Методические указания к выполнению курсового проекта для студентов всех форм обучения Специальность: 080502/5 Экономика и управление на предприятии химической
Вид материала | Методические указания |
СодержаниеПроизводственная мощность |
- Методические указания к изучению дисциплины и выполнению контрольной работы для студентов, 518.49kb.
- Методические указания к выполнению курсовой работы для студентов всех форм обучения, 524.31kb.
- Программа и методические указания для студентов всех форм обучения Специальность 080502/5, 198.27kb.
- Тамбовский Государственный Технический Университет внешнеэкономическая деятельность, 218.63kb.
- Методические указания к выполнению курсовой работы на тему «Планирование объема ремонтных, 1135.96kb.
- Методические указания к выполнению контрольной работы для студентов всех форм обучения, 330.41kb.
- Методические указания к изучению дисциплины и выполнению контрольной работы для студентов, 151.06kb.
- Методические указания к выполнению курсовой работы по специальности 060800 Экономика, 313.82kb.
- Методические указания к изучению дисциплины и выполнению контрольной работы для студентов, 575.27kb.
- Методические указания по выполнению выпускной квалификационной работы специальность, 289.49kb.
Производственная мощность характеризует максимально возможный объём производства продукции при оптимальном уровне организации и использования всех факторов производства за определенный период времени.
При организации многостадийного производства необходимо, в первую очередь, определить среднегодовую производственную мощность каждого производственного звена (участка, стадии и т.п.), после чего определяется мощность производства (цеха, предприятия) в целом.
В зависимости от особенностей организации производства (непрерывное, прерывное, периодическое) применяется соответствующая методика расчета производственной мощности.
Для условий непрерывного производства следует руководствоваться следующей формулой расчета производственной мощности участка (отдельной технологической стадии):
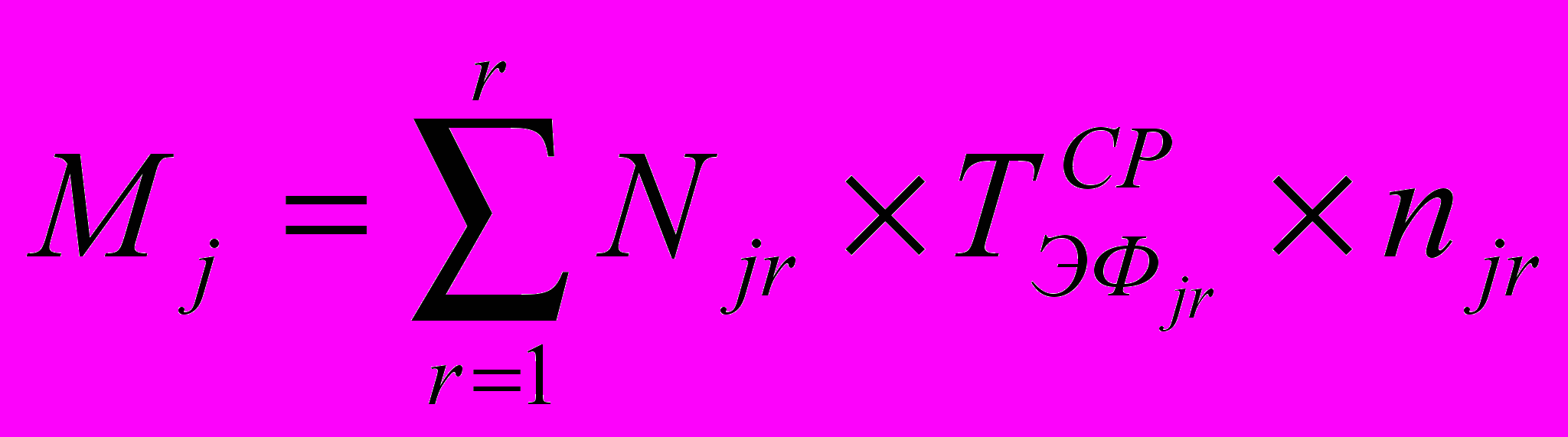
где:
Мj – среднегодовая производственная мощность j-го участка в течение межремонтного цикла;
Njr - часовая производительность единицы r-го вида однотипного оборудования j-го участка;
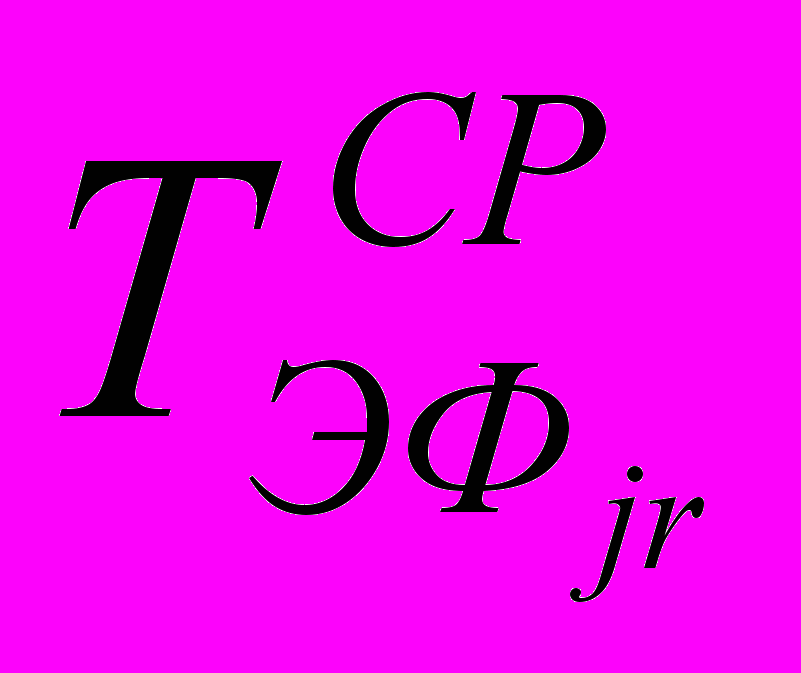
njr – количество единиц r-го вида однотипного оборудования, установленного на j-ом участке;
r – количество видов однотипного оборудования j-го участка.
Для условий периодического производства может быть использована следующая формула расчета производственной мощности участка:
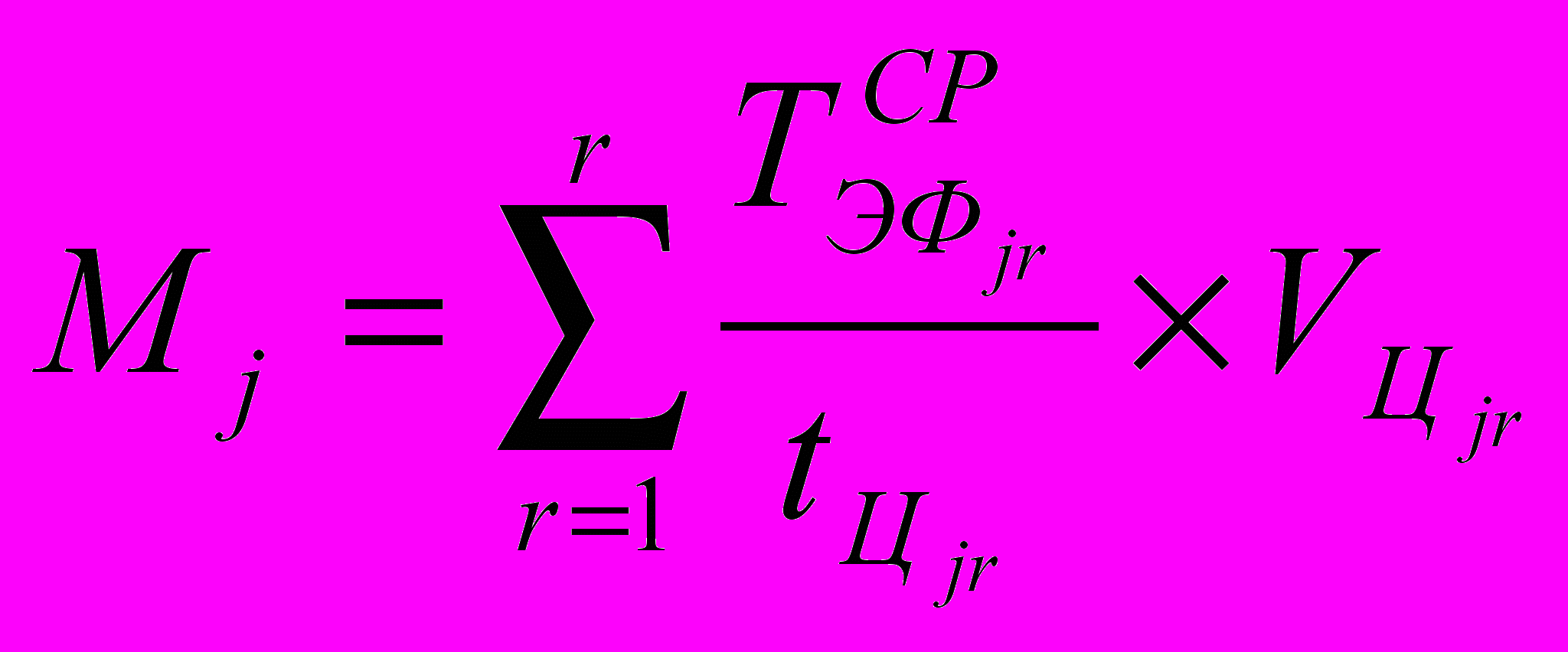
где:
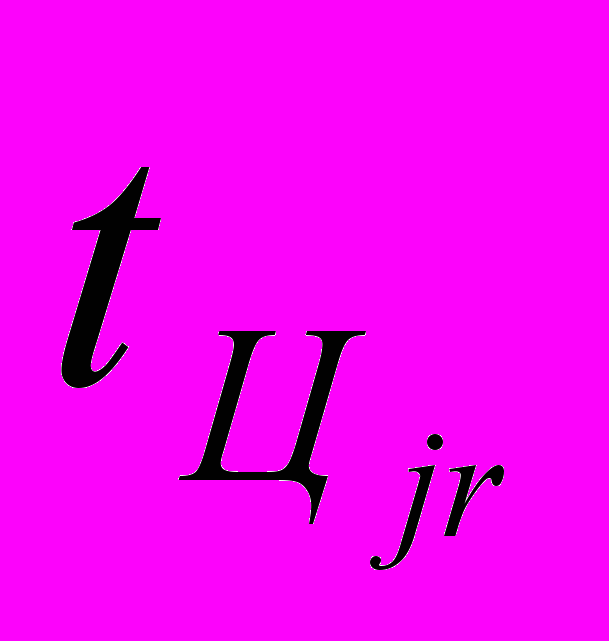
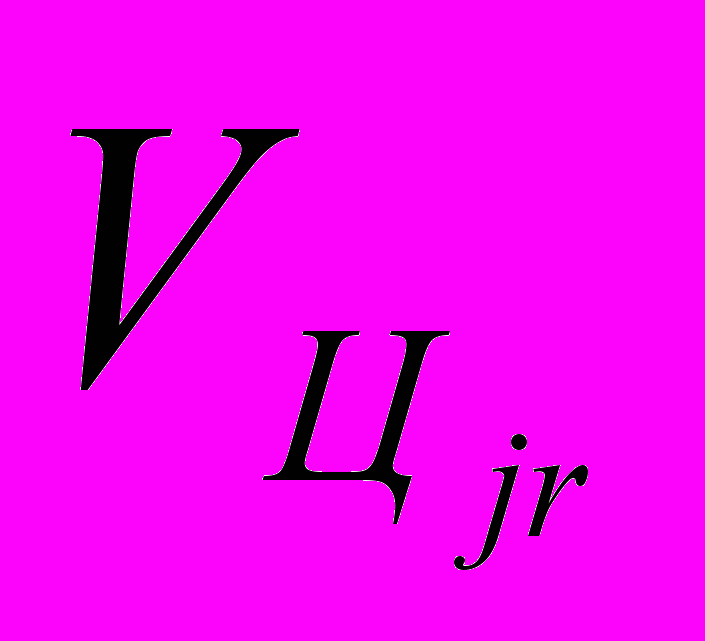
Производственная мощность производства (цеха, предприятия) в целом определяется уровнем производственной мощности ведущего участка (оборудования, стадии, передела), т.е.:
Мцех = Мвед (9)
Ведущее оборудование (стадия, участок) выбирается на основе соответствующих признаков. В качестве таких признаков могут быть рекомендованы:
- сложность и уникальность оборудования или процесса, осуществляемого с его помощью;
- получение целевого (конечного) продукта и т.д.
2.6 Построение профиля производственной мощности и его анализ
Профиль производственной мощности цеха составляется путем построения диаграммы мощностей отдельных участков, расположенных по ходу последовательного выполнения производственных операций (процессов, стадий), пример которого показан на рис.1 (ведущий – -й участок).
Анализ профиля производственной мощности сводится к определению коэффициентов сопряженности отдельных j-х участков производства (
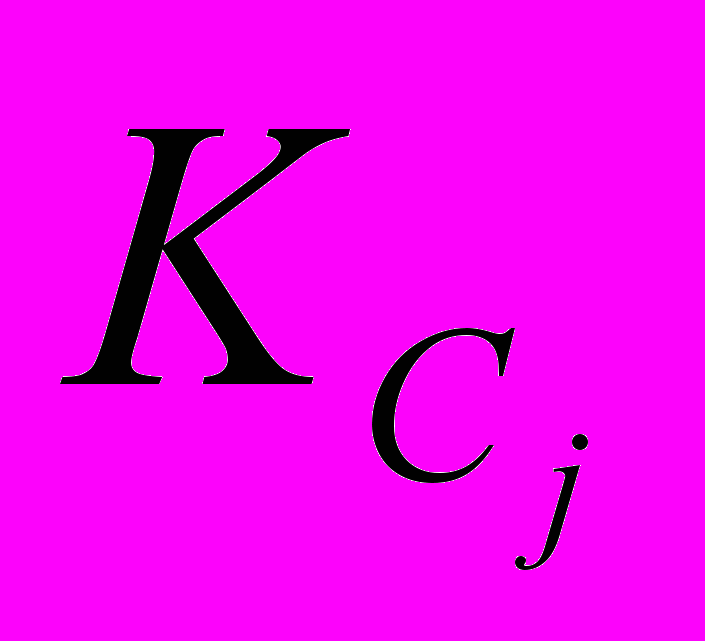
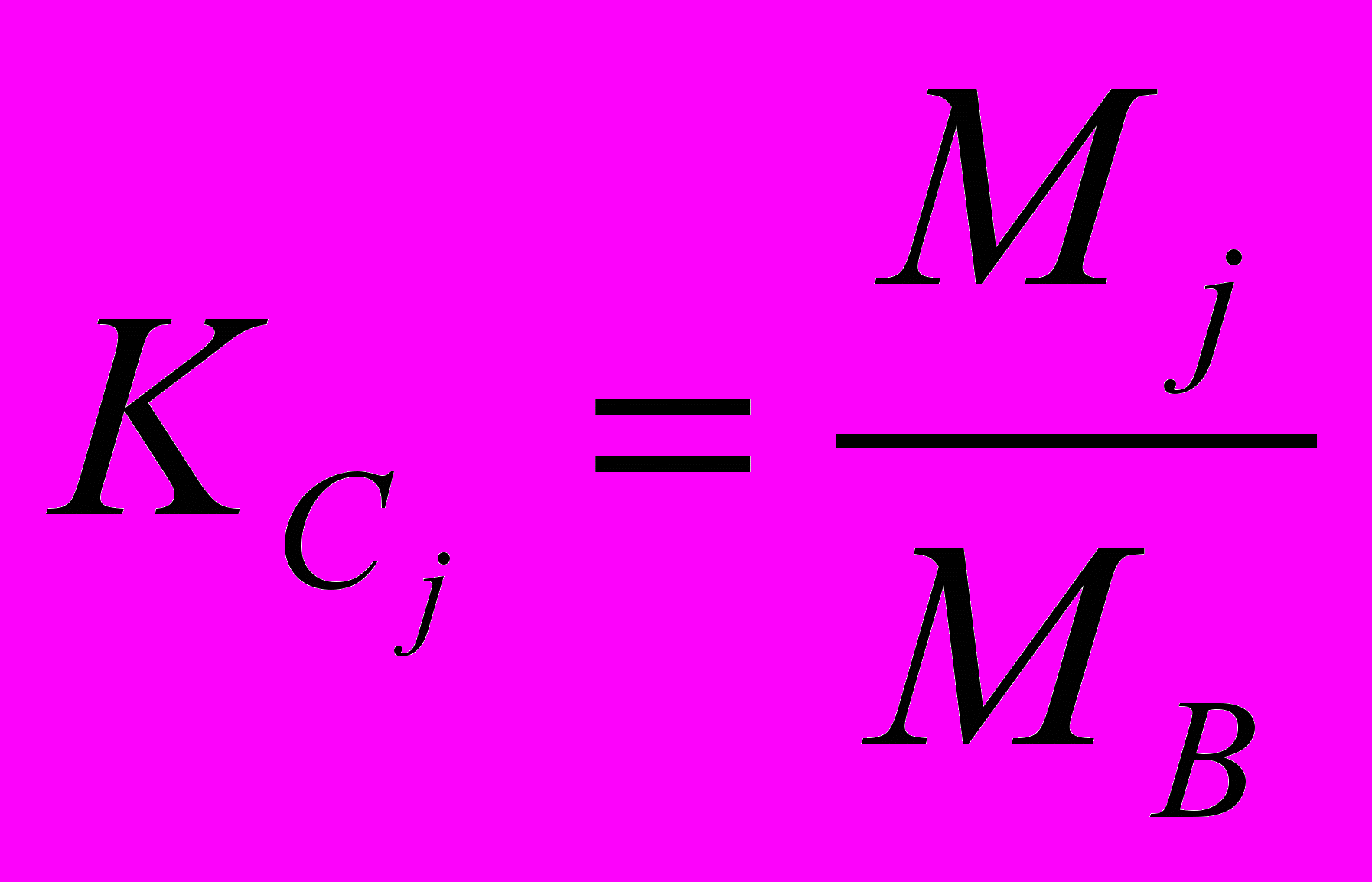
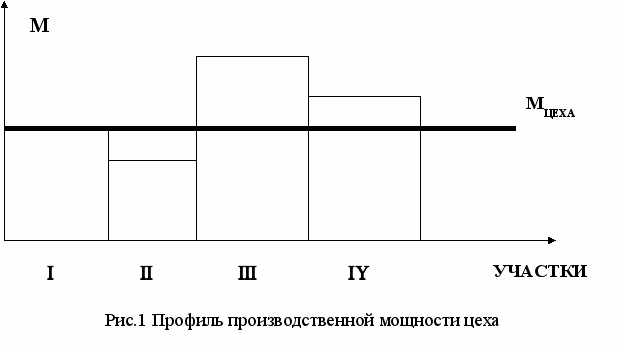
Если
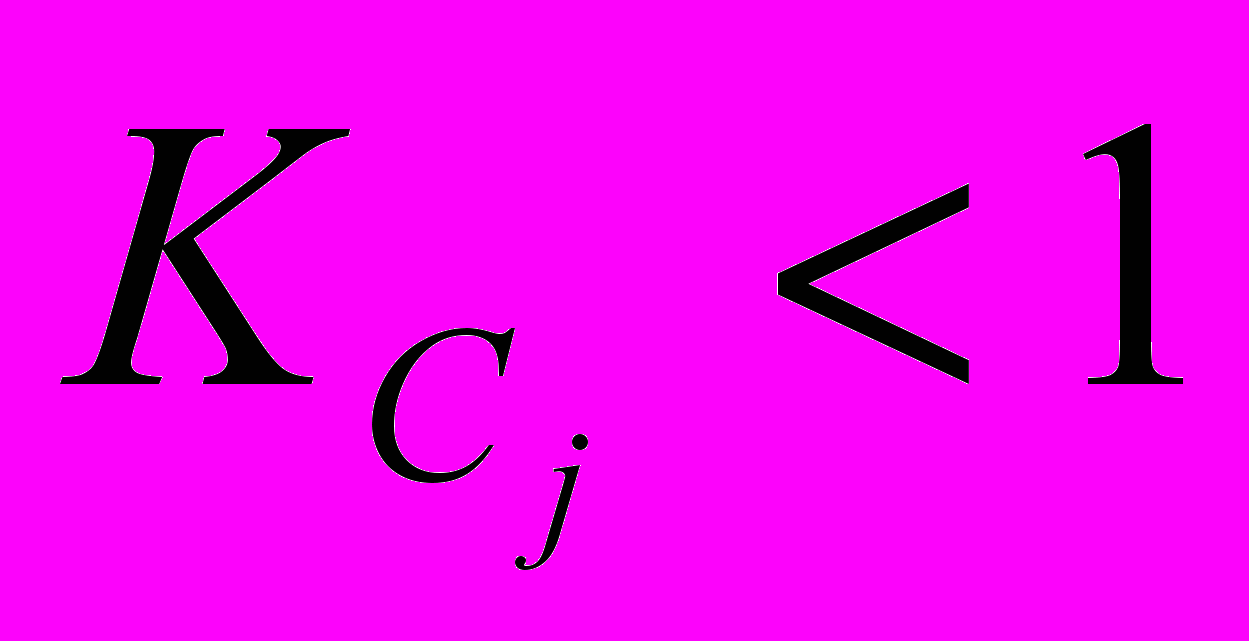
Если
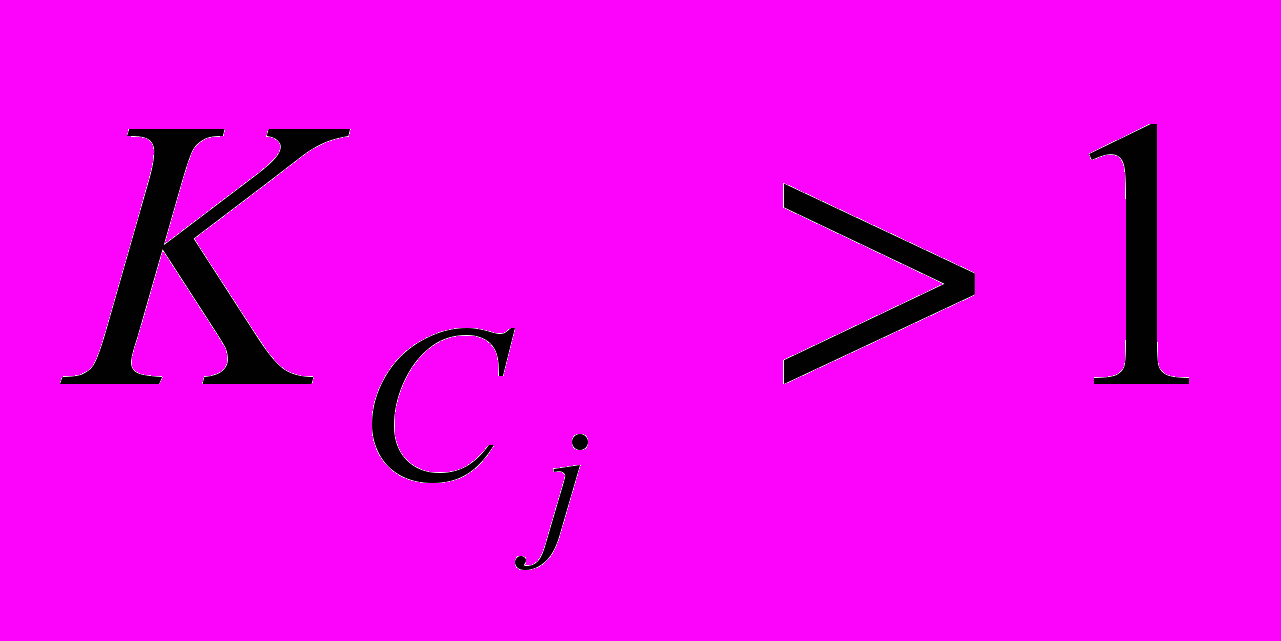
Важнейшим показателем оценки уровня организации производства является коэффициент использования производственной мощности цеха (КИМ), определяемый по формуле:
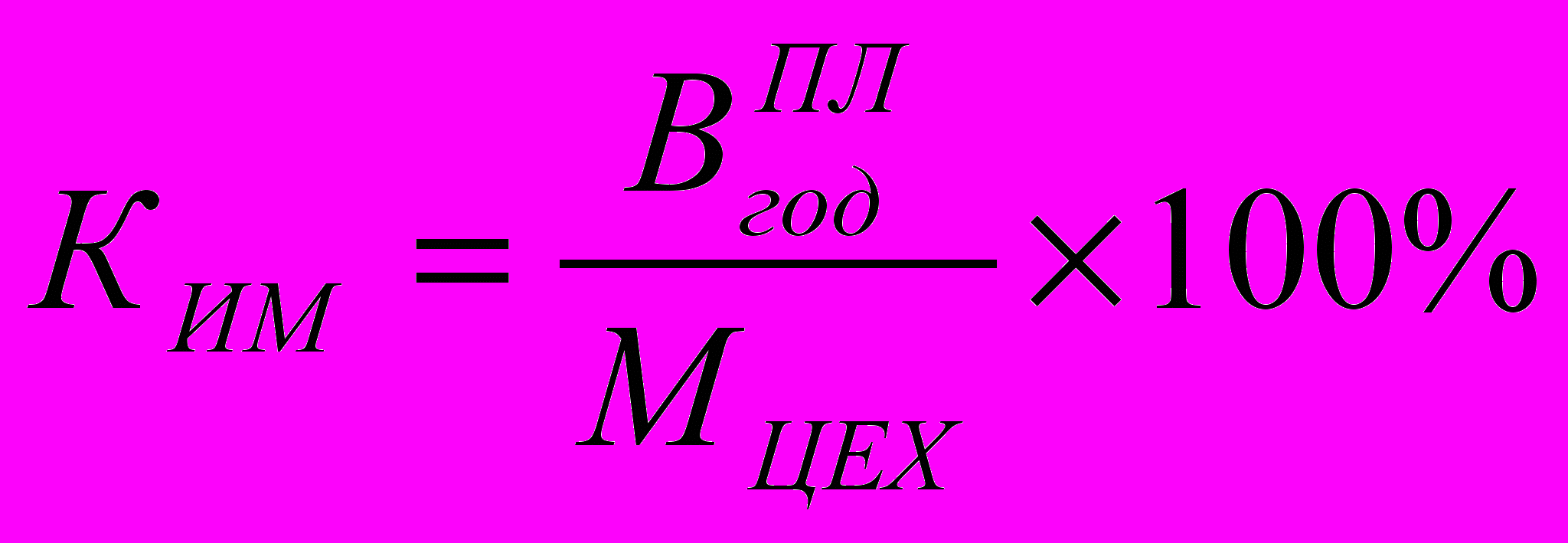
где:
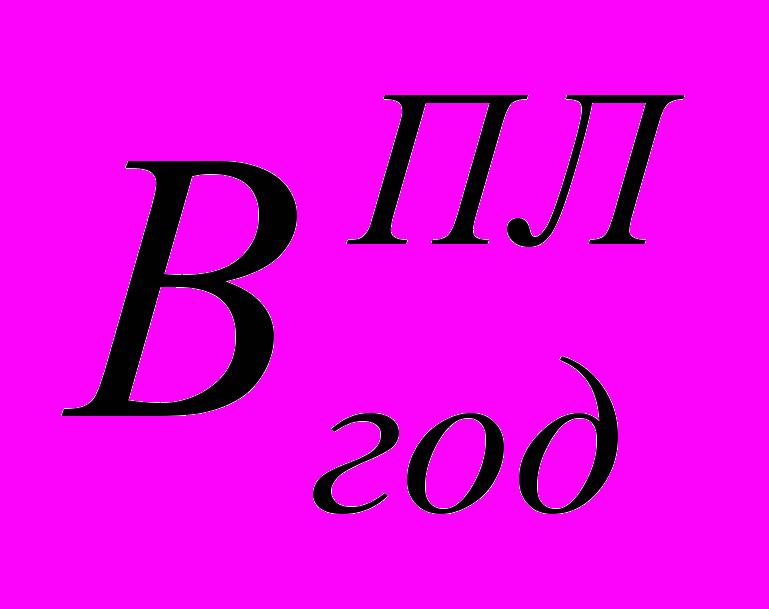
Мцех – среднегодовая производственная мощность цеха в течение межремонтного цикла.
2.7 Разработка организационно-технических мероприятий по выравниванию профиля производственной мощности цеха
Мощность цеха устанавливается по мощности ведущего участка и сопоставляется с мощностями отдельных участков.
На основе проведенного анализа производственного профиля разрабатываются организационно-технические мероприятия, направленные на устранение (сокращение) “узких мест” и рациональное использование производственных резервов за счет:
- сокращения производственного цикла;
- изменения структуры ремонтного цикла;
- увеличения производительности оборудования;
- изменения количества принимаемого к установке оборудования или его замены аналогичным, но имеющим иные технико-экономические характеристики, позволяющие наиболее рационально решить поставленные задачи.
Если устранение “узких мест” предусматривается за счет сокращения времени на планово-предупредительный ремонт, или увеличения ремонтного пробега оборудования, то следует выполнить новые расчеты по обоснованию количества ремонтов и времени простоев оборудования в ремонте, с определением в конечном итоге среднегодового эффективного фонда времени в течение межремонтного цикла. Здесь же следует построить новый график ППР для рассматриваемого оборудования.
Если мероприятия направлены на увеличение часовой производительности единицы оборудования, то следует исходить из ограничений, обусловленных особенностями и условиями проведения каждого технологического процесса, применяемого оборудования, в конечном итоге приводящим к повышению их КПД (как правило, в пределах не более 15-20%).
Также требуют обоснования мероприятия, связанные с изменением количества однотипного оборудования. При этом, не следует избегать возможности установки нескольких однотипных единиц оборудования, отличающихся друг от друга технико-экономическими параметрами, в первую очередь, производительностью.
Составляется новый профиль производственной мощности цеха, учитывающий предлагаемые мероприятия на всех участках (стадиях) производства. Вновь определяется коэффициент сопряженности производственных мощностей каждого участка и проводится анализ полученных изменений.
В конечном итоге рассчитывается окончательный (итоговый) показатель использования производственной мощности цеха (
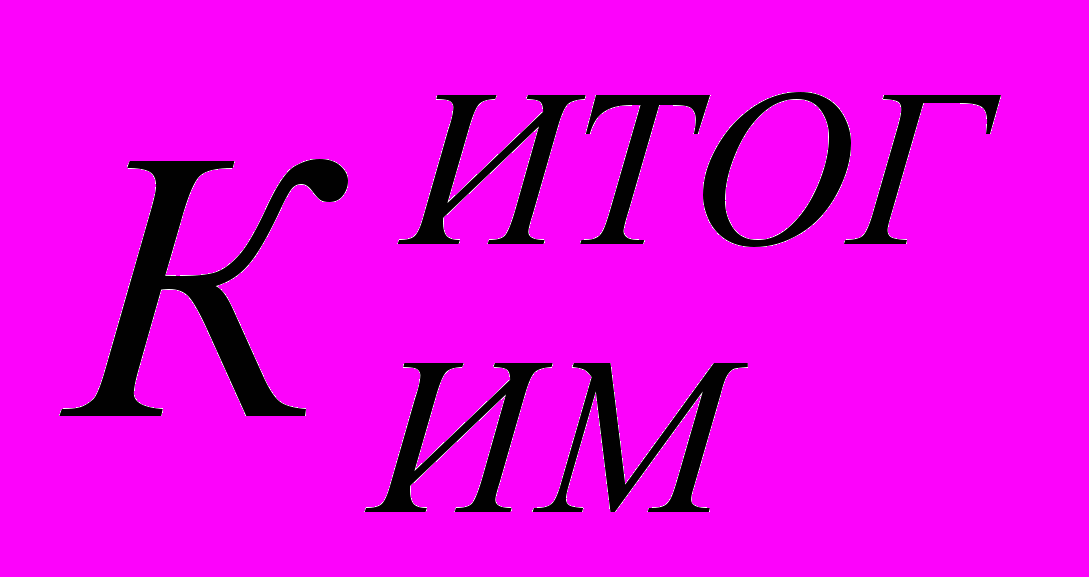
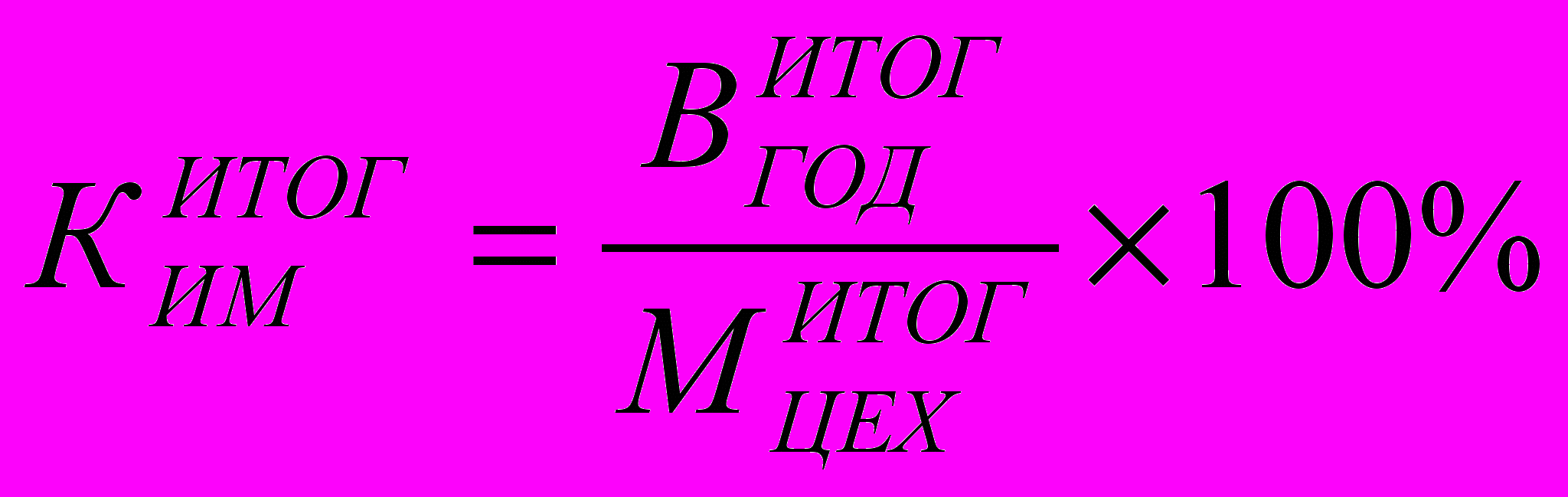
Таким образом, в результате предлагаемых мероприятий могут быть изменены значения не только производственной мощности цеха, но и производственной программы. Производственная программа может быть изменена в случае, если в результате предлагаемых организационно-технических мероприятий коэффициент использования мощности остается на недопустимо низком уровне – менее 70% (принимаем, что рассматриваемая продукция имеет на данном товарном рынке спрос).
