Планирование потребности в материалах
Вид материала | Лекция |
СодержаниеЗависимый и независимый спрос Возрастание значимости MRP Принцип работы «точно в срок» Ключевые требования системы JIT Реализация выполнения операций JIT |
- Налоговое планирование в организации (на материалах организации). Управление налоговыми, 44.39kb.
- Планирование производственной программы промышленного предприятия. Расчет потребности, 236.9kb.
- Стратегическое планирование Бюджетирование Планирование потребности в персонале Подбор, 52.91kb.
- Потребности, ресурсы, выбор Потребности, 83.17kb.
- Анализ и планирование рентабельности банковского капитала с учётом рисков. Анализ социальных, 55.73kb.
- Совершенствование механизма планирования оборотных средств предприятия, 81.15kb.
- Барьеры в международной торговле услугами содержание, 155.42kb.
- Планирование потребности в персонале Сбор информации о вакансии, 2376kb.
- Тема: § 50. Потребности и производство Потребности человека, 51.5kb.
- Оперативный план работы с персоналом в организации. Планирование потребности в персонале, 59.76kb.
Лекция 7
Управление материальным потоком
Планирование потребности в материалах
Ранее мы рассмотрели подход к планированию логистических функций на основе требований к ресурсам. У этого подхода есть ряд недостатков. Например, он достаточно жесток и потому с опозданием реагирует на изменение условий, он слишком полагается на прогнозы – которые часто оказываются ошибочными.
Один из способов устранить это состоит в том, чтобы постоянно сопоставлять предложение логистических услуг с фактическим спросом на них. В этом случае нам необходим механизм определения реального спроса, а не его планирования. В некоторых случаях фактический спрос известен заранее, и возможным оказывается применение планирования потребности в материалах (material requirements planning, MRP). В этом случае для доставки материалов используется основной график.
Зависимый и независимый спрос
Основной подход к планированию исходит из допущения, что общий спрос на продукты складывается из отдельных составляющих спроса большого числа потребителей. Эти отдельные компоненты никак не зависят друг от друга, что формирует независимый спрос (independent demand). В этом случае планирование может осуществляться на основании стандартных методов, рассмотренных нами ранее.
Во многих случаях, однако, один спрос не независим от другого, или спрос на один продукт не независим от спроса на другой продукт. Когда производитель использует набор компонентов для изготовления конечного продукта, спрос на каждый из компонентов связан с другими - поскольку каждый зависит, в свою очередь, от производственного плана изготовления конечного продукта. В этом случае мы имеем зависимый спрос (dependent demand).
Типовой подход на основе MRP заключается в том, что основной график разбивается на составляющие, и на основе этого планируется доставка всех необходимых материалов.
Разница между традиционным подходом и подходом на основе MRP можно проиллюстрировать примером заказа продуктов для ресторана. Традиционный подход предполагает анализ объема и состава использованных на прошлой неделе продуктов, чтобы на основе прошлого спроса спрогнозировать будущий и не испытывать недостатка. Альтернативный подход на основе MRP предполагает анализ блюд, которые шеф-повар собирается готовить каждый день, определение необходимых для этого продуктов и формирование заказа на эти продукты для их своевременного поступления.
Важная разница между этими подходами состоит в характере запасов материалов. При независимом спросе запасы не связываются с производственными планами, а потому должны быть достаточно высокими для удовлетворения любого спроса. Они снижаются во время выполнения операций, но вскоре снова пополняются. При использовании метода MRP запасы обычно низкие, но они повышаются, когда заказы доставляются перед началом выполнения операций. Динамика изменения запасов показана на рисунках ниже.
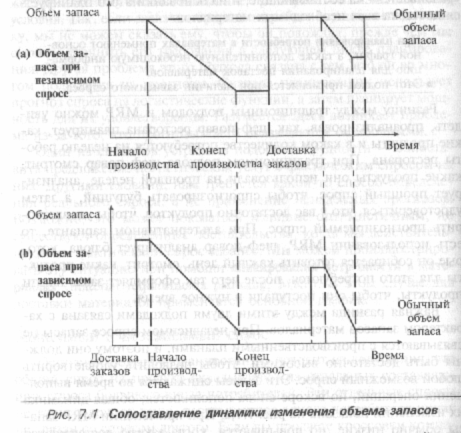
Подход на основе MRP
При MRP используется большой объем информации о графиках, продуктах и материалах. Эта информация поступает из следующих источников:
- основной график, где указывается объем каждого продукта, изготавливаемого в каждый период времени;
- ведомость спецификации материалов, где перечисляются материалы, необходимые для производства каждого продукта;
- учетной документации по запасам, где показано наличие материалов.
Ведомость спецификации материалов – это упорядоченный список всех составляющих, необходимых для производства конкретного продукта. В нем показаны материалы, части и комплектующие, а так же последовательность их использования. Пример спецификации на простейший продукт приведен ниже.
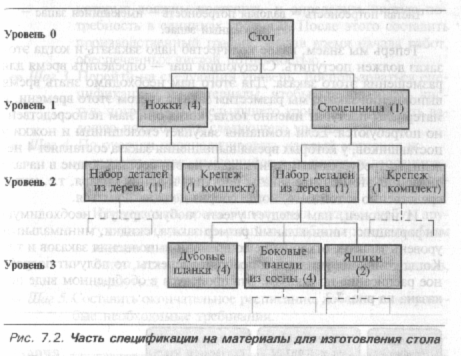
Пусть по основному графику компания планирует в феврале изготовить 10 столов. Очевидно, что в начале февраля ей потребуется 10 столешниц и 40 ножек. Это составляет валовую потребность (gross requirements). На практике не обязательно заказывать все, поскольку часть может быть в запасе или учтена уже размещенными заказами. Если вычесть эти данные из валовой потребности, мы получим чистую потребность (net requirements). Теперь известно, какое количество надо заказать и когда заказ должен поступить. Следующий шаг – определить время размещения заказа. Для этого надо знать время его выполнения: разместив заказ заранее с учетом этого времени, мы получим материалы именно тогда, когда они потребуются. При этом следует учесть всю остальную необходимую информацию: минимальный размер заказа, возможные скидки, разброс времени выполнения заказов и пр. Учтя все эти факторы, получают подробное расписание заказов. В обобщенном виде процедура показана на рисунке ниже.
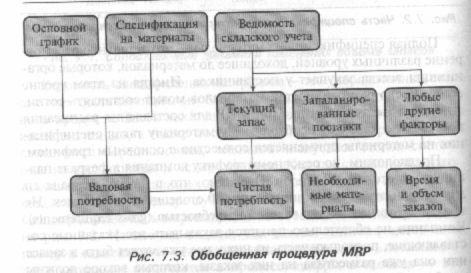
Она состоит из следующих шагов.
Шаг 1. Использовать основной график для определения валовой потребности в единицах уровня 0.
Шаг 2. Вычесть имеющийся запас и уже размещенные заказы для определения чистой потребности в единицах уровня 0.
Шаг 3. Перейти на следующий уровень. Воспользоваться спецификацией материалов для преобразования чистой потребности предыдущих уровней в валовую потребность следующего уровня.
Шаг 4. Проанализировать каждый материал, определив необходимый дополнительный объем. Используя время выполнения заказа и любую иную значимую информацию, определить объемы заказов и время их размещения.
Шаг 5. Составить окончательное расписание, учтя в нем все необходимые условия.
Достоинства MRP
При MRP удается избежать затрат на чрезмерные запасы, появляющиеся в результате вероятностного планирования. Это дает определенные преимущества:
- уменьшение объема запасов (экономия на капитале, используемых площадях, складских работах и пр.);
- повышение скорости оборачиваемости запасов;
- повышение качества обслуживания потребителей (нет задержек, связанных с нехваткой материалов);
- повышение стабильности во времени и скорости доставки заказов;
- уменьшение времени на экспедирование и на выполнение срочных заказов;
- возможность использования графиков MRP для планирования других видов логистической деятельности.
Недостатки MRP
Использование MRP связано с обработкой большого количества информации и необходимостью вычислений. Базовая информация поступает из подробного основного графика, а потому MRP не может применяться если такого графика нет, если он не разрабатывается заранее, если он не точен, если планы часто меняются. То же относится к другим источникам информации – спецификации на материалы, данные о запасах и заказах, время выполнения заказов и другие сведения о поставщиках. В одном случае организации не ведут подобный учет, в другом случае получают ее в ином формате или с недостаточной точностью и достоверностью. Это особенно опасно, поскольку большое число мелких ошибок могут вызвать проблемы, с учетом отсутствия страховых запасов. Еще одна проблема этого подхода – негибкость. В наличии имеются только те материалы, которые нужны для выполнения конкретного основного графика, и внести коррективы сложно.
