4 Разработка технологического процесса
Вид материала | Документы |
- Кафедра технологии машиностроения и методики профессионального обучения курсовой проект, 88.72kb.
- Кафедра технологии машиностроения и методики профессионального обучения курсовой проект, 81.68kb.
- 3 5 Разработка маршрутного технологического процесса, 138.63kb.
- Кафедра технологии машиностроения и методики профессионального обучения курсовой проект, 89.23kb.
- Курсовой проект разработка технологического процесса механической обработки детали, 81.31kb.
- «Разработка технологического процесса изготовления детали «Корпус вибратора», 678.89kb.
- 1. 2 Патентные исследования, 27.99kb.
- Расчетно-пояснительная записка, 642.73kb.
- «Российский государственный профессионально-педагогический университет», 117.59kb.
- Задание на курсовой проект; реферат, 294.21kb.
4.7. Разработка технологического процесса
4.7.1. Типовые технологические процессы
Одной из характерных особенностей стандартизации при конструировании транспортных и технологических машин и оборудования в машиностроении, в том числе и лесном машиностроении, состоит в том, что заданные машины необходимо разрабатывать исходя не только из чисто технических условий, но и из совокупности признаков, характерных для всего ряда смежных типов и размеров. Детали и узлы конструктивно нормализованного ряда позволяют использовать преемственность повторяющихся конструктивных признаков в машинах. Широкая унификация деталей машин обуславливает применение более эффективных методов производства за счет типизации технологических процессов и является основой ускорения технологической подготовки производства.
В основу разработки типовых технологических процессов положена конструктивно-технологическая классификация, предусматривающая систематизацию деталей и узлов по основным признакам как конструктивного, так и технологического подобия. Классификация деталей является первым этапом по созданию типовой технологии. Для деталей транспортных и технологических машин ее проводят на основе технологических классификаторов [31]. В основе классификационных признаков для деталей транспортных и технологических машин выбирают геометрическую форму, конструктивную характеристику отдельных элементов, взаимное расположение элементов, наименование, выполняемую функцию.
Базой транспортных и технологических машин и оборудования лесного комплекса является гусеничная или колесная базы.
Валы транспортных и технологических машин характеризуются цилиндрической формой при длине значительно превышающей основной диаметр. К этим валам относятся ступенчатые и гладкие (коробок перемены передач, торсионные и др.), пустотелые, эксцентриковые (балансиры, кривошипы), кулачковые, коленчатые. Смещение центров при обработке шатунных шеек коленчатого вала или обточка кулачков и эксцентриков распределительных валов не изменяют основную схему технологического процесса изготовления деталей этого подкласса.
Цилиндрические, конические и червячные зубчатые колеса, чашки дифференциалов, ведущие колеса, опорные и направляющие катки транспортных и технологических машин на гусеничной базе, ступицы машин на колесной базе, тормозные барабаны, корпуса и фланцы планетарных коробок, кольца включения, фрикционные диски и другие относятся к деталям, характерным признаком которых является отношение высоты и основного диаметра. Поэтому главными поверхностями обработки таких деталей являются торцы, цилиндрические наружные и внутренние поверхности, обрабатываемых на различных станках токарной группы.
Рычаги, вилки, шатуны, стойки, кронштейны относятся к деталям, у которых наружная поверхность образована сочетанием элементов различной геометрической формы. В транспортных и технологических машинах к рычагам и вилкам относятся рычаги рулевого управления, рычаги подвески, вилки переключения передач, вилки карданных валов, рычаги амортизаторов, балки передней оси машин на колесной базе. Главными поверхностями при обработке таких деталей являются площадки на концах стержня и отверстия на этих площадках.
К корпусным деталям относят литые или сварные детали коробчатого типа, представляющие собой основу для пространственного координирования и кинематической связи деталей и узлов, монтируемых в них. В транспортных и технологических машинах – это корпуса коробок передач, редукторов ведущего, промежуточного и задних мостов и другие. Главными поверхностями при обработке корпусных деталей являются плоскости и основные отверстия, а также обработка мелких отверстий и нарезание в них резьбы.
4.7.1.1. Типовой технологический процесс изготовления валов
К валам относят детали, образованные наружными и внутренними поверхностями вращения; имеющими одну общую прямолинейную ось при отношении длины цилиндрической части к наибольшему наружному диаметру более двух (рис. 22).
Валы классифицируются по различным признакам.
По форме наружных поверхностей:
– бесступенчатые;
– ступенчатые;
– с фасонными частями (конусами, шлицами, фланцами, зубчатыми венцами, кулачками, рейками и т.п.).