В заключении необходимо дать оценку изменений рассчитываемых показателей, происшедших в результате проведения предлагаемых мероприятий:
- абсолютный прирост (уменьшение) производственной мощности цеха (М):

- относительное изменение производственной мощности цеха (М%):
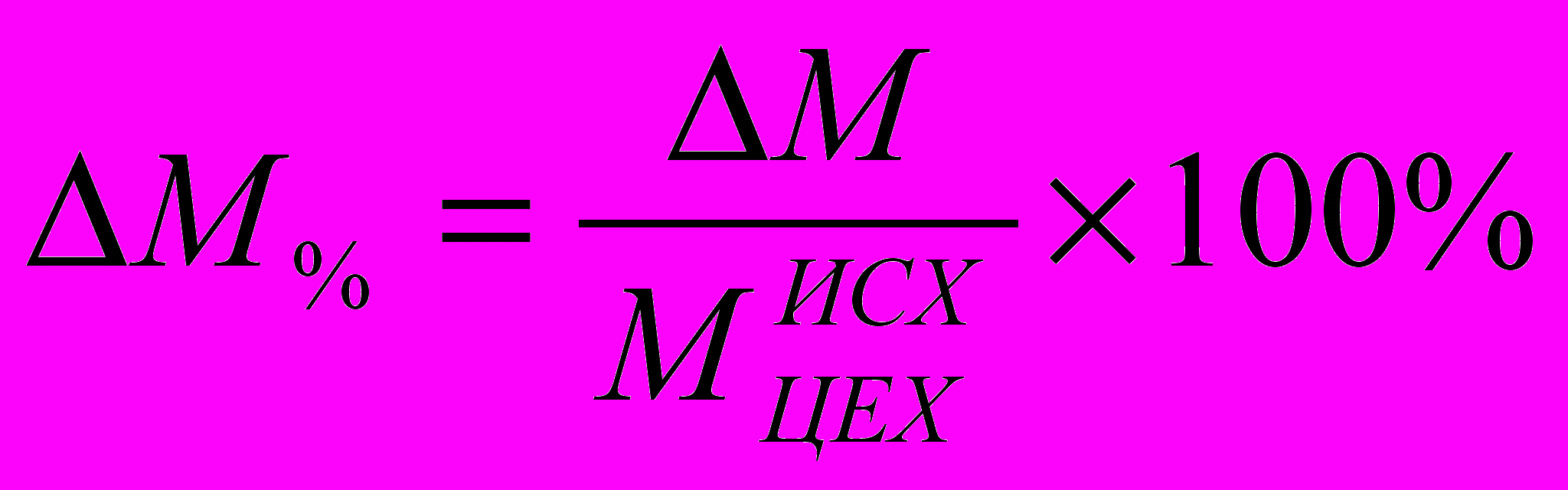
- индекс изменения производственной мощности (IM):
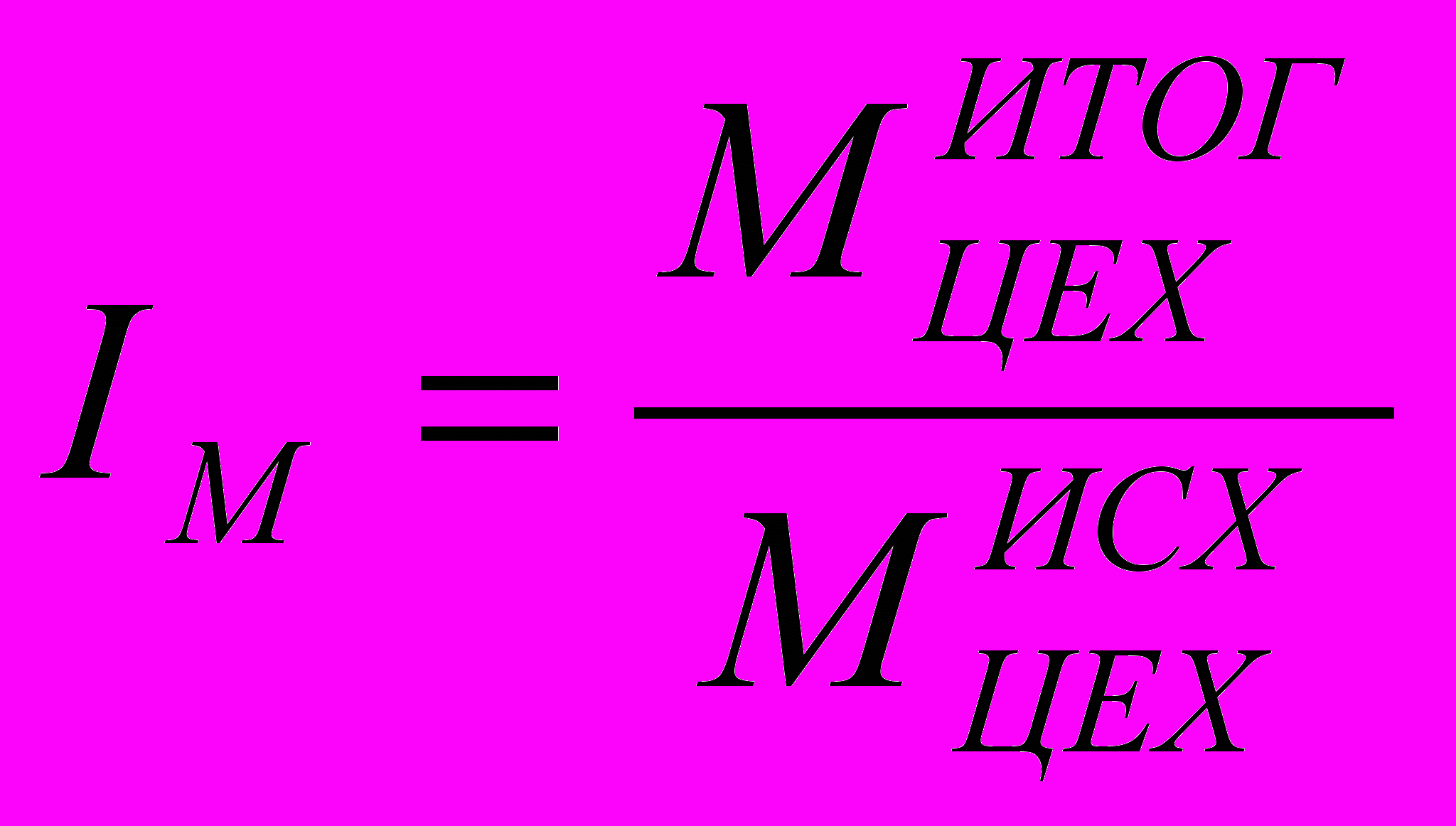
- абсолютное изменение коэффициента использования производственной мощности цеха (КИМ):

- относительное изменение коэффициента использования производственной мощности цеха (
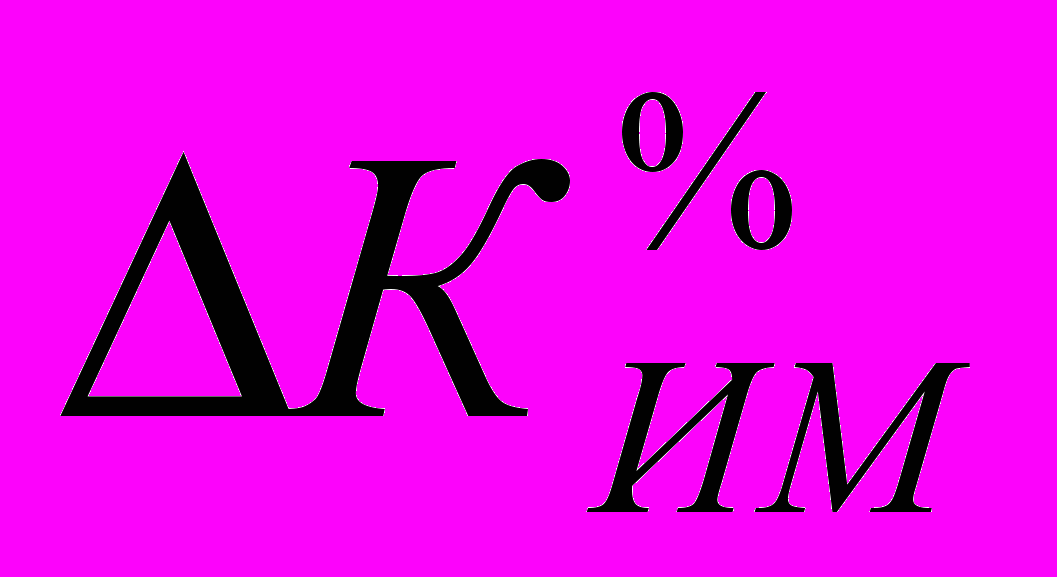
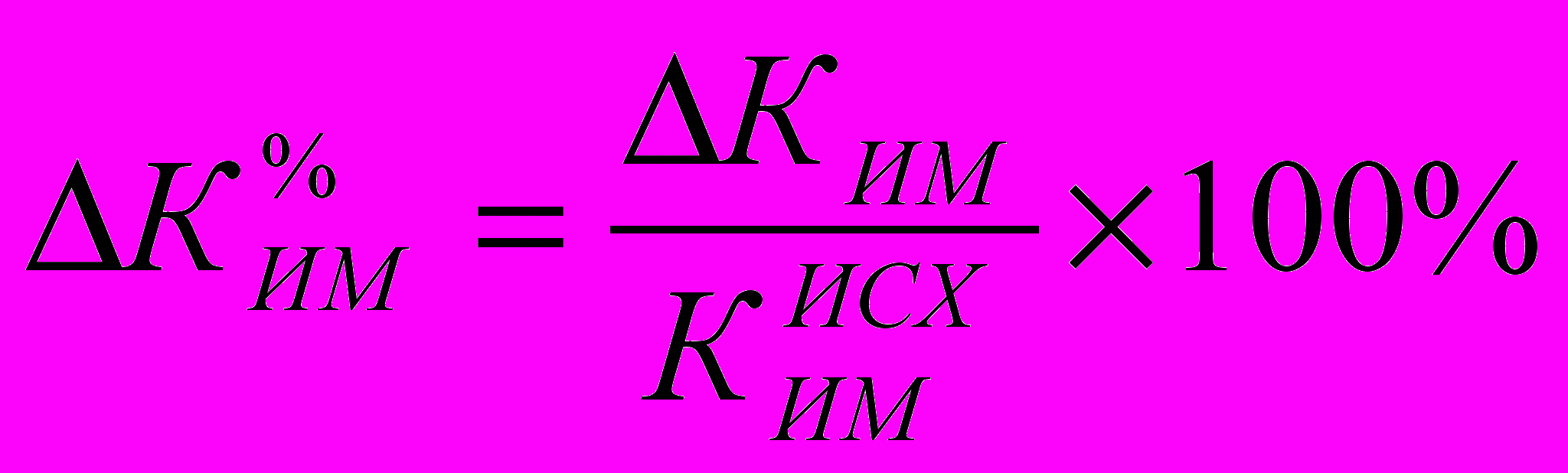
- индекс изменения коэффициента использования производственной мощности цеха (
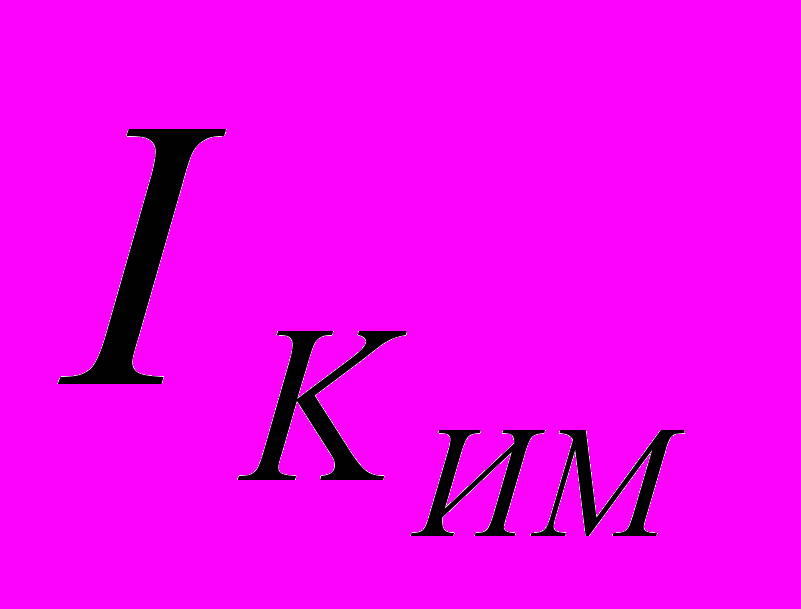
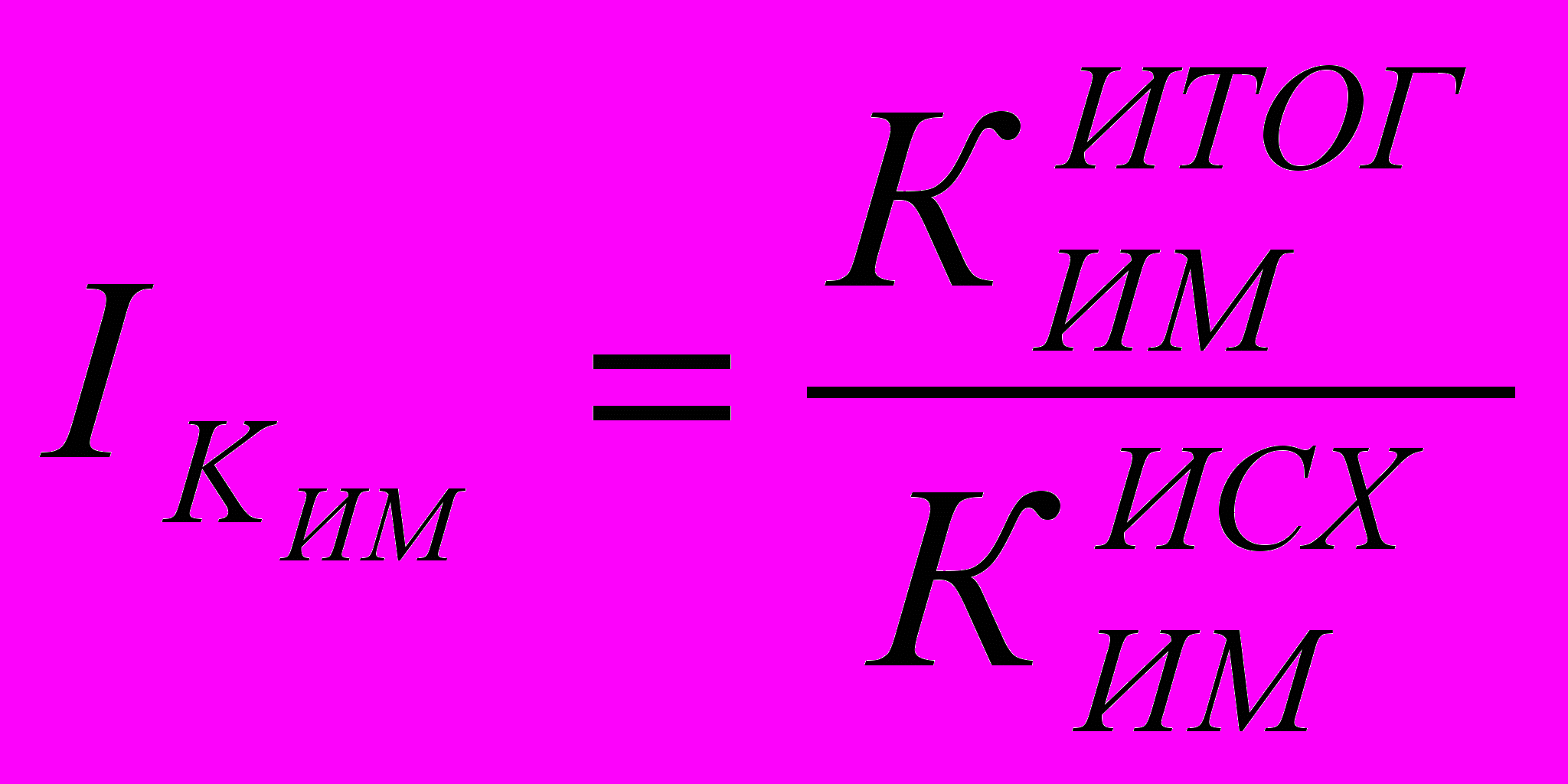
Рекомендуется проведение факторного анализа изменения производственной мощности в результате проведения разрабатываемых мероприятий, как за счет влияния экстенсивных, так и интенсивных факторов.
