Лекция 11 Тема: Состав и количество основного оборудования в поточном производстве
Вид материала | Лекция |
СодержаниеАгрегатный станок Автоматическая линия 80% сборочного цикла приходится на переходы, связанные с подачей, ориентацией и совмещением деталей, и лишь 20 |
- Лекция 12 Тема: Состав и количество основного оборудования в непоточном производстве, 602.73kb.
- План лекций для студентов педиатрического факультета на весенний семестр 2011-2012, 50.89kb.
- Воробьева Ольга Владимировна Атмосфера и атмосферные явления. Тема урок, 55.05kb.
- Лекция Тема: система междуранодных отношений, 117.17kb.
- Программа по дисциплине сд. 3 " Технологическое оборудование в производстве, обработке, 220.17kb.
- Аннотация диплом, 1006.46kb.
- Лекция «Математика в жизни, производстве, науке, в твоей будущей профессии», 51.21kb.
- 1 11 Тема 2 12 тема 3 13 Тема 4 14 Тема 5 15 Тема 6 17 Тема 7 20 Тема 8 22 Тема, 284.17kb.
- Учебное пособие Москва 2007 Содержание Лекция № Актуальность борьбы с шумом на производстве,, 1016.54kb.
- План помещения Служебный состав завода Gibson Расположение оборудования, 201.2kb.
Лекция 11
Тема: Состав и количество основного оборудования в поточном производстве
Термины и определения:
Промышленный робот — автономное устройство, состоящее из механического манипулятора и перепрограммируемой системы управления, которое применяется для перемещения объектов в пространстве и для выполнения различных производственных процессов.
Установ – часть технологической операции, выполняемая при неизменном закреплении обрабатываемых заготовок или собираемой сборочной единицы.
Агрегатный станок – специальный металлорежущий станок, построенный на базе нормализованных кинематически не связанных между собой узлов (агрегатов). Силовые узлы имеют индивидуальные приводы, а взаимозависимость и последовательность их движения задаётся единой системой управления.
Автоматическая линия – система машин, комплекс основного и вспомогательного оборудования, автоматически выполняющего в определённой технологической последовательности и с заданным ритмом весь процесс изготовления или переработки продукта производства или части его.
Планшайба (нем. Planscheibe) – приспособление, применяемое в токарных, расточных и некоторых др. металлорежущих станках, на котором закрепляется обрабатываемая заготовка или режущий инструмент для сообщения им вращательного движения. Как правило, на планшайбах устанавливаются заготовки сложной формы или большого диаметра при небольшой длине.
Одним из этапов технологического проектирования машиностроительного производства является определение состава и количества основного оборудования, которое должно обеспечивать высокую эффективность производственного процесса. При выборе состава основного оборудования следует ориентироваться на основные организационно-технические направления, причем следует иметь в виду, что за счет выравнивания времени выполнения операций одновременно достигается и сокращение количества основного оборудования.
Для обеспечения высокого общего уровня автоматизации производственных процессов при выборе основного оборудования в поточном производстве следует не только ориентироваться на высокую автоматизацию выполнения операций технологического процесса, но и учитывать возможность стыковки его с вспомогательным оборудованием с целью образования единой производственной системы. Так, например, конструкция станка должна быть такой, чтобы был удобен доступ в рабочую зону автоматических загрузочных устройств, должны быть предусмотрены возможность стыковки в единую систему управления участком, надежная система стружкоудаления и т. д.
Поточное производство характеризуется незначительной номенклатурой выпуска продукции и высокой интенсивностью технологических процессов, которая может быть достигнута только при использовании параллельной и параллельно-последовательной структуры выполнения операции, что следует учесть при выборе типажа оборудования.
Вследствие интенсивного развития техники необходима быстрая смена выпускаемой продукции. Это в свою очередь накладывает отпечаток на выбор основного оборудования для поточного производства, которое должно обеспечить возможность эффективного изготовления более широкой номенклатуры изделий. Этому требованию удовлетворяют агрегатные переналаживаемые станки с ЧПУ, позволяющие при многоинструментальной обработке с помощью многошпиндельных головок осуществлять быстрый переход с обработки деталей одного типоразмера на другой.
В сборочном производстве приблизительно 80% сборочного цикла приходится на переходы, связанные с подачей, ориентацией и совмещением деталей, и лишь 20% — на переходы по соединению деталей.
Повышение технологических возможностей оборудования, работающего по параллельному и параллельно-последовательному принципам, в частности их гибкости, связано с дополнительными материальными затратами, которые могут окупиться только благодаря сокращению расходов на переналадки. Это необходимо учитывать при выборе типа основного оборудования.
