Лекция 13. Сварка металлов. Ее роль в современном производстве
Вид материала | Лекция |
- Пятый физические основы сваривания металлов, 781.92kb.
- Программа вступительного экзамена в аспирантуру по специальности 05. 03. 06 «Сварка, 131.86kb.
- История развития сварки в России, 33.92kb.
- Лекция 16. Способы сварки давлением. Контактная сварка. Стыковая, точечная, шовная, 82.74kb.
- Государственный стандарт союза сср сварка, пайка и термическая резка металлов гост, 487.3kb.
- Ю. М. Дедков, М. Г. Слотинцева Сб. «Свойства и применение платиновых металлов и сплавов, 100.81kb.
- Лабораторная работа №2 Автоматическая сварка под слоем флюса, 33.88kb.
- Тема: сварка алюминия и его сплавов, 56.75kb.
- Лекция 4 Концептуальные уровни в познании веществ и химические системы, 94.08kb.
- Реферат по теме: «Металлы. Свойства металлов.», 196.2kb.
Лекция 13. Сварка металлов. Ее роль в современном производстве.
Сваркой называется процесс соединения металлических и неметаллических материалов, при котором устанавливаются межатомные и межмолекулярные связи по контактируемым поверхностям соединяемых деталей.
Сварка имеет применение в промышленности, как при изготовлении новых изделий, так и при ремонтных работах.
Сварка наряду с литьем, обработкой металлов давлением, резанием является основным технологическим процессом изготовления различных металлических конструкций и изделий.
Преимущества процессов сварки по сравнению с другими способами соединения металлов состоят в следующем:
1. в сварных соединениях отсутствует ослабление металла отверстиями, которые необходимы в клепаных соединениях;
2. в сварных соединениях нет необходимости применять промежуточные элементы, например, уголки;
3. по сравнению с литыми сварные конструкции дают большую экономию металла за счет его рационального использования, так как в литых конструкциях в одном узле не допускается сочетание тонких и толстых стенок;
4. при изготовлении сложных и тяжелых кованых изделий можно использовать принцип разделения их на ряд простых, несложных поковок с последующим соединением в одно целое с помощью сварки. При таком способе уменьшается время изготовления, упрощается технология. В настоящее время получили распространение штампосварные конструкции. Нашли применение и сварные комбинированные конструкции из проката, поковок и литья.
Сварные конструкции имеют особенности, которые могут отрицательно влиять на их прочность и надежность. Основными из них являются:
-повышенная чувствительность к концентраторам напряжений и к хрупким разрушениям;
-изменение исходных свойств основного материала в зоне сварного шва;
-остаточные деформации и напряжения.
Влияние этих факторов можно исключить выбором схемы конструкции, правильным выбором основного и сварочного материалов, назначением оптимальной технологии заготовительных, сборочных и сварочных операций.
Физические основы получения сварного соединения
и классификация способов сварки
Физическая сущность процесса сварки заключается в установлении прочных межатомных и межмолекулярных связей по контактируемым поверхностям соединяемых деталей. Это достигается сближением соединяемых поверхностей на расстояния порядка 10-8 см, что соизмеримо с параметрами кристаллических решеток этих металлов и созданием необходимых условий: температуры нагрева, времени контакта и качества поверхностей. Образуются общие для соединяемых заготовок кристаллические решетки.
Применяется сварка плавлением и сварка давлением.
При сварке плавлением происходит расплавление кромок заготовок (при необходимости и присадочного прутка) для заполнения зазора между ними. Образуется общая сварочная ванна расплавленного металла, в которой по мере удаления источника нагрева происходит процесс кристаллизации металла, образуя сварочный шов.
К сварке плавлением относятся: дуговая сварка, электрошлаковая, газовая, электронно-лучевая и др.
При сварке давлением соединение заготовок производится пластической деформацией соединяемых поверхностей. Пластическая деформация осуществляется путем приложения внешних сил и нагрева для снижения сопротивления деформации. В процессе деформации происходит смятие неровностей и течение металла вдоль соединяемых поверхностей. Этим обеспечивается необходимый контакт между заготовками и условия для возникновения межатомных связей.