2.8. Производственная структура цеха и организационная структура управления цехом
Проектирование производственной структуры цеха включает определение состава, количества производственных участков (стадий) и обслуживающих (инфраструктурных) звеньев и их взаимосвязи.
При проектировании производственной структуры цеха следует учитывать особенности каждого технологического процесса (стадии) и характер производимой продукции, формы кооперации и специализации, методы организации производства (поточный или непоточный, серийный, массовый) и другие факторы.
В работе следует предложить производственную структуру цеха, выделив участки основного и инфраструктурного характера и формы их взаимосвязи, руководствуясь типовыми схемами, используемыми на предприятиях химической отрасли.
Руководствуясь типовыми рекомендациями разработать организационную структуру управления цехом по производству рассматриваемой продукции.
2.9 Организация работы участка фасовки и комплектации готовой продукции (ГП)
Настоящий раздел проекта выполняется на основе данных, сбор которых осуществляется на основе специального задания, согласованного с руководителем проекта, если проект выполняется на основе самостоятельно собираемой информации на предприятиях химической промышленности.
Если же проект выполняется на основе организации производства серной кислоты, то для выполнения данного раздела следует руководствоваться индивидуальным заданием, представленным в таблице 4.
Предлагается рассчитать основные параметры организации участка фасовки и комплектации реактивной серной кислоты, располагая следующими исходными данными:
- объём исходного резервуара (сборника) серной кислоты (Qл);
- размер заказываемой партии готовой продукции (Зл);
