Обработка металлов резанием
Вид материала | Документы |
- Шифр специальности: 05. 16. 01 Металловедение и термическая обработка металлов и сплавов, 25.46kb.
- Обработка металлов давлением при обработке металлов давлением, 131.9kb.
- Программа профессиональной переподготовки мтф п/п-1 «металловедение и термическая обработка, 34.45kb.
- Лекция 7 термическая обработка металлов, 136.74kb.
- Научные основы и технологические способы обработки гетерофазных сплавов с высоким уровнем, 572.64kb.
- Программа вступительного испытания по направлению «Металлургия», 51.65kb.
- 05. 16. 01 Металловедение и термическая обработка металлов, 25.25kb.
- Развитие научных основ и разработка совмещенных методов обработки металлов давлением,, 606kb.
- Реферат по теме: «Металлы. Свойства металлов.», 196.2kb.
- Закономерности превращения, 589.18kb.
Геометрические параметры режущей части влияют на основные факторы процесса резания: трение между поверхностями Р. и заготовки, форму и направление схода стружки, деформацию поверхностного слоя, стойкость Р., силы резания, интенсивность и величину изнашивания Р., шероховатость обработанной поверхности и др.
В зависимости от конкретных условий обработки (обрабатываемого материала, режима резания, типа Р., жёсткости системы станок — приспособление — инструмент — деталь, характера обработки, способа получения обрабатываемой заготовки и др.) экспериментально найдены оптимальные параметры геомерии режущей части Р. (рис. 2—5): = [(—10)—25]°; = (6 + 12)°; = (10 + 90)°; 1 = (0—20)°; = [(—4)—15]°.
При обработке изделий Р. с увеличенным радиусом при вершине r уменьшается шероховатость поверхности, но возрастают силы отжатия Р. от обрабатываемого изделия и увеличивается его прогиб, а также повышаются вибрации. Поэтому принимают r = 1 мм; для упрощения заточки твердосплавного Р. вместо закругления вершины делают переходную режущую кромку длина 1—2 мм с 0 = /2. Для Р. с минералокерамическими пластинками рекомендуется: = [(—5)—(—10)]°; = (8—10)°; = (75—90)° (для нежёстких деталей) и = (10—30)° (для особо жёстких деталей).
От свойств инструментального материала, конструкции Р. и геометрии их режущей части в значительной степени зависит эффективность процесса обработки металлов резанием — наиболее трудоёмкой части технологического процесса производства. Эта проблема тесно связана с обработкой новых труднообрабатываемых материалов, повышением требований к точности изготовления и качеству поверхностей, предварительной настройкой на размер и быстрой сменой инструмента без подналадки. Для обработки нержавеющих и жаропрочных сталей и сплавов Всесоюзным научно-исследовательским институтом твёрдых сплавов (ВНИИТС) разработаны особо мелкозернистые твёрдые сплавы ВК6-ОМ, ВК10-ОМ, ВК15-ОМ, для чистовой и получистовой скоростной обработки легированных, модифицированных и ковких чугунов — твёрдый сплав ТТ8К16, а для прерывистых работ с ударами — твёрдый сплав ТТ20К9. Находят применение многогранные неперетачиваемые твердосплавные пластинки с износостойким покрытием — карбидом титана, который наносится тонким слоем (до 5 мкм) методом осаждения из газовой фазы. Всесоюзным научно-исследовательским инструментальным институтом (ВНИИ) разработан ряд конструкций Р. с многогранными режущими вставками и стружколомающими канавками. Широко применяются Р. с механическим закреплением пластин, Р. со вставками из композиционных материалов, поликристаллических алмазов и т. п. См. также Металлорежущий инструмент, Дереворежущий инструмент.
Лит.: Грановский Г. И., Металлорежущий инструмент. Конструкция и эксплуатация, 2 изд., М., 1954; Семенченко И. И., Матюшин В. М., Сахаров Г. Н., Проектирование металлорежущих инструментов, М., 1963; Режущий инструмент. Резцы, М., 1965; Резание конструкционных материалов, режущие инструменты и станки, под ред. В. А. Кривоухова, М., 1967; Аршинов В. А., Алексеев Г. А., Резание металлов и режущий инструмент, 2 изд., М., 1967; Пути совершенствования металлорежущего инструмента. Обзор, М., 1972; Бобров В. Ф., Иерусалимский Д. Е., Резание металлов самовращающимися резцами, М., 1972; Гладилин А. Н., Малевский Н. П., Справочник молодого инструментальщика по режущему инструменту, 3 изд., М., 1973; Резание конструкционных материалов, режущие инструменты и станки, 2 изд., М., 1974.
Д. Л. Юдин.