К сварке давлением относятся: контактная, диффузионная, ультразвуковая, взрывом, трением, холодом и др.
Элементы сварного соединения
Сварным соединением называется элемент сварной конструкции, состоящий из двух или нескольких деталей и сварного шва, соединяющего эти детали (рис.1.).
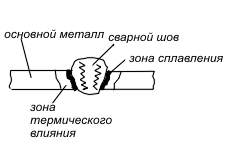
Рис.1. Сварное соединение
Сварной шов–участок сварного соединения, образовавшийся в результате кристаллизации сварочной ванны.
Основным дефектом сварного шва является возникновение в металле шва кристаллизационных (горячих) трещин вследствие литейной усадки металла шва, дендритной кристаллизации шва и наличия легкоплавких соединений в металле шва. Затвердевание легкоплавких соединений в уже закристаллизовавшемся металле приводит к образованию усадочных раковин (горячих трещин).
Зона сплавления–зона, где находятся частично сплавившиеся зерна металла на границе основного металла и шва. Толщина доны 0,2 мм.
К числу дефектов в зоне сплавления можно отнести:
1)образование трещин вследствие выделения водорода из металла шва в момент его кристаллизации;
2)образование межкристаллитной коррозии при сварке нержавеющих сталей (ножевая коррозия).
Зона термического влияния (ЗТВ)–участок основного металла, не подвергшийся расплавлению, структура и свойства которого изменились в результате нагрева.
В этой зоне могут возникнуть закалочные структуры, межкристаллитная коррозия, увеличиться зерно металла и, как следствие, возникнуть трещины.
Основной металл–из него изготавливается конструкция.
Общее требование, предъявляемое к сварным соединениям заключается в достижении равной прочности и коррозионной стойкости основного металла и металла шва.
С
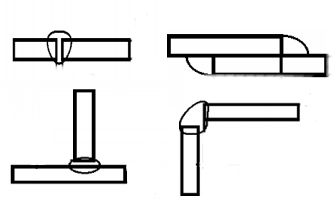
стыковые
нахлесточные
тавровые
угловые
Электрическая дуговая сварка
Электрическая дуговая сварка–термический способ получения сварного соединения, при котором источником нагрева является электрическая дуга.
Различают:
- сварку неплавящимся электродом
- сварку плавящимся электродом
- сварку дугой косвенного действия
- сварку трехфазной дугой.
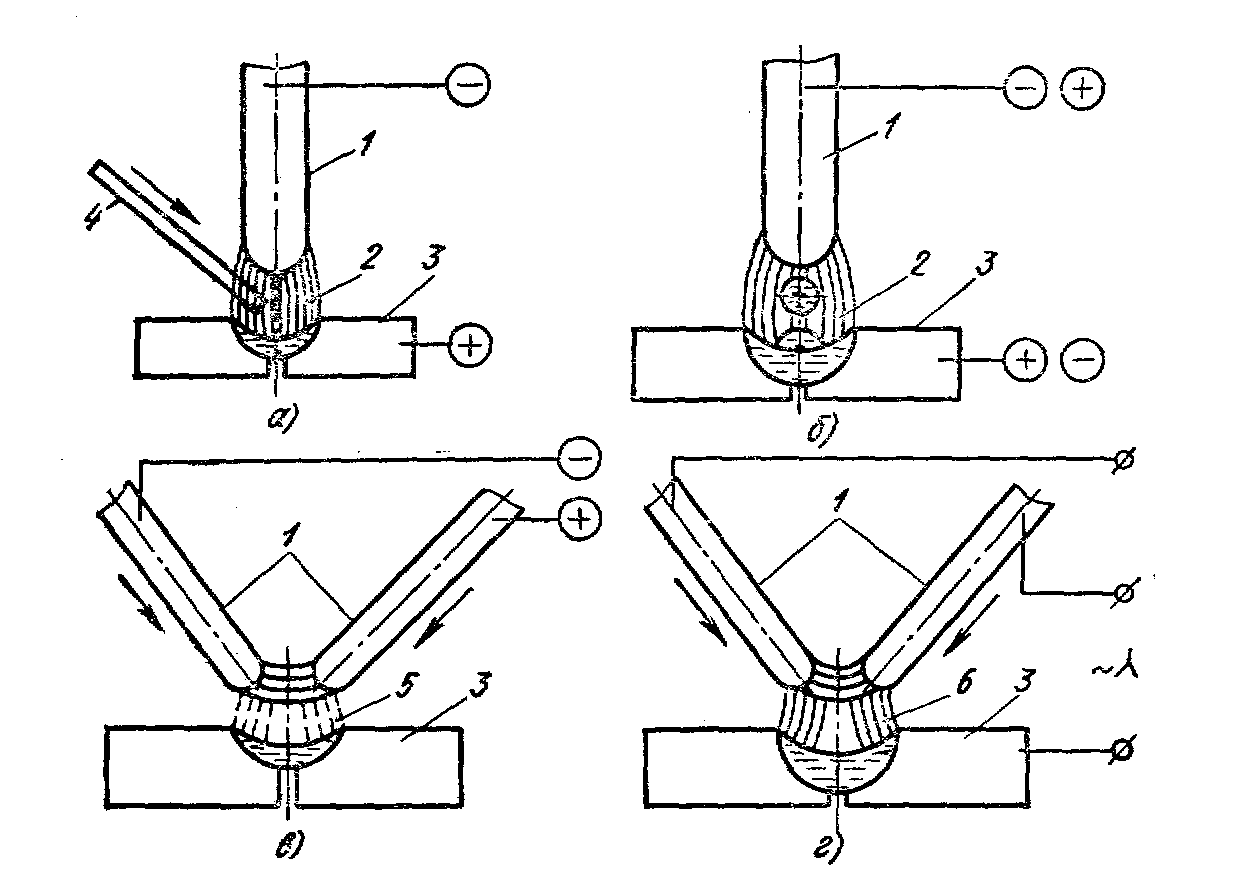