- продолжительность технологических операций, выполняемых при фасовке и комплектации партии отгружаемой продукции (ti);
- емкости тары (бутыли) для готовой продукции (
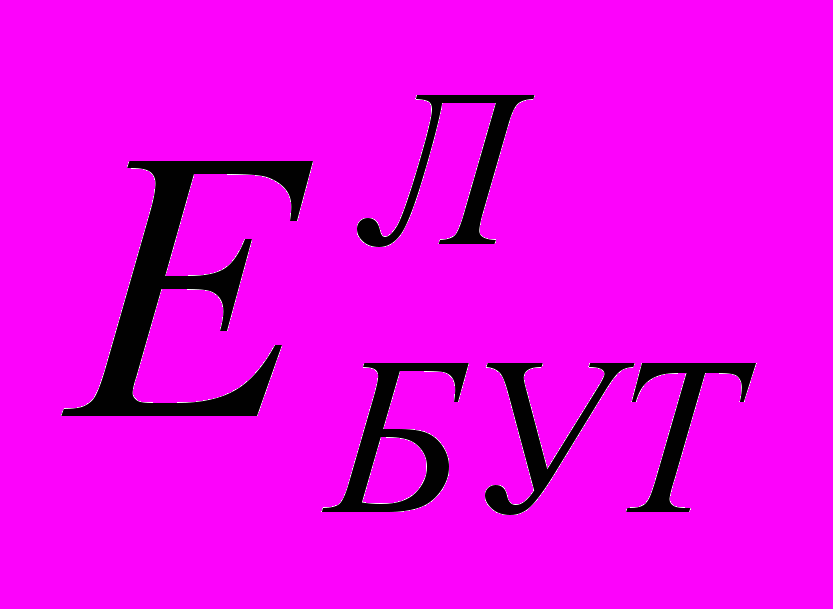
- вместимости транспортного контейнера (
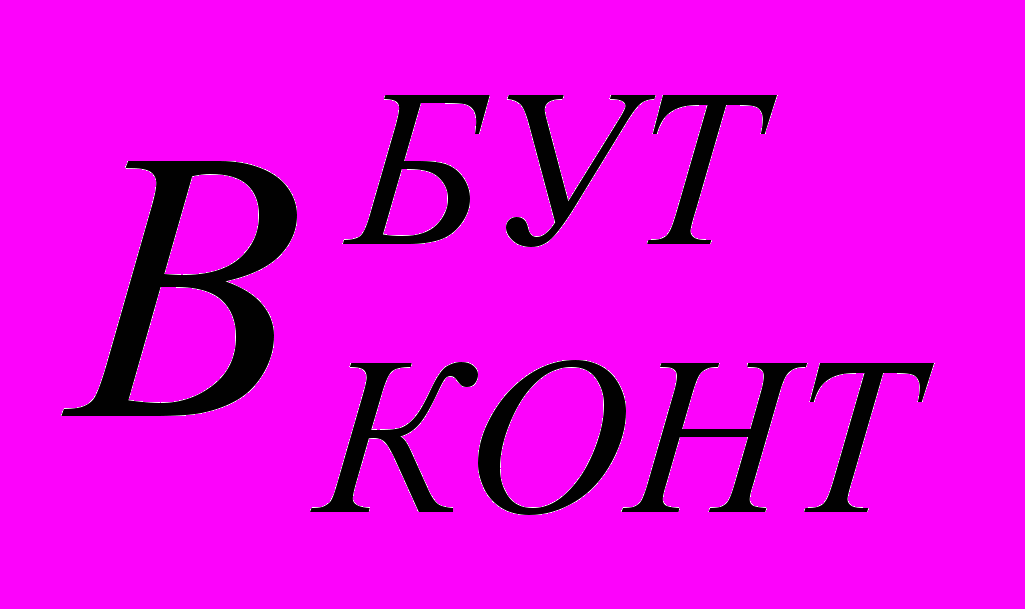
- грузоподъёмность транспортных средств.
Расчеты рекомендуется проводить в следующей последовательности:
- определяется размер заказываемой партии в следующих единицах измерения:
- в количестве бутылей заданной емкости (Збут):
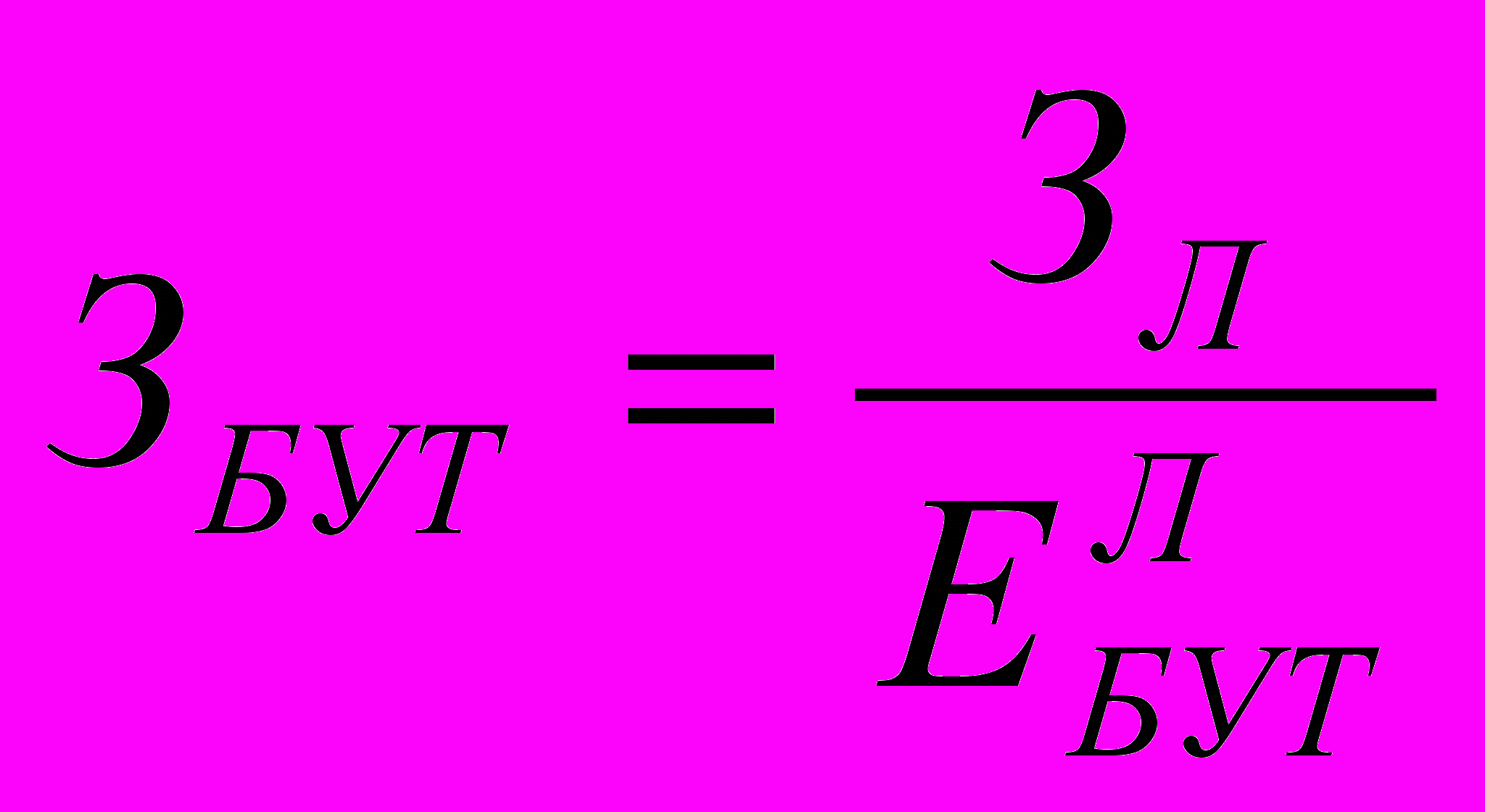
- в количестве контейнеров заданной вместимости (Зконт):
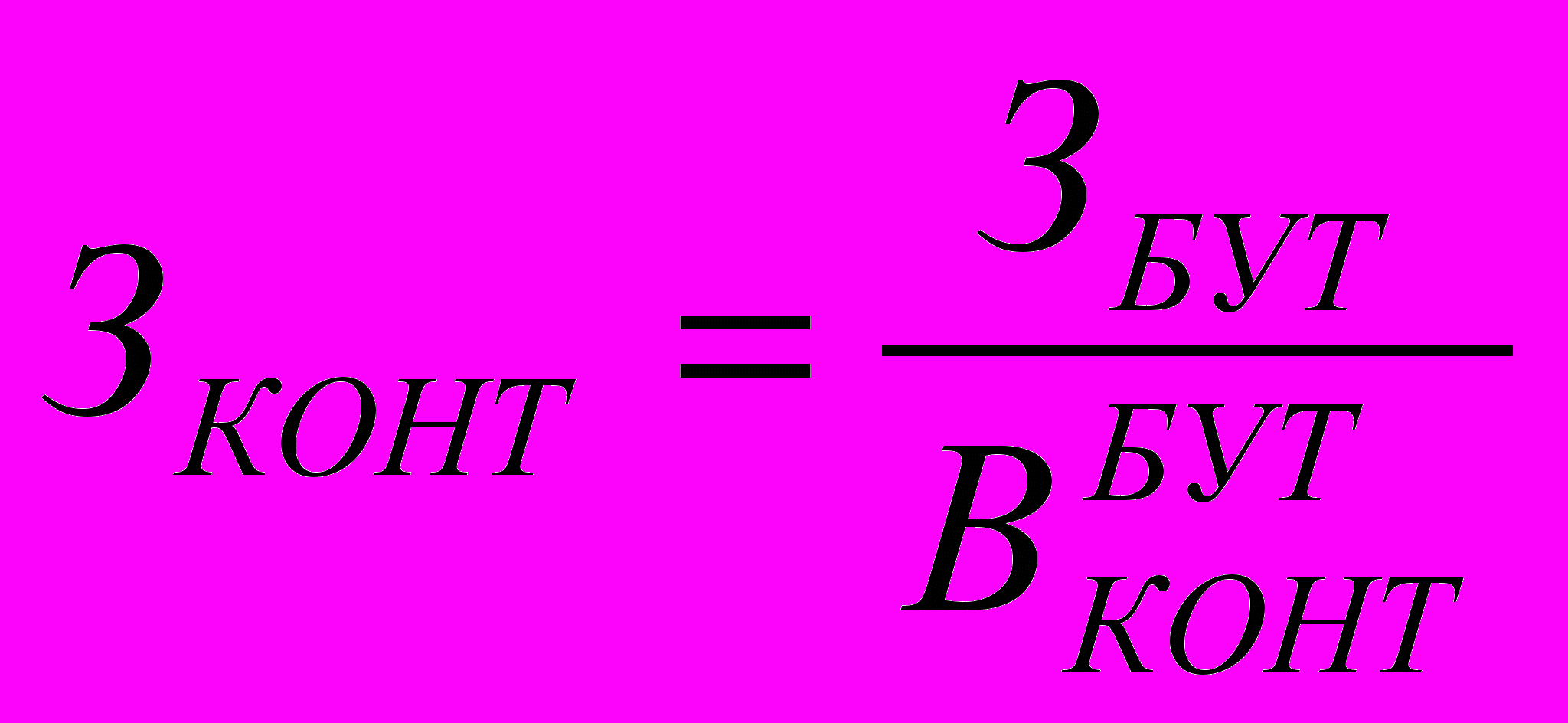
- определяется количество загрузок исходного сборника (резервуара) готовой продукции для выполнения заказа соответствующего объёма готовой продукции:
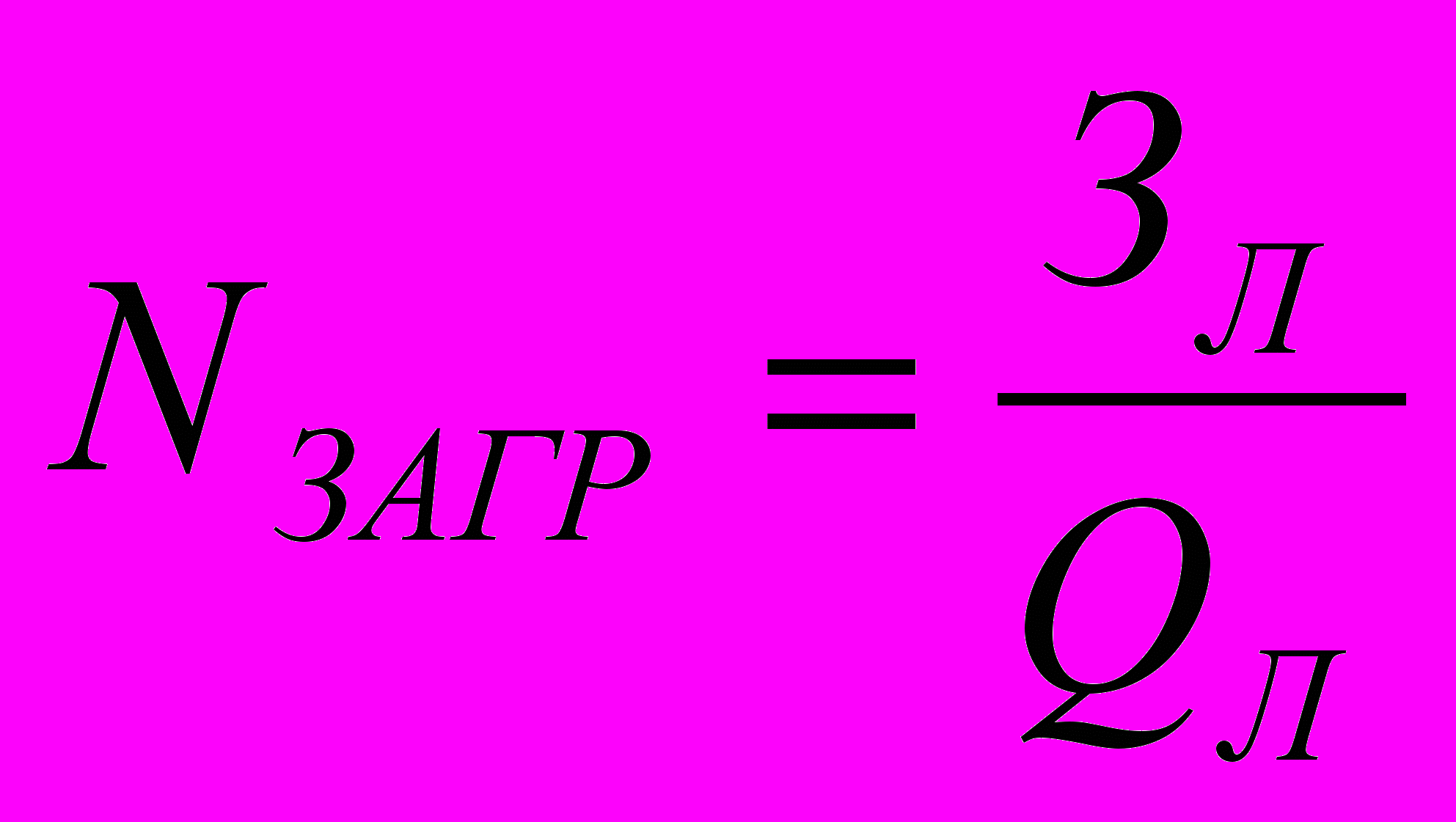
- на основе данных о структуре производственного цикла и продолжительности его составляющих технологических операций (табл.4) рассчитывается продолжительность производственного цикла в расчете на размер заказываемой партии, измеренной количеством контейнеров (Зконт). Расчеты производятся для различных вариантов его организации: при последовательном, параллельном и смешанном выполнении технологических операций на основе аналитических формул:
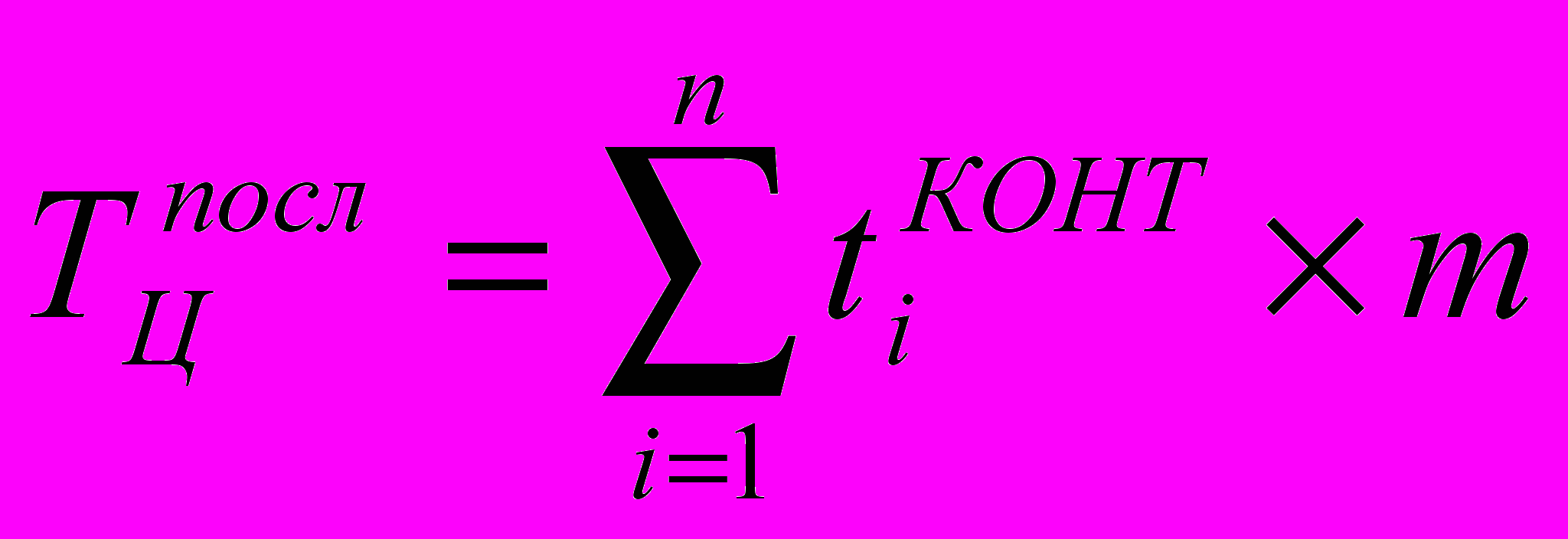

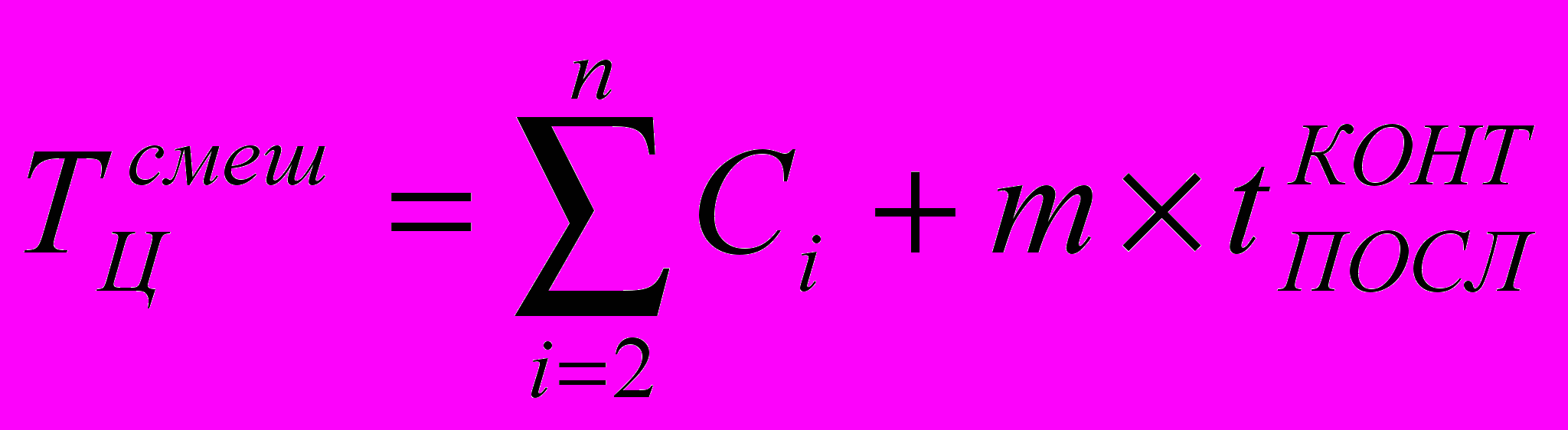
где:
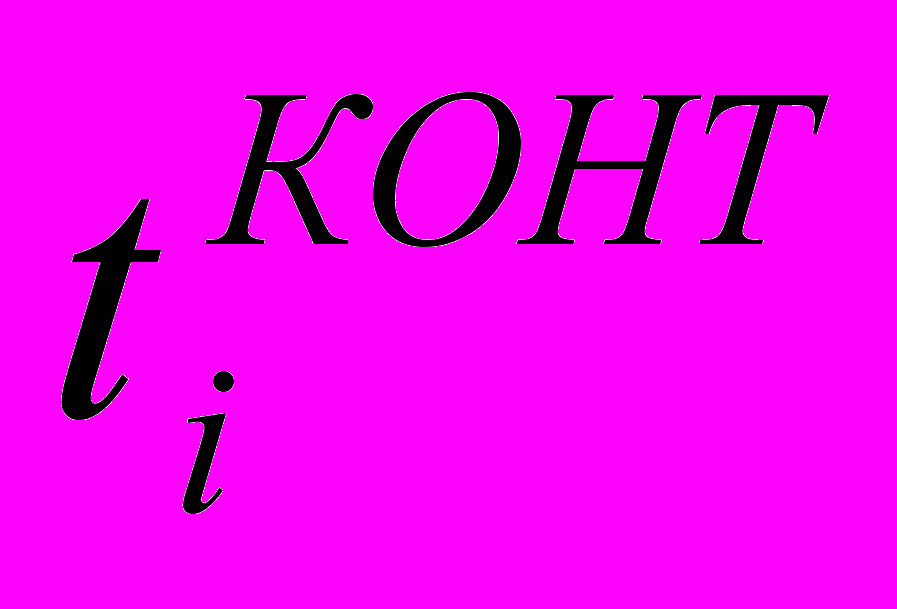

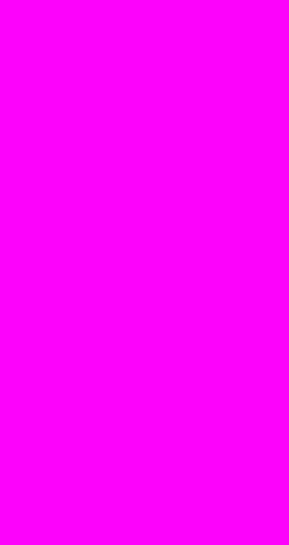
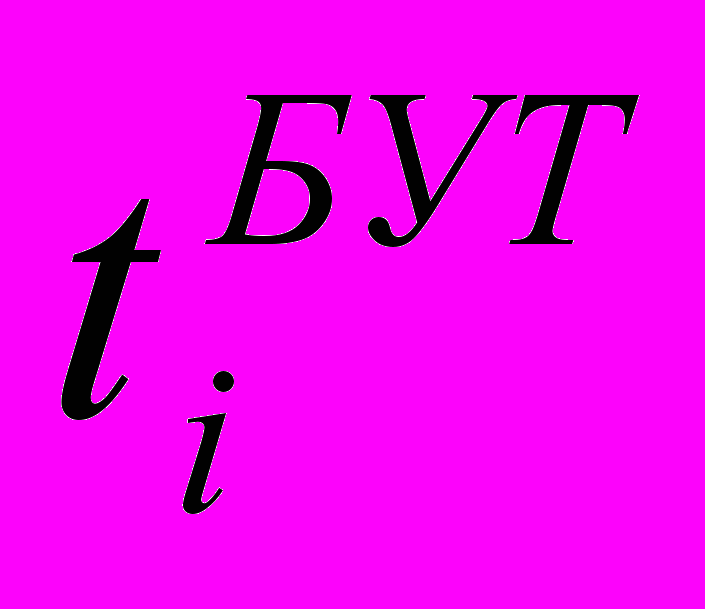
n – количество технологических стадий (операций) на всем производственном конвейере;
Таблица 4
Исходные данные для проектирования участка фасовки и комплектации готовой продукции
(индивидуальные задания по вариантам)
№ п/п | Наименование показателей | Единица измер. | В А Р И А Н Т Ы | |||||||||
1 | 2 | 3 | 4 | 5 | 6 | 7 | 8 | 9 | 10 | |||
1 | Объём заказываемой партии | тыс. литр. | 1,2 | 1,5 | 1,6 | 1,8 | 2,0 | 1,4 | 1,75 | 1,3 | 2,25 | 1,25 |
2 | Емкость тары (бутыли) | литр | 10 | 12 | 15 | 20 | 10 | 12 | 15 | 20 | 15 | 10 |
3 | Вместимость контейнера | бут. | 12 | 12 | 10 | 6 | 15 | 10 | 8 | 8 | 12 | 20 |
4 | Грузоподъёмность транспорта | конт. | 1 | 1 | 1 | 1 | 1 | 1 | 1 | 1 | 1 | 1 |
5 | Ёмкость исходного сборника | литр | 500 | 400 | 450 | 300 | 350 | 600 | 500 | 300 | 400 | 250 |
6 | Продолжительность выполнения технологических операций: | | | | | | | | | | | |
6.1 | Розлив в тару | мин/литр | 0,5 | 0,6 | 0,4 | 0,5 | 0,6 | 0,4 | 0,5 | 0,6 | 0,4 | 0,5 |
6.2 | Закупорка и маркировка тары | мин/бут | 0,5 | 0,5 | 0,5 | 0,5 | 0,5 | 0,5 | 0,5 | 0,5 | 0,5 | 0,5 |
6.3 | Укладка в контейнер | сек./бут. | 20 | 25 | 25 | 30 | 20 | 25 | 25 | 30 | 25 | 20 |
6.4 | Погрузка и доставка контейнера на склад | мин/конт. | 10 | 12 | 15 | 8 | 10 | 12 | 10 | 12 | 8 | 10 |
6.5 | Установка контейнера | мин/конт. | 1,0 | 1,5 | 1,2 | 1,0 | 1,5 | 1,2 | 1,0 | 1,5 | 1,2 | 1,25 |
6.6 | Возврат транспорта | мин. | 8 | 9 | 12 | 6 | 8 | 10 | 8 | 9 | 6 | 8 |
m – количество контейнеров, отгружаемых в рамках заказанной партии (Зконт);
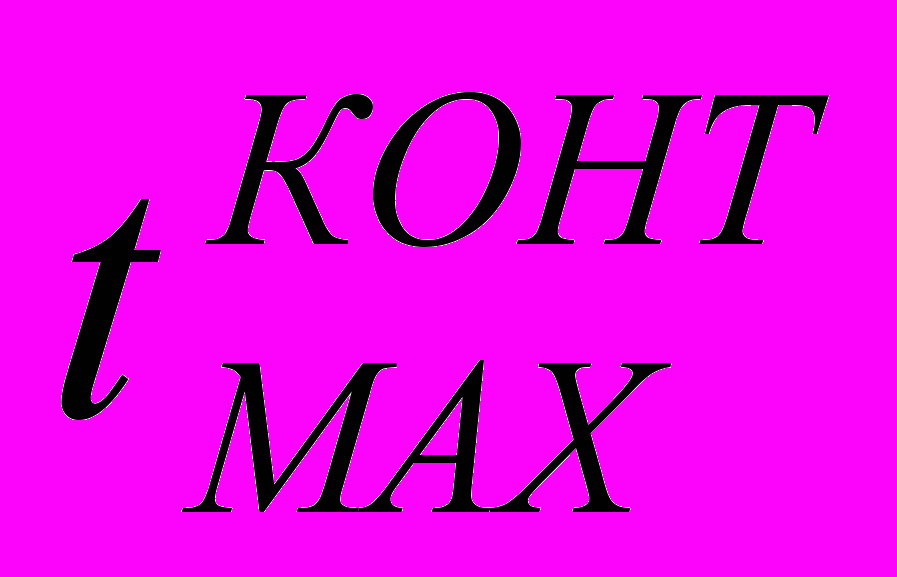
Сi – величина смещения начала следующей i-й стадии (операции) по отношению к предыдущей (i-1-й операции);
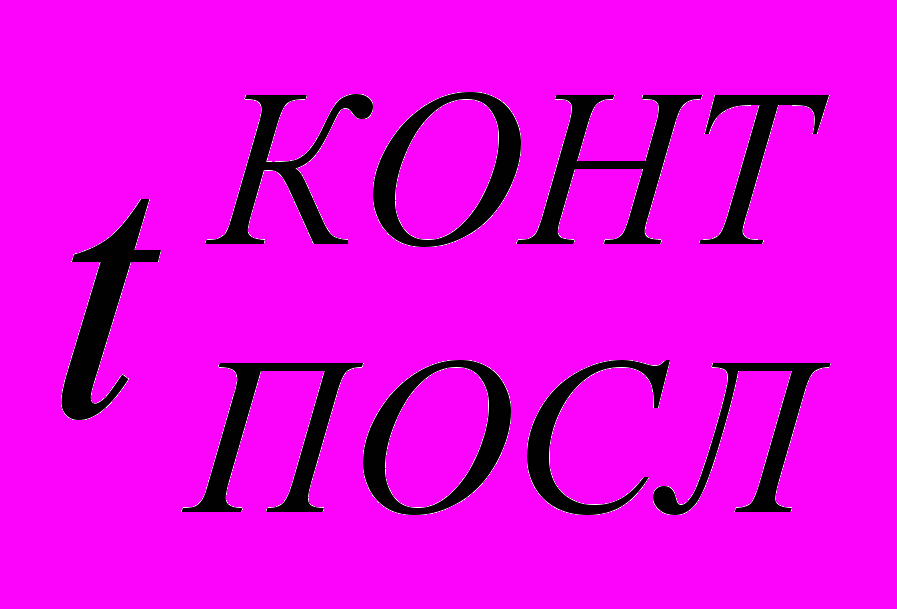
- определяется (выбирается) наиболее приемлемый (оптимальный) вариант организации процесса фасовки и комплектования партии отгружаемой продукции, принимая во внимание, в первую очередь, продолжительность цикла, и для которого графически изображается структура производственного цикла и последовательность выполнения технологических операций (стадий) в расчете на заданный размер партии (Зконт).
- для выбранного варианта организации работы участка фасовки и комплектования ГП рассчитываются параметры его работы в условиях конвейера:
- ритм потока (r) в расчете на выход с конвейера на склад одного контейнера:
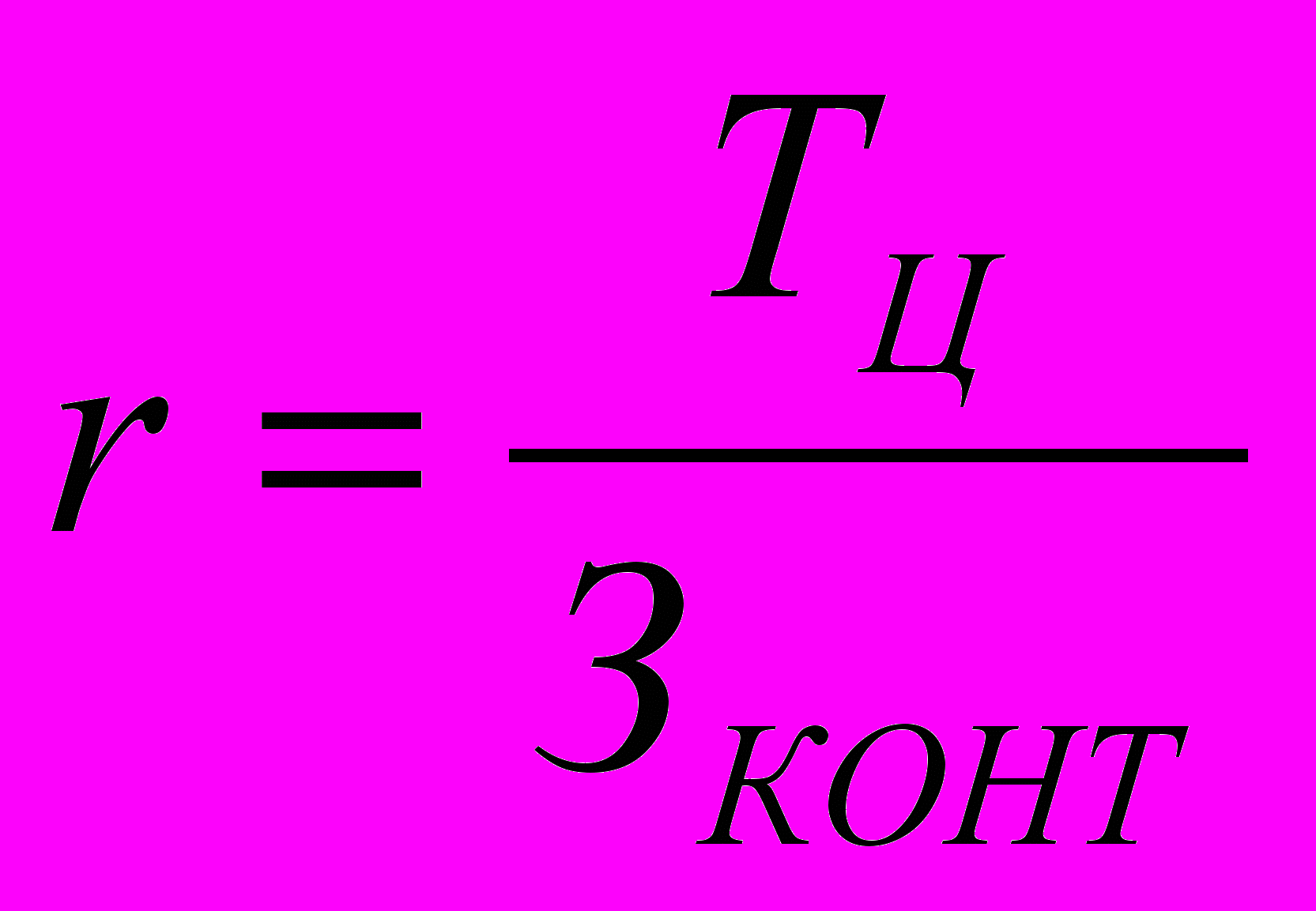
- продолжительность i-ой технологической стадии на обработку изделий (бутылей), входящих в один контейнер (
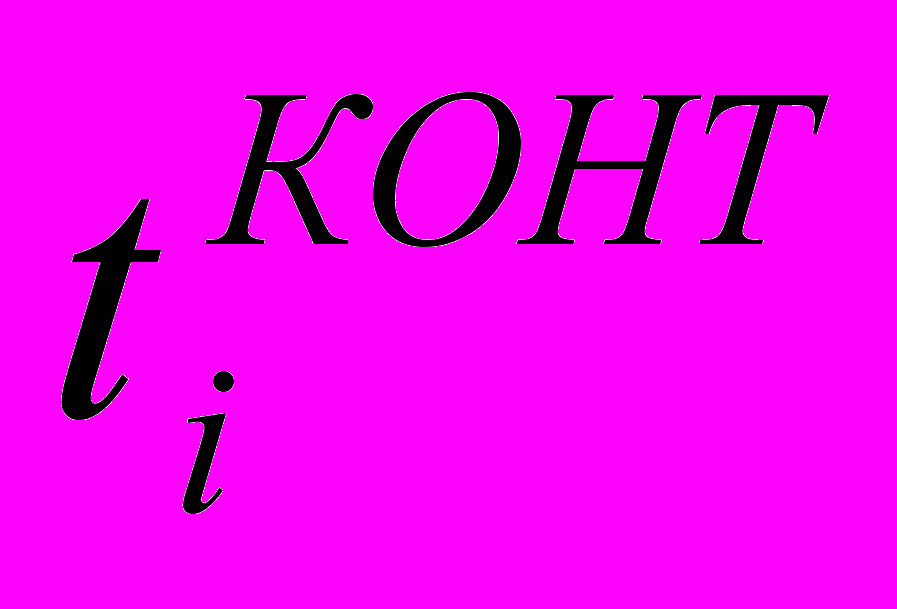
- число рабочих мест на каждой i-ой технологической стадии (mi) для синхронизации работы конвейера:
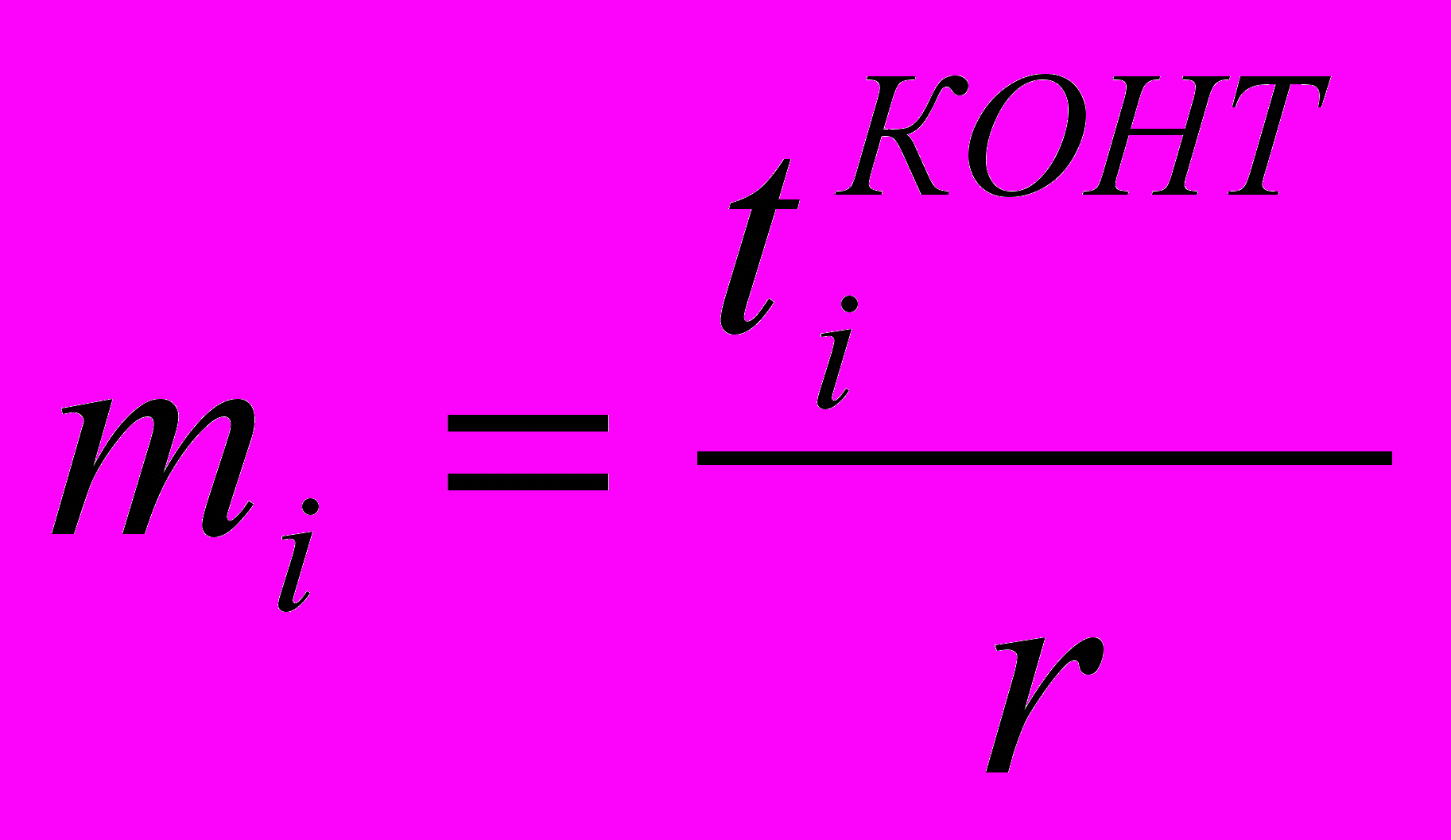
- общее число рабочих мест на конвейере (mобщ):
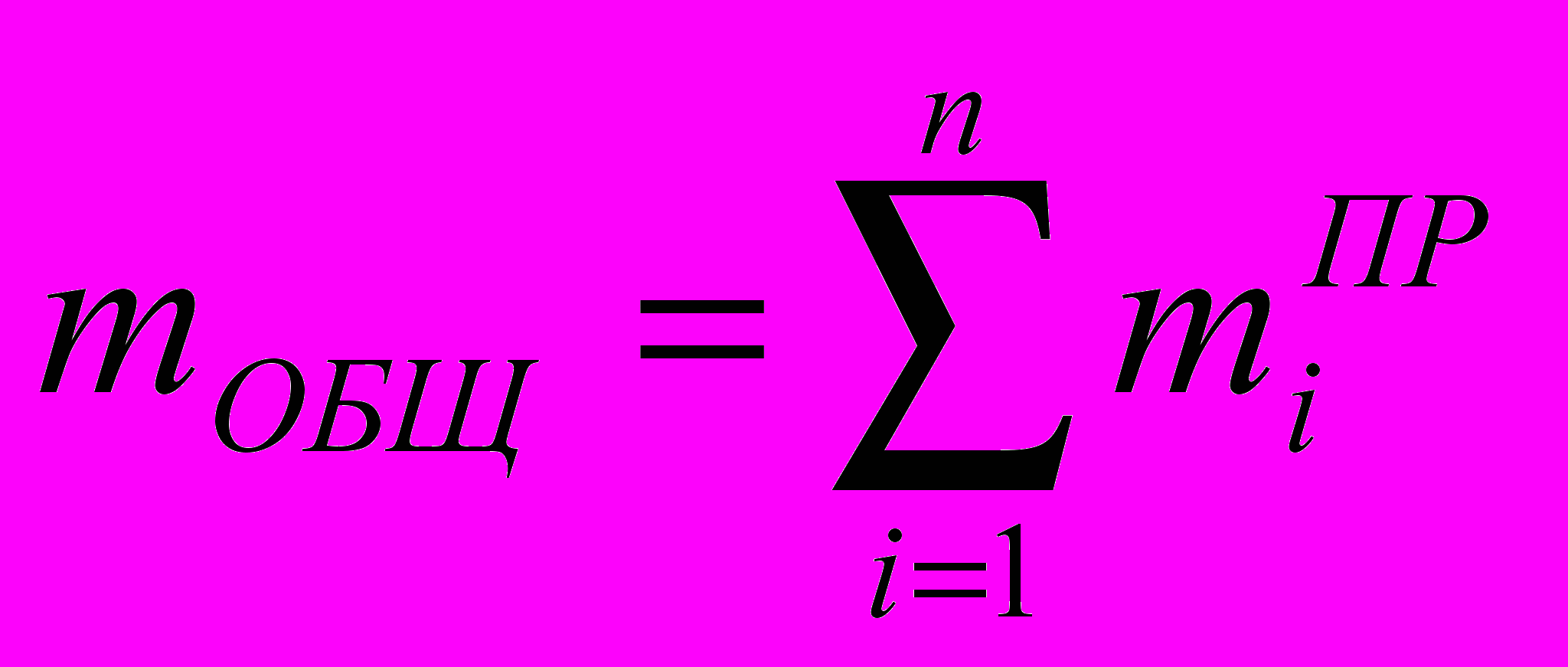
где:
ti – время на выполнение операции с одной единицей продукции (бутылью) на i-ой стадии процесса;
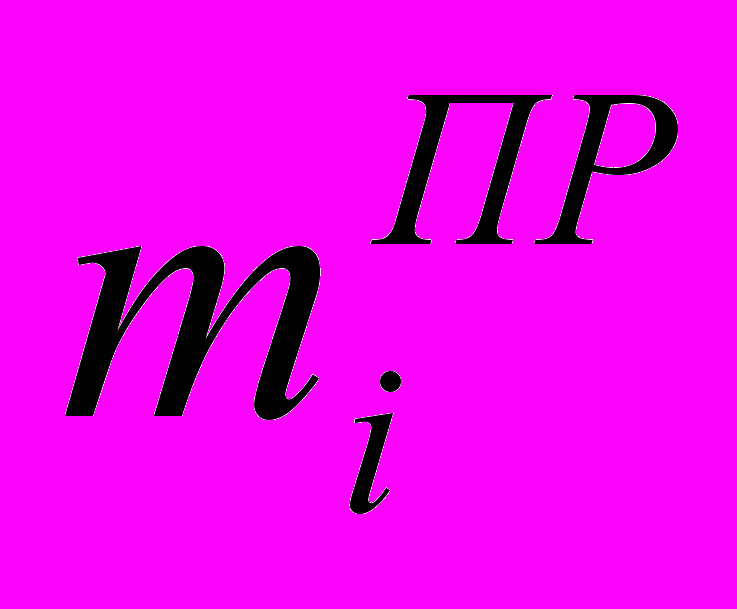
- определяется коэффициент загрузки рабочих мест на каждой i-ой стадии процесса:

- результаты расчетов основных параметров работы участка фасовки и комплектации ГП, представить в виде сводной таблицы, пример которой представлен в табл. 5.
Таблица 5
Основные параметры работы участка фасовки и комплектования ГП в расчете на заданный объём заказа
№ п/п | Наименование показателя | Ед. измер. | Значение показателя |
1 | Объём заказываемой партии | литр | |
| | бут. | |
| | конт. | |
2 | Емкость бутыли | литр | |
3 | Вместимость контейнера | бут. | |
| | литр | |
4 | Количество загрузок сборника ГП | раз | |
5 | Продолжительность производственного цикла на выполнение заказа при его организации: | | |
| - последовательно | мин | |
| - параллельно | мин | |
| - смешанным образом | мин | |
6 | Ритм потока | мин/конт | |
7 | Общее число рабочих мест | чел. | |
8 | Коэффициент загрузки рабочих мест по i-м стадиям | % | |