Наиболее общими недостатками MRP считаются:
- низкая гибкость, не позволяющая реагировать на внешние изменения;
- большой объем подробной и достоверной информации;
- размер заказов, диктуемый MRP, может быть неэффективным;
- MRP может оказаться дорогостоящим и требовать большого времени на реализацию.
Возрастание значимости MRP
Использование MRP
Мы изучили основной MRP подход, теперь мы изучим способы, которые позволяют получать более высокие результаты. Например, основная процедура может предусматривать серию небольших часто размещаемых заказов. В этом случае можно объединить их в более крупный, или осуществить пакетирование (batching). Пакетирование может быть выполнено четырьмя основными методами.
- Партия с размером по потребности (lot-for-lot). Заказ выполняется в точном соответствии с чистой потребностью MRP на каждый период. Это дает преимущества малого заказа, но требует высоких затрат на размещение заказа, на доставку продукции и административные расходы.
- Партия с фиксированным размером заказа (fixed-order quantity). В этом случае предприятие формирует удобный для себя объем заказа (например, соответствующий грузоподъемности автомобиля, размеру контейнера, или определяемый как рентабельный – о чем будет сказано далее). Всякий раз, когда нужно поставить продукцию, заказывается именно это количество, а любые не истраченные излишки отправляются в запас.
- Периодически размещаемые заказы (periodic orders). В этом случае объединяется потребность за какой-то постоянный период времени, и регулярно размещаются заказы, объем которых может меняться. Работа с регулярным расписанием -–это простоя вариант, а размещение заказов – отработанная процедура.
- Объемы заказов, устанавливаемые правилами (batching rules). Для вычисления оптимального объема заказа применяется заранее установленная процедура. Как правило, при этом используется комбинация заказов, при которой общие издержки становятся минимальными. На практике это вызывает сложности в составлении графиков.
Другое направление совершенствования метода связано с тем, что для производства различных видов продукции применяются одни и те же материалы. В этом случае можно объединять спрос, поступивший по всем видам продукции, и получить обобщенную валовую потребность. Аналогично, когда разные материалы заказываются у одного поставщика, есть смысл сводить их в единый заказ. Во всех случаях объем заказываемой партии требуется определять более широко, с учетом разных видов продукции и разных материалов из одного источника.
Более серьезное расширение применение метода MRP требует введения обратной связи. Для размещения заказов на материалы MRP исходит из основного графика, но этот график обычно имеет те или иные отклонения. В цепи поставок, как это было показано ранее, эти отклонения могут многократно усиливаться, и поставщики в конце цепи поставки получают совершенно не те показатели, что на входе в цепь. Операционные возможности оказываются не в состоянии справиться с изменениями спроса, особенно в пиковых режимах.
Очевидно, что подобные проблемы лучше предусмотреть заранее, на этапах планирования, чтобы графики и мощности можно было корректировать до подготовки окончательных планов. Иными словами, должна быть введена обратная связь от MRP к планированию использования мощностей. Эта связь называется планированием потребности в мощностях (capacity requirements planning), а общая система с такой связью называется MRP с замкнутой обратной связью (closed-loop MRP).
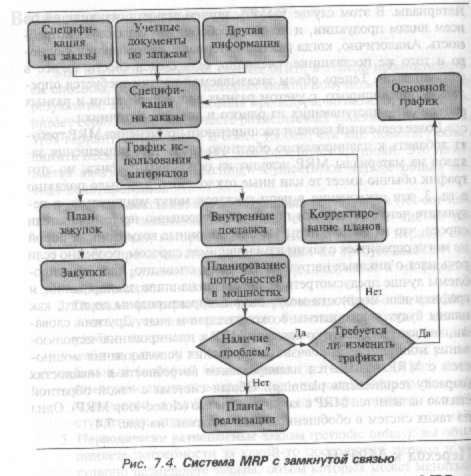
Переход к MRP II
Планирование потребности в мощностях расширяет границы MRP подхода и его использования в организациях. Мы начинали применять MRP для составления графиков поставки материалов, а теперь можем воспользоваться им для планирования мощностей. Но можно пойти дальше: материалы лишь один ресурс, а организации необходимо составлять графики по всем ресурсам – сотрудникам, оборудованию, сооружениям, финансам, транспорту и пр. Применение подхода MRP к анализу всех этих ресурсов является масштабным расширением подхода, который получает в этом случае название планирование производственных ресурсов (manufacture resource planning) или MRP II.