Рис.2. Сварка неплавящимся электродом (а); сварка плавящимся электродом (б); сварка дугой косвенного действия (в); сварка трехфазной дугой (г).
Сварка неплавящимся электродом (метод Бенардоса)
Это сварка угольным или вольфрамовым электродом. Дуга 2 горит между электродом 1 и изделием 3. Теплотой дуги расплавляются кромки свариваемого изделия и присадочный пруток 4. Образующийся при этом жидкий металл сварочной ванны перемешивается с присадочным. После остывания и кристаллизации жидкого металла образуется сварной шов.
Сварка производится на постоянном токе как на прямой полярности (электрод становится катодом (–), заготовка – анодом (+), так и на обратной полярности (плюс на электрод, он становится анодом, минус на заготовку, она становится катодом). В этом случае дуга становится неустойчивой.
Ввиду того, что сварочная ванна не защищена от действия атмосферного воздуха, механические и пластические свойства наплавленного металла низкие. Сварку, как правило, ведут в среде защитных газов. Применяется при сварке тонкостенных деталей с отбортовкой, дуговой резке и наплавке металлов, для заварки дефектов литья, сварки цветных металлов.
Сварка плавящимся электродом (метод Славянова)
Дуга 2 постоянного (при прямой или обратной полярности) или переменного тока горит между плавящимся металлическим электродом 1 и свариваемым изделием 3. Электрод подается в сварочную ванну, расплавляется и пополняет сварочную ванну жидким металлом, то есть является одновременно и присадочным металлом. В качестве электрода используется сварочная проволока (лента или пластина), близкая по химическому составу к свариваемому материалу.
Этот способ имеет наибольшее производственное значение. Применяется при изготовлении новых конструкций и при ремонтных работах.
Сварной шов может образовываться и без участия присадочного металла за счет расплавления отбортованных кромок. При питании дуги постоянным током расход электродов оказывается неодинаковым (вследствие различного тепловыделения на аноде и катоде), поэтому питание дуги осуществляется источником переменного тока, что обеспечивает равномерный расход электродов.
