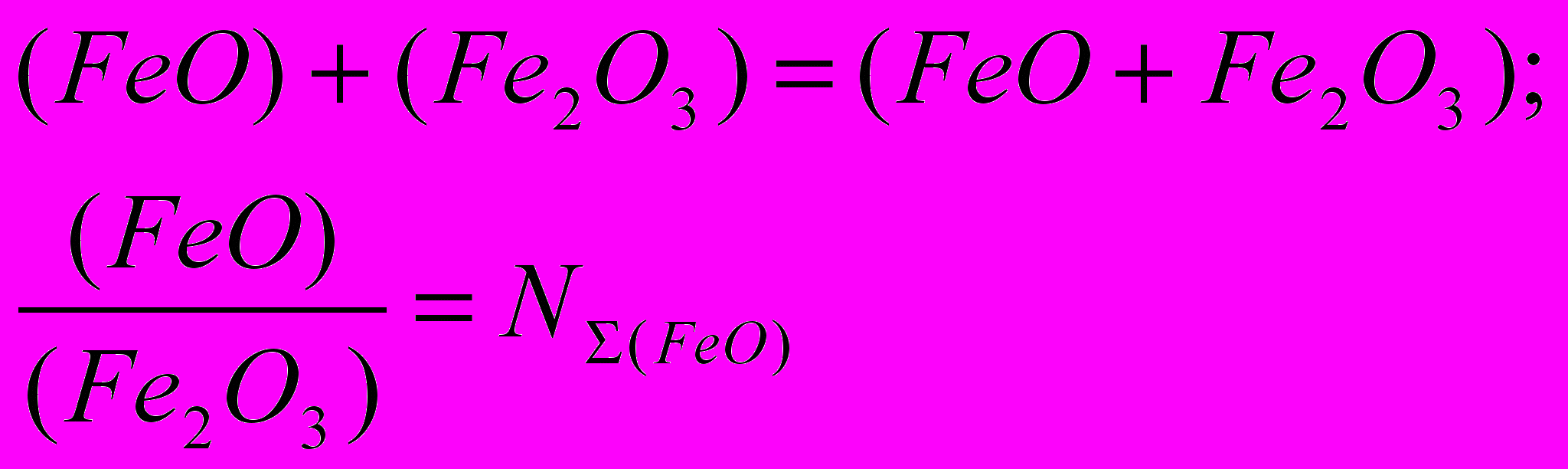
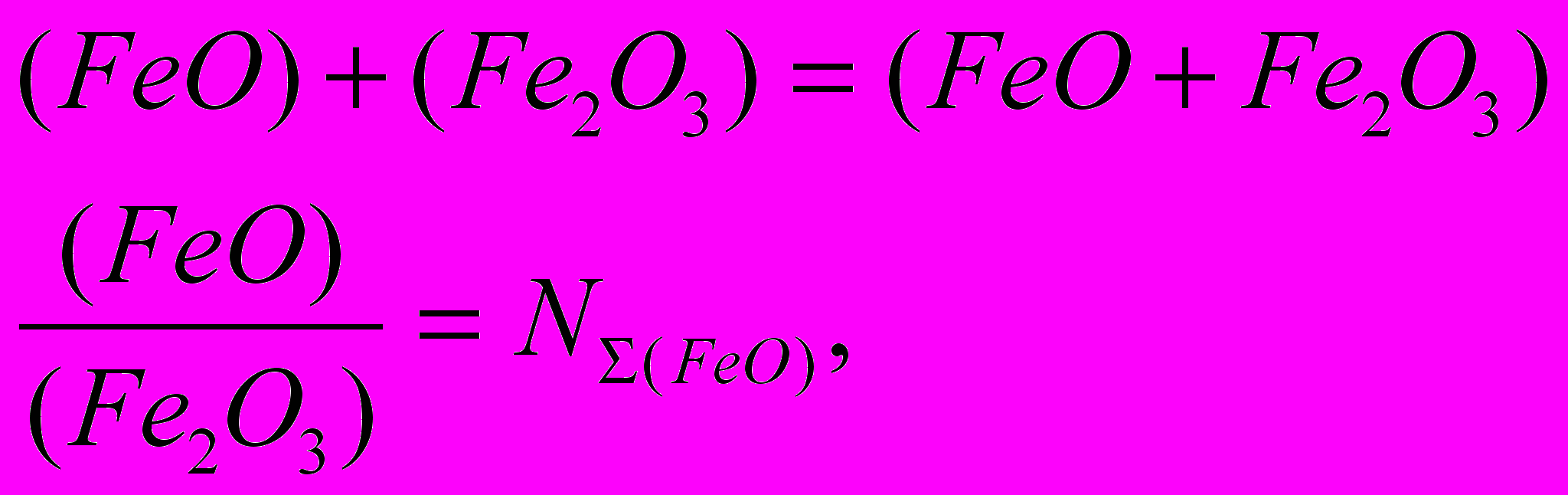
где
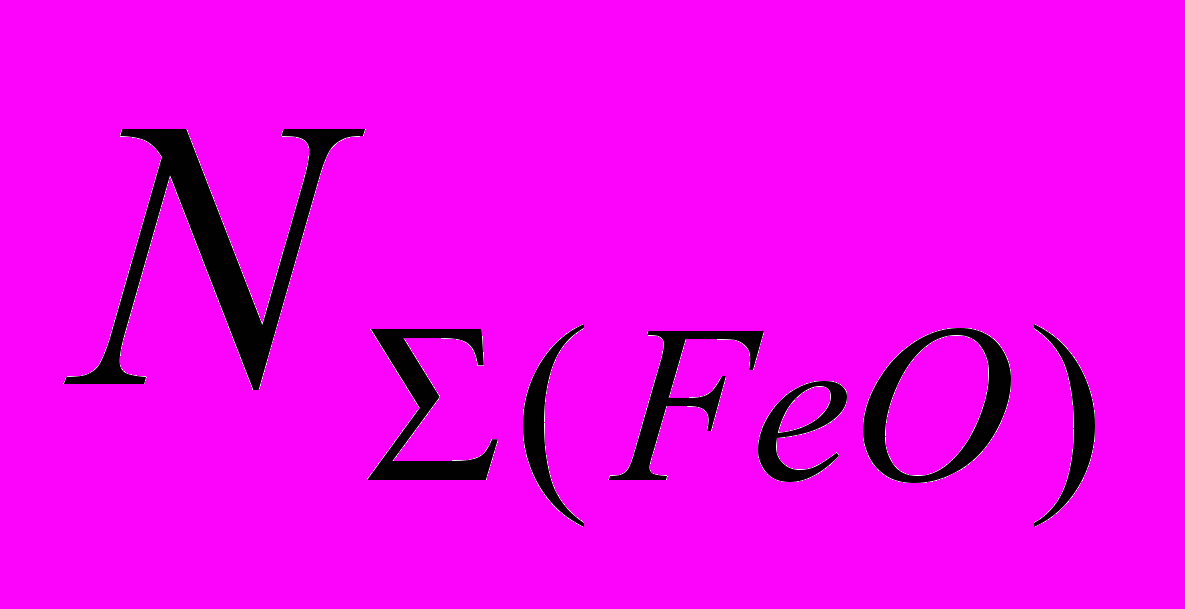
Получим зависимость содержания оксидов железа от общей окисленности электропечного шлака:
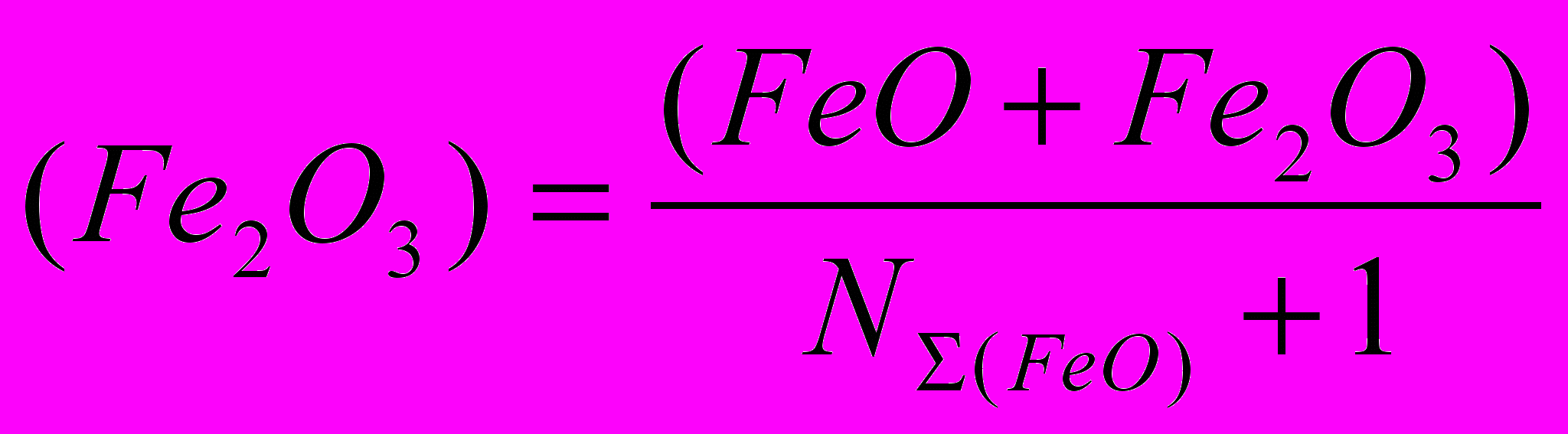

Таким образом, появляется возможность оценки потерь железа в современном электросталеплавильном процессе (рисунок 3).

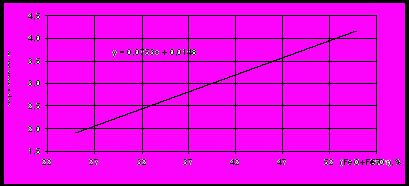
Рисунок 3 – Зависимость потерь железа с его оксидами в шлаке от общей окисленности шлака современной ДСП
В ДСП предусмотрены инжекторы для вспенивания шлака и восстановления оксидов железа. Вдувают 5 – 6 кг/т углеродсодержащего материала в струе воздуха, однако эффективность вспенивания (взаимодействия этого материала с оксидами железа) неудовлетворительна. На это указывает отсутствие зависимости общей окисленности шлака от расхода вдуваемого углерода. Анализ отходящих газов в тот же период плавки показал резкий скачёк содержания оксидов углерода (особенно СО) и увеличение температуры (рисунок 4, 5).

Рисунок 4 – Состав отходящих газов по ходу плавки № 450818:

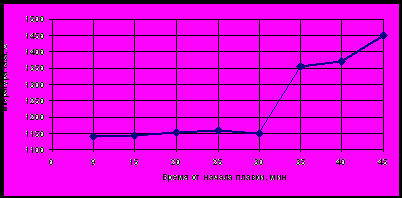
Рисунок 5 – Изменение температуры отходящего газа по ходу плавки № 450818