По форме внутренних поверхностей:
– сплошные;
– полые.
По соотношению размеров:
– жесткие;
– нежесткие.
Жесткими считаются валы, у которых отношение длины к диаметру (l/d) не превышает 10 – 12. Валы с большим соотношением называют нежесткими
Особую группу составляют коленчатые, кулачковые валы, шпиндели и крупные валы (диаметром более 200 мм и массой более 1 т.).
Основные технологические задачи при обработке валов следующие:
– выдержать: точность и шероховатость поверхностей (5 – 7 квалитет; шероховатость Ra 0,03 – 2,5 мкм); прямолинейность общей оси; концентричность поверхностей вращения; соосность резьб с наружными поверхностями или точными внутренними цилиндрическими отверстиями;
– получить глубокие центральные отверстия, соосные наружной поверхности в пустотелых валах (допускаемые отклонения ± 0,02) с радиальным биением шеек и торцовым биением торцов 0,02 – 0,03;
– выполнить шпоночные канавки и шлицы, параллельные оси вала (допускаемое отклонение 0,03 на длине 100мм).
а) ![]() | б) ![]() | в) ![]() |
г) ![]() | д) ![]() | е) ![]() |
Рис. 22. Типичные ступенчатые валы:
а – ступенчатый вал без шлицев и зубчатого венца; б – шлицевой вал; в – вал-шестерня без шлицев;
г – вал-шестерня со шлицами; д – вал-шестерня коническая со шлицами; е – полый ступенчатый вал
Материалом для валов служат стали следующих марок: А12, 20, 20Л, 25, 30, 35, 40, 45, 45Г2, 20Х, 35Х, 40Х, 35ХС, 40ХС, 35СГ, 18ХГТ, 20ХН3А, ЗОХНЗ, 35ХНЗМ, 45ХН2МФ и др.
В большинстве случаев заготовками для валов служит прокат. Заготовки отрезают из прокатного материала фрикционными и дисковыми пилами, абразивными кругами, резцом и др. Для валов, диаметры ступеней которых отличаются больше чем на 10 мм, заготовки отрезают из проката и затем куют под молотами или штампуют в подкладных или закрытых штампах. Главное требование к заготовкам – прямолинейность, которая не должна выходить за пределы 0,1–0,15 мм на 1м длины. Поэтому прокат перед отрезкой заготовок подвергают правке на специальных правильно-калибровочных станках и др.
Основные технологические базы - преимущественно центровые отверстия, центровые фаски для пустотелых валов.
Основные операции при обработке гладких и ступенчатых валов – это центрование, обточка на токарных станках, шлифование посадочных поверхностей, доводка поверхностей.
Таблица 39
Маршрутный технологический процесс обработки ступенчатых валов
№ | Операция | Оборудование | Технологическая база | |
Наименование | Содержание | |||
000 | Заготовительная Правильная Отрезная Термическая | Правка прутка | Правильно-калибровочная машина | Наружная поверхность |
Разрезание прутка по длине | Токарный, отрезной станки. Ножницы. Ножовка. | Наружная поверхность | ||
010 | Фрезерно-центровальная. Токарная | Фрезерование (подрезание) торцов и центрование (Подготовка технологических баз) | Фрезерно-центровальный или токарный станки | Наружная поверхность |
015 | Токарная | Черновая и чистовая токарная обработка | Токарный станок | Центровые отверстия |
020 | Фрезерная | Фрезерование шпоночных канавок, лысок, уступов | Фрезерный станок (шпоночно-фрезерный) | Центровые отверстия, шейки вала |
025 | Сверлильная. | Сверление отверстий, нарезание резьбы | Сверлильный станок | Шейки вала |
030 | Шлицефрезерная | Черновая, чистовая обработка шлицев | Шлицефрезерный станок | Центровые отверстия |
035 | Зубообрабатывающая | Черновое, чистовое нарезание зубьев | Зубофрезерный станок | Центровые отверстия |
040 | Термическая | Термообработка | Печь, установка ТВЧ | Центровые отверстия |
045 | Токарная. Шлифовальная | Зачистка, центровых отверстий | Токарный. Центрошлифовальный | Центровые отверстия |
050 | Шлифовальная | Шлифование опорных шеек | Шлифовальный станок | Центровые отверстия |
055 | Шлицешлифовальная | Обработка боковых поверхностей шлицев и центрирующих диаметров шлицевой части вала | Шлицешлифовальный, круглошлифовальный станки | Центровые отверстия |
060 | Зубообрабатывающая | Отделка зубьев | | Центровые отверстия |
065 | Моечная | | | |
070 | Контрольная | | | |
Основные схемы базирования.