Сварка дугой косвенного действия
В этом случае дуга 5 горит между двумя неплавящимися электродами 1. Основной металл заготовок 3 нагревается и плавится теплом, излучаемым столбом дуги. Применяется при сварке тонкого металла. Процесс малопроизводительный.
Сварной шов может образовываться и без участия присадочного металла за счет расплавления отбортованных кромок. При питании дуги постоянным током расход электродов оказывается неодинаковым вследствие различного тепловыделения на аноде и катоде. Поэтому питание дуги осуществляется источником переменного тока, что обеспечивает равномерный расход электродов.
Сварка трехфазной дугой
Два электрода 1 и заготовки 3 подключены к разным фазам трехфазного тока. Дуга 6 возникает между электродами, а также между каждым электродом и основным металлом.
По производительности сварка трехфазной дугой в 2–3 раза превышает дуговую сварку по способу Славянова. Этот метод преимущественно используют при автоматической сварке под слоем флюса для металла большой толщины.
Электрическая сварочная дуга и ее свойства
Электрическая сварочная дуга представляет собой электрический разряд в газообразной среде, который сопровождается выделением большого количества тепла и света. Температура столба дуги достигает 6000оС. Процесс зажигания дуги состоит из 3–х этапов:
1) короткое замыкание электрода на заготовку
2) отвод электрода от заготовки на расстояние 3 – 6 мм
3) возникновение устойчивого дугового разряда.
Короткое замыкание выполняется для разогрева торца электрода и заготовки в зоне контакта с электродом. После отвода электрода с его разогретого торца (катода) под действием электрического поля начинается эмиссия электронов. Электроны, вылетевшие с поверхности катода, направляются к аноду и, сталкиваясь на своем пути с молекулами и атомами паров и газов, расщепляют их на положительные ионы и отрицательные электроны. В результате дуговой промежуток становится электропроводным и через него начинается разряд электричества. Взаимная бомбардировка катода положительными ионами и анода отрицательными электронами переводит кинетическую энергию этих частиц в тепловую энергию, происходит нагрев и расплавление электродного и основного металлов.
Полная тепловая мощность дуги рассчитывается по формуле:
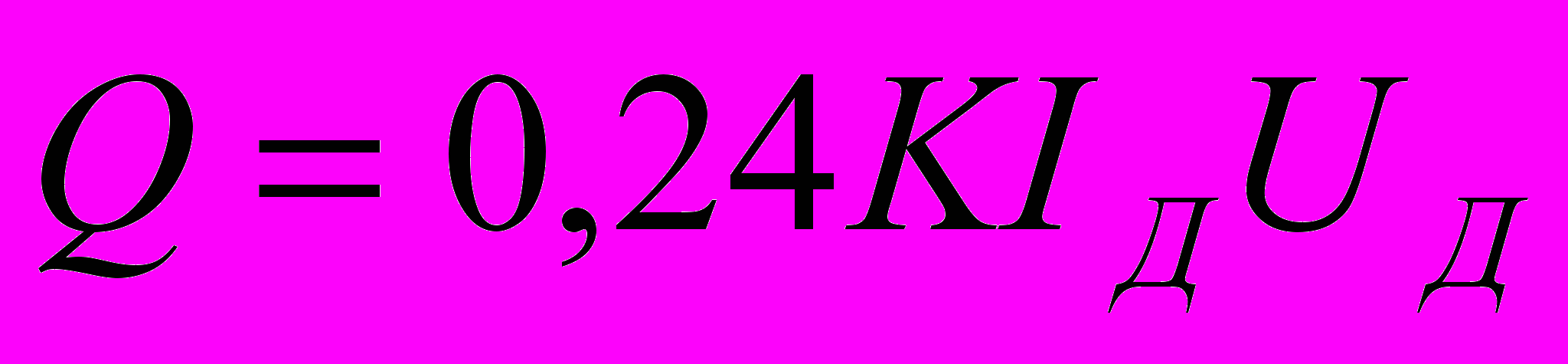
где: К–коэффициент несинусоидальности напряжения и тока. Для постоянного тока К=1, для переменного тока К=0,7–0,9.