Расчет количества основного оборудования для поточного производства производится по точной программе и предусматривает разработку подробного технологического процесса обработки или сборки с техническим нормированием выполнения каждой операции на все изготовляемые изделия, входящие в программу выпуска.
Расчет числа станков, необходимых для каждой операции, выполняют на основании штучно-калькуляционного времени и объема выпуска каждого наименования изделия, проходящего эту операцию, по формуле:
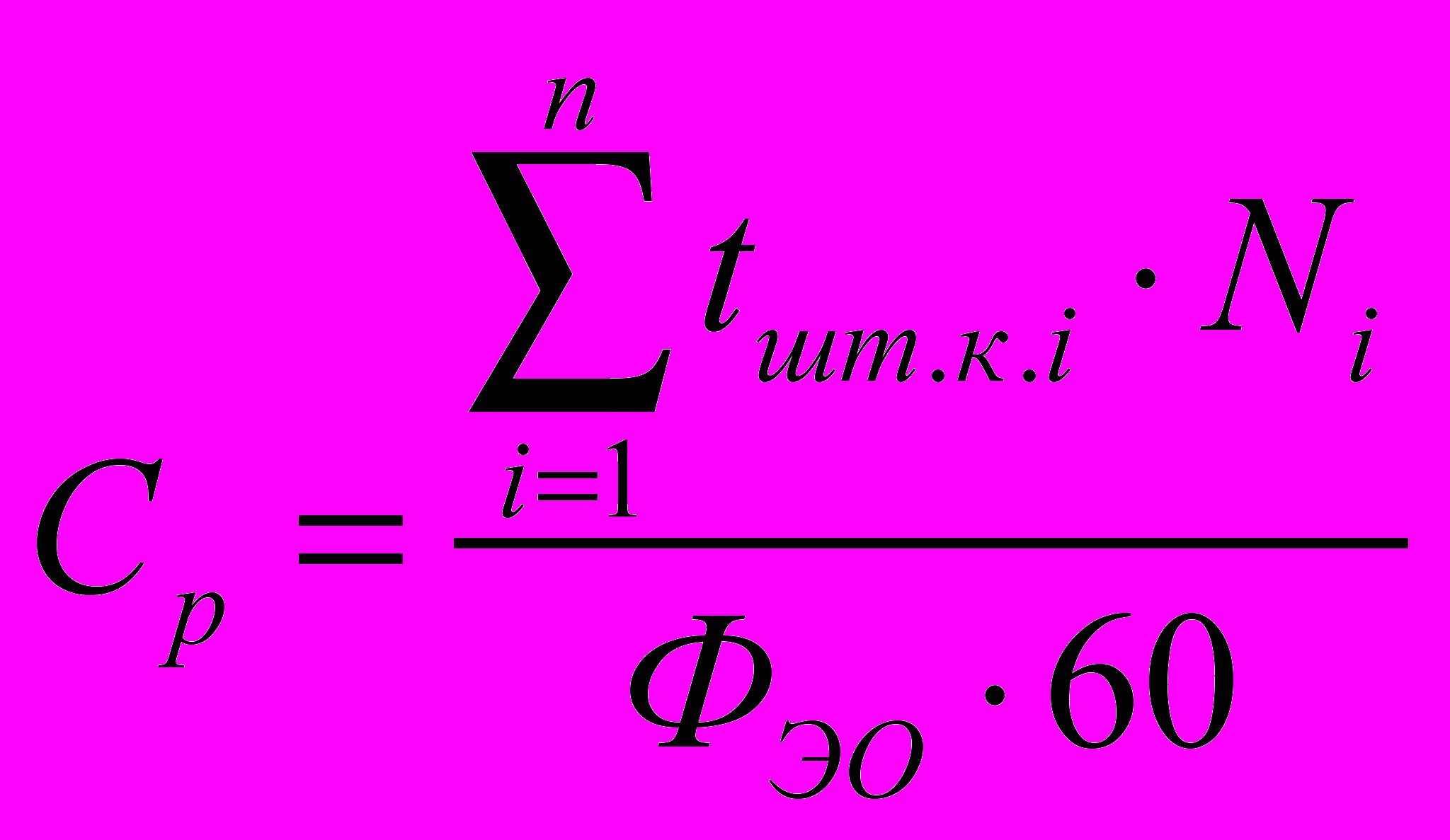
где п — число наименований изделий, проходящих данную операцию;
tшт.к.i, Ni — соответственно время изготовления изделия на данной операции [мин], и ее годовой объем выпуска [шт];
Фэо — эффективный годовой фонд времени работы основного оборудования [ч].
Штучно-калькуляционное время определяется по формуле, приведенной в лекции 10, а при отсутствии данных по составляющим можно пользоваться формулой:
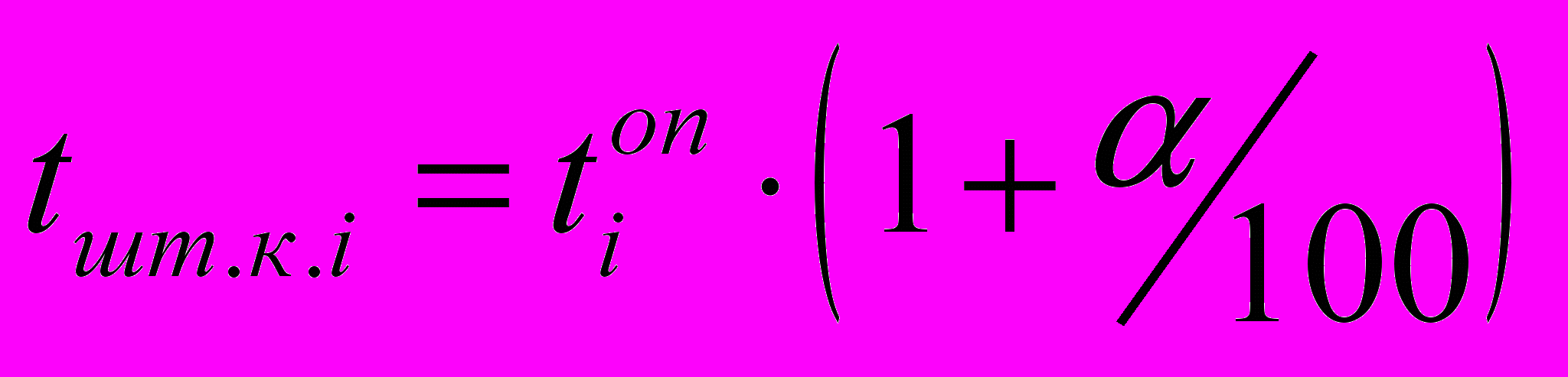
где α — процент потерь времени (внецикловых) от оперативного времени, α = 6...18% в зависимости от сложности наладки.
При непрерывно-поточном производстве такая составляющая штучно-калькуляционного времени как подготовительно-заключительное время не учитывается, так как в данном случае отсутствует переналадка оборудования на другие наименования изделий.
Вычисленное значение Ср округляют до ближайшего большего целого числа, получая при этом количество основного оборудования Спр, принятое для выполнения данной операции. Коэффициент загрузки основного оборудования на данной операции К3 = Ср/Спр.
Следует учесть, что коэффициент загрузки всегда меньше единицы. В случае незначительного превышения (на 5...10%) расчетного количества основного оборудования над ближайшим целым числом необходимо пересмотреть содержание структуры выполнения операции, параметры режимов ее проведения и состава технологического оснащения, что в итоге приведет к общему повышению коэффициента загрузки оборудования. Желательно, чтобы при проектировании поточного производства К3 был больше 0,65.
Верхняя граница коэффициента загрузки оборудования устанавливается исходя из организационных потерь производства, учитываемых коэффициентом использования оборудования.
При расчете числа станций на сборочном конвейере необходимо учесть, что помимо рабочих станций на конвейере размещают 5...10% резервных для случая изменения конструкции собираемого изделия.
При выборе состава и количества основного оборудования необходимо предусмотреть построение технологической системы в виде автоматической линии. Существуют автоматические линии для осуществления технологических процессов механической обработки, сборки, мойки, окраски, упаковки и других операций, которые могут быть классифицированы по различным признакам.
Стационарные автоматические линии характеризуются тем, что изготовляемое изделие не изменяет своего положения относительно основного оборудования и лишь по окончании операции на очередной позиции транспортируется в следующую позицию. На роторных линиях одновременно выполняются технологическая операция и транспортирование. Вследствие ограниченных технологических возможностей роторных линий их используют в основном при сборке и механической обработке простых по конструкции изделий, требующих незначительного числа переходов.
По технологическому назначению различают линии для выполнения операции одного типа (например, механообработка, сборка, окраска и т. д.) и комбинированные линии для выполнения операций различных типов (например, сборка изделий совместно с окраской на одном конвейере, механическая обработка со сборкой и т. д.). Вследствие сложности комбинированных линий их используют довольно редко, а наибольшее применение находят специализированные линии, выполняющие однотипные операции.
По типу используемого оборудования в автоматических линиях их подразделяют на линии, состоящие из специального, агрегатного и специализированного, а также многоцелевого оборудования.
Линии из специального оборудования используют в поточном производстве в том случае, когда изделия изготовляют в течение нескольких лет в большом объеме, что позволяет благодаря концентрации переходов и параллельной структуре выполнения основных и вспомогательных приемов в операции значительно сократить станкоемкость изготовления изделий. Поэтому не используют серийно выпускаемое, а проектируют специальное оборудование.
Линии, скомпонованные из агрегатного и специализированного оборудования (многорезцовые одношпиндельные и многошпиндельные токарные автоматы и полуавтоматы, сверлильные и другие станки, встраиваемые в автоматические линии), применяют преимущественно в поточном производстве с более широкой номенклатурой выпускаемых изделий.
Линии, состоящие из многоцелевого оборудования, используют в гибких производственных системах (ГПС). Они позволяют осуществлять быстрый переход с изготовления изделий одного типоразмера на изготовление изделий другого типоразмера.
Вследствие того, что в поточном производстве используют специальное оборудование и автоматические линии, очень важен выбор оптимальной структурно-компоновочной схемы оборудования, на базе которой выдается техническое задание на его проектирование. Выбор структурно-компоновочной схемы технологической системы обычно производится при комбинаторном, пошаговом решении задачи с поиском оптимального варианта.
Критерием оптимальности служит минимум приведенных затрат, который учитывает объем выпускаемой продукции, станкоемкость выполнения переходов при изготовлении изделия, нормативный коэффициент экономической эффективности, потери времени на отказы оборудования, зависящие от его сложности, затраты на заработную плату обслуживающего персонала, стоимость оборудования и ряд других факторов. В качестве ограничений принимают условия обеспечения требуемого качества изделий и требуемой производительности.
Важным этапом проектирования автоматической линии является разработка структурно-компоновочного варианта линии, обеспечивающего наилучшие технико-экономические показатели. Поэтому из множества вариантов построения линии, отличающихся числом позиций, участков, потоков, типом накопителей, должен быть выбран один, который обеспечит заданную производительность при минимальных приведенных затратах.
Выбор оптимального структурно-компоновочного варианта автоматической линии следует осуществлять непосредственно после разработки последовательности выполнения переходов технологического процесса изготовления изделия и их нормирования. Он производится в следующей последовательности:
• определяется технологически минимальное число рабочих позиций линии qmin;
• оценивается возможность дальнейшей дифференциации технологического процесса и определяется технологически максимальное число рабочих позиций линии qmax;
• рассчитывается длительность совмещенных и несовмещенных переходов tpi и их суммарная величина на позициях
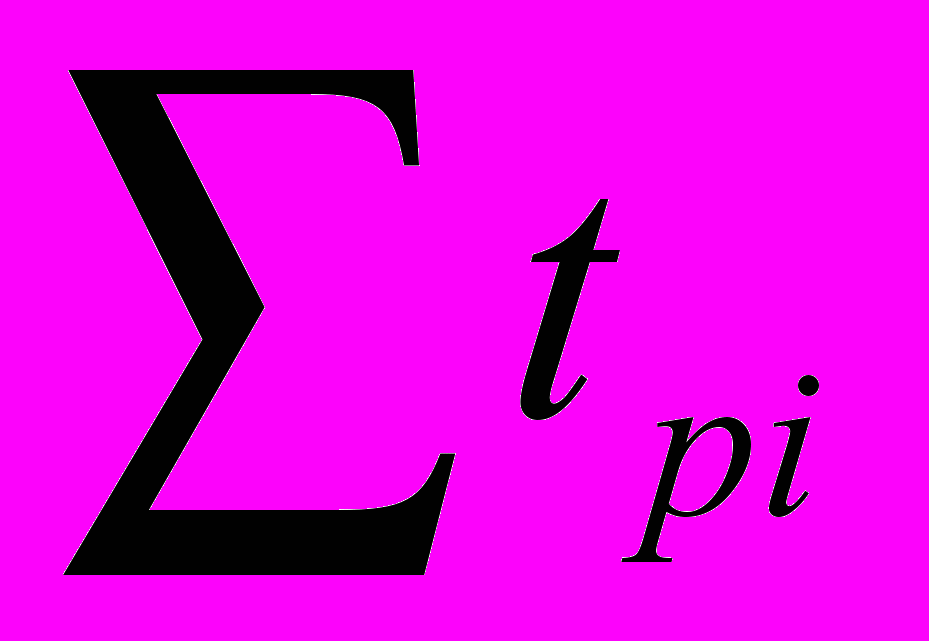
• выбирается конструктивно-компоновочный вариант по строения позиций линии (тип транспортной системы, накопителей, ориентаторов), производится расчет средней ожидаемой длительности времени вспомогательных ходов рабочего цикла tB (транспортирование между позициями, зажим и разжим спутников), зависящего от выбранного типа транспортно-загрузочной системы, и оценка ожидаемой стоимости типовых элементов линии;
• производится укрупненный расчет ожидаемых показателей надежности инструментальной системы и оборудования линии, т. е. ожидаемых внецикловых потерь по инструменту и оснастке
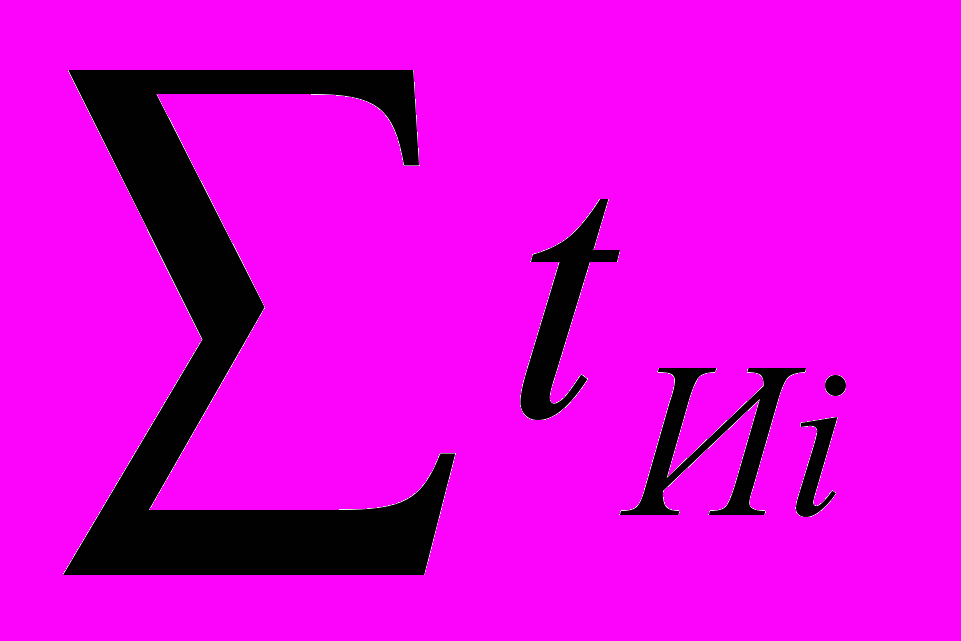
• рассчитывается ожидаемая производительность линии Qi;
• определяются варианты построения компоновок автоматической линии путем дифференциации лимитирующих операций технологического процесса, отличающихся числом позиций q {qmin < q < qmax), участков-секций ny (1 < ny < q), параллельных потоков изготовления изделий р (р = 1, … , n) при выбранных режимах выполнения переходов, количества оборудования, обслуживаемого одним наладчиком, вместимости накопителей и т. д.;
• выбираются из полученных вариантов несколько конкурирующих, которые удовлетворяют требуемому диапазону производительности;
• оптимизируются технико-экономические показатели отобранных конкурирующих вариантов путем варьирования режимов выполнения лимитирующих операций, вместимости накопителей, количества наладчиков;
• рассчитываются ожидаемые экономические показатели Сi отобранных рациональных конкурирующих вариантов и выбирается оптимальный структурно-компоновочный вариант построения автоматической линии.