Формы передней поверхности резцов: II — плоская с фаской. Область применения: резцы всех типов для обработки стали; f = 0,2—0,3 мм при чистовой обработке; f = 0,8—1,0 мм при черновой обработке, g =0° для резцов из быстрорежущей стали, g = (—5) — (—10)° — из твёрдого сплава.


Формы передней поверхности резцов: 1 — плоская без фаски; 2 — плоская с фаской; 3 — радиусная с фаской; 4 — плоская отрицательная; 5 — плоская с фаской и опущенной вершиной.


Формы передней поверхности резцов: V — плоская с фаской и опущенной вершиной. Область применения: черновое точение стали с крупной стружкой и подачами ≥ 1,5 мм/об; gj = (—10) — (—15)°.


Рис. 3. Резец конструкции ЦНИИТМаш с механическим закреплением пластинки: 1 — державка; 2 — подкладка; 3 — пластина; 4 — болт; 5 — шайба; 6 — прижим; 7 — передвижной упор.


Рис. 4. Резец с многогранной неперетачиваемой твердосплавной пластинкой: 1 — державка; 2 — пластинка; 3 — штифт; 4 — клин; 5 — винт.

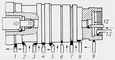
Рис. 1. Токарные резцы: 1 — проходной прямой правый; 2 — проходной упорный правый; 3 — подрезной левый; 4 — подрезной; 5 — проходной отогнутый правый; 6 — отрезной; 7 — фасонный; 8 — подрезной правый; 9 — резьбовой (для наружной резьбы); 10 — расточный упорный (в борштанге); 11 — расточный (в борштанге); 12 — расточный; 13 — расточный для внутренней резьбы.


Рис. 5. Резец конструкции ВНИИ с твердосплавной пластинкой.


Рис. 2. Резец с зачищающей режущей кромкой: 1 — главная режущая кромка; 2 — переходная режущая кромка; 3 — зачищающая кромка.


Формы передней поверхности резцов: IV — плоская отрицательная. Область применения: резцы с пластинками твёрдого сплава при черновом точении стали с временным сопротивлением σвр ≥ 1000 Мн/м2 (100 кгс/мм2 ),стального литья с коркой при точении с ударами.


Формы передней поверхности резцов: III — радиусная с фаской. Область применения: резцы всех типов для обработки стали; R = 3—18 мм — для быстрорежущей стали; R = 2—6 мм — для твёрдого сплава; f и gj — аналогичны форме II.
Фреза (от франц. fraise), режущий многозубый (многолезвийный) инструмент в виде тела вращения для обработки металлов и др. конструкционных материалов резанием (фрезерованием). По типу (назначению) различают Ф. цилиндрические, торцовые, дисковые пазовые (одно-, двух- и трёхсторонние), отрезные (прорезные), концевые, шпоночные, Т-образные пазовые, угловые, фасонные (в т. ч. модульно-дисковые и пальцевые), червячные (см. рис. 1); по сечению зуба — остроконечные, затылованные; по форме зубьев — с прямыми, винтовыми, разнонаправленными зубьями; по направлению винтовых канавок — с правыми и левыми канавками; по конструкции — цельные, составные, сборные, со вставными зубьями (ножами), комплектные: по способу крепления — насадные, с хвостовиком (конические или цилиндрические); по материалу режущей части — из быстрорежущей стали, твёрдого сплава, композиционного материала. На рис. 2 и 3 даны геометрические параметры режущей части наиболее широко используемых типов Ф. — цилиндрический и торцовой. Экспериментально установлены следующие диапазоны оптимальных геометрических параметров режущей части: передний угол — (—10)—30°; главный задний угол — 10—30 °; вспомогательный задний угол 1 — 4—10 °; главный угол в плане — 30—90°; вспомогательный угол в плане 1 — 1—10 °; длина переходной режущей кромки l — 1—2 мм; угол наклона главной режущей кромки — (—5)—
15 °; угол наклона винтовых канавок (зубьев) — 10—45 °. На производительность фрезерования, стойкость Ф., качество обработанных поверхностей, силу резания и т.п. влияют и др. геометрические параметры Ф.: n — задний угол в нормальном сечении, — поперечный передний угол, — продольный передний угол, 0 — угол в плане переходной режущей кромки. См. также ст. Геометрия резца.
Лит.: Гладилин А. Н., Малевский Н. П., Справочник молодого инструментальщика по режущему инструменту, 3 изд., М., 1973; Вульф А. М., Резание металлов, 2 изд., Л., 1973; Резание конструкционных материалов, режущие инструменты и станки, 2 изд., М., 1974; Обработка металлов резанием. Справочник технолога, 3 изд., М., 1974.
Д. Л. Юдин.

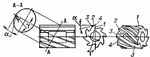
Рис. 2. Геометрические параметры режущей части цилиндрической фрезы: 1 — передняя поверхность зуба; 2 — задняя поверхность зуба; 3 — затылочная поверхность зуба; 4 — винтовая главная режущая кромка зуба.


Рис. 1. Основные типы фрез: 1 — цилиндрическая; 2 — торцовая; 3 и 4 — дисковые пазовые; 5 — прорезная; 6 и 7 — концевые; 8 — угловая; 9 и 10 — фасонные; 11 — шпоночная.


Рис. 3. Геометрические параметры режущей части торцовой фрезы: 1 — главная режущая кромка; 2 — переходная режущая кромка.
Протяжка в металлообработке,
1) операция, применяемая при обработке металлов давлением (например, ковке) с целью уменьшения толщины стенки и увеличения длины исходной заготовки, имеющей форму стакана и обычно полученной в результате несквозной прошивки. Под действием пуансона заготовка протягивается через одну или несколько последовательно расположенных матриц. Обычно П. производят на протяжных гидравлических прессах.
2) То же, что вытяжка.
Развёртка, многолезвийный металлорежущий инструмент, предназначенный для точной и чистовой обработки (развёртывания) отверстий после их предварительной обработки сверлом, зенкером или расточным резцом. Р. могут быть машинными (применяются на станках) и ручными (применяются при слесарных работах). Р. различают: по форме развёртываемого отверстия — цилиндрические, конические и ступенчатые; по форме зубьев — с прямыми и винтовыми зубьями; по способу закрепления — вставные (с хвостовиком) и насадные (с отверстием); по конструкции — цельные, составные (сборные), напайные, с механическим или клеевым закреплением зубьев (ножей), разжимные и плавающие. Рабочая часть Р. состоит из режущих и калибрующих зубьев. Режущие зубья остро затачивают, на калибрующих — оставляют ленточку шириной 0,1—0,3 мм. Конец калибрующей части выполняется с обратным конусом по направлению к хвостовику для уменьшения трения Р. о стенки отверстия.
Лит.: Семенченко И. И., Матюшин В. М., Сахаров Г. Н., Проектирование металлорежущих инструментов, М. 1963; Космачёв И. Г., Карманный справочник технолога-инструментальщика, 2 изд. Л., 1970; Резание конструкционных материалов, режущие инструменты и станки, М 1974.
Д. Л. Юдин.

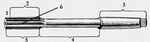
Схема развертки: 1 — режущая часть; 2 — калибрующая часть; 3 — хвостовик; 4 — шейка; 5 — рабочая часть; 6 — зуб.
Цековка, металлорежущий инструмент в виде головки с режущими зубьями на торцовой поверхности, разновидность зенкера. Ц. имеет нижнюю гладкую направляющую часть, вставляемую в отверстие, вокруг которого производится обработка, что позволяет выдерживать взаимную перпендикулярность получаемой поверхности и оси отверстия.
Сверло, режущий инструмент для получения отверстия сверлением или увеличения его диаметра при рассверливании. В металлообработке различают С. по конструкции и назначению: винтовые (спиральные) универсальные; для получения глубоких отверстий (одно- и двухстороннего резания); центровочные (для обработки центровых отверстий). Наиболее распространённое винтовое С. представляет собой стержень (рис. 1) с рабочей частью, имеющей режущие элементы — главные режущие кромки, вспомогательные режущие кромки (кромки-ленточки) и поперечную кромку, и хвостовиком, которым С. крепится в шпинделе станка, патроне или сверлильной головке. Рабочая часть выполняется с равномерной обратной конусностью — 0,03—0,12 мм на 100 мм длины С. Изготовляют также С. специальных конструкций — без поперечной кромки, с особой заточкой, со стружкоразделительными канавками. Стандартные винтовые С. имеют диаметр от 0,25 до 80 мм. В зависимости от свойств обрабатываемого материала, режима резания и материала режущей части С. применяют пять различных форм заточки режущей части (рис. 2). Основные нормируемые геометрические параметры винтовых С. (рис. 3): угол наклона винтовых канавок , угол при вершине 2, угол наклона поперечной кромки , задний угол и, передний угол . Для всего диапазона диаметров С. принимают = 18—30°, 2= 80—140°, = 47—55°, = 8—14°, tg = tg/sindr/D, где dr — диаметр режущей части С. в точке, для которой определяется угол. Режущая часть С. изготовляется из быстрорежущих сталей и твёрдых сплавов или композитных материалов; хвостовики делают из сталей 45, 40Х (при режущей части из быстрорежущей стали) и сталей ХС, 40Х, 45Х (при режущей части из твёрдых сплавов или композитных материалов).
Д. Л. Юдин.
В деревообработке наряду со С. с конической заточкой применяют спиральные С. с направляющим центром и подрезателями, С. для кольцевого сверления, С. полые с выталкивателем и др. (рис. 4а, 4б, 4в). Наиболее распространены спиральные С. Для спиральных С. = 22—30°, 2 при сверлении перпендикулярно волокнам древесины составляет 120°, при сверлении вдоль волокон — 60—80°, = 20—30°. Для уменьшения усилий резания спиральных С. с направляющим центром и подрезателями высота подрезателей h принимается не более максимальной подачи. Обычно h = 0,8—2 мм, а высота направляющего центра — 3,5—8,5 мм.
С. изготовляют из инструментальной стали Х6ВФ или из быстрорежущей стали Р6М5. Для сверления древесностружечных и древесноволокнистых плит, фанерованных щитов и др. древесных материалов используют С., оснащенные пластинками и коронками из твёрдых сплавов.
В. С. Рыбалко.
Лит.: Грубе А. Э., Дереворежущие инструменты, 3 изд., М., 1971. См. также лит. при ст. Металлорежущий инструмент.

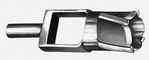
Рис. 4в. Сверло для кольцевого сверления для обработки древесины и древесных материалов.


Рис. 3. Углы винтового сверла по металлу.

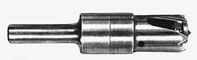
Рис. 4б. Сверло цилиндрическое полое с выталкивателем (для высверливания пробок) для обработки древесины и древесных материалов.

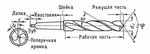
Рис. 1. Винтовое сверло по металлу.


Рис. 2. Формы заточки сверла по металлу: а — одинарная или нормальная; б — одинарная с подточкой поперечной кромки; в — одинарная с подточкой поперечной кромки и ленточки; г — двойная с подточкой поперечной кромки; д — двойная с подточкой поперечной кромки и ленточки.

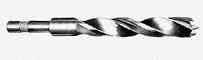
Рис. 4а. Сверло спиральное с направляющим центром и подрезателем для обработки древесины и древесных материалов.
Зенкер (нем. Senker), металлорежущий инструмент, предназначенный для чистовой обработки стенок отверстий — зенкерования. В отличие от сверла, З. обычно имеет от 3 до 6 режущих кромок, расположенных относительно оси наклонно или перпендикулярно (у торцевых З.). З. изготовляют цельными из быстрорежущей стали, сварными (с хвостовиками из углеродистой конструкционной стали), сборными (со вставными ножами из твёрдого сплава), насадными (с напаянными пластинками из твёрдого сплава) и др.
Зенковка (от нем. senken — углублять), режущий инструмент для зенкования. З. комплектуют обычно в наборе с центровочными свёрлами. Размеры З. в каждом наборе зависят от диаметра отверстия, угол при вершине составляет 60°. Различают З. для снятия фасок центровых отверстий диаметром от 0,5 до 1,5 мм (простые), для отверстий от 0,5 до 6 мм (без предохранительного или с предохранительным конусом) и для отверстий от 8 до 12 мм (с конусным хвостовиком). Режущую часть З. изготовляют из быстрорежущей стали; З. с коническими хвостовиками делают сварными, хвостовики — из углеродистой конструкционной стали.
Метчик, режущий инструмент для нарезания винтовой резьбы в предварительно просверленном отверстии. М. представляет собой цилиндрический валик, имеющий на одном конце режущие кромки. Другой конец М. (хвостовик) предназначен для закрепления в патроне или удержания его в воротке во время работы. Основные типы М.: ручные; гаечные — для нарезания за один проход полной резьбы в сквозных отверстиях; машинные — для нарезания резьбы главным образом в глухих отверстиях на сверлильных станках, автоматах и специальных агрегатных станках; станочные — для получения резьбы в сквозных отверстиях на гайконарезных станках; бесканавочные — для нарезания за один проход резьбы в сквозных отверстиях; автоматные — для нарезания резьбы в гайках на гайконарезных автоматах; плашечные и маточные — для нарезания резьбы и калибровки и удаления заусенцев в резьбовых отверстиях круглых плашек. Материал для изготовления М. — легированная инструментальная и быстрорежущая сталь. См. Металлорежущий инструмент.
Плашка, резьбонарезной инструмент для нарезания наружной резьбы вручную или на металлорежущем станке (обычно за один проход). В процессе резания П. и заготовка совершают 2 относительных движения: вращение вокруг продольной оси резьбы и продольную подачу (равную шагу резьбы); при этом П., навинчиваясь на заготовку, нарезает резьбу режущими перьями. П. требует принудительной подачи на 1—2 шага только при врезании, дальнейшее осевое движение может происходить самоподачей (самозатягиванием).
По наружной форме П. бывают круглые, квадратные, шестигранные, трубчатые и др. По конструкции различают П. цельные, разрезные и раздвижные. Существуют П. к резьбонарезным головкам и слесарным клуппам, резьба которыми нарезается за нескольких проходов. Наиболее распространена круглая П., имеющая, подобно гайке, центральное отверстие с резьбой, вокруг которого расположено 3—6 гладких отверстий, пересекающих центральное отверстие для образования зубьев П. и канавок для отвода стружки. Трубчатые П. применяются на токарно-револьверных станках и автоматах, где облегчены условия выхода стружки. Скорость резания при работе П. 2,5—4 м/мин; низкие скорости резания обусловлены плохим теплоотводом от узких режущих перьев. П. изготовляются, как правило, из инструментальной стали и быстрорежущей стали.
Н. А. Щемелев.
Резьбонарезной инструмент, металлорежущий инструмент для получения резьбы на различных деталях. К Р. и. относятся резьбовые резцы, метчики, плашки, резьбонарезные головки, резьбовые фрезы и резьбовые шлифовальные круги. Резьбовые резцы [стержневые, призматические и круглые (дисковые)] применяют для нарезания наружных и внутренних резьб за один или несколько проходов в зависимости от выбранной технологии. Вращающиеся резцы (призматические и круглые многониточные) применяют при скоростном резании. Для нарезания внутренней резьбы диаметром до 50 мм используют обычно метчики (ручные, гаечные, машинно-ручные, плашечные и сборные маточные). Наружную крепёжную резьбу (главным образом на болтах, винтах и т. п. ) получают плашками (круглыми и раздвижными).
Резьбонарезные головки — наиболее совершенный и высокопроизводительный инструмент для нарезания резьбы на станках за один проход. Резьбовые фрезы (дисковые и гребенчатые) применяют для нарезания наружных и внутренних резьб. Дисковыми резьбовыми фрезами чаще всего нарезают длинные, многозаходные резьбы с большим шагом; гребенчатыми (многониточными) насадными и концевыми резьбовыми фрезами — короткие наружные резьбы с небольшим шагом (0,5—6 мм). Концевыми фрезами получают также внутренние резьбы диаметром от 15 мм и больше. Резьбовые шлифовальные круги (однониточные и многониточные) используют для чистовой обработки резьб и на резьбошлифовальных станках. Рабочие поверхности круга соответствуют профилю резьбы; в процессе работы профиль поверхности поддерживается путём правки.