Основными конструкторскими базами большинства валов являются поверхности опорных шеек. Однако использовать их в качестве технологических баз для обработки наружных поверхностей на всех операциях затруднительно. Для условия сохранения единства и постоянства баз за технологические базы принимают поверхности центровых отверстий (ГОСТ 14034–74). Для исключения погрешности базирования при выдерживании длин ступеней от торца вала необходимо в качестве опорной технологической базы использовать торец заготовки. С этой целью заготовку устанавливают на плавающий передний центр.
Передача крутящего момента при установке вала в центрах осуществляется с помощью поводкового патрона (ГОСТ 2571–71) или хомутика (ГОСТ 2578–70).
Основные операции механической обработки
Заготовительная.
Для заготовок из проката: рубка прутка на прессе или резка прутка на фрезерно-отрезном или другом станке. Для заготовок, получаемых методом пластического деформирования, штамповать или ковать заготовку.
Правильная (применяется для проката). Правка заготовки на прессе или другом оборудовании. В массовом производстве может производиться до отрезки заготовки. В этом случае правится весь пруток на правильно-калибровочном станке.
Термическая.
Улучшение, нормализация.
Подготовка технологических баз.
Операцию обработки торцов и сверление центровых отверстий в зависимости от типа производства производят:
– в единичном производстве подрезку торцов и центрование на универсальных токарных станках последовательно за два установа с установкой заготовки по наружному диаметру в патроне;
– в серийном производстве подрезку торцов выполняют раздельно от центрования на продольно-фрезерных или горизонтально-фрезерных станках, а центрование – на одностороннем или двустороннем центровальном станке. Применяются фрезерно-центровальные полуавтоматы последовательного действия с установкой заготовки по наружному диаметру в призмы и базированием в осевом направлении по упору;
– в массовом производстве применяют фрезерно-центровальные станки
барабанного типа, которые одновременно фрезеруют и центруют две за
готовки без съема их со станка.
Форму и размеры центровых отверстий назначают в соответствии с их технологическими функциями по ГОСТ 14034–74 (см. табл. 2)
Для нежестких валов (отношение l/d > 12) - обработка шеек под люнеты.
Токарная (черновая).
Выполняется за два установа на одной операции (единичное производство) или каждый уставов выполняется как отдельная операция.
Производится точение наружных поверхностей (с припуском под чистовое точение) и канавок. Это обеспечивает получение точности IT 12, шероховатости Ra = 6,3. В зависимости от типа производства операцию выполняют: в единичном производстве на токарно-винторезных станках; в мелкосерийном – на универсальных токарных станках с гидросуппортами и станках с ЧПУ; в серийном – на копировальных станках, горизонтальных многорезцовых, вертикальных одношпиндельных полуавтоматах и станках с ЧПУ; в крупносерийном и массовом – на многошпиндельных многорезцовых полуавтоматах; мелкие валы могут обрабатываться на токарных автоматах.
Токарная (чистовая).
Аналогична приведенной выше. Производится чистовое точение шеек (с припуском под шлифование). Обеспечивается точность 11 – 10 квалитет, шероховатость Ra = 3,2.
Фрезерная.
Фрезерование шпоночных канавок, шлицев, зубьев, всевозможных лысок.
Шпоночные пазы в зависимости от конструкции обрабатывают дисковой фрезой (если паз сквозной) на горизонтально-фрезерных станках, пальцевой шпоночной фрезой (если паз глухой) на вертикально-фрезерных станках. В серийном и массовом производствах для получения глухих шпоночных пазов применяют шпоночно-фрезерные полуавтоматы, работающие «маятниковым» методом.
Технологическая база – поверхности центровых отверстий или наружные цилиндрические поверхности вала. При установке на наружные цилиндрические поверхности вала (на призмы) возникает погрешность базирования, связанная с колебаниями диаметров установочных шеек вала в партии.
Шлицефрезерная.
Шлицевые поверхности на валах чаще всего получают обкатыванием червячной фрезой на шлицефрезерных или зубофрезерных станках с установкой вала в центрах. При диаметре шейки вала более 80 мм шлицы фрезеруют за два рабочих хода.
Сверлильная.
Сверление всевозможных отверстий.
Резьбонарезная.
На закаливаемых шейках резьбу изготавливают до термообработки. Если вал не подвергается закалке, то резьбу нарезают после окончательного шлифования шеек (для предохранения резьбы от повреждений). