Обработка металлов резанием
Вид материала | Документы |
Нарезание резьбы |
- Шифр специальности: 05. 16. 01 Металловедение и термическая обработка металлов и сплавов, 25.46kb.
- Обработка металлов давлением при обработке металлов давлением, 131.9kb.
- Программа профессиональной переподготовки мтф п/п-1 «металловедение и термическая обработка, 34.45kb.
- Лекция 7 термическая обработка металлов, 136.74kb.
- Научные основы и технологические способы обработки гетерофазных сплавов с высоким уровнем, 572.64kb.
- Программа вступительного испытания по направлению «Металлургия», 51.65kb.
- 05. 16. 01 Металловедение и термическая обработка металлов, 25.25kb.
- Развитие научных основ и разработка совмещенных методов обработки металлов давлением,, 606kb.
- Реферат по теме: «Металлы. Свойства металлов.», 196.2kb.
- Закономерности превращения, 589.18kb.
Шероховатость поверхности, совокупность неровностей, образующих микрорельеф поверхности детали. Возникает главным образом вследствие пластической деформации поверхностного слоя заготовки при её обработке из-за неровностей режущих кромок инструмента, трения, вырывания частиц материала с поверхности заготовки, вибрации заготовки и инструмента и т.п. Ш. п. — важный показатель в технической характеристике изделия, влияющий на эксплуатационные свойства деталей и узлов машин — износостойкость трущихся поверхностей, усталостную прочность, коррозионную устойчивость, сохранение натяга при неподвижных посадках и т.п. Требования к Ш. п. устанавливают, исходя из функционального назначения поверхностей деталей и их конструктивных особенностей. В сов. производстве длительное время применяли систему, характеризующую чистоту поверхности с соответствующими ей классами; новая система (введена с 1 января 1975) отменяет использовавшиеся ранее классы чистоты.
Расширенный комплекс параметров новой системы способствует установлению обоснованных требований для поверхностей различного эксплуатационного назначения. При определении числовых значений Ш. п. отсчёт производят от единой базы, за которую принята средняя линия профиля т (рис.). Измерения производят в пределах базовой длины l, т. е. длины участка поверхности, выбранного для измерения Ш. п. без учёта других видов неровностей (например, волнистости), имеющих шаг более l. Числовые значения базовой длины выбирают из ряда: 0,01; 0,03; 0,08; 0,25; 0,8; 2,5; 8; 25 мм. Количественно Ш. п. оценивают следующими основными параметрами (одним или несколькими): средним арифметическим отклонением профиля Ra, высотой неровностей профиля по 10 точкам Rz, наибольшей высотой неровностей профиля Rтах, средним шагом неровностей Sm, средним шагом неровностей по вершинам S, относительной опорной длиной профиля tp. Числовые значения параметров шероховатости, типы направлений неровностей поверхностей (параллельное, перпендикулярное, кругообразное и др.) установлены стандартом. Выбор параметров Ш. п. зависит от конструкции деталей и функционального назначения их поверхностей. Например, для трущихся поверхностей ответственных деталей устанавливают допустимые значения Ra (или Rz), Rтах, tp и направление неровностей; для поверхностей циклически нагруженных ответственных деталей — Rтах, Sm и S и т.п. Требования к Ш. п. указывают числовым значением (или диапазоном значений) одного или нескольких параметров и базовой длиной. Для неответственных поверхностей Ш. п. определяется требованиями технической эстетики, коррозионной стойкости и технологией изготовления.
В СССР стандартом установлены 14 классов Ш. п. (табл.): 1—3-й классы обеспечивают обдирочной обработкой (точением, фрезерованием, строганием); 4—6-й классы — получистовой обработкой; 7—9-й классы — чистовой обработкой (шлифованием, тонким точением, протягиванием, развёртыванием и т.п.); 10—14-й классы — доводочной обработкой (такие, как притирка) суперфиниш, хонингование и др.). Классы шероховатости с 6-го по 14-й разделяются на разряды а, б, в. В классах 1—5, 13 и 14-й не применяют параметр Ra, а в классах 6—12 — параметр Rz, что вызвано необходимостью однозначного определения класса Ш. п. при различных методах контроля. В отличие от применявшихся до 1975 обозначений классов чистоты на чертежах (равносторонний треугольник с добавлением к нему номера класса, например 3 или 7), Ш. п. обозначают знаком с указанием над ним числового значения (в мкм) одного из выбранных параметров шероховатости. Значение Ra указывают только числом, а др. параметры — с символом, например Rz3,2. Указанное числовое значение ограничивает наибольшую Ш. п. по параметрам Ra или Rz. Поверхности в состоянии поставки или обработанные без снятия стружки обозначают символом


Начальная Ш. п., которую детали получают после их изготовления и сборки, изменяется в процессе приработки. Получающаяся после приработки (при трении качения, трении скольжения и др.) Ш. п., обеспечивающая минимальный износ и сохраняющаяся в ходе длительной эксплуатации машин, называется оптимальной шероховатостью. Параметры оптимальной Ш. п. зависят от конструкции и материала трущихся деталей, качества смазки и других условий работы.
Для измерения Ш. п. обычно применяют следующие методы: контактный—щуповыми приборами (профилометрами и профилографами) и бесконтактный — оптическими приборами. В машиностроении часто используют визуальный метод, сравнивая контролируемую поверхность с поверхностью образца или детали, Ш. п. которой аттестована.
Классы шероховатости поверхности
Классы | Параметры шероховатости, мкм | Базовая длина l, мм | ||
Разряды | Ra | Rz | ||
1 | — | — | 320—160 | 8 |
2 | — | — | 160—80 | |
3 | — | — | 80—40 | |
4 | — | — | 40—20 | 2,5 |
5 | — | — | 20—10 | |
6 | а | 2,5—2,0 | — | 0,8 |
б | 2,0—1,6 | |||
в | 1,6—1,25 | |||
7 | а | 1,25—1,0 | — | |
б | 1,0—0,80 | |||
в | 0,80—0,63 | |||
8 | а | 0,63—0,50 | — | |
б | 0,50—0,40 | |||
в | 0,40—0,32 | |||
9 | а | 0,32—0,25 | — | 0,25 |
б | 0,25—0,20 | |||
в | 0,20—0,16 | |||
10 | а | 0,160—0,125 | ||
б | 0,125—0,100 | |||
в | 0,100—0,080 | |||
11 | а | 0,080—0,063 | ||
б | 0,063—0,050 | |||
в | 0,050— 0,040 | |||
12 | а | 0,040—0,032 | ||
б | 0,032—0,025 | |||
в | 0,025—0,020 | |||
13 | а | | 0,100—0,080 | 0,08 |
б | 0,080—0,063 | |||
в | 0,063—0,050 | |||
14 | а | | 0,050—0,040 | |
б | 0,040—0,032 | |||
в | 0,032-0,025 |
Лит.: Якушев А. И., Взаимозаменяемость, стандартизация и технические измерения, 4 изд., М., 1975; ГОСТ 2789—73. Шероховатость поверхности. Параметры и характеристики; ГОСТ2.309—73. Обозначения шероховатости поверхностей.
О. А. Владимиров, А. А. Пархоменко.

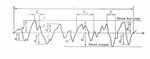
Действительный профиль (профилограмма) поверхности: 1 — выступ профиля; 2 — местная впадина; 3 — местный выступ; 4 — впадина профиля.
Точение, токарная обработка, одна из основных операций обработки резанием, выполняемая на металлорежущих станках и деревообрабатывающих станках токарной группы, обычно при вращательном движении изделия и поступательном движении резца.
Фрезерование в металлообработке, процесс резания металлов и др. твёрдых материалов фрезой. Ф. применяется для обработки плоских и фасонных поверхностей (в т. ч. резьбовых поверхностей, зубчатых и червячных колёс) и осуществляется на фрезерных станках. Схема Ф. цилиндрической фрезой показана на рис. 1. Главное движение при Ф. — вращение инструмента, движение подачи — поступательное перемещение заготовки; скорость резания равна окружной скорости наиболее удалённых от оси фрезы точек её зубьев. При Ф. различают три вида подачи. Минутная подача S (в мм/мин); подача на один оборот фрезы S0 (в мм/об); подача на один зуб фрезы Sz (в мм/зуб) — относительное перемещение фрезы и заготовки при повороте фрезы на один угловой шаг =

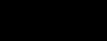
где z — число зубьев фрезы, n — частота вращения фрезы (об/мин). Глубина резания t (мм) при Ф. — толщина срезаемого слоя металла, измеренная перпендикулярно к обработанной поверхности. Ширина Ф. В (мм) — ширина обрабатываемой поверхности в направлении, параллельном оси фрезы. Существуют две возможные схемы Ф.: против подачи (встречное Ф.), когда в нижней точке контакта фрезы с обрабатываемой заготовкой векторы скорости резания и подачи противоположны (рис. 2, а), и по подаче (попутное Ф.), когда эти векторы совпадают (рис. 2, б), amax — наибольшая толщина срезаемого слоя металла; — угол контакта фрезы. При черновом Ф. обычно применяется вторая схема, при чистовом Ф. — первая. Площадь поперечного сечения слоя металла, срезаемого зубом фрезы, меняется в каждый момент времени резания и, следовательно, меняются и действующие на зуб силы. Равномерное Ф. может быть достигнуто при использовании фрез с винтовыми зубьями, работа которых характеризуется примерным постоянством площади поперечного сечения срезаемого слоя металла. Основное технологическое время при Ф.:

где L — общая длина прохода заготовки (в мм) относительно фрезы в направлении подачи, i — число проходов. Скорость резания, допускаемая при Ф., зависит от типа фрезы, материала и геометрических параметров её режущей части и др. элементов, режима резания, состояния поверхностного слоя заготовки и т.п. (см. Обработка металлов резанием). В процессе Ф. возникают силы сопротивления резанию. По окружной силе может быть определён крутящий момент на шпинделе фрезерного станка. Осевая сила действует на подшипник шпинделя станка, устройство для закрепления заготовки, а также детали и узлы механизма подачи. Радиальная сила действует на опоры шпинделя и оправку, в которой закрепляется фреза. Горизонтальная сила нагружает механизм подачи и устройство для закрепления заготовки. В деревообработке Ф. может осуществляться также на фуговальных станках, рейсмусовых станках и др. с помощью ножевых валов или головок со вставными ножами (см. Дереворежущий инструмент).
Лит. см. при ст. Обработка металлов резанием.
Д. Л. Юдин.


Рис. 1. Схема резания при фрезеровании цилиндрической фрезой: 1 — обрабатываемая поверхность; 2 — обработанная поверхность; 3 — поверхность резания.