Фактически в газоходе-охладителе газоочистки вместо охлаждения продолжаются экзотермические реакции окисления углерода и дожигания его монооксида. В итоге, к блокам рукавных фильтров подходит газ с температурой 180 0С и выше, что значительно больше допустимого, фильтры выходят из строя.
Установлено, что при окисленности шлака более 40 % (особенно более 50 %), затруднена кампания по его вспениванию. Это приводит к увеличенному расходу электроэнергии (рисунок 6).
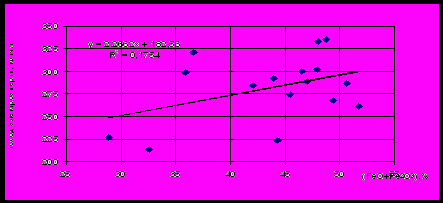
Рисунок 6 – Зависимость удельного расхода электроэнергии от общей окисленности шлака
Эта зависимость согласуется с литературными данными о рациональной общей окисленности электропечного шлака в пределах 25-35 %. Полученные экспериментальные данные свидетельствуют о том, что в действующей технологии рабочая область окисленности шлака электропечи не соответствует рациональной. Требуется удерживать общую окисленность шлака не более 40 %, а содержание (Fe2O3) не более 10 %. Отмечено, что основность шлака в экспериментальных пробах составляла 1,8 – 2,0, что по литературным данным соответствует рекомендуемой для его хорошего вспенивания.
Проведённые промышленные исследования позволили получить новые данные, и появилась возможность для разработки уточнённого математического описания современного процесса выплавки стали в дуговых электропечах.
В третьей главе приводится математическое моделирование процесса выплавки стали в современной дуговой электропечи. В качестве основы для создания математической модели плавки стали в современной ДСП были выбраны многолетние разработки в области моделирования сталеплавильных процессов на кафедре металлургии чёрных металлов ГОУ ВПО «МГТУ им.Г.И. Носова» под руководством А.М. Бигеева. Модель дополнена полученными в ходе промышленных исследований на ДСП данными (глава 2) по общему содержанию оксидов железа (FeO) и (Fe2O3), их соотношению, составу и температуре отходящих газов, потерям железа, основности шлака и удельному расходом электроэнергии. В расчёте учитываются влияния современных способов интенсификации плавки на структуру материального и теплового балансов. Предусмотрена возможность применения железосодержащего сырья с разной степенью металлизации и рассчитывается склонность шлака к вспениванию.
Большинство параметров плавки рассчитывали по уравнениям, входящим в базовую модель А.М. Бигеева. В соответствии с особенностями плавки стали в современной электродуговой печи в модель были внесены ряд дополнений и изменений.
В случае необходимости расчёта плавки с применением брикетов металлизованного сырья (как частичных заменителей лома) вводится коэффициент пересчёта К1:
При замене 1 кг лома

где
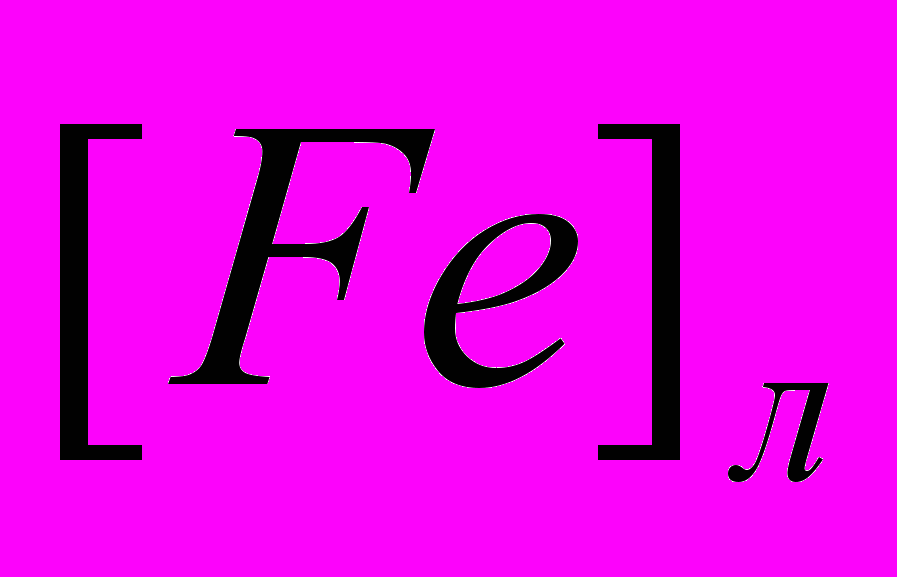
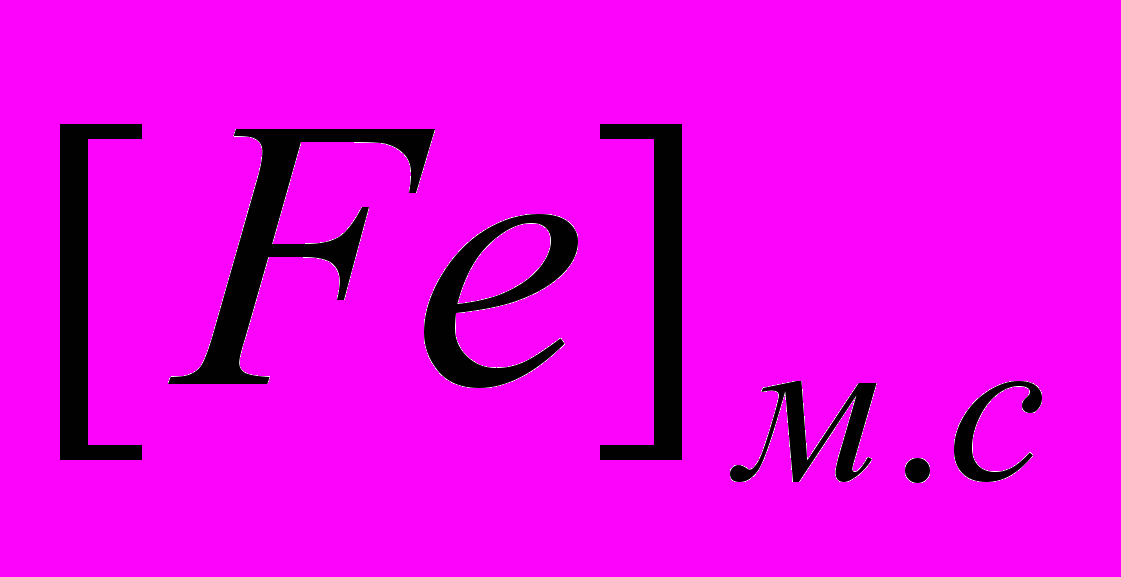
Расход брикетов металлизованного сырья на плавку

где
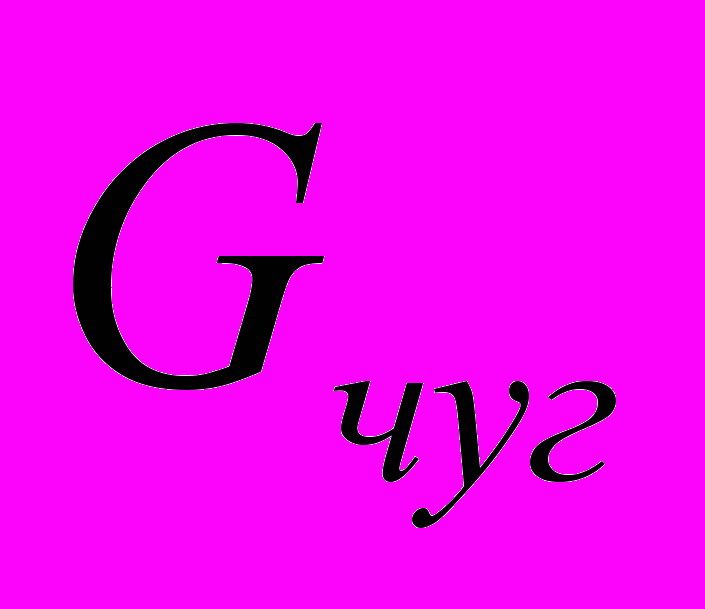
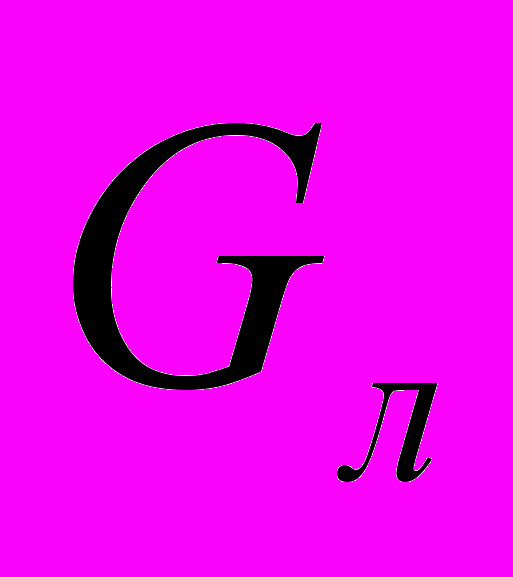
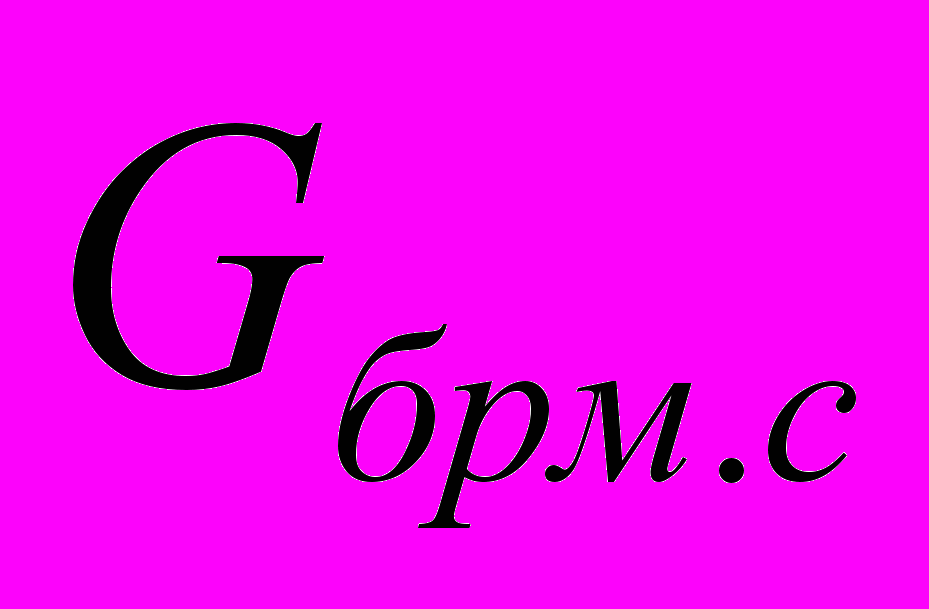
Для оценки вспенивания шлака используется индекс вспенивания. Он имеет размерность времени, а физический его смысл может быть определён как время прохождения пузырька газа через слой шлака по формуле (8):
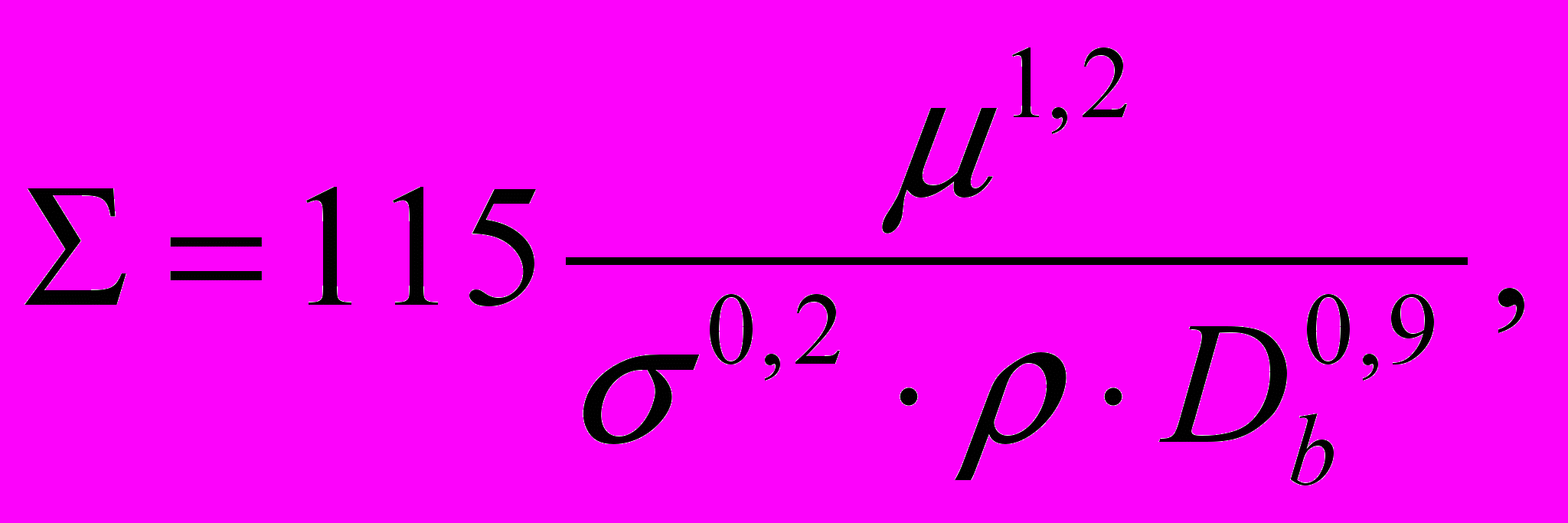
где
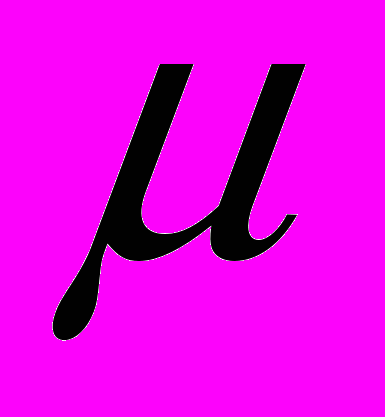

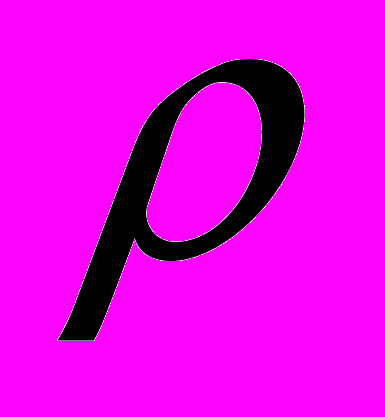
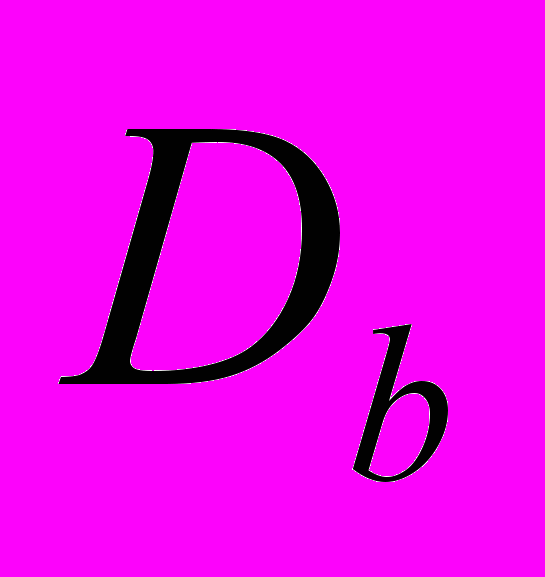
Плотность шлака определяется по формуле

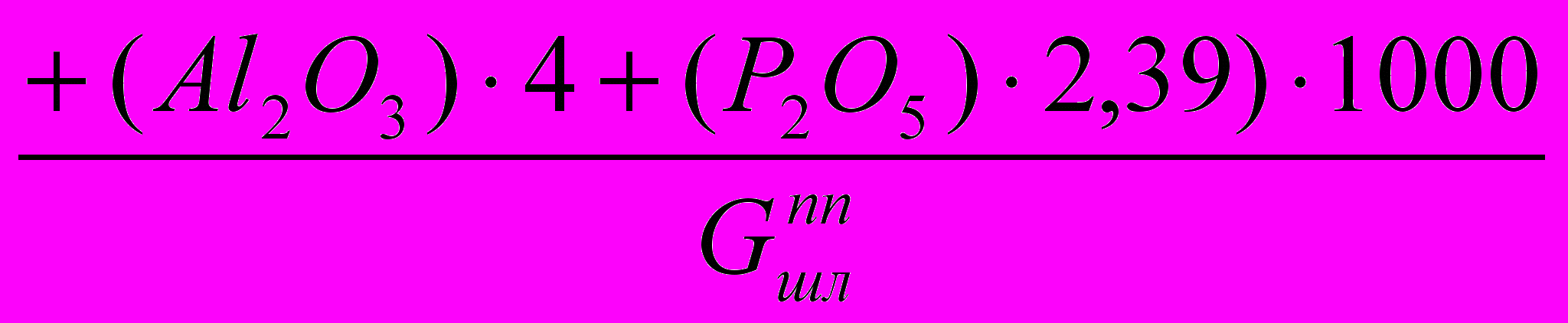
а поверхностное натяжение:

Вязкость шлака принимается по известным зависимостям от температуры.
Определим коэффициент вспенивания шлака fr как отношение объёма пены, состоящей из объёма вспенивающего газа и объёма шлака, к объёму шлака в невспененном состоянии по формуле:

Объём шлака составит
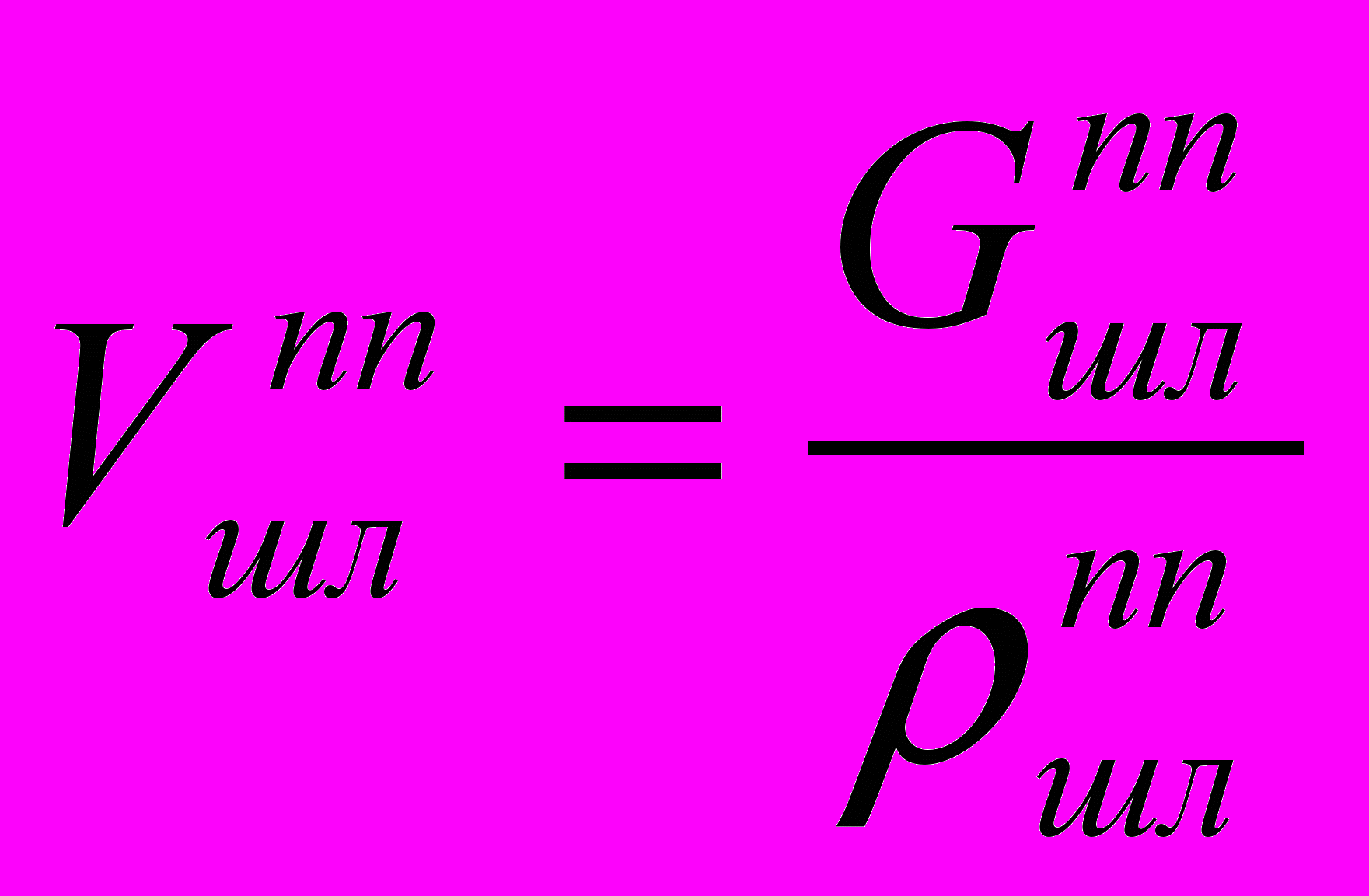
а высота шлака в печи составит