IД – сварочный ток, А;
UД – напряжение дуги, В.
Не все тепло дуги расходуется на плавление присадочного и основного металлов.
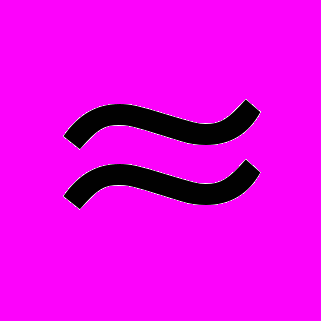
Электрические свойства дуги выражаются статической вольтамперной характеристикой, которая представляет собой зависимость между напряжением на дуге и током дуги (рис.3а). Характеристика состоит из трех участков: I, II, Ш, каждому из которых присущи свои особенности.
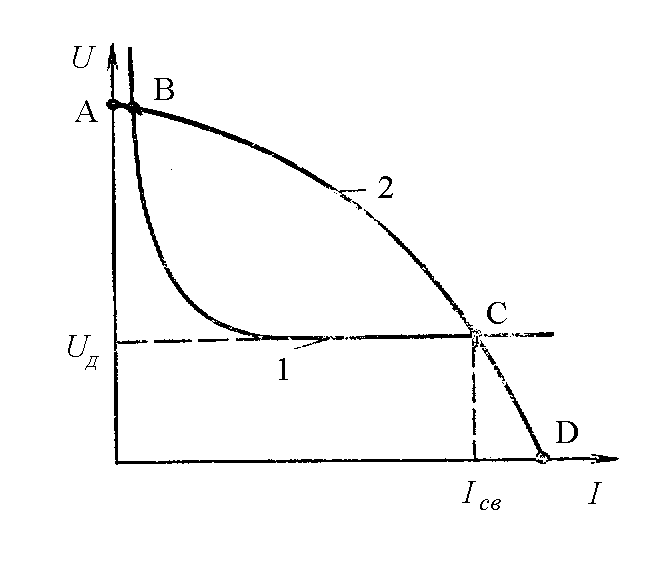
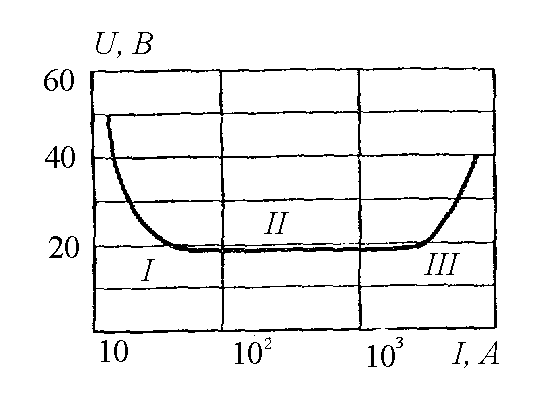
а) б)
Рис.3. Вольтамперная характеристика дуги (а) и совмещенная вольтамперная характеристика дуги и источника тока (б)
Как видно из рисунка, она может быть:
-падающая – участок I. Дуга с падающей характеристикой малоустойчива и имеет ограниченное применение.
-жесткая – участок II. Дуга с жесткой характеристикой, когда напряжение не зависит от силы тока, имеет самое широкое применение. На этом участке напряжение дуги определяется длиной дуги:
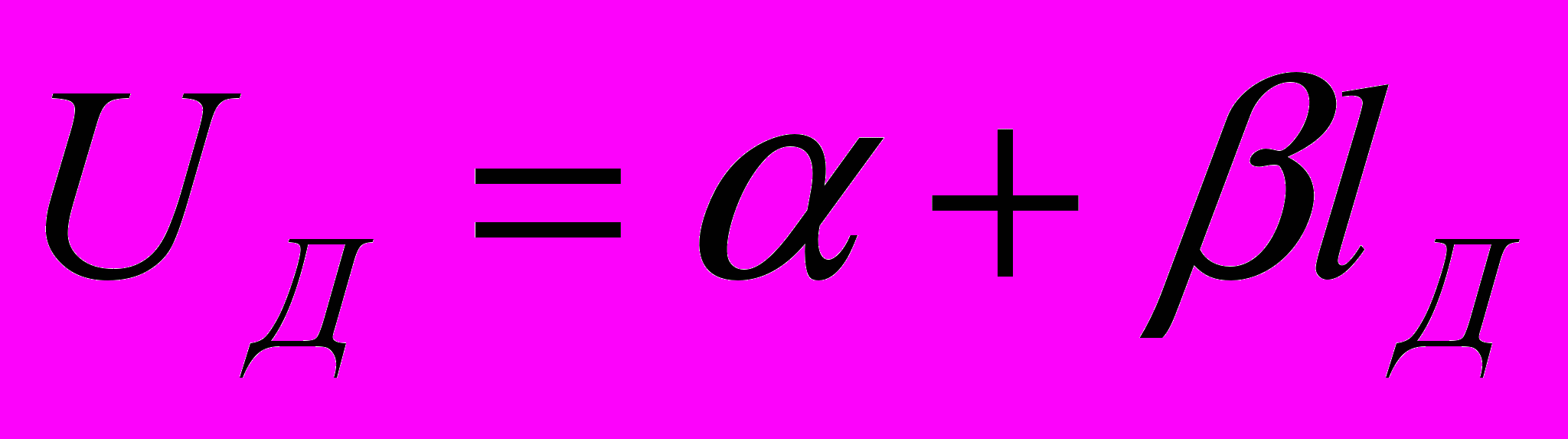
где:
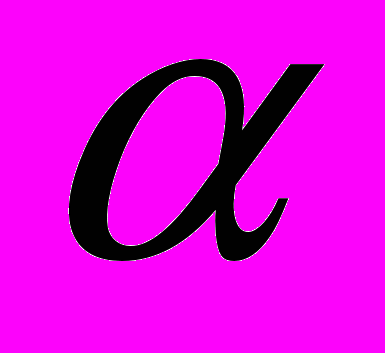
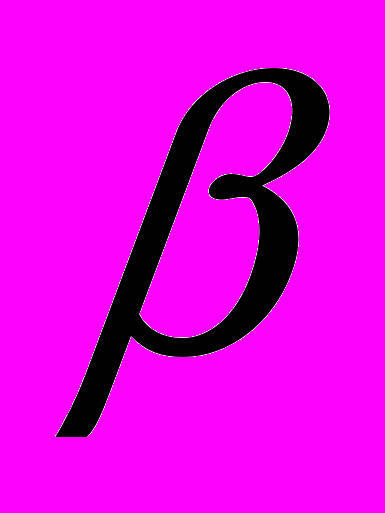
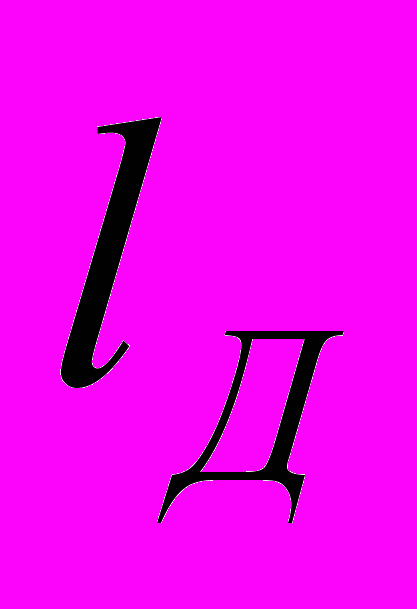
-возрастающая – участок III. Дуга с возрастающей характеристикой применяется при автоматической сварке под слоем флюса на повышенных режимах и при сварке в среде защитных газов плавящимся электродом.
Для обеспечения высокого качества сварных соединений необходимо устойчивое горение дуги. Постоянный ток обеспечивает высокую устойчивость дуги. При переменном токе дуга периодически гаснет и возбуждается вновь.
Источниками переменного тока являются сварочные трансформаторы. Источниками постоянного тока – генераторы и выпрямители.