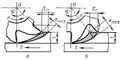
Рис. 2. Схемы фрезерования: а — против подачи; б — по подаче.
Растачивание, процесс механической обработки внутренних поверхностей расточными резцами с целью увеличения диаметра. Р. осуществляется на токарных, расточных и др. металлорежущих станках. Можно обрабатывать сквозные и глухие цилиндрическими и коническими отверстия, выемки, канавки и др. Точность обработки при Р. — 4—5-го классов, шероховатость поверхности — 2—3-го классов чистоты.
Зенкерование, способ обработки поверхностей отверстий, предварительно просверлённых, полученных горячей или холодной штамповкой и литьём. З. применяют при обработке цилиндрических отверстий, углублений под головки или шейки болтов и винтов, торцевых поверхностей бобышек под шайбы, упорные кольца и т.п. З. является также промежуточной операцией после сверления перед развёртыванием. Повышает точность и чистоту поверхности, т.к. зенкер, в отличие от сверла, имеет больше режущих кромок. Отверстие, полученное З., имеет более точное по сравнению со сверлёным направление оси, поэтому З. широко применяют при чистовой и получистовой обработке. З. выполняется на сверлильных, револьверных и расточных станках.
Развёртывание, одна из разновидностей обработки отверстий резанием (после сверления и зенкерования) многолезвийным режущим инструментом — развёрткой. В результате чернового Р. снимается припуск на обработку не более 0,5 мм на диаметр, обеспечиваются шероховатость поверхности 7-го класса, точность 3-го класса. При чистовом Р. снимается припуск не более 0,2 мм; шероховатость — до 9-го класса, точность — до 2-го.
Рассверливание, процесс механической обработки сверлом имеющегося отверстия с целью увеличения его диаметра. Р. осуществляется на сверлильных, расточных, токарных и др. металлорежущих станках, а также вручную — сверлильными электрических или пневматических машинками, дрелью и др. Точность обработки при Р. — 4—5-го классов, шероховатость поверхности — 2—3-го классов.
Нарезание резьбы, технологические процессы получения резьбы снятием стружки на поверхностях различных деталей. Н. р. производят на специализированных резьбонарезных, гайконарезных, болтонарезных, резьбофрезерных, резьбошлифовальных, а также на токарных (в том числе автоматах и полуавтоматах) и револьверных станках.
Простейший способ Н. р. — при помощи метчиков и плашек — осуществляется вручную, на гайконарезных или болтонарезных станках. На токарных станках резьбу нарезают резцами за несколько проходов (рис. 1). Резьбу с шагом S 2,5 мм нарезают по профильной схеме с радиальной подачей, резьбу с шагом S 2,5 мм нарезают вначале по генераторной схеме с боковой подачей (черновые проходы), затем по профильной схеме (чистовые). Н. р. резцом — процесс малопроизводительный, но позволяющий при небольших подачах получать резьбу с малой шероховатостью поверхности (класс чистоты 8—9), с 4-й степенью точности. Производительность повышается при Н. р. резьбовыми гребёнками и резьбовыми фрезами, так как при этом Н. р. можно осуществить за один проход. Наиболее прогрессивный способ, названный скоростным, или вихревым, обеспечивает повышение производительности в 2—2,5 раза по сравнению с резьбофрезерованием и более чем в 10 раз по сравнению с Н. р. резцом. Н. р. при этом производят резцовыми головками методами схватывания и огибания (). Резцовая головка с одним или несколькими резцами, оснащенными пластинами из твёрдого сплава, расположена эксцентрично по отношению к обрабатываемой заготовке. Заготовка совершает от 30 до 300 об/мин в одном направлении, а резцовая головка — от 1000 до 3000 об/мин в противоположном направлении. Заготовке за один её оборот сообщается осевая подача на один шаг резьбы; каждый резец приходит в соприкосновение с заготовкой один раз за оборот головки. Скорость резания достигает 400 м/мин. Метод применим для Н. р. как на наружных, так и на внутренних поверхностях при диаметре более 50 мм и обеспечивает шероховатость поверхности 6-го класса (6) и 5—6-ю степень точности. Получение резьбы возможно пластической деформацией (см. Накатка резьбы).
Лит.: Барбашов Ф. А., Резьбофрезерные работы, 2 изд., М., 1970; Данилевский В. В., Технология машиностроения, М., 1972; Справочник технолога машиностроителя, 3 изд., т. 1—2, М., 1972.
А. Ф. Дубровский.

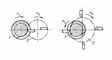
Рис. 2. Схема вихревого нарезания резьбы: а — методом схватывания; б — методом огибания; 1 — заготовка; 2 — резцовая головка; nз — направление вращения заготовки; np — направление вращения резцовой головки.


Рис. 1. Схема нарезания резьбы на токарном станке: а — по профильной схеме резания; б — по генераторной схеме; 1 — резьбовой профиль; 2 — резец; S — величина подачи резца, равная шагу резьбы; Sp — радиальная подача; SБ — боковая подача.