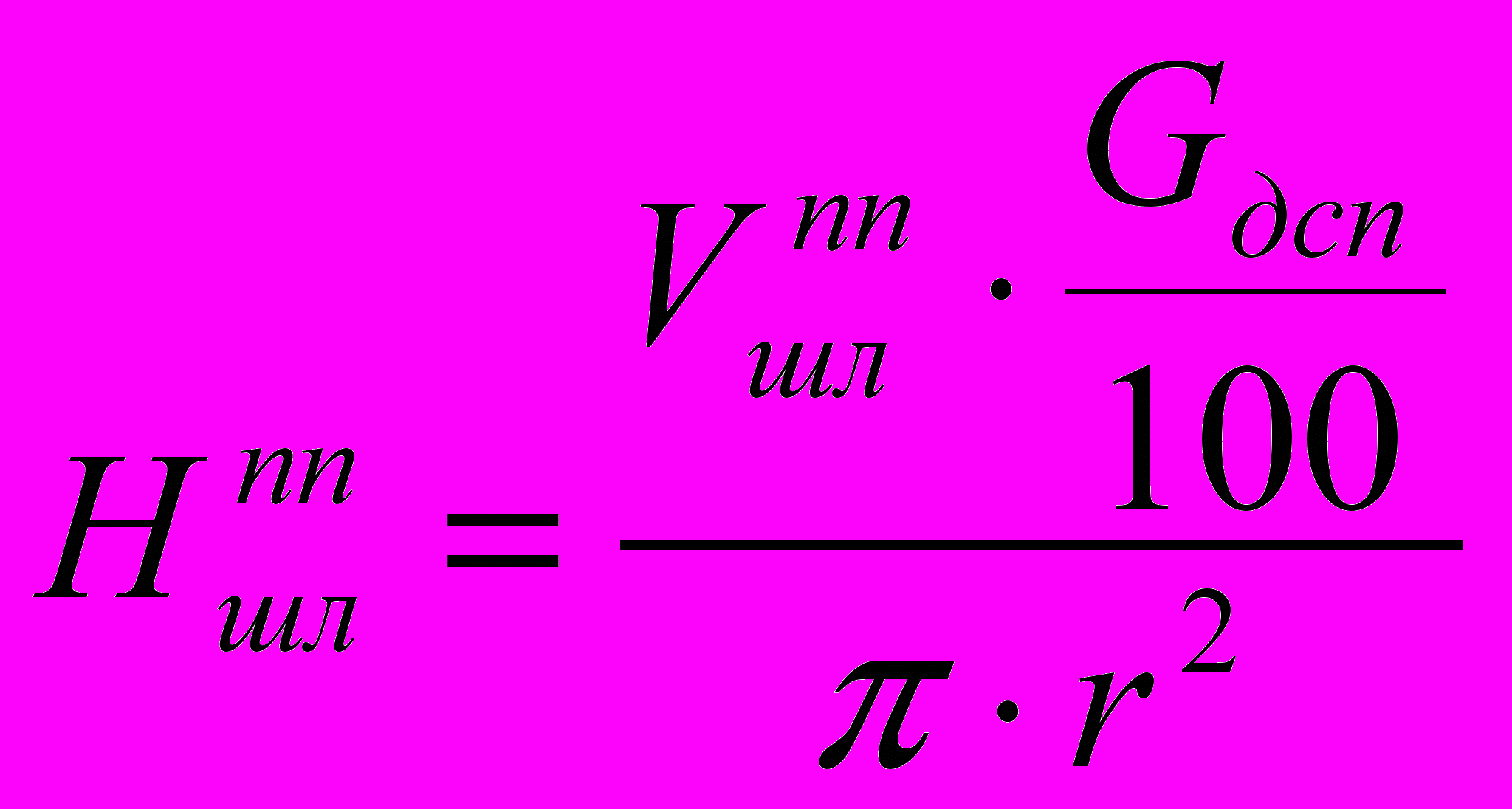
а объём вспенивающего газа составил
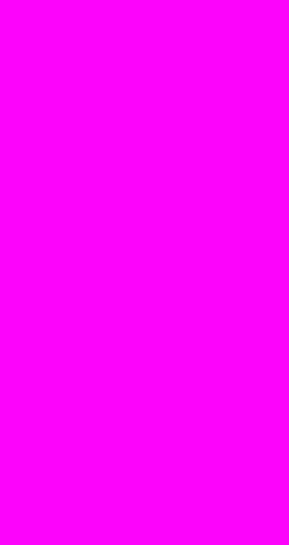
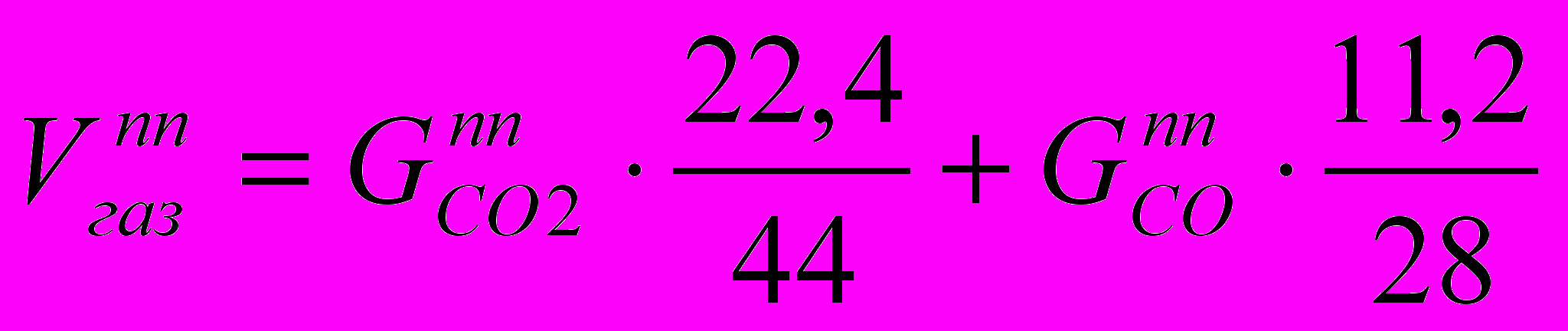
В тепловом балансе современной плавки в ДСП также произошли значительные изменения, связанные, прежде всего, с использованием водоохлаждаемых элементов в конструкции печи, применением топливно-кислородных устройств и инжекторов для вспенивания шлака, наличием «болота», а в ряде случаев работой на жидком чугуне и металлизованном сырье.
Математическая модель уточнена по температуре и составу отходящих газов, по роли тепловых эффектов реакций окисления железа до (FeO) и (Fe2O3) и вдуваемого углерода.
Полученная математическая модель технологии выплавки стали в современной ДСП послужила основой для создания мультимедийной обучающей системы «Сталевар ДСП». В настоящее время программный комплекс «Сталевар ДСП» успешно внедрён в процесс обучения производственного персонала ОАО «ММК» и студентов металлургических специальностей ГОУ ВПО «МГТУ им.Г.И. Носова».
В четвертой главе приводятся результаты исследования трёх видов железосодержащего сырья с разной степенью металлизации в качестве компонентов шихты для ДСП-180 ЭСПЦ ОАО «ММК». Исследование этих материалов проводилось в три этапа:
1. Математическое моделирование плавки (с помощью модели, полученной в главе 3) в условиях ДСП-180 ОАО «ММК» с целью определения целесообразности применения разных шихтовых материалов
2. Лабораторные эксперименты с целью горячего физического моделирования плавок с различной шихтовкой.
3. Промышленные плавки в условиях ЭСПЦ ОАО «ММК».
Приводятся результаты математического моделирования и лабораторных испытаний брикетов металлизованного сидеритового сырья Бакальского месторождения, брикетированной окалины прокатных цехов ОАО «ММК» и результаты математического моделирования, лабораторных и промышленных испытаний горячебрикетированного железа (ГБЖ) производства ОАО «Лебединский ГОК».
Лабораторные эксперименты проводились на базе кафедры электрометаллургии и литейного производства ГОУ ВПО «МГТУ им.Г.И. Носова» в электропечи ёмкостью 12 кг. Базовая шихтовка составляла 75 % стального лома и 25 % чугуна. Далее шихтовка лабораторных плавок менялась согласно данным, полученным с применением математической модели. Часть лома заменялась исследуемыми альтернативными материалами.
Из проведённых опытных плавок сделано заключение о минимально допустимой степени металлизации 85 % в железосодержащем материале при максимально допустимом уровне содержания оксидов железа – 15%. Выполнение этих условий способен обеспечить производитель ГБЖ – ОАО «Лебединский ГОК».
Результаты опытных промышленных плавок согласуются с результатами математического моделирования и лабораторных исследований (таблица).
Таблица – Химический состав металла-полупродукта, %
Вид | Шихтовка плавки, % | Состав металла на выпуске, % | ||||||||
лом | чугун | ГБЖ | С | Mn | S | P | Cr | Ni | Cu | |
Расч. | 100 | 0 | 0 | 0,040 | 0,068 | 0,030 | 0,021 | 0,046 | 0,078 | 0,220 |
Пром. | 100 | 0 | 0 | 0,042 | 0,044 | 0,060 | 0,018 | 0,051 | 0,091 | 0,188 |
Расч. | 75 | 25 | 0 | 0,050 | 0,084 | 0,035 | 0,040 | 0,039 | 0,065 | 0,160 |
Пром. | 75 | 25 | 0 | 0,074 | 0,068 | 0,037 | 0,050 | 0,048 | 0,096 | 0,173 |
Расч. | 60 | 25 | 15 | 0,050 | 0,055 | 0,040 | 0,017 | 0,036 | 0,043 | 0,130 |
Лаб. | 60 | 25 | 15 | 0,890 | 0,320 | 0,053 | - | 0,048 | 0,077 | 0,170 |
Пром. | 60 | 25 | 15 | 0,060 | 0,043 | 0,047 | 0,008 | 0,044 | 0,089 | 0,182 |
Примечание: Расч. – расчётная, Пром. – промышленная, Лаб. – лабораторная плавка.
Показана принципиальная возможность использования ГБЖ в количестве до 50 тонн на плавку, что позволяет получать кондиционный металл с пониженным содержанием фосфора и остаточных элементов по сравнению с обычными плавками.
В 2010 году на ДСП-180 ЭСПЦ ОАО «ММК» была успешно переработана промышленная партия ГБЖ ОАО «Лебединский ГОК». Материал подавался в завалку вместе с ломом в количестве 20 – 30 т.
ОБЩИЕ ВЫВОДЫ
1. Промышленные исследования в условиях действующего производства на современной ДСП-180 ЭСПЦ ОАО «ММК» позволили определить ранее неизвестное соотношение оксидов железа (FeO) и (Fe2O3) в шлаке, состав и температуру отходящих газов. Выявлено, что в действующей технологии ДСП-180 ЭСПЦ ОАО «ММК», рабочая область общей окисленности шлака (45–52 %) электропечи не соответствует рациональной.
2. Для хорошего вспенивания шлака и максимально эффективного использования электрической энергии дуги требуется удерживать общую окисленность шлака в пределах 30–40 %, а содержание (Fe2O3) не более 10 %. Даны рекомендации по совершенствованию процесса вдувания углеродсодержащего материала для вспенивания шлака. Произведена оценка склонности шлака разного химического состава к вспениванию.
3. Математическая модель плавки стали в современной дуговой электропечи дополнена полученными в ходе промышленных исследований на ДСП данными по общему содержанию оксидов железа (FeO) и (Fe2O3), их соотношению, составом и температурой отходящих газов, потерями железа, основностью шлака и удельным расходом электроэнергии. В модели учитывается влияния современных способов интенсификации плавки на материальный и тепловой баланс. Появилась возможность расчёта применения различных видов шихты, в том числе железосодержащего сырья с разной степенью металлизации.
4. Полученная математическая модель технологии выплавки стали в современной ДСП, послужила основой для создания мультимедийной обучающей системы «Сталевар ДСП». В настоящее время программный комплекс «Сталевар ДСП» успешно внедрён в процесс обучения производственного персонала ОАО «ММК» и студентов металлургических специальностей ГОУ ВПО «МГТУ им.Г.И. Носова».
5. С помощью модернизированной математической модели современной электродуговой плавки были реализованы лабораторные и промышленные эксперименты по изучению трёх видов железосодержащего сырья с разной степенью металлизации в качестве шихты для ДСП-180 ЭСПЦ ОАО «ММК». Сделан вывод о минимально допустимой степени металлизации 85 % в железосодержащем материале, при максимально допустимом уровне содержания оксидов железа 15 %.
Основное содержание работы отражено в следующих публикациях:
1. Особенности работы ДСП на длинных дугах / В.А. Бигеев, А.Е. Малофеев, А.В. Пантелеев и др. // Вестник МГТУ им. Г.И. Носова. – Магнитогорск: ГОУ ВПО «МГТУ». – 2006. – № 4 (16). – С. 20 – 21.
2. Регулирование окисленности шлака по ходу плавки в современной дуговой печи / В.А. Бигеев, А.Е. Малофеев, А.В. Пантелеев // Сталь- 2009.-№3-С.89.
3. Изучение поведения химических элементов при выплавке полупродукта в сверхмощной дуговой сталеплавильной печи с различным расходом жидкого чугуна / Л.В. Алексеев, А.М. Столяров, А.Е. Малофеев и др. // Вестник МГТУ им. Г.И. Носова. – Магнитогорск: ГОУ ВПО «МГТУ». – 2009. – № 1 (25). – С. 38 – 41.
4. Особенности материального и теплового балансов ДСП-180 ОАО «ММК» / У.Б. Ахметов, А.Е. Малофеев, А.В. Пантелеев и др. // Теория и технология металлургического производства: Межрегион. сб. науч. тр. / Под ред. В.М. Колокольцева. – Вып. 7. – Магнитогорск: ГОУ ВПО «МГТУ» – 2007. – С. 84 – 87.
5. Совершенствование процесса вспенивания шлака в ДСП / Бигеев В.А., Малофеев А.Е. // Тезисы докладов научно-технической конференции молодых специалистов – Магнитогорск: ОАО «ММК» - 2007 – С. 30-32.
6. Поведение углерода в современной ДСП / Пантелеев В.А., Малофеев А.Е. // Тезисы докладов научно-технической конференции молодых специалистов – Магнитогорск: ОАО «ММК» - 2006 – С. 45-47.
7. Особенности шлакового режима при выплавке стали в современной ДСП / Бигеев В.А., Пантелеев А.В., Малофеев А.Е. // Материалы III Конгресса металлургов Урала – Челябинск: 2008 – С. 89-91.
8. Анализ особенностей материального и теплового балансов ДСП-180 ОАО «ММК» / Малофеев А.Е., Бигеев В.А., // Тезисы докладов научно-технической конференции молодых специалистов – Магнитогорск: ОАО «ММК» - 2008 – С. 36-37
9. Совершенствование процесса вспенивания шлака в дуговых сталеплавильных печах Бигеев В.А., Малофеев А.Е. // Материалы 65-й научно-технической конференции: Сб. докл. – Магнитогорск: ГОУ ВПО «МГТУ». – 2007. – Т. 1. – 234 с.
10. Окисленность шлака в современной дуговой сталеплавильной печи / Бигеев В.А., Малофеев А.Е., Пантелеев А.В. // Материалы Х Международного конгресса сталеплавильщиков.- Магнитогорск - 2008.
11. Регулирование окисленности шлака по ходу плавки современной дуговой сталеплавильной печи / Бигеев В.А., Малофеев А.Е., Л.В. Алексеев // Материалы 67-й научно-технической конференции: Сб. докл. – Магнитогорск: ГОУ ВПО «МГТУ». – 2009. – Т. 1. – С. 74-76.
12. Регулирование окисленности шлака по ходу плавки современной дуговой сталеплавильной печи / Бигеев В.А., Малофеев А.Е., А.Н. Федянин // Теория и технология металлургического производства: Межрегион. сб. науч. тр. / Под ред. В.М. Колокольцева. – Вып. 9. – Магнитогорск: ГОУ ВПО «МГТУ» – 2009. – С. 44 – 46.
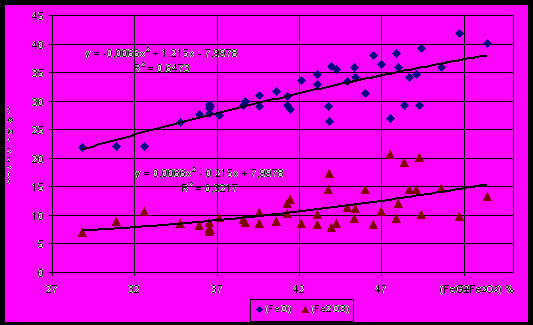