Более широкое применение имеет сварка на переменном токе, так как оборудование для сварки на переменном токе значительно дешевле, имеет меньший вес, габариты, проще в эксплуатации. Кроме того, к.п.д. сварочных трансформаторов составляет 0,8–0,85, а агрегатов на постоянном токе – 0,3–0,6. При сварке переменным током расход электроэнергии на 1кг наплавленного металла достигает 3–4 кВт·ч/кг, а при сварке постоянным током – 6–10 3–4 кВт.
Для повышения устойчивости дуги на переменном токе применяют следующие методы:
1)короткие дуги
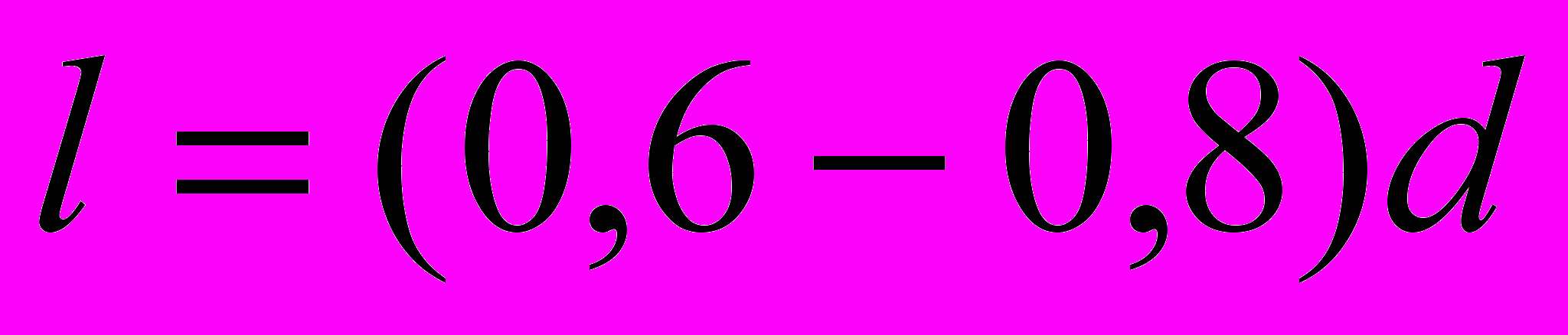
2)увеличение частоты тока до 150-450 Гц.
3)применение обмазки электродов, которые повышают степень ионизации дугового промежутка.
4)наложение тока высокой частоты от специального осциллятора. Ток от осциллятора непрерывно ионизирует дуговой промежуток.
Загрязнение поверхности изделия маслом, краской и т.п. резко ухудшает стабильность горения дуги.
Источники тока характеризуются внешней характеристикой, представляющей собой зависимость напряжения на его выходных клеммах (зажимах) от нагрузки – тока в электрической цепи. Для того, чтобы дуга с жесткой характеристикой горела устойчиво, необходима крутопадающая характеристика источника тока (рис.3б). На рисунке: 1– статическая характеристика дуги: 2 – внешняя характеристика источника питания. Источники тока с крутопадающей характеристикой удовлетворяют следующим требованиям:
- обеспечивают легкое зажигание и устойчивое горение дуги;
- ограничивают ток короткого замыкания;
- безопасны в работе.
На рис.3б точка А соответствует режиму холостого хода источника тока (величина сварочного тока I =0; для источников постоянного тока величина этого напряжения должна быть не ниже 30–35 В, для источников переменного тока – не менее 50–55 В. Напряжение холостого хода из соображений безопасности не должно превышать UX.X= 60 – 80 B). Дуга отсутствует. Точка D соответствует режиму короткого замыкания (напряжение короткого замыкания UК.З=0; IК.З. =IМАХ). Точка В соответствует моменту зажигания и неустойчивому горению дуги. Точка С соответствует рабочему сварочному режиму с устойчивым горением дуги и величиной сварочного тока IСВ.
Для питания дуги с возрастающей статической характеристикой более пригодны источники тока с жесткой или возрастающей внешней характеристикой.