При этом создается интегрированная система, разбивающая основной график на базовые составляющие и позволяющая разрабатывать расписание по всем видам работ, оборудованию, операторам, машинам и сооружениям, требующимся для выполнения этого графика.
В рамках этого подхода графики составляются по всем операциям, включая финансы, маркетинг, продажи, управление персоналом и т.д. MRP II имеет конечной целью создание полностью интегрированной системы синхронизации всех функций организации, которая объединяет графики всех функций и ресурсов на уровне основного графика.
Связь всех видов деятельности с основным графиком может обеспечить очень высокую эффективность логистики, поскольку устраняет задержки доставки заказов дефициты, незавершенное производство. К сожалению, на практике реализация MRPII встречает серьезные трудности. Разработать графики, которые все заинтересованные лица считают в равной степени хорошими и работоспособными, трудно. Сложно определить и то, в какой мере выходы от тесного интегрирования окупят затраченные на это усилия. MRPII не обеспечивает и большой гибкости, в связи с чем организация, масштабно использующая такой вариант, может стать громоздкой и медленно реагировать на изменение условий.
Все это в ряде случаев не дает довести до конца подход MRPII, взятый на вооружение организацией. Для таких частичных вариантов используются разные названия: планирование распределения ресурсов (distribution resource planning), планирование логистических ресурсов (logistics resource planning). Эти термины используются бессистемно и нестрого: первый, например, используют для систем, в которых спрос поступает не от производственного плана, а от заказов потребителей, второй – когда подход на основе MRP осуществляется только для планирования логистики.
Принцип работы «точно в срок»
Работа «точно в срок» (just in time, JIT) предполагает иной принцип планирования и контроля материального потока. Все виды деятельности организуются таким образом, чтобы они совершались точно в то время, когда они необходимы. Иными словами, они не выполняются слишком рано (из-за чего материалы ждут, когда они потребуются), или слишком поздно (из-за чего страдает качество обслуживания заказчиков или потребителей).
Подход JIT кажется очевидной идеей, но может оказать очень сильное влияние на способ организации передвижения всех материалов. Например, при традиционном подходе к закупке сырья его следует закупать на ранних этапах и хранить в виде запасов до того момента, когда оно потребуется. MRP снижает размер запасов, координируя прибытие материалов с запросами на них. Цель JIT – обеспечить доставку материалов непосредственно ко времени выполнения операции, тем самы практически устраняя запасы.
Основная цель накопления запасов – иметь резервный фонд материалов между операциями. Запасы накапливают, когда все идет нормально, чтобы использовать их, когда возникают проблемы. Запасы гарантируют отсутствие сбоев при выполнении операций и менеджерами старой формации считаются важнейшим элементом всей производственной системы.
Чем выше обеспечена степень соответствия между поставками материалов и спросом на них, тем меньший запас требуется. Если несоответствие поставок и спроса устранено полностью, запасы не нужны вообще.
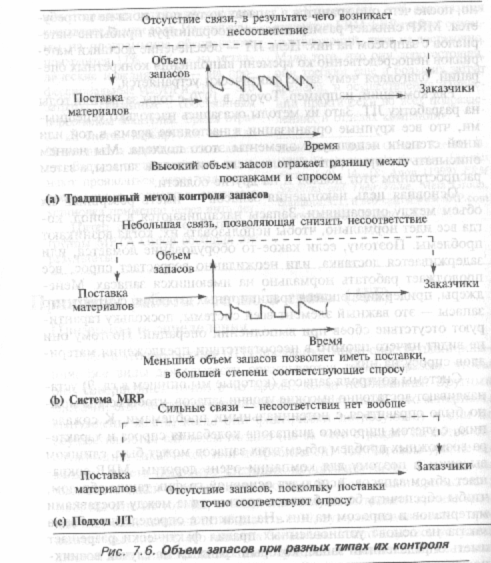
Точка зрения JIT на запасы такова:
- запасы нужны для корректировки краткосрочных несоответствий спроса и поставки;
- эти запасы не служат никакой полезной цели и объясняются лишь плохой координацией;
- пока существует запас, очевидных проблем не возникает и менеджеры не имеют стимулов совершенствовать материальный поток;
- в результате операции плохо управляются, а проблемы прячутся в запасы;
- радикальное решение состоит в отыскании причин, вызывающих разницу между предложением и спросом, и в устранении этих причин.
Эффективность работы JIT
В широком значении подход JIT рассматривает организацию как набор проблем, мешающих эффективному управлению операциями. Среди этих проблем – слишком большое время выполнения заказов, нестабильность доставки, несбалансированность операций, ограниченная мощность, поломки оборудования, бракованные материалы, перерывы в работе, ненадежные поставщики, низкое качество, большой объем канцелярской работы, слишком большие изменения. Эти проблемы пытаются решить за счет создания запасов, но они лишь скрывают проблемы.
Надо изменить взгляды по нескольким направлениям деятельности.
Запасы. Необходимо выявить причины их появления и попытаться устранить их.
Качество. Любые дефекты приводят к затратам. Необходимо выявить причины и добиться устранения дефектов (это полностью соответствует комплексному подходу на основе управления качеством).
Поставщики. JIT в полной мере полагается на надежность поставщиков, и потому поощряет долгосрочные партнерские соглашения с общими целями.
Объем партии. В ходе операций часто экономично выпускать крупные партии продукции, поскольку снижаются затраты на переналадку оборудования и перерывы в производстве. Но при низком спросе продукция, изготовленная крупными партиями, долго лежит в запасах JIT отыскивает способы нахождения оптимального объема партии.
Время выполнения заказов. Продолжительное время выполнения заказов поощряет накопление больших запасов, поскольку это позволяет учесть любые неожиданности, которые могут возникнуть до следующей поставки. JIT ставит цель осуществлять поставки чаще и меньшими партиями, снижая время выполнения заказов.
Надежность. В основе JIT лежит непрерывное постоянное производство, и все операции должны выполнятся надежно. Если что-то не так, надо отыскивать причину и устранять источник ненадежности.
Работники. Подход JIT утверждает, что между обычными работниками и руководителями нет никакого различия, поскольку благосостояние каждого зависит от успеха организации в целом.
Итак, JIT – это не только минимизация запасов. Координируя все виды деятельности, этот подход повышает эффективность и устраняет отходы по всем видам ресурсов.
Ключевые требования системы JIT
Подход JIT успешно работает только в определенных типах организаций, и в первую очередь на сборочных производствах большой мощности, выпускающих практически одну и ту же продукцию. Это происходит по следующим причинам:
- каждый раз при смене продукции возникают сбои и задержки, а для JIT нужна стабильная среда;
- стабильная среда позволяет применить специализированное оборудование, эффективное при массовом производстве;
- уровень производства должен обеспечивать постоянный, без сбоев и всплесков поток продуктов через все производства;
- отсутствие страховых запасов делает производство крайне чувствительным к дефектам;
- возможные сбои в подобной системе должны устраняться максимально быстро, что требует высочайшей квалификации персонала и высокой заинтересованности в успехе предприятия.
Реализация выполнения операций JIT
Успех системы JIT определяется не только основной концепцией (выполнения действий только тогда, когда их целесообразно выполнять), но и тем, насколько хорошо определено, как именно их нужно выполнять. Система работает, «протягивая» материалы через весь процесс их обработки.
В традиционном процессе каждой операции общим расписанием устанавливается время, к которому она должны быть завершена. Полученный продукт «проталкивается» дальше и становится затем запасом незавершенного производства в начале следующей операции. В этом случае полностью игнорируется, что делает в этот момент следующая операция, а она может быть занята выполнением совершенно другой задачи или ожидать поступления другой единицы для сборки. В лучшем случае следующая операция должна завершить свой предыдущий цикл до того, как она сможет начать обрабатывать новую единицу, переданную ей с предыдущего участка. Результатом становится задержки и рост запасов незавершенного производства.
В JIT используется другой подход, при котором обрабатываемая единица «тянется» через весь процесс. Когда в ходе одной операции заканчивается ее обработка, то на предыдущую операцию посылается сигнал готовности работать сней. Предыдущая операция отправляет обрабатываемую единицу дальше только тогда, когда она получает этот сигнал. В этом процессе более ранние операции не проталкивают (push) работу дальше, а скорее вытягивают (pull) ее.
Если в буфете готовят поднос и выносят бутерброды на прилавок – это выталкивающая стратегия, а при заказе конкретного вида бутерброда его готовят и доставляют клиенту «вытягивая» и ликвидируя тем самым незавершенное производство. Видно, что в последнем случае появляется задержка выполнения заказа, почему в реально действующих системах заказы отправляются с некоторым опережением, т.е. до появления физической потребности. Кроме того, материалы поступают не непрерывным потоком, а хоть малыми, но партиями – и потому некоторый запас незавершенного производства в JIT системах все-таки существует. Справедливо утверждать, что в JIT системах запасы не устраняются, а минимизируются.
Канбан
Для реализации JIT необходимо иметь какой-либо способ организации потока продукции, вытягиваемой в ходе процесса. Простейшая система перемещает продукцию между участками в некотором контейнере. Возвращение порожнего контейнера на предыдущий участок есть сигнал заполнить его.
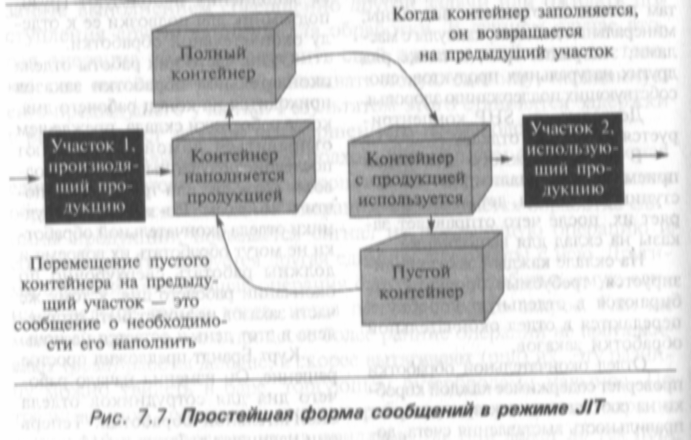
Для большинства операций этот метод недостаточно надежен, и его заменяют на систему канбан. Канбан – это японское название карточки или любой иной наглядной формы учета используемых материалов. С помощью этой карточки орагнизуется вытягивание материалов в ходе общего процесса производства. Способов реализации канбана много, но наиболее общая схема использует два различных вида карт: канбан производства и канбан перемещения.
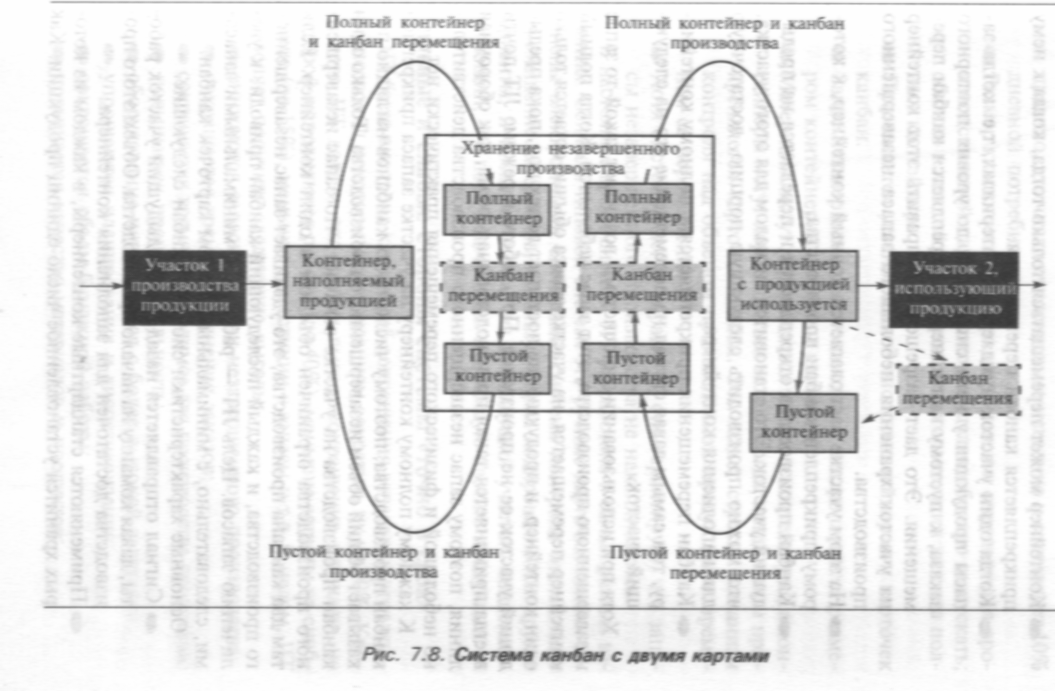
Основные черты системы подобного рода таковы:
- все материалы хранятся и перемещаются в стандартных контейнерах, для каждого материала используется свой контейнер;
- контейнер перемещается лишь тогда, когда к нему прикрепляется канбан перемещения;
- когда участок нуждается в материалах, к порожнему контейнеру прикрепляется канбан перемещения, что является сигналом отправить контейнер на участок хранения небольшого запаса незавершенного производства;
- канбан производства открепляется и передается на предыдущий участок, являясь сигналом начала производства новой порции, достаточной для наполнения контейнера;
- канбан перемещения прикрепляется к полному контейнеру, тем самым давая сигнал на его перемещение на следующий участок.
К каждому полному контейнеру на участке запаса прикреплен канбан производства, и общее число таких канбанов наглядно показывает объем незавершенного производства. Целью JIT является работа с минимальными запасами и, следовательно, с минимальным числом карточек канбан.
Достоинства системы канбан:
- снижение запасов сырья и незавершенного производства;
- сокращение времени выполнения заказов;
- сокращение времени производства продукции;
- повышение производительности;
- повышение загрузки оборудования;
- упрощение планирования и диспетчеризации;
- сокращение объема документации;
- повышение качества материалов и продуктов;
- снижение объема отходов;
- повышение ответственности работников;
- улучшение отношений с поставщиками;
- стремление решать проблемы, возникающие при работе.
К сожалению, за некоторые выгоды надо платить высокую цену. Повышение качества продукции и сокращение простоев вынуждает покупать более дорогое оборудование. Небольшие партии продукции повышают затраты на производство. Высокий профессионализм работников увеличивает затраты на их подготовку и заработную плату. Реакция на быстрое изменение спроса требует резервной мощности оборудования. Самое главное – это неспособность JIT системы справляться с непредвиденными обстоятельствами (поломки, забастовки, аварии).
Специфические проблемы в JIT системах таковы:
- более высокий риск от полного внедрения новых систем и операций;
- первоначальные инвестиции и затраты на реализацию;
- долгое время до существенного улучшения;
- зависимость от высокого качества поставляемых материалов;
- неспособность всех поставщиков перейти на JIT системы;
- необходимость в стабильном производстве, при сезонности и колебаниях спроса;
- снижение гибкости при удовлетворении особых или меняющихся запросов;
- отсутствие духа сотрудничества у работников;
- необходимость изменения общей планировки сооружений;
- работа сотрудников в обстановке стресса.
Расширение JIT на всю цепь поставок
Расширение зоны деятельности JIT и вовлечение в него всех звеньев цепи поставок носит название быстрой реакции (quick response, QR), планирования непрерывного пополнения (continuous replenishment planning, CRP), или эффективной реакции на запросы потребителей (efficient consumer response, ECR).
ECR «тянет» материальные ресурсы через организации, входящие в цепь поставок. С этой целью организации должны выполнить следующую последовательность шагов.
- разработка логистической стратегии на основе оперативно пополняемых запасов;
- понимание принципов ECR, равно как и их влияния на операции;
- формулировка целей по ECR и измерение показателей, получаемых при организации партнерств с другими организациями;
- внедрение систем электронного обмена данными между поставщиками и потребителями;
- создание потоковой логистики, при которой материалы перемещаются с максимальной эффективностью;
- сопоставление операций с лучшими аналогами и непрерывное совершенствование.