Ожидаемая производительность линии рассчитывается по формуле:
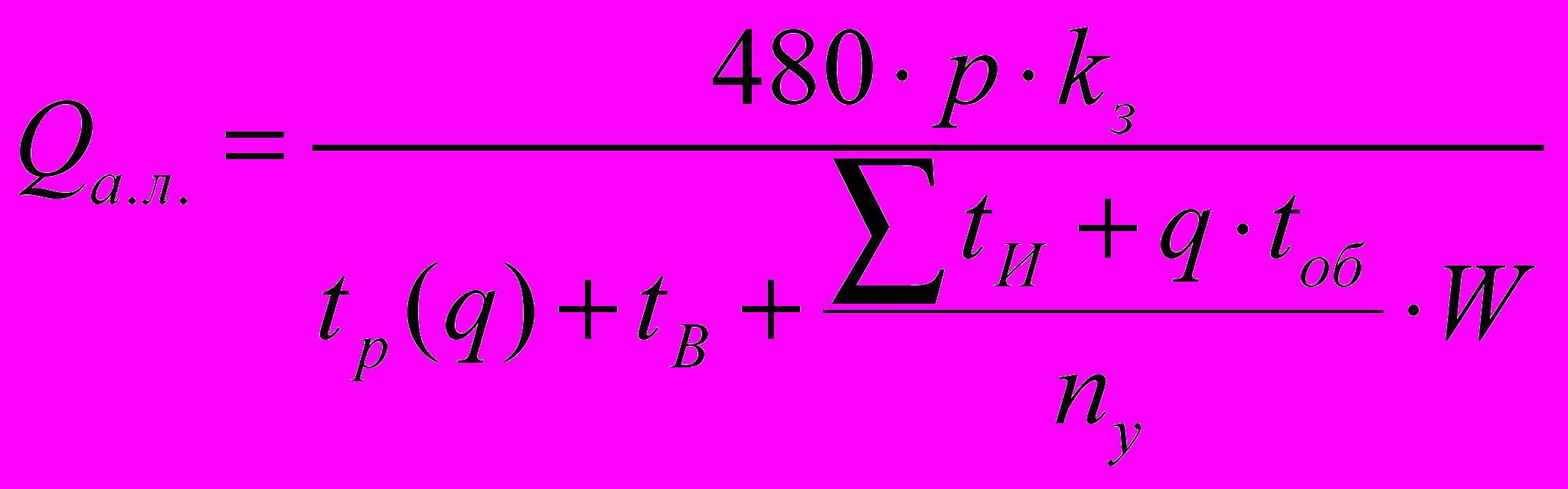
где W — коэффициент возрастания простоев лимитирующего участка вследствие неполной компенсации потерь накопителями.
Ожидаемую производительность линии оценивают с учетом технических и организационных простоев. Обычно принимают коэффициент загрузки линии К3 = 0,85...0,9. Коэффициент возрастания простоев вследствие неполной их компенсации накопителями принимают в зависимости от числа участков линий и вместимости накопителей. При вместимости накопителей, обеспечивающих работу линии в течение 30...50 мин, коэффициент W выбирают в зависимости от числа участков:
пу | 1 | 2 | 3 | 4 | 5 | 6 |
W | 1,0 | 1,10 | 1,15 | 1,18 | 1,20 | 1,22 |
Так как расчеты выполняют на ранних этапах проектирования и они носят укрупненный характер, в них не учитывают затраты на электроэнергию и инструмент, отнесенные к единице продукции, амортизационные отчисления рассчитывают по нормативным коэффициентам в зависимости от стоимости. Аналогичным образом учитывают и затраты на текущий ремонт и обслуживание.
Целенаправленный поиск оптимального структурно-компоновочного решения основного оборудования позволяет сократить число рассматриваемых вариантов структуры выполнения операций, причем на последних шагах поиска используют уточненный критерий. Все это приводит к значительному сокращению трудоемкости проектных работ.
При окончательном выборе структурно-компоновочной схемы основного оборудования необходимо учесть ограничения, накладываемые конструкцией изготовляемых изделий (например, минимально возможное расстояние между шпинделями в многошпиндельной головке, доступность для обработки или сборки с одного установа и т. п.), технологической последовательностью выполнения операции и жесткостью технологической системы, обеспечивающей выполнение требований к качеству изготовляемых изделий, надежностью и габаритными размерами основного оборудования. При начальных стадиях проектирования учесть эти ограничения невозможно вследствие значительного усложнения целевой функции, по которой просчитывают множество вариантов проектных решений.
Принятие оптимального решения по выбору компоновочного варианта основного оборудования может осуществляв ЭВМ, выполняющая как расчетные работы, так и моделирование процессов изготовления изделий. Вследствие сложности формализации сквозного проектирования автоматических линий ЭВМ чаще всего используют в режиме диалога специалиста-технолога и ЭВМ. При этом творческие вопросы проектирования решает технолог, а рутинные вычислительные работы, оценку решения и определение направления поиска оптимального варианта выполняет ЭВМ.