Резьбонарезная головка, приспособление для нарезания наружной или внутренней резьбы на токарных, сверлильных и др. металлорежущих станках. В радиальных прорезях корпуса Р. г. установлено обычно 4 плашки или 4 резца. Плашки в Р. г. устанавливаются так, чтобы направление ниток одной плашки являлось продолжением ниток смежной плашки. Как правило, Р. г. имеет механизм автоматического вывода плашек в конце рабочего хода. Применяются также Р. г. с плашками, регулируемыми на требуемый диаметр резьбы.
Геометрия резца, форма и углы заточки режущей части резца. Г. р. влияет на характер процесса резания материалов, на его производительность и экономичность, качество обработанной детали, стойкость (время работы до нормального затупления) резца и т.п. Все определения по Г. р., приводимые ниже, справедливы для др. режущих инструментов (свёрл, протяжек, фрез). Режущую часть составляют рабочие поверхности (рис. 1): передняя, по которой сходит образующаяся в процессе резания стружка, задняя главная и задняя вспомогательная, обращенные к обрабатываемой поверхности заготовки. Рабочие поверхности при пересечении образуют режущие кромки.
Главная режущая кромка, выполняющая основную работу при резании, образуется в результате пересечения передней и главной задней поверхности; вспомогательная режущая кромка — при пересечении передней и вспомогательной задней поверхности. Место сопряжения главной и вспомогательной режущих кромок называется вершиной резца. Вершина резца — наиболее ослабленная его часть, определяющая прочность режущей части кромки резца в целом; поэтому для повышения прочности вершина резца делается либо закруглённой (с радиусом 0,5—2 мм), либо в виде прямолинейной переходной режущей кромки (длиной 0,5—3 мм).
Элементы режущей части резца подразделяют на статические, определяющие углы заточки инструмента, и кинематические, зависящие от характера процесса резания и от установки резца. Углы заточки определяют форму режущей части при проектировании, изготовлении и контроле резца. Режущая часть резца имеет форму клина, заточенного под определёнными углами. Для определения углов установлены следующие координатные плоскости: плоскость резания и основная плоскость. Плоскость резания — это плоскость, касательная к поверхности резания и проходящая через главную режущую кромку. Основная плоскость — плоскость, параллельная продольной (параллельной оси заготовки) и поперечной (перпендикулярной оси заготовки) подачам резца. Эти координатные плоскости взаимно перпендикулярны. Главные углы резца определяются в главной секущей плоскости, перпендикулярной проекции главной режущей кромки на основную плоскость (рис. 2). Главный задний угол — угол между главной задней поверхностью резца и плоскостью резания. При выборе заднего угла, во избежание трения задней поверхности резца об обрабатываемую поверхность и поверхность резания, учитывают величину подачи: чем она больше, тем больше задний угол. Угол заострения — угол между передней и главной задней поверхностями резца. Главный передний угол — угол между передней поверхностью резца и плоскостью, перпендикулярной плоскости резания. Выбор переднего угла зависит прежде всего от физико-механических свойств обрабатываемого материала. Чем больше передний угол, тем легче процесс образования стружки, тем меньше усилие резания и затрачиваемая мощность. Чем выше твёрдость обрабатываемого материала, тем меньшие значения передних углов резца принимают для его обработки. Угол резания — угол между передней поверхностью резца и плоскостью резания. Главный угол в плане — угол между направлением подачи и проекцией главной режущей кромки на основную плоскость; вспомогательный угол в плане 1 — угол между направлением подачи и проекцией вспомогательной режущей кромки на основную плоскость. Углы и 1 определяют, с одной стороны, условия работы режущей кромки, а с другой — распределение нагрузки от силы резания. Чем меньше угол в плане, тем (при неизменной глубине резания и подаче) меньше тепловая и силовая нагрузки на единицу длины главной режущей кромки, а следовательно, лучше условия работы. Уменьшение угла в плане ниже оптимального значения может привести к чрезмерной деформации обрабатываемой заготовки, к снижению точности обработки и вибрациям. Угол при вершине в плане — угол между проекциями режущих кромок на основную плоскость: = 180°— ( +1). Угол в плане переходной (прямолинейной) режущей кромки 0 — угол между направлением подачи и проекцией переходной режущей кромки на основную плоскость: обычно 0 = /2. Угол наклона главной режущей кромки — угол, заключённый между режущей кромкой и линией, проведённой через вершину резца параллельно основной плоскости; угол положительный, когда вершина резца — наинизшая точка режущей кромки; отрицательный, когда вершина резца — наивысшая точка, и равен нулю, если главная режущая кромка параллельна основной плоскости. Угол оказывает влияние на направление схода стружки.
Лит. см. при ст. Обработка металлов резанием.
В. В. Данилевский.


Рис. 2. Углы резания.

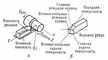
Рис. 1. Схема процесса резания (а) и основные элементы резца (б).
Стали.
Инструментальная сталь, углеродистая или легированная сталь для изготовления режущих и измерительных инструментов, штампов холодного и горячего деформирования, а также деталей машин, испытывающих повышенный износ при умеренных динамических нагрузках (шарико- и роликоподшипники, зубчатые колёса, ходовые винты в высокоточных станках и др.). Как правило, И. с. содержит более 0,6—0,7% С; исключение — штамповые стали для горячего деформирования, содержащие 0,3—0,6% С. Для улучшения эксплуатационных свойств И. с. подвергают термической обработке (закалке, отпуску), в результате которой твёрдость И. с. повышается до 60—66 HRC, прочность при изгибе — 2,5—3,5 Гн/м2 (250—350 кгс/мм2). С увеличением твёрдости повышается и износостойкость И. с. — способность сохранять неизменные размеры и форму рабочей поверхности при трении с высокими давлениями. И. с., легированные хромом и марганцем, обладают более высокой закаливаемостью и прокаливаемостью, чем углеродистые. Повышенная красностойкость И. с. — способность сохранять высокую твёрдость и износостойкость при температурах до 500—700 °С — достигается легированием сталей вольфрамом, молибденом, ванадием. В зависимости от устойчивости против нагрева, возникающего в процессе эксплуатации, И. с. подразделяют на три группы (см. табл.).
Химический состав широко распространённых в СССР инструментальных сталей,
% в среднем
Марка стали | C | Mn | Si | Cr | W | Mo | V |
Стали с небольшой устойчивостью против нагрева | |||||||
Углеродистые стали | |||||||
У8А | 0,8 | 0,25 | 0,25 | 0,1 | — | — | — |
У10А | 1,0 | 0,25 | 0,25 | 0,1 | — | — | — |
У12А | 1,2 | 0,25 | 0,25 | 0,1 | — | — | — |
У13А | 1,3 | 0,25 | 0,25 | 0,1 | — | — | — |
Низколегированные стали | |||||||
9ХФ | 0,9 | 0,4 | 0,25 | 0,55 | — | — | 0,2 |
11ХФ | 1,1 | 0,5 | 0,25 | 0,55 | — | — | 0,1 |
13Х | 0,3 | 0,4 | 0,25 | 0,55 | — | — | — |
В2Ф | 1,2 | 0,4 | 0,25 | 0,5 | 1,7 | — | 0,1 |
Легированные стали | |||||||
Х | 1,0 | 0,3 | 0,2 | 1,5 | — | — | — |
ХВСГ | 1,0 | 0,75 | 0,85 | 0,9 | 0,85 | — | 0,1 |
7ХГ2ВМ | 0,75 | 2,1 | 0,3 | 1,7 | 1,1 | 0,7 | 0,15 |
6ХС | 0,65 | 0,25 | 0,8 | 1,1 | — | — | — |
Стали с повышенной устойчивостью против нагрева | |||||||
Х6ВФ | 1,1 | 0,25 | 0,25 | 6 | 1,3 | — | 0,6 |
Х6Ф4М | 1,65 | 0,25 | 0,25 | 6 | — | 0,8 | 3,8 |
X12М | 1,55 | 0,25 | 0,25 | 12 | — | 0,5 | — |
55Х6В3СМФ | 0,55 | 0,25 | 0,8 | 6 | 3 | 0,8 | 0,8 |
Стали, устойчивые против нагрева (штамповые стали) | |||||||
4Х52ВФС | 0,4 | 0,25 | 1,0 | 5 | 2,0 | — | 0,8 |
4Х3БМФС | 0,4 | 0,35 | 0,8 | 3,5 | 1,0 | 1,4 | 0,7 |
3Х2В8Ф | 0,35 | 0,25 | 0,25 | 2,5 | 8,0 | — | 0,3 |
2Х8В8М2К5 | 0,25 | 0,25 | 0,4 | 7,5 | 7,5 | 1,8 | 8,0 |