Учебное пособие для студентов г. Севастополь 2009
Вид материала | Учебное пособие |
- Учебное пособие для студентов среднего профессионального образования Санкт-Петербург, 2198.48kb.
- Учебное пособие для студентов среднего профессионального образования Санкт-Петербург, 2212.78kb.
- Учебное пособие для студентов среднего профессионального образования Санкт-Петербург, 1556.74kb.
- Учебное пособие для студентов среднего профессионального образования Санкт-Петербург, 1486.86kb.
- Учебное пособие для студентов среднего профессионального образования экономических, 4287.52kb.
- Учебное пособие для студентов среднего профессионального образования экономических, 3683.83kb.
- Учебное пособие для студентов среднего профессионального образования экономических, 933.21kb.
- Учебное пособие Санкт-Петербург 2009 удк 802., 485.15kb.
- Учебное пособие Тамбов 2009 удк 339. 138, 1882.57kb.
- Учебное пособие по курсам «Экономика отрасли» и "Инвестиционный менеджмент" для студентов, 4819.39kb.
1.3.1 Показатели мощности
Мощность измеряется в кВт, а к абсолютным показателям мощности относятся:
- суммарная мощность главных двигателей СЭУ, NеГД;
- эффективная мощность, которая передается от ГЭУ валопроводу, NеУ;
- мощность, подведенная к винту, NвУ;
- мощность судовой электростанции, NСЭС.
Для СЭУ с прямой передачей от главных двигателей к винтам эффективная мощность ГЭУ NеУ и NвУ определяются соотношениями:
NеУ= NеГД; NвУ= NеУвп,
где вп – КПД водопровода.
Для СЭУ с непрямой передачей
NеУ= NеГДп,
где п – КПД передачи.
Буксировочнная мощность или мощность полезной тяги для судна в целом определяется по формуле:
NR= NеУвп= NеГДпвпвк,
где - пропульсивный коэффициент (=NR/Nв); в – КПД винта; к – коэффициент влияния корпуса судна на работу винта.
Относительные показатели мощности СЭУ:
- энергонасыщенность судна N, которая определяется по формуле:
N= NеУ/D или N= NвУ/D, кВт,
где D – полное водоизмещение судна, т;
- относительная мощность СЭС:
е=NСЭС/ NеУ;
- степень электрофикации судна:
ес= NСЭС/Dпор, кВт/т,
где Dпор – водоизмещение судна порошнем, т.
Таблица 1.1 Относительные показатели мощности СЭУ отдельных типов морских судов
№ п/п | Типы судов | N кВт/т | е |
1 | Пассажирские и грузопассажирские | 0,8…1,7 | 0,2…0,3 |
2 | Универсальные сухогрузы | 0,3…0,7 | 0,15…0,25 |
3 | Танкеры | 0,1…0,3 | 0,1…0,2 |
4 | Средние морозильные траулеры | 0,55…0,81 | 0,4…0,5 |
5 | Большие морозильные траулеры | 0,30…0,55 | 0,7…1,3 |
6 | Промыслово-производственные рефрижераторы | 0,39…0,41 | 0,57…0,7 |
- Показатели массы
К абсолютным показателям массы СЭУ относятся:
- сухая масса установки (масса всех элементов без воды, масел и топлива), Gcy, т;
- масса установки в рабочем состоянии (с водой, топливом и маслом в элементах и трубопроводах), Gy, т;
- масса запасов топлива, масла и технической воды, Gз, т;
- полная масса установки с запасами, Gyз, т.
В Gyз входят:
- масса машинной установки (двигателей, генераторов рабочего тела, передач, валопроводов, движителей, вспомогательных установок, теплообменных аппаратов, трубопроводов, систем управления и контроля, запасных частей СЭУ;
- масса всех жидкостей в механизмах, аппаратах и трубопроводах СЭУ;
- масса предметов для ремонта СЭУ (инструмент, расходные материалы и вещества);
- масса энергетических запасов (топлива, масла технической воды).
В качестве удельного массового показателя СЭУ используется:
me= Gcy/Ney, кг/кВт.
В таблице 1.2 приведены значения me для различных типов СЭУ.
Таблица 1.2 Значения удельного массового показателя для различных типов СЭУ.
Типы СЭУ | me, кг/кВт |
Дизельная с малооборотным двигателем и прямой передачей | 80…100 |
Дизель-редукторная среднеоборотная | 60…70 |
ПТУ транспортных судов | 50…60 |
Газотурбинная: для транспортных судов для быстроходных для судов на воздушной подушке для судов на подводных крыльях | 25…35 5…10 2…3 1,2…1,5 |
Другим относительным (удельным) показателям СЭУ является относительная масса энергетических запасов.
З=G З/DУ
Масса энергетических запасов G З судов дальнего плавания, как правило, превышает массу СЭУ в рабочем состоянии (G У).
- Габаритные показатели СЭУ
Основными габаритными показателями СЭУ является площадь машинного отделения, FМО, м2 и объем VМО, м3 машинного отделения, а также протяженность машинного отделения по длине судна, L МО, м.
Машинное отделение, как правило, располагается в основном корпусе судна. Объем помещений для СЭУ определяется с учетом особенностей установки, ее типа, а также типа главной передачи. Так, для морских транспортных судов с дизельными и паротурбинными установками относительный объем помещений СЭУ, как правило, составляет 0,35…0,7 м3/кВт, а для судов на воздушной подушке и на подводных крыльях на порядок меньше, т.е. 0,03…0,07 м3/кВт.
Относительными габаритными показателями СЭУ являются:
- относительная длина машинного отделения:
lу=LMO/L,
где L – длина судна между перпендикулярами, м;
- энергонасыщенность помещений СЭУ по длине nL, кВт/м, по площади палубы nF кВт/ м2 и по объему nV, кВт/ м3, определяются по формулам:
nL=( Ney+NСЭС)/ LMO;
nF=( Ney+NСЭС)/F MO;
nV=( Ney+NСЭС)/V MO.
Зависимость энергонасыщенности машинного отделения от типа СЭУ показана в таблице 1.3.
Таблица 1.3
Тип СЭУ | nL, кВт/м | nF кВт/ м2 | nV, кВт/ м3 |
Дизельные малооборотные | 220…480 | 15…30 | 1,3…2,2 |
ПТУ с ГТЗД | 370…550 | 22…37 | 2,06…2,65 |
Применяются и другие показатели, характеризующие СЭУ. Они будут рассмотрены на 3-м курсе при детальном изучении существующих главных двигателей и вспомогательных механизмов.
2. ПАРОВЫЕ КОТЛЫ
2.1 История создания, устройство и принцип действия парового котла
2.1.1 История создания парового котла
Еще в древности человек научился использовать энергию огня – в начале для отпугивания хищников, охоты на диких животных, приготовления пищи и обогрева жилища. Затем, по мере совершенствования навыков, человек, став земледельцем, использовал огонь для выжигания участков леса с целью последующего использования земли для выращивания окультуренных растений и организации пастбищ для диких животных, на которых охотился, а в дальнейшем для одомашненного скота.
В этот же исторический период человек заметил, что при нагревании из воды получается пар. В глубокой древности появились простейшие устройства для получения пара. К таковым можно отнести, например, шар Герона Александрийского. Однако, в течение многих столетий, вплоть до конца XVI – начала XVII веков энергия водяного пара практически не использовалась. Немногочисленные паровые водоподъемники, действовавшие в те времена, не имели собственного генератора пара – парового котла.
Впервые паровой котел как генератор пара был отделен от исполнительного механизма в 1600 г. в установке Джамбатиста дела Порта, предназначенной для подъема воды. Однако отсутствие в то время универсального парового двигателя тормозило развитие паровых котлов.
Развитие паровых котлов как самостоятельных агрегатов начинается с момента изобретения первого универсального двигателя – паровой машины, сконструированной и построенной российским изобретателем И.И.Ползуновым в 1763 – 1765 годах на алтайских заводах. Котел И.И. Ползунова имел уже основные элементы, присущие любому паровому котлу.
Исключительно мощным подъемом пароэнергетики был ознаменован XIX в. – «век пара».
На основе паровых двигателей, превращающих тепловую энергию в механическую работу было организовано производство XIX века. Развитие крупной промышленности потребовало расширения рынков и быстрой, безопасной и массовой переброски сырья и товаров. Как отметил в это время Ф.Энгельс: «Пар произвел переворот в путях сообщения не только на Земле, но и на воде».
Началом внедрения пара на морских судах считается постройка Фултоном в 1807 г. парохода «Клермонт». На этом деревянном судне с машинной мощностью в 20 лс. (1 лс. = 0,735 кВт) был установлен небольшой котел с кирпичной обмуровкой, в котором сжигались дрова.
Первый русский пароход «Елизавета» совершил рейс от Петербурга до Кронштадта 3 ноября 1815 г. А в период 1815-1822 гг. было построено еще несколько пароходов, на которых устанавливались медные и железные коробчатые котлы с давлением пара 0,2…0,3 ат (1 ат = 98066,5 Па).
Через 20 лет после постройки первого парового судна в мировом флоте насчитывалось уже около тысячи пароходов и их рост стал обгонять рост числа парусных судов.
В связи с применением в качестве топлива дров, а также малой надежности таких СЭУ в начале XIX в. океанские пароходы были парусно-паровыми. До середины XIX в. питание котлов осуществлялось в основном морской водой. Образующаяся при этом в большом количестве накипь на поверхности нагрева вызывала перегрев стенок и нередко приводило к взрывам котлов. Постройка во 2-й половине XIX в. стальных цилиндрических котлов и применение для их питания конденсата пара (пресной воды) дали возможность повысить давление до 5-7 ат и уменьшить тем самым опасность взрыва.
В 70-х годах XIX в. появились судовые огнетрубные оборотные котлы, в которых применен перегрев пара, а в дальнейшем – подогрев подаваемого в топку воздуха, необходимого для сжигания топлива.
В конце XIX в. появилась паровая турбина и выяснилось, что огнетрубный котел не может удовлетворить потребности турбины в паре повышенных параметров. Необходим был водотрубный котел и к началу XXв. насчитывалось уже около 50-ти конструкций водотрубных котлов.
Большой вклад в совершенствование котельной техники принадлежит российским ученым и инженерам. Например, инженер, а в дальнейшем академик АНСССР В.Г.Шухов создал оригинальную конструкцию мощного водотрубного котла, который затем копировали на Западе. Котлы конструкции Долголенко В.Я. были установлены на ряде кораблей военного флота, в том числе на крейсере «Аврора».
Отечественной науке и технике принадлежит заслуга в решении проблем сжигания жидкого топлива в топках котлов. Так, способ сжигания жидкого топлива распылением был впервые предложен в 1865 г. А.И.Шпаковским. В конце XX в. коллектив инженеров Тентелевского завода создал первую форсунку с механическим распылом жидкого топлива.
Следует отметить, что серьезный вклад в совершенствование паровых котлов внес прославленный адмирал Русского флота С.О.Макаров, именем которого названы Государственная морская Академия в Санкт-Петербурге, Государственный кораблестроительный институт в Николаеве, Высший Военно-морской институт во Владивостоке.
Что же предложил и сделал С.О.Макаров?
- Разработал устройства и способы ускоренной разводки пара в корабельных паровых котлах, что было важно для боевых кораблей, на которых подъем температуры воды в котлах до 100ºС занимал целый час, а с внедрением устройства Макарова – всего 10-20 минут.
- Добился повышения экономичности паровых установок за счет внедрения ступенчатого использования пара.
- Предложил использовать в качестве топлива для паровых котлов нефтяные остатки – мазут. В результате именно русский флот первым стал использовать жидкое топливо в котельных агрегатах.
Начиная с конца 30-х годов XX в. и особенно после окончания Великой Отечественной войны большое развитие получило морское котлостроение.
Освоение котельной техники и ее эксплуатация в сложных условиях морского плавания требует глубоких знаний теории современной судовой теплоэнергетики. Такие знания студенты получают при изучении дисциплины «Техническая термодинамика» и «Теплопередача» на 3 курсе.
2.1.2 Устройство и принципы действия парового котла
Паровым котлом называется агрегат, предназначенный для непрерывного производства (генерации) пара за счет превращения какого-либо вида энергии в тепловую.
В любом котле имеется топка (рисунок 2.1), предназначенная для сжигания топлива в потоке специально подводимого воздуха. Воздух, расходуемый на горение топлива для лучшего сгорания, как правило, предварительно подогревается.
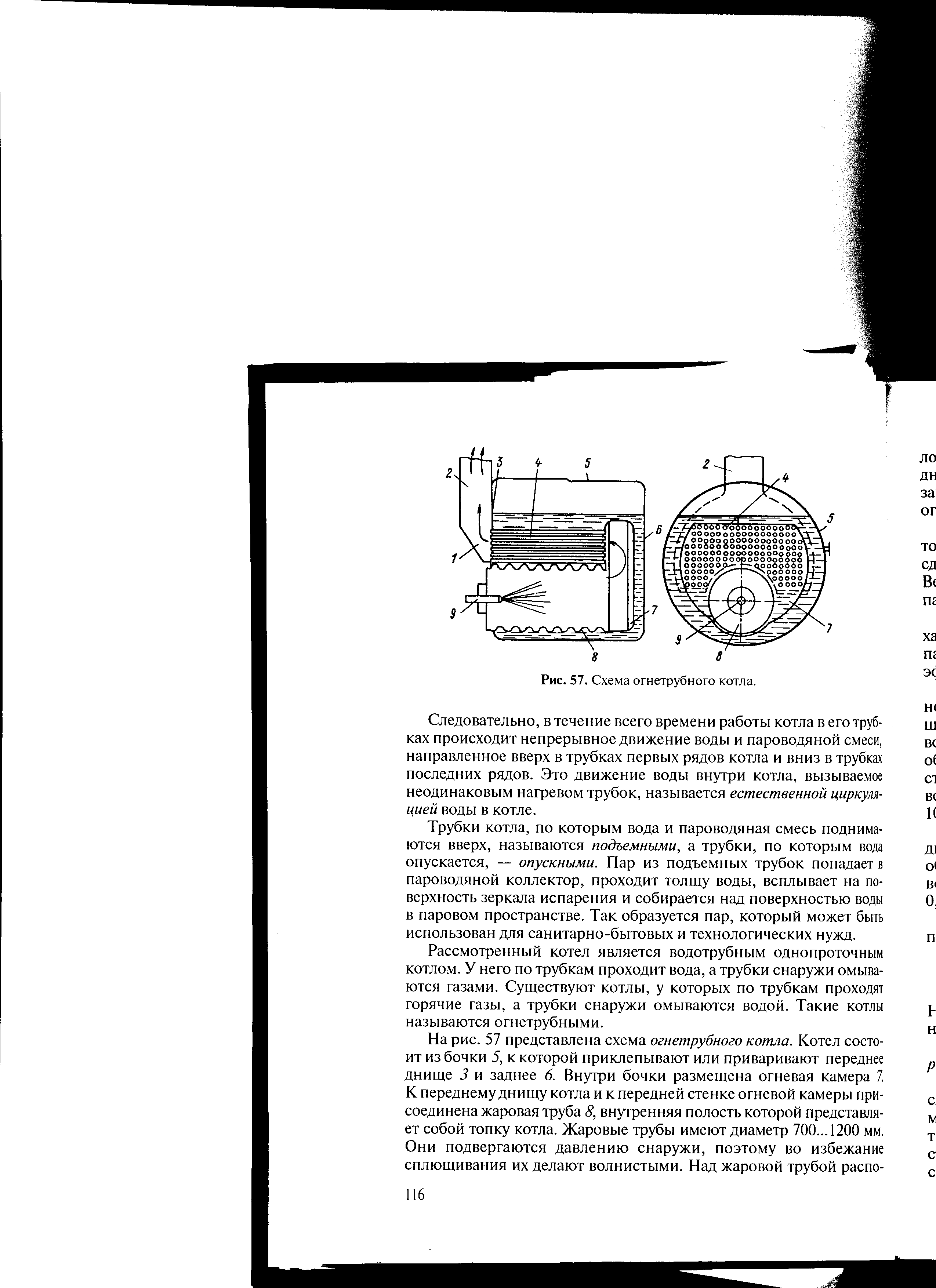
Рисунок 2.1 Схема огнетрубного котла: 1 – дымовая коробка; 2 – дымовая труба; 3 – переднее днище; 4 – дымогарные трубы; 5 – корпус; 6 – заднее днище; 7 – огневая камера; 8 – жаровая труба; 9 – форсунка.
В результате горения в топке образуются газообразные продукты сгорания, теплота которых за счет теплопроводности передается рабочей среде (воде, пару) через поверхность нагрева котла.
Все паровые котлы в зависимости от организации потоков рабочего тела разделяются на огнетрубные и водотрубные.
В огнетрубных котлах горячие газы проходят внутри труб, а вода находится между ними.
В водотрубных котлах пламя и горячие газы омывают трубы снаружи, а внутри труб перемещается нагреваемая рабочая среда – вода и пар (за счет естественной тепловой конвекции).
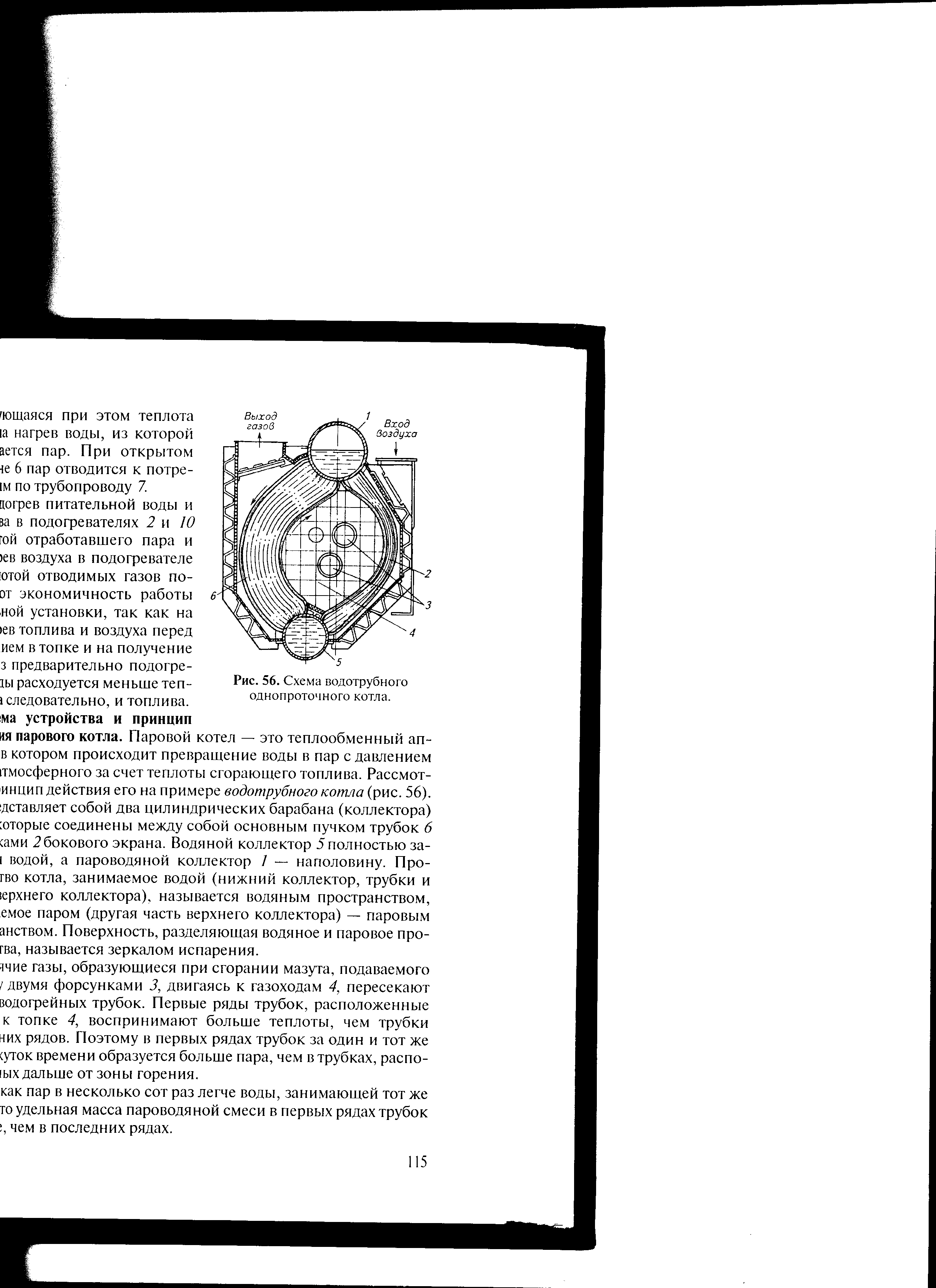
Рисунок 2.2 Схема водотрубного однопроточного котла:
1 – пароводяной коллектор; 2 – трубы бокового экрана; 3 – форсунки; 4 – топка; 5 – водяной коллектор; 6 – основной пучок труб.
В том и другом случае получается пар, имеющий высокую температуру и избыточное давление, который в дальнейшем приводит в действие паровую машину (поршневую) или турбину, а также используется для общесудовых нужд (нагрев воды, масла, топлива, в системе кондиционирования и т.д.).
2.2 Классификация морских паровых котлов
Судовые паровые котлы классифицируются по ряду признаков:
- по назначению – главные паровые котлы, вырабатывающие пар, используемый в главных паровых турбинах; вспомогательные и утилизационные котлы, вырабатывающие пар для вспомогательных и технологических нужд (отопления, душевых, обогрева судовых систем, обработка рыбы и т.п.);
- по конструкции – огнетрубные, водотрубные, комбинированные (соединяющие в себе элементы огнетрубных и водотрубных);
- по роду используемого топлива – котлы, работающие на мазуте, либо утилизационные котлы (использующие теплоту отходящих газов дизелей
или других тепловых машин);
- по типу циркуляции воды и пароводяной смеси – котлы с естественной циркуляцией и котлы с принудительной циркуляцией (под действием специального насоса);
- по виду тяги – котлы с искусственной тягой (с помощью котельного вентилятора) и котлы с естественной тягой (с помощью дымовой трубы).
Рассмотрим особенности различных типов котлов.
Огнетрубные котлы. Основные преимущества огнетрубных котлов заключаются в следующем:
- малая чувствительность к резким колебаниям нагрузки (расхода пара) за счет большой аккумулирующей способности котла (количество воды в котле в несколько раз превышает его паропроизводительность);
- относительно малая чувствительность к качеству воды;
- длительный срок службы (до 40 лет);
- простота обслуживанием.
Недостатками огнетрубных котлов являются:
- невозможность получения пара давлением более 8 мПа;
- большая масса по сравнению с водотрубным котлом такой же паропроизводительности;
- жесткость конструкции не допускает быстрого подъема и снижения давления пара, т.к. возникновение температурных напряжений может привести к образованию трещин и появлению течи. Из-за этого недостатка на подъем давления пара до рабочего значения затрачивается до 12 и даже 24 часов;
- низкий коэффициент полезного действия;
- взрывоопасность при значительной силе возможного взрыва, что почти всегда приводит к гибели судна.
Перечисленные недостатки ограничивают применение огнетрубных котлов на судах морского и речного транспорта.
Водотрубные котлы являются более совершенными и это определяет их широкое применение на судах, включая промысловые суда.
Достоинства водотрубных котлов:
- удельный паросъем (количество пара, полученное с единицы площади нагрева) в 2…3 раза выше, чем у огнетрубных. Это объясняется лучшим теплообменом между горячими газами и водой. Так, общая паропроизводительность водотрубного котла в 10..15 раз выше максимальной паропроизводительности огнетрубного котла;
- масса и габариты водотрубных котлов в несколько раз меньше, чем огнетрубных такой же производительности;
- быстрый ввод в действие (минимальное время поднятие пара до рабочего давления составляют 1…1,5 часа);
- меньшая взрывоопасность (из-за малого объема воды, находящегося внутри котла).
Недостатки водотрубных котлов:
- невозможность получения пара давлением более 8 мПа;
- малая теплоаккумулирующая способность, что при резком изменении нагрузки отрицательно влияют на параметры пара;
- большая масса по сравнению с водотрубным котлом такой же паропроизводительности;
- жесткость конструкции не допускает быстрого подъема и снижения давления пара, т.к. возникновение температурных напряжений может привести к образованию трещин и появлении течи. Из-за этого недостатка на подъем давления пара до рабочего значения затрачивается до 12 и даже до 24 часов;
- низкий коэффициент полезного действия;
- взрывоопасность при значительной силе возможного взрыва, что почти всегда приводит к гибели судна.
Перечисленные недостатки ограничивают применение огнетрубных котлов на судах промыслового флота.
Водотрубные котлы являются более совершенными и это определяет их широкое применение на морском флоте, включая промысловые суда.
Достоинства водотрубных котлов:
- удельный паросъем (количество пара, получение с единицы площади нагрева) в 2…3 раза выше, чем у огнетрубных. Это объясняется лучшим теплообменом между горячими газами и водой. Так, общая паропроизводительность водотрубного котла в 10…15 раз выше максимальной паропроизводительности огнетрубного котла;
- масса и габариты водотрубных котлов в несколько раз меньше, чем огнетрубных такой же производительности;
- быстрый ввод в действие (минимальное время поднятия пара до рабочего давления составляет 1 – 1,5 часа);
- меньшая взрывоопасность (из-за малого объема воды, находящейся внутри водогрейных труб котла).
Недостатки водотрубных котлов:
- малая теплоаккумулирующая способность, что при резком изменении нагрузки отрицательно влияет на параметры пара;
- высокая чувствительность к качеству питательной воды. Так, при значительных отложениях накипи на поверхности нагрева создается опасность перегрева металла водогрейных труб и их разрыва;
- для обслуживания водотрубных котлов требуется более высокая квалификация персонала.
Вспомогательные котлы.
На судах дизельного флота необходим пар низкого давления для ответственных потребителей: подогревателей топлива, вспомогательных механизмов и хозяйственно-бытовых потребителей. Велика потребность в таком паре на танкерах для обеспечения работы грузовых насосов, обогрева груза и мойки танков, а также для бытовых нужд. На теплоходах для производства пара и воды устанавливаются вспомогательные котлы, называемые котельными агрегатами.
В зависимости от вида первичного энергоносителя вспомогательные котлы разделяют на автономные (вспомогательные), утилизационные и комбинированные. Автономные вспомогательные котлы работают на топливе, сжигаемом в их топках. Утилизационные котлы используют тепло выпускных газов дизелей. Это важно, так как потеря тепла с уходящими выпускными газами судовых дизелей составляет 25-30% от общего теплового баллона. Утилизация этого тепла необходима.
Утилизационные котлы различают по следующим признакам:
- по назначению – парогенераторы, парогенераторы-глушители, водогрейные, водогрейные-глушители;
- по виду – газотрубные и водотрубные;
- по виду теплоносителя – на выпускных газах дизеля или на выпускных газах и топливе, сжигаемом в топке котла (комбинированные).
Утилизационные котлы могут быть с ручным управлением и автоматизированные, а также огнетрубные и водотрубные. В связи с тем, что утилизационные котлы могут вырабатывать пар только во время работы главных дизелей, их объединяют со вспомогательными котлами в единую конструкцию. На ходу судна работают оба котла совместно, а на стоянке судна работает только вспомогательный котел, а утилизационный отключается.
В качестве вспомогательных и утилизационных применяется множество типов котлов.
2.3 Основные характеристики паровых котлов
Работу и эффективность любого парового котла характеризуют рядом основных показателей. Рассмотрим основные из них.
Поверхность нагрев, F – это площадь поверхности всех металлических стенок котла, которая с одной стороны обогревается пламенем горящего топлива и дымовыми газами, а с другой стороны омывается водой, из которой в результате нагрева образуется пар. Поверхность нагрева позволяет судить о размерах котла и измеряется в м2 со стороны обогрева пламенем и газом. На современных судах поверхность нагрева, например, вспомогательных паровых котлов составляет 10…100 м2.
Паропроизводительность, D – это количество пара, производимого котлом в единицу времени при заданных параметрах пара. Паропроизводительность вспомогательных судовых котлов составляет 0,5…12 т/ч, а утилизационных – до 250 кг/ч.
Удельный паросъем, d – количество пара, получаемого в котле с 1 м2 поверхности нагрева в единицу времени:
d = D/ F, т/м2.ч) или Кт/(м2.с),
где d – удельный паросъем; D – паропроизводительность, кг/ч или т/ч; F – поверхность нагрева, м2.
Удельный паросъем d характеризует интенсивность производства пара. На современных судах с каждого м2 поверхности котла снимается до 60 кг пара в час, т.е. d=60 кг/ м2.ч.
К параметрам пара относятся рабочее давление P, мПа и температура пара t, ºС.
Коэффициент полезного действия (КПД) является основной качественной характеристикой, отражающей экономичность работы парового котла. Он представляет собой отношение теплоты, использованной для получения пара, ко всему количеству теплоты, выделившейся при сгорании топлива в топке. Для судовых котлов КПД равен 0,75…0,93. Это значит, что 75…93% теплоты, полученной от сжигания топлива, затрачивается на создание пара, а от 7 до 25% теплоты теряется с уходящими дымовыми газами или излучается в окружающую среду.
3. ПАРОТУРБИННЫЕ УСТАНОВКИ
3.1 Назначение, состав и принципиальная схема ПТУ.
Паротурбинная установка предназначена для обеспечения движения судна, а также для приведения в действие вспомогательных механизмов и агрегатов за счет энергии пара.
Основными элементами главной ПТУ являются: паровой котел (парогенератор – на атомной энергетической установке), главная паровая турбина, главный конденсатор, главная зубчатая передача. Совокупность перечисленных элементов (без парового котла) представляет собой главный турбозубчатый агрегат (ГТЗА).
Кроме ГТЗА в ПТУ входят: вспомогательная паровая турбина с конденсатором, приводящая в действие электрогенератор (турбогенератор) судовой электростанции. На судах с электродвижением турбогенератор является главным. Отработанный во вспомогательном турбогенераторе пар может сбрасываться в свой (вспомогательный) или в главный конденсатор.
Принципиальная схема ПТУ показана на рисунке 3.1.
Пар с необходимыми температурой и давлением создается в паровом котле и подается в турбину, где тепловая энергия пара превращается в механическую энергию вращения ротора. Эта энергия передается через редуктор и судовой валопровод гребному винту.
Отработанный пар из турбины поступает в конденсатор, где, охлаждаясь, превращается в питательную воду (конденсат), которая питательным насосом подается в паровой котел. В конденсаторе охлаждающей средой является забортная (морская) вода.
Паротурбинная установка на ряду с ГТЗА имеет в своем составе вспомогательные паровые турбины и электрические двигатели для привода насосов и вентиляторов; теплообменники (подогреватели и охладители рабочих тел); вспомогательные конденсаторы; системы подогрева, охлаждения, герметизации лабиринтных уплотнений между статором и валом ротора турбины, циркуляции, дренажа и др. Совокупность указанного оборудования представляет собой единый энергетический комплекс ПТУ.
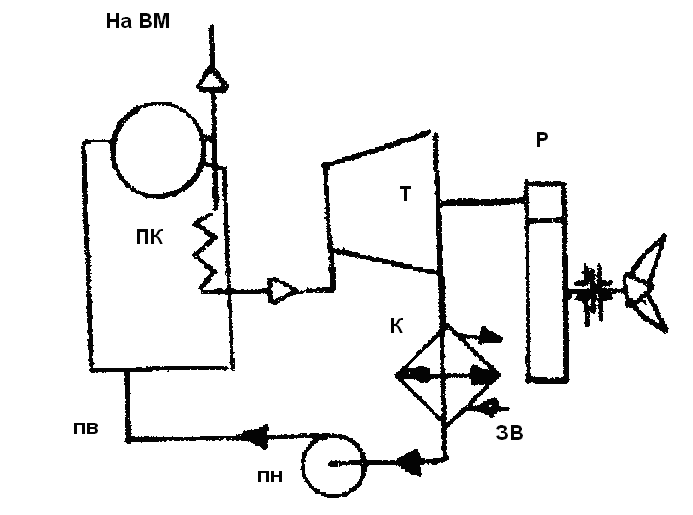
Рисунок 3.1 Принципиальная схема простейшей ПТУ:
ПК – паровой котел; Т – турбина; Р – редуктор; К – конденсатор; ПН – питательный насос; ПВ – питательная вода; ЗВ – забортная вода; ВМ – вспомогательные механизмы.
3.2 Тепловые схемы ПТУ
Для расчета и изучения теплоэкономических характеристик ПТУ используются их тепловые схемы.
Под тепловой схемой понимается условная схематизированная модель реальной установки и взаимосвязи между ее частями, необходимыми для осуществления рабочего процесса и выполнения функций ПТУ.
В зависимости от поставленных целей тепловая схема может быть исполнена как принципиальная или развернутая.
Принципиальная тепловая схема (рисунок 3.1) отражает последовательное соединение элементов ПТУ, тип термодинамического цикла и способ обеспечения энергией главных и вспомогательных механизмов и потребителей.
На развернутой схеме, кроме того, что указывается на принципиальной, демонстрируются количество и вид включенных в схему механизмов и аппаратов, емкостей, автоматов и прочих важных устройств.
Развернутые схемы бывают полными или менее полными. Все тепловые схемы делятся на нерегенеративные и регенеративные. Регенеративные делятся на схемы 1го рода, 2го рода и 3го рода.
Схемы 1го рода предусматривают регенеративный подогрев питательной воды паром, отобранным из главной турбины. В схемах 2го рода регенеративный процесс осуществляется отобранным паром от вспомогательных турбин.
В тепловых схемах 3го рода (смешанного типа) для регенерации используется пар, отобранный от главных и вспомогательных турбин одновременно.
Рассмотрим названные тепловые схемы ПТУ,
3.2.1 Нерегенеративная тепловая схема ПТУ
Нерегенеративная тепловая схема ПТУ (рисунок 3.2) используется на судах с жесткими массогабаритными ограничениями, на военных надводных кораблях и атомных подводных лодках. КПД установки, работающей с таким циклом, на 6…10% ниже, чем КПД регенеративной ПТУ.
Главная турбина работает на перегретом паре, который генерирует паровой котел (ПК). Паром этих же параметров питается вспомогательная турбина (ВТ) и теплообменные аппараты (ТА). Отработанный во всех перечисленных элементах пар сбрасывается в общий главный конденсатор (ГК), в котором пар превращается в воду (конденсат). Конденсат конденсатным насосом (КН) подается в теплый ящик (ТЯ), играющий роль аккумулятора питательной воды. Теплый ящик через вентиляционную трубу соединен со средой машинного отделения. Поэтому в питательной воде может находиться излишнее количество агрессивных газов. Такая схема питания парового котла имеет название открытой.
Питательный насос (ПН) принимает воду из теплого ящика и подает ее в паровой котел.
Открытая система питания применяется в ПТУ с давлением пара не более 2 мПа.
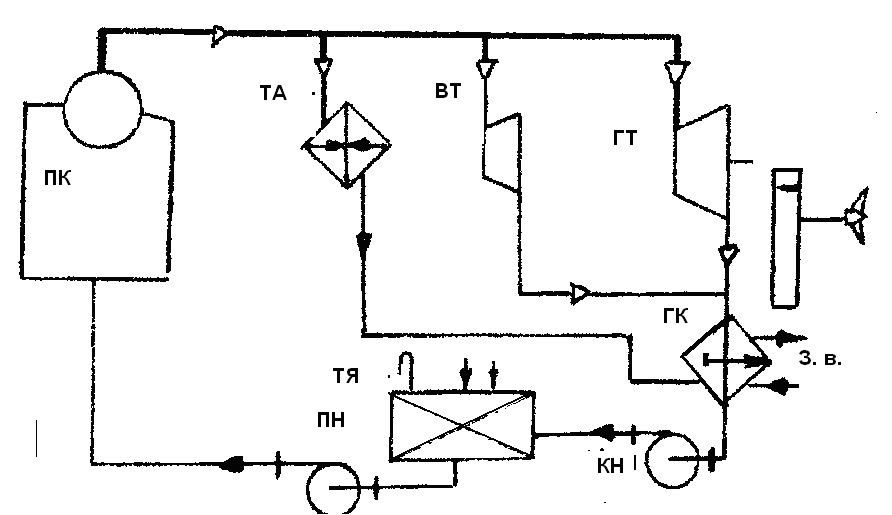
Рисунок 3.2 Нерегенеративная тепловая схема ПТУ.
ГТ – главная турбина; ВТ – вспомогательная турбина; ТА – теплообменный аппарат; ТЯ – тепловой ящик; ПН – питательный насос;
КН – конденсатный насос; ГК – главный конденсатор.
В регенеративных тепловых схемах подогрев питательной воды осуществляется теплотой пара, который частично отработал в турбине. За счет этого уменьшается количество отработанного пара, который сбрасывается в конденсатор. Одновременно уменьшаются потери теплоты, отводимой забортной водой.
3.2.2 Регенеративная тепловая схема 2го рода.
Такая схема используется в ПТУ, которые длительно работают на режимах с частичной нагрузкой.
В рассматриваемой схеме (рисунок 3.3) регенеративный процесс осуществляется отработанным паром вспомогательных турбин (турбогенератора, турбонасоса и т.п.).
Главная турбина (ГТ) работает на перегретом паре. Пар таких же параметров приводит в действие вспомогательные паровые двигатели (ВТ) и теплообменные аппараты (ТА). Отработанный пар от ГТ, ВТ и ТА сбрасывается в общий для них главный конденсатор (ГК), где происходит превращения пара в конденсат (горячую воду).
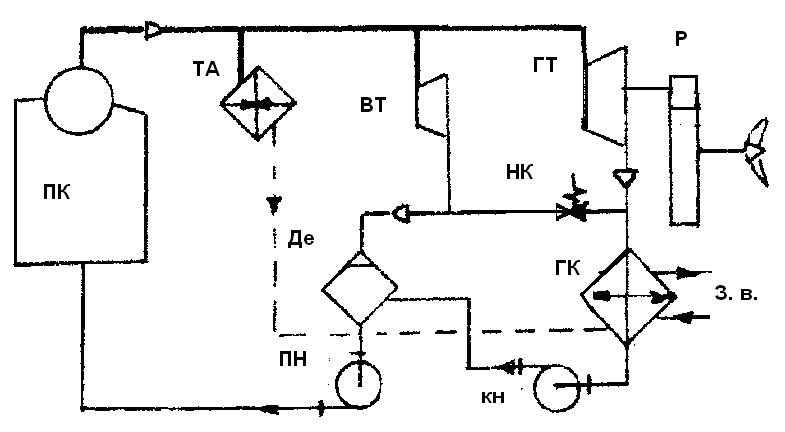
Рисунок 3.3 Тепловая схема ПТУ с регенерацией теплоты отработанного пара вспомогательных турбин (2го рода).
Конденсат конденсатным насосом (КН) подается в деаэратор (Дэ), который работает отОТ отработанного в ВТ пара. Этот пар поступает также и в ГК, но через подпружиненный невозвратный клапан (НК). Давление в магистрали отработанного пара выше, чем в ГК, поэтому излишек отработанного пара в ГК перепускается автоматически. Необходимое количество отработанного пара с высокой температурой подходит к подогревателю питательной воды – деаэратору (Дэ), в котором конденсируется. При нагревании воды до температуры насыщения происходит ее деаэрация, т.е. отделение растворенных в воде газов. В данной тепловой схеме 2го рода применяется закрытая схема питания котла. При этом газы выделяются в деаэраторе. Кроме того, деаэратор используется как аккумулятор и емкость, достаточная для подпитки котла в течение 12…15 минут при неработающем конденсатном насосе.
Оставшаяся часть теплоты отработавшего пара используется полезно. В результате затраты топлива и теплоты на ПТУ меньше, чем в ПТУ нерегенеративного типа.
3.2.3 Регенеративная тепловая схема 1го рода.
По этой схеме пар, который частично расширился в главной турбине, используется для подогрева питательной воды в теплообменниках поверхностного типа.
Такая тепловая схема называется идеализированной, потому что главная турбина является единым потребителем свежего рабочего пара, а отработанный в ней пар используется только для подогрева питательной воды. На схеме (рисунок 3.4) показаны три промежуточных отбора пара (I, II, III) от главной турбины и этот пар поступает в три регенеративных подогревателя питательной воды (ПП1, Дэ и ПП3).
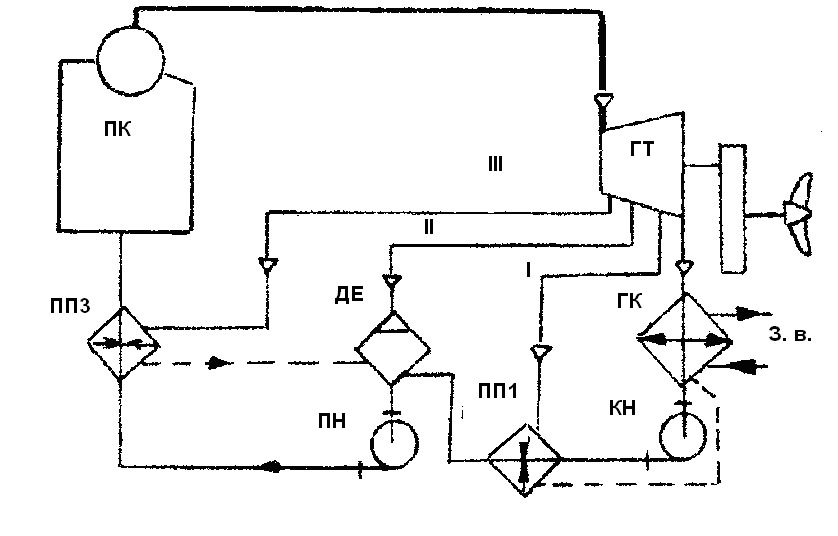
Рисунок 3.4 Тепловая схема идеализированной ПТУ с регенерацией теплоты в цикле главной турбины (схема 1го рода).
Конденсат (горячий) от подогревателя ПП1 подводится к главному конденсатору, а из теплообменника ПП3 – к деаэратору, где смешивается с питательной водой и подогревает ее. Питательная вода из деаэратора Дэ подается питательным насосом ПН в паровой котел. Количество отборов пара влияет на экономичность ПТУ. С увеличением количества отборов повышается температура питательной воды на выходе с последней ступени подогрева. В судовых ПТУ выполняют как правило 4…5 ступеней отбора пара. Таким образом, схемы 1го рода предусматривают подогрев питательной воды паром, отобранным от главной турбины. Такие тепловые схемы ПТУ применяются на транспортных судах, имеющее длительность плавания более 90% времени жизни судна.
3.3 Характеристики судовых ПТУ.
Паротурбинными установками оснащаются многотоннажные суда (танкеры, нефтевозы, газовозы, специальные и другие суда), большие пассажирские суда и ледоколы.
Основными характеристиками судовых ПТУ являются:
- количество парогенераторов (паровых котлов);
- давление пара, мПа (за парогенератором, за промежуточными пароперегревателями);
- температура пара, ºС (за парогенератором, за промежуточным пароперегревателем);
- тип ПТУ (без промежуточного перегрева, с промежуточным перегревом);
- мощность ГТЗА, мВт (номинальная и максимальная);
- количество отборов пара;
- количество ступеней подогрева питательной воды;
- удельный затраты топлива на все потребители судна, кг/(кВт.ч).
Такие характеристики ПТУ позволяют получать основные данные о судах с ПТУ.
Например, наиболее мощной ПТУ обладает пассажирское судно «Юнайтед Стейтс» водоизмещением 53.330 т и эксплутационной скоростью хода 30 узлов. Для обеспечения такой скорости хода это судно имеет 4 ГТЗА суммарной мощностью 181 мВт.
Для сравнения, танкер серии «Крым» имеет водоизмещение 150.000 т, а скорость хода 17 узлов, мощность его ГТЗА – 22 мВт. На таком танкере установлен один ГТЗА с турбинами высокого, среднего и низкого давления. Давление пара за парогенератором 7,65 мПа, за промежуточным пароперегревателем 1,46 мПа. Температура рабочего пара 510ºС. От турбины осуществляется 5 отборов пара, который используется в 5-ти ступенях подогрева питательной воды. Удельные затраты топлива на все потребители танкера – 0,258 кг/( кВт.ч).
Кроме перечисленных выше характеристик ПТУ, указываются также:
- мощность на гребном винте, мВт (на танкере «Крым» - 22 мВт);
- паропроизводительность котлов, т/ч;
- электрическая мощность генераторов, кВт;
- эффективный КПД ГТЗА (на танкере «Крым» - 0,807);
- КПД котла (на танкере «Крым» - 0,96);
- тип главного и вспомогательного конденсаторов (одноходовой, двухходовой и т.д.);
- тип редуктора (одноступенчатый, двухступенчатый, трехступенчатый, смешанного типа; тип зубьев);
- реверсивный или нереверсивный ГТЗА;
- тип винта (фиксированного или регулируемого шага).
А
(3.1)
бсолютный КПД ГТЗА определяется по формуле:
е=t.bi.be,
где t – термический КПД цикла (характеризует затраты энергии в конденсаторе); bi – внутренний индикаторный КПД ГТЗА; be – эффективный КПД ГТЗА.
Анализ затрат энергии в ПТУ показывает, что лишь малое количество химической энергии топлива переходит в полученную работу, а большая доля теряется. Наибольшие затраты энергии происходят при конденсации пара (50…60% теплоты, от подаваемой к ГТЗА).
В то же время имеется возможность повышать характеристики ПТУ. Например:
- повышение только давления пара за котлом позволяет снизить затраты топлива на 3…8%;
- увеличение количества ступеней регенеративного подогрева питательной воды позволяет повышать КПД ПТУ. Так при одноступенчатом подогреве питательной воды КПД цикла повышается на 3,5…4%, двухступенчатом – на 5,5…6%, трехступенчатом – на 7…7,5%, четырехступенчатом – на 8…8,5%. Однако увеличение количества ступеней подогрева питательной воды более пяти не дает эффекта увеличения КПД цикла;
- увеличение КПД главного котла до 0,96…0,98 достигается улучшением процессов горения топлива, а также снижением затрат с выпускными газами.
Существуют и другие способы повышения КПД ПТУ.
Следует отметить, что несмотря на большую и плодотворную работу конструкторских фирм по совершенствованию ПТУ, такие установки до сегодняшнего времени не находят широкого применения на транспортном флоте. Начиная с конца 70-х годов XX в. флот наполняется за год лишь единицами судов с паротурбинными энергетическими установками.
4. ГАЗОТУРБИННЫЕ УСТАНОВКИ
4.1 Назначение и принцип действия ГТУ.
Газотурбинная установка предназначена для преобразования тепловой энергии сжигаемого топлива в механическую работу.
Газотурбинные двигатели начали использоваться в исследовательских целях в морском флоте во 2-й половине 50-х годов XX века. В 60-х годах XX века они уже начали применяться на кораблях военно-морских флотов, а также и на гражданских судах. Этому способствовало то, что газотурбинные двигатели (ГТД) имели малые массогабаритные показатели, большую мощность, высокий уровень автоматизации и удобство обслуживания, высокую маневренность, что позволяет развивать полную мощность в течение 2…3 минут после запуска; возможность быстрой замены турбоагрегата, что способствует снижению трудоемкости при ремонте в условиях судна.
Опыт эксплуатации судов с ГТУ свидетельствует, что такие установки эффективны в основном на быстроходных специальных судах и на судах с динамическими принципами поддержания (СВП и СПК). Появление судов и кораблей на воздушной подушке, а также контейнеровозов, баржевозов и т.п. стало способствовать широкому внедрению ГТУ в морском флоте на качественно новом уровне.
Принцип действия ГТУ можно продемонстрировать с помощью простейшего цикла ГТД, изображенного на рисунке 4.1. Атмосферный воздух в компрессоре сжимается и подается в камеру сгорания, где обеспечивает сжигание топлива и получение газа с температурой от 400 до 1300ºС. Из камеры сгорания горячий газ, имеющий высокое давление, поступает в газовую турбину, где расширяется и производит механическую работу вращения ротора, которая передается через редуктор на гребной винт.
Эффективность работы ГТУ можно повысить за счет ее усложнения, т.е. путем включения новых элементов. Например, вместо одной турбины устанавливают отдельный привод на компрессор и на отбор мощности потребителю, а в цикл ГТУ вводят регенерацию теплоты уходящих газов, промежуточное охлаждение воздуха или подогрев газа, используют утилизацию теплоты.

Рисунок 4.1 Принципиальная тепловая схема ГТД:
АВ – атмосферный воздух; К – компрессор; Т – топливо; КС – камера сгорания; ГТ – газовая турбина; Р – редуктор; ГВ – гребной винт.
В энергетических установках транспортных судов используют ГТД трех основных типов:
- легкий ГТД авиационного типа;
- ГТД промыслового типа (тяжелые, в которых реализуется сложный тепловой цикл);
- ГТД, работающий с теплоутилизационным контуром.
Легкие ГТД как правило работают по простому тепловому циклу, а в цикл тяжелых ГТД вводят регенерацию.
4.2 Тепловые схемы сложных газотурбинных двигателей.
4.2.1 Цикл ГТД с регенерацией теплоты выпускных газов
В ГТД простого цикла (рисунок 4.1) выпускные газы имеют высокую температуру и уносят с собой в окружающую среду большое количество неиспользованной теплоты. Эти потери можно существенно уменьшить, если в цикл турбины ввести регенерацию выпускных газов – использовать их теплоту для подогрева сжатого компрессором воздуха. В этом случае в камеру сгорания подводится подогретый воздух, что обеспечивает более эффективное сгорание топлива и повышает КПД установки.
Регенерация практически осуществляется введением в схему установки теплообменного аппарата – регенератора, включаемого в поток воздуха после компрессора в камеру сгорания, а по потоку газа – за последней турбиной перед выпускным трактом (рисунок 4.2).
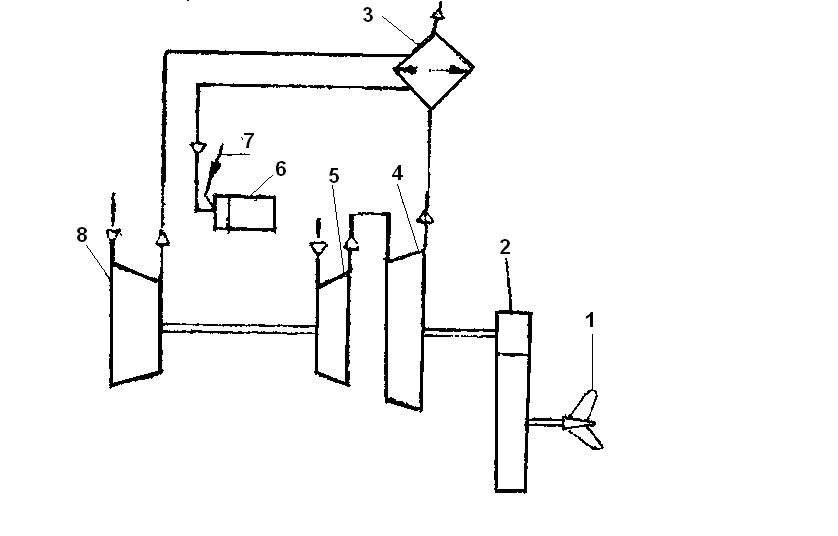
Рисунок 4.2 Тепловая схема ГТУ с регенерацией:
1 – гребной винт; 2-редуктор; 3-регенератор; 4-силовая турбина; 5-турбина компрессора; 6-камера сгорания; 7-подведение топлива; 8-компрессор.
Воздух, сжатый компрессором, поступает в регенератор и нагревшись подается в камеру сгорания. Из камеры сгорания газы последовательно поступают в турбину компрессора и силовую турбину, где расширяется почти до атмосферного давления. Отработанные в турбинах газы направляются к регенератору, где отдают свою теплоту воздуху. Мощность, развиваемая турбокомпрессором, затрачивается на привод компрессора, а силовой турбины – на вращение гребного винта.
В такой ГТУ:
- Регенерация повышает КПД цикла и уменьшает затраты топлива за счет его сгорания в подогретом воздухе.
- Уменьшаются потери теплоты с уходящими газами.
- Однако, затраты давления воздуха и газа уменьшают полезную работу расширения в цикле и увеличивают затраты воздуха.
Таким образом, регенерация является экономически эффективной, но приводит к усложнению установки. Введение регенерации, кроме того, повышает гидравлическое сопротивление в газовоздушном тракте, а это приводит к снижению КПД двигателя.
4.2.2 Цикл ГТД с промежуточным подогревом и охлаждением.
Полезная работа ГТД получается за счет работы турбины. Поэтому какие-либо меры, направленные на увеличение работы расширения в турбине или уменьшения работы в компрессоре, должны увеличивать полезную работу ГТД.
В реальном двигателе работа сжатия в компрессоре может быть уменьшена за счет применения двухступенчатого сжатия воздуха и его промежуточного охлаждения на пути между ступенями при постоянном давлении. При этом работа, затраченная в другой ступени сжатия, уменьшается пропорционально снижению температуры воздуха в воздухоохладителе. Это способствует уменьшению общей работы сжатия в двухступенчатом компрессоре.
Работу в турбине можно также увеличивать путем использования в ней ступенчатого расширения газов с промежуточным подогревом их между ступенями.
Такая схема ГТУ приведена на рисунке 4.3.
Воздух сжимается в КНД и охлаждается в воздухоохладителе ВО. В КВД происходит дальнейшее сжатие воздуха. В результате температура воздуха в конце может быть близкой к начальной.
После КВД воздух подается в КСВД, где в результате сжигания топлива получается высокотемпературный газ. Имеющий высокую температуру и давление газ подается к ТВД, где расширяется и подается в КСНД, в которой его температура повышается за счет сжигания топлива. Подогретый таким образом газ подводится к ТНД, где расширяется. В камеру сгорания КСНД дополнительный воздух для горения не подводится. В судовых ГТД промежуточное охлаждение воздуха находит применение, а промежуточный подогрев газов из-за сложности и низкой надежности практически не применяется.
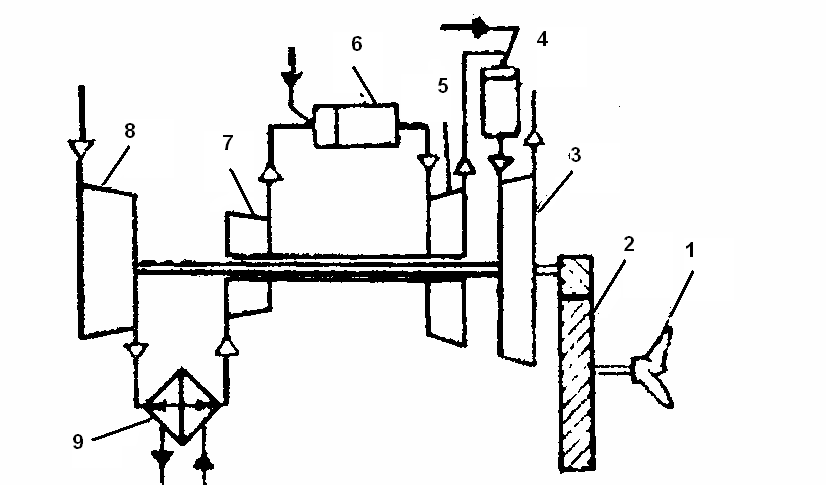
Рисунок 4.3 Тепловая схема ГТУ с промежуточным охлаждением и подогревом:
1-двигатель; 2-редуктор; 3-ТНД; 4-камера сгорания низкого давления; 5-ТВД; 6-камера сгорания высокого давления; 7-КВД; 8-КНД;
9-воздухоохладитель.
Принципиальные схемы ГТД, изображенные на рисунках 4.1 и 4.3, называют блочными, так как в них компрессор и потребитель (турбина) имеют жесткую связь. При таком соединении совместная работа этих двух потребителей энергии возможна только на одном режиме при постоянной частоте вращения. Это означает, что блочный ГТД пригоден для привода электрогенератора, водометного движителя или винта регулируемого шага.
На практике чаще всего в одном ГТД применяют две или три турбины и один или два компрессора. При этом силовой является свободная турбина.
4.3 Характеристики судовых ГТУ.
4.3.1 Судовые ГТД зарубежных фирм
В настоящее время ГТД является основным главным двигателем надводных военных кораблей, в том числе кораблей и судов с динамическими принципами поддержания. Ими оснащены более 500 боевых кораблей. По состоянию на конец 2000 года наибольшее количество кораблей с ГТД имели: США – 280, Великобритания, Япония и Южная Корея – по 40 кораблей. При этом программа переоснащения кораблей иностранных флотов предусматривает потребность в ГТД – примерно в 700 единиц.
Большинство зарубежных корабельных и судовых ГТД построены на основе авиационных двигателей. Такая практика привела к тому, что многие авиадвигателестроительные фирмы имеют специальные морские подразделения, которые прорабатывают морские модификации ГТД.
Основными производителями морских ГТД в США являются фирмы «Дженерал Электрик», «Лайкоминг», «Амисон» и др., а в Великобритании – «Ролс-Ройс».
Основные параметры судовых ГТД иностранных фирм:
- Мощность: максимальная – от 4,5 до 42 мВт; номинальная – от 4,2 до 41,8 мВт.
- Расход топлива: на максимальной мощности – от 210 до 269 г/(кВт.ч); на номинальной мощности от 200 до 272 г/(кВт.ч).
- КПД – от 0,373 до 0,424.
- Частота вращения ротора силовой турбины – от 3600 д0 7000 об/мин
4.3.2 Судовые ГТД, произведенные в Украине.
Разработкой ГТД авиационного типа в Украине занимается НПП «Машпроект», а серийным производством - ПО «Заря».
Основные параметры некоторых ГТД, произведенных в Украине:
- Мощность номинальная – от 2,85 до 28,7 мВт.
- Расход топлива на номинальной мощности от 233 до 288 г/(кВт.ч).
- КПД – от 0,285 до 0,418.
- Частота вращения ротора от 880 до 10.000 об/мин.
Например, ГТД марки ДЖ59 серийно выпускается с 1989 года и является многоцелевым. Он применятся в качестве главного двигателя на морских судах, а также на подвижных и стационарных электростанциях и компрессорных станциях. Этот двигатель двухкаскадный со свободной силовой турбиной. В камере сгорания применены 10 жаровых труб с топливными форсунками и двумя блоками зажигания. Запуск двигателя осуществляется с помощью электростартеров общей мощностью 210 кВт, а также пневмостартером. Этот двигатель изготавливается нереверсивным и реверсивным (ДЖ59R) с газовым реверсом. Следует заметить, что после резкого повышения цен на дизельное топливо, на котором работают ГТД надводные корабли и суда с такими двигателями стали нерентабельными. Еще в 1979 г. было принято решение о замене ГТД на судах на СЭУ с ДВС.
Таким образом, использование на морских транспортных судах ГТД авиационного типа является нерентабельным. Однако они являются основными двигателями в ВМФ на надводных кораблях и на кораблях с динамическими принципами поддержаниями. На зарубежных военных флотах ГТУ широко используется на кораблях с динамическим поддержанием (на воздушной подушке и на подводных крыльях).
5. Дизельные энергетические установки.
5.1 История создания и развития судовых двигателей внутреннего сгорания
Зарождение идеи создания двигателя внутреннего сгорания (ДВС) относится еще к концу XVII в. Так, в 1680 г. Гюйгенс предлагал построить двигатель, работающий за счет взрывов пороха в цилиндре, а более чем через 100 лет в 1794 г. Роберт Стрит получил английский патент на двигатель внутреннего сгорания, работающий на жидком топливе. В 1801 г. Лебон получил французский патент на газовый двигатель с электрическим воспламенением горячей смеси. В английском патенте, выданном в 1833 г. Вельману Райту, предусматривалось применение рабочего цилиндра с рубашкой для водяного охлаждения, а в патенте выданном в 1838 г. тоже англичанину Вильяму Барнету, предлагалось производить предварительное сжатие горючего газа и воздуха.
Несмотря на столь интенсивную деятельность изобретателей, успех в создании ДВС, пригодного для практического применения был достигнут лишь в 1860 г. Ленуаром, построившим двигатель, работавший на светильном газе без предварительного сжатия горючей смеси. КПД этого двигателя не превышал 3%.
В 1862 г. Бо-де-Роша разработал четырехтактный цикл. Однако практически четырехтактный двигатель был создан только через 15 лет (в 1877г.).
В 1879 г. инженер-механик русского флота И.С.Костович сконструировал первый в мире легкий бензиновый ДВС мощностью 80 л.с., предназначенный для дережабля.
В 1892 г. Р.Дизель получил патент на устройство нового типа ДВС, а в 1893 г. выпустил брошюру под названием «Теория и конструкция рационального теплового двигателя, призванного заменить паровую машину и другие существующие двигатели». В качестве топлива Дизель предлагал использовать угольную пыль. Однако такой двигатель оказался неработоспособным.
После этого практически каждый год осуществлялись попытки построить двигатель, работающий по принципу Дизеля. Однако устройство первых дизелей было очень несовершенным. При этом крупным недостатком было то, что он работал на дорогом топливе – керосине.
В 1898 г. Петербургский механический завод (сейчас завод «Русский дизель») по совету известного русского теплотехника профессора Г.Ф. Деппа приступил к постройке дизелей, работающих на дешевом топливе – сырой нефти. Такой двигатель был испытан через год. Он успешно работал и расходовал топлива лишь 300,5 г/(кВт.ч), тогда как зарубежные двигатели расходовали 326 г/(кВт.ч) более дорогого топлива – керосина.
Первый русский дизель был одноцилиндровым и развивал мощность 14,7 кВт при частоте оборотов вала 200 об/мин.
Известный русский специалист в области судостроения профессор К.П.Боклевский впервые выдвинул идею о целесообразности использования ДВС на судах. Русские заводы очень скоро осуществили эту идею.
Весной 1903 г. вступил в эксплуатацию первый в мире русский теплоход «Вандал» с тремя трехцилиндровыми четырехтактными дизелями мощностью по 88 кВт с электрической передачей на гребные винты. Таким образом, первый в мире теплоход был и первым в мире дизель-электроходом.
В 1904 г. вступил в эксплуатацию второй теплоход «Сармат» с двумя дизелями мощностью по 132 кВт.
После создания первых теплоходов постройка судовых дизелей началась на нескольких русских заводах. Наиболее передовыми и сегодня являются Коломенский и Сормовский заводы, а также завод «Русский дизель» и «Звезда», выпускающий высокооборотные легкие дизеля.
Дизельные ЭУ обладают следующими преимуществами по сравнению с ПТУ и ГТУ:
- высокая термодинамическая эффективность при низком расходе топлива;
- умеренные трудозатраты в эксплуатации и высокая надежность;
- возможность сжигать жидкие топлива широкой номенклатуры, в том числе и тяжелые;
- высокая степень приспособленности к автоматизации сравнительно простыми средствами;
- широкая возможность унификации узлов и деталей, что упрощает эксплуатацию и снабжение запасными частями.
Такие качества дизелей обусловили их широкое распространение на судах морского и речного флота в качестве главных и вспомогательных двигателей, а также способствовало быстрому развитию судового дизелестроения практически во всех странах мира. До 60-х годов XX века исключение составляли США, где потребность в мощных судовых двигателях удовлетворялась в основном за счет ПТУ. Однако в период 1965-1966 гг. три американские фирмы заключили соглашения на производство и поставку судовых малооборотных дизелей большой мощности со швейцарской фирмой Зульцер, датской фирмой Бурмейстер и Вайн и итальянской фирмой Фиат.
Таким образом, в истории развития дизелестроения можем выделить следующие этапы:
- с 1680 г. до 1880 г. – период попыток создания дизеля и создание бензинового ДВС (200 лет);
- с 1892 г. до 1904 г. – создание и внедрение на судах дизеля - ДВС, работающего при воспламенении от сжатия горючей смеси.
- 1904 г.по настоящее время – успешное внедрение дизелей на судах морского и речного флота.
5.2 Принцип действия, классификация и основные характеристики судовых двигателей внутреннего сгорания.
Двигатель внутреннего сгорания – это машина, которая преобразует тепловую энергию, полученную в результате сжигания топлива внутри цилиндров двигателя, в механическую энергию вращения.
К ДВС относятся карбюраторные двигатели, в которых карбюратором служит аппарат для образования рабочей смеси воздуха и распыленного топлива с подачей ее в цилиндры, где происходит ее воспламенение от свечей зажигания.
Дизелями называются двигатели, в которых топливо в цилиндре воспламеняется в результате сжатия воздуха до высокой температуры.
У
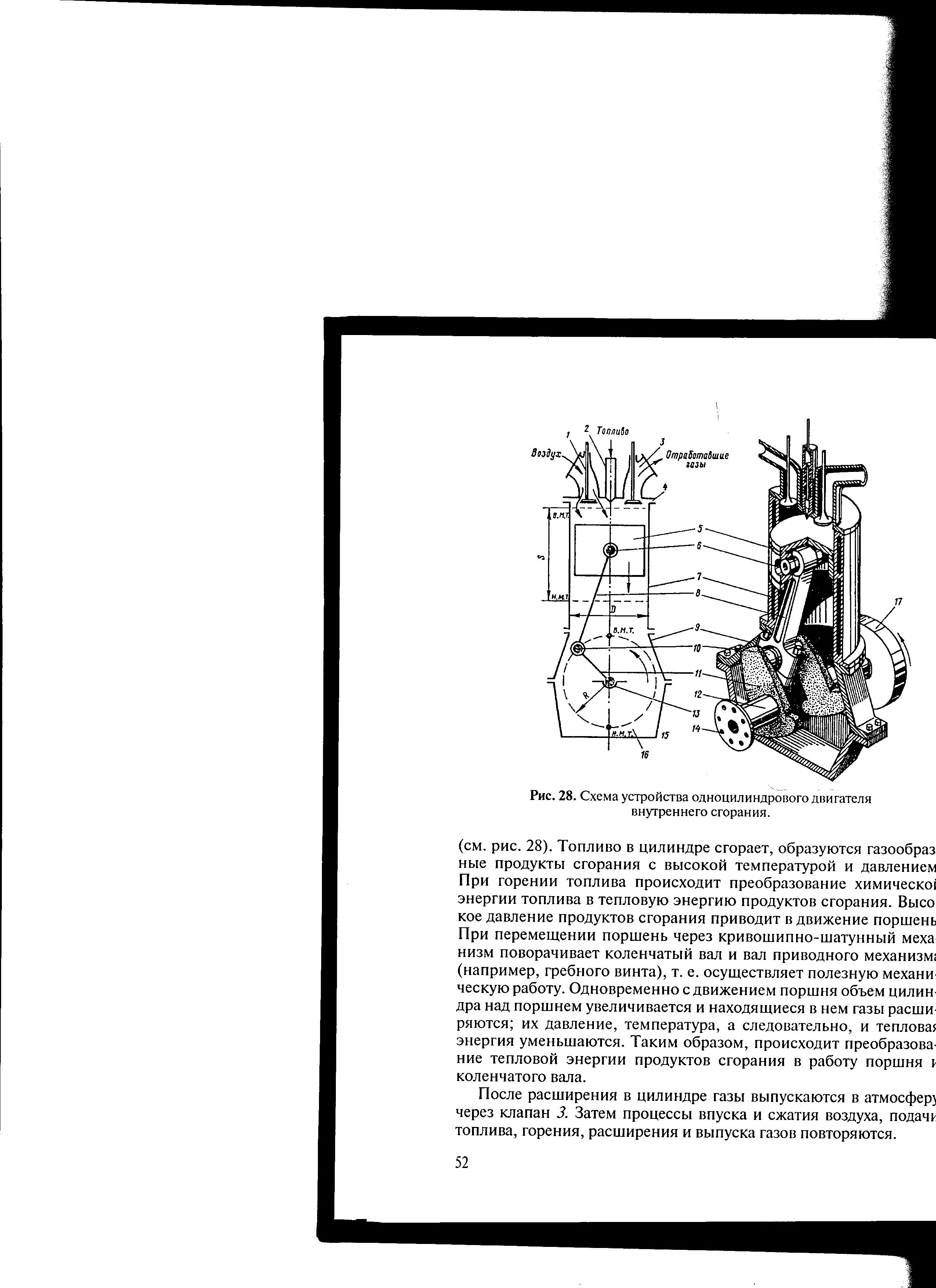
Рисунок 5.1 Принципиальная схема устройства дизеля.
Цилиндр 7, закрытый сверху крышкой 4, установлен на станине 9, закрепленной на фундаментной раме 15. В цилиндре движется поршень 5, который с помощью поршневого пальца 6 соединен с шатуном 8. Нижняя часть шатуна соединена с мотылевой шейкой 10 коленчатого вала, который состоит из колена (мотыля и кривошипа) и рамовых шеек 12. Колено, образованное двумя щеками 11 и шатунной шейкой 10. Рамовыми шейками колончатый вал уложен в рамовые подшипники 13 фундаментной рамы 15.
Механизм, образованный шатуном и коленчатым валом, называется кривошипно-шатунным. Он служит для преобразования возвратно-поступательного движения поршня в цилиндре во вращательное движение коленчатого вала.
Принцип действия дизеля состоит в следующем. При движении поршня 5 вниз в цилиндре 7 создается разряжение, открывается впускной клапан 1 и полость цилиндра над поршнем заполняется воздухом. При движении поршня вверх воздух в цилиндре сжимается до давления 3…4 мПа, в результате чего температура воздуха повышается в среднем до 600С. Когда поршень находится около крайнего верхнего положения (за 10…30С) поворота коленчатого, в полость цилиндра через форсунку 2 впрыскивается топливо. Топливо попадает в разогретый до высокой температуры воздух, перемешивается с ним, воспламеняется и сгорает. В результате в цилиндре образуются продукты сгорания (газы) с температурой 1800С и давлением 5…8 мПа. Газы, расширяясь, давят на поршень (при этом оба клапана в крышке цилиндра закрыты) и перемещают его вниз. Поршень через шатун действует на коленчатый вал и приводит его во вращение.
Одновременно с движением поршня вниз объем цилиндра над поршнем увеличивается, а находившееся над ним газы расширяются, а давление, температура и тепловая энергия газов уменьшаются.
После расширения в цилиндре при последующем движении поршня вверх газы выталкиваются через открывшийся выпускной клапан 3. Затем процессы выпуска воздуха, сжатия, подачи топлива, горения, расширения и выпуска газов повторяются.
Таким образом, во время работы дизеля химическая энергия топлива преобразуется в тепловую энергию продуктов сгорания с последующим ее преобразованием в механическую энергию движения поршня и вращения коленчатого вала.
На рисунке 5.1 представлена схема устройства одноцилиндрового дизеля. Обычно применяют многоцилиндровые дизели, состоящие из ряда одинаковых цилиндров и общего коленчатого вала.
Для нормальной работы дизеля обеспечивается определенная последовательность процессов в каждом из цилиндров: наполнение воздухом (всасывание), сжатие, подача топлива и горение, расширение продуктов сгорания и удаление отрабатывающих газов. Этот ряд последовательно протекающих в цилиндре процессов, обеспечивающих непрерывную работу двигателя, называется рабочим циклом. Часть рабочего цикла, протекающая за один ход поршня, называется тактом.
Двигатели, в которых рабочий цикл совершается за 4 хода поршня (за два оборота коленчатого вала), называются четырехтактными. Их рабочий цикл представлен на Рис. 5.2.
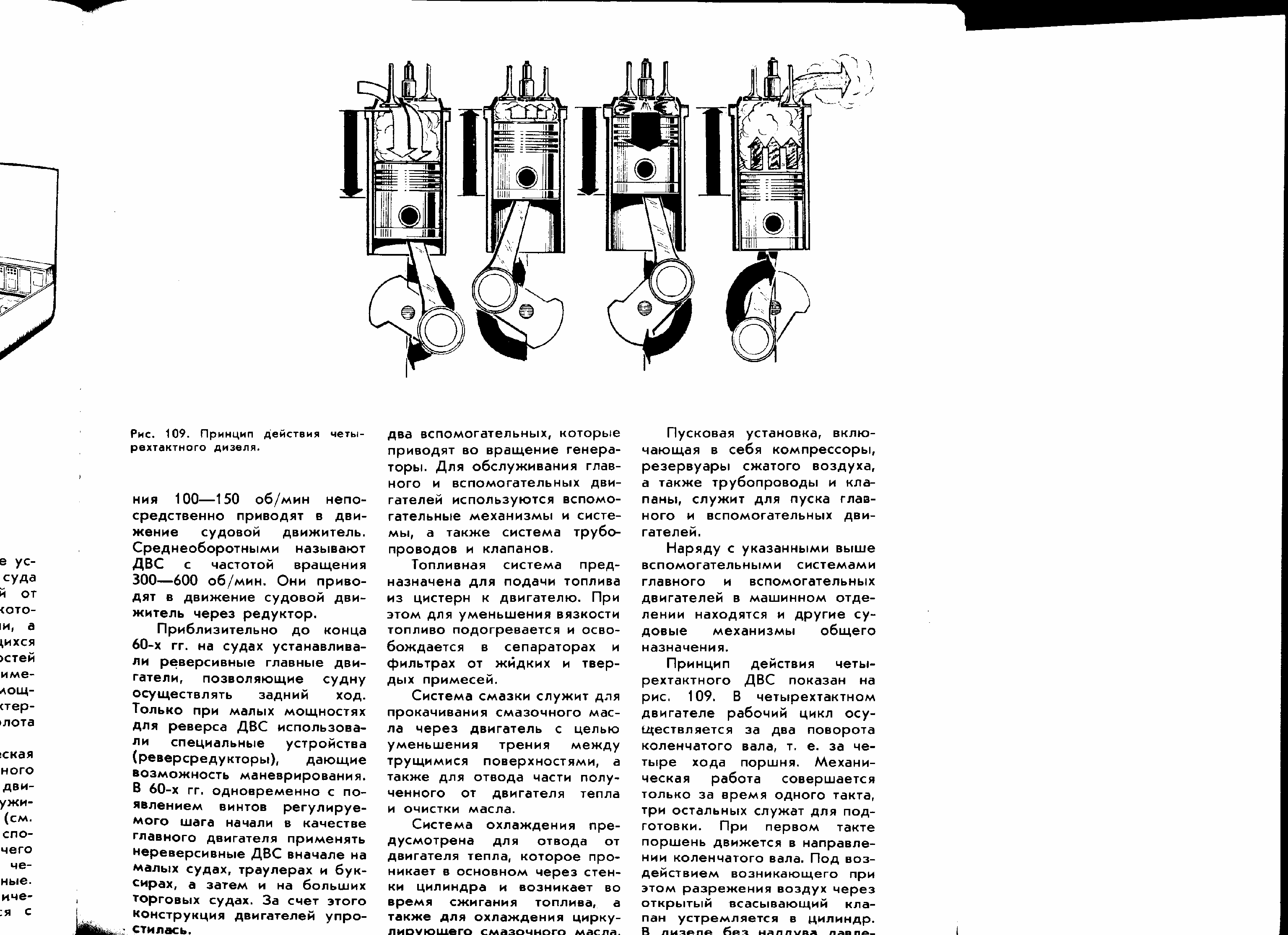
Рис. 5.2 Принцип действия четырехтактного дизеля.
Двигатели, в которых рабочий цикл совершается за два хода поршня (за один оборот коленчатого вала), называются двухтактными (см. рис. 5.3).
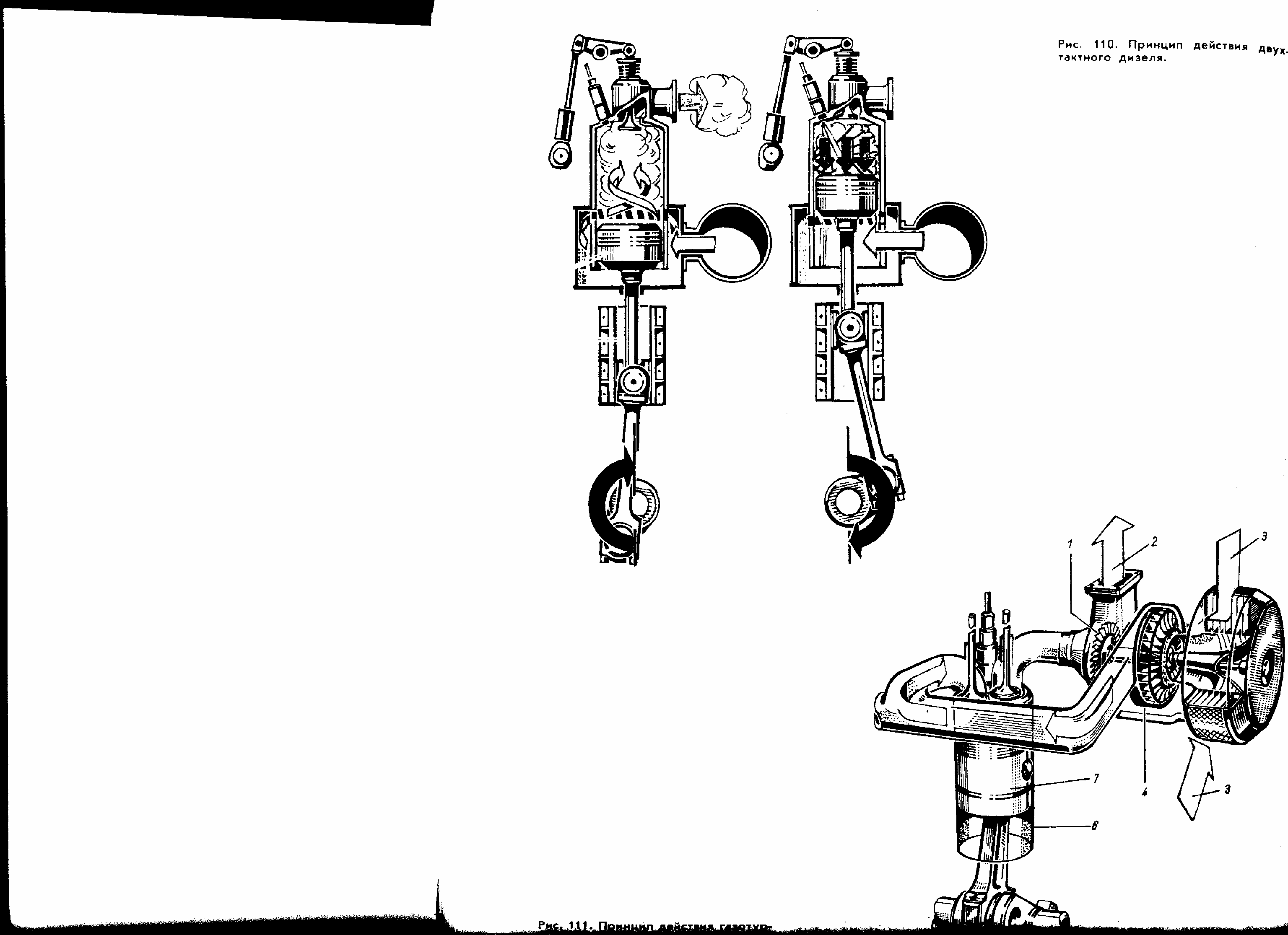
Рис. 5.3. Принцип действия двухтактного дизеля.
Классификация ДВС.
По назначению ДВС делятся на главные и вспомогательные. Главные обеспечивают ход судна. Вспомогательные обеспечивают работу электрогенераторов.
По осуществлению рабочего цикла ДВС бывают четырехтактными и двухтактными.
По способу образования рабочей смеси ДВС могут быть с внутренним и с внешним смесеобразованием. Ко второй относятся карбюраторные, а к первой дизельные ДВС.
По способу наполнения цилиндров свежим воздухом – двигатели баз наддува и двигатели с наддувом. В последних воздух в рабочие цилиндры нагнетается под давлением специальным нагнетателем (компрессором или газотурбинным компрессором), в результате чего достигается увеличение воздушного заряда и повышение мощности двигателя.
По способу воспламенения горючей смеси различают:
- двигатели, в которых распыленное топливо воспламеняется при смешивании со сжатым воздухом и поэтому разогретым воздухом (дизели);
- двигатели с воспламенением от электрической искры (карбюраторные двигатели).
По конструктивному исполнению двигатели бывают тронковые, у которых поршень посредством пальца шарнирно соединяется с шатуном (рисунок 5.1) и крейцкопфные (рисунок 5.4), у которых поршень 1 через шток 2 жестко соединен с ползуном 3 (крейцкопфом), а последний шарнирно связан с шатуном 5.
В тронковых двигателях боковые усилия, возникающие при работе кривошипношатунного механизма, воспринимаются поршнем и передаются на цилиндр. У крейцкопфных боковые усилия передаются через ползуны крейцкопфа 3 направляющим параллелям 4, которые являются частью остова двигателя.

Рисунок 5.4 Схема крейцкопфного дизеля.
В зависимости от расположения цилиндров ДВС могут быть: однорядными, V – образными, X – образными и звездообразными.
Двухтактные ДВС иногда выполняются с противоположным движением поршней (рисунок 5.4). В каждом цилиндре такого двигателя находятся по два поршня, при сближении которых газы сжимаются, а при расхождении расширяются. Выпуск газов и подача воздуха или горючей смеси производится через окна, расположенные в цилиндре на определенных уровнях.
По направлению вращения коленчатого вала различают двигатели правого (вращение по часовой стрелке, если смотреть со стороны потребителя энергии) и двигатели левого (против часовой стрелки) вращения.
По способу изменения направления вращения вала двигатели делят на реверсивные и нереверсивные. Реверсивные – такие двигатели, у которых можно изменять направление вращения коленчатого вала. Как правило это мощные двигатели. Нереверсивными выполняют двигатели меньшей мощности (до 220 кВт). Задний ход судна в этом случае выполняется при помощи реверсивной передачи, установленной между двигателем и гребным валом.
По частоте вращения коленчатого вала различают двигатели малооборотные (n=100…200об/мин), среднеоборотные (n=200…750 об/мин) и высокооборотные (n>750 об/мин).
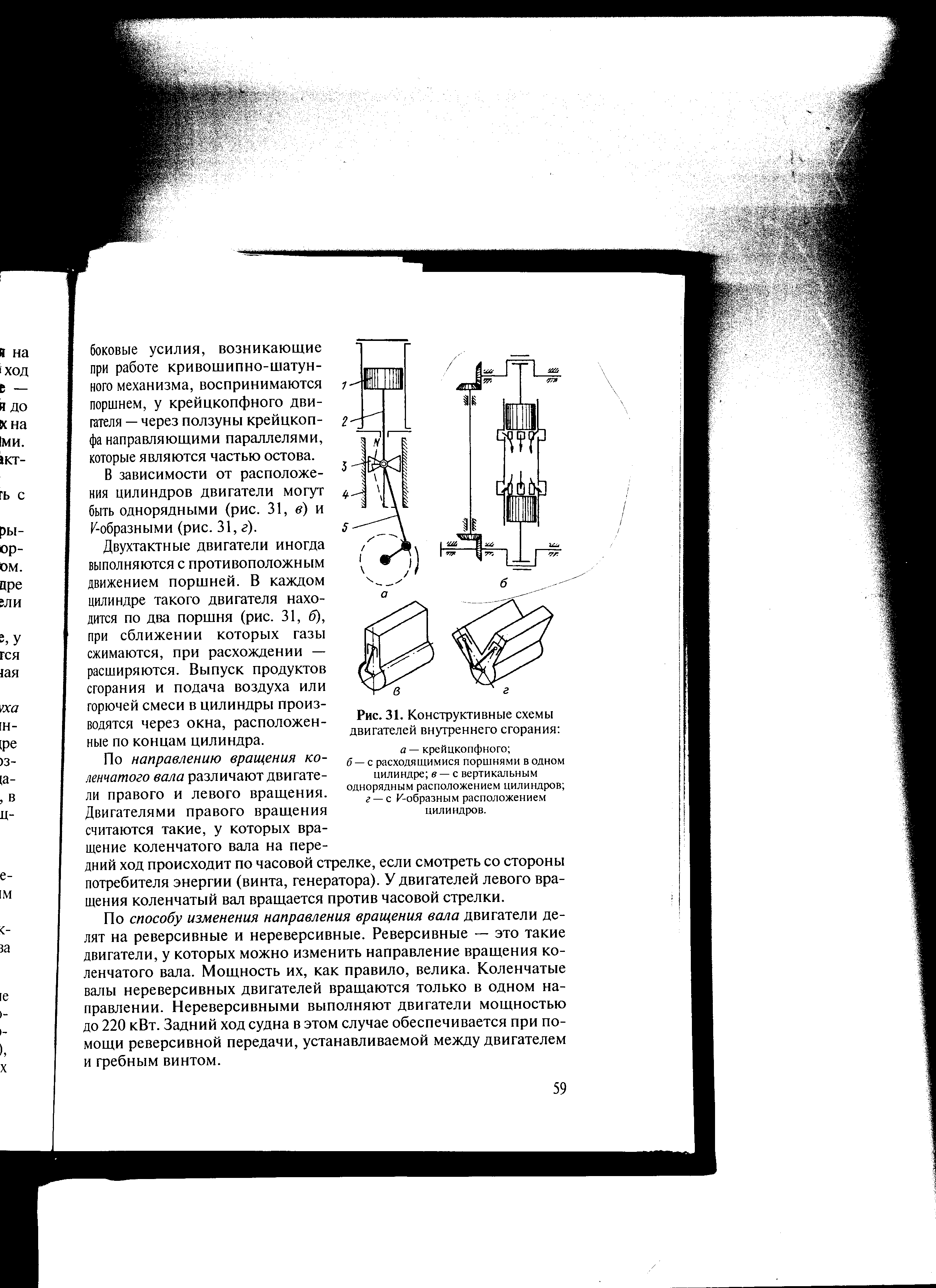
Рисунок 5.5 – Схема 2-тактного дизеля с противоположно движущимися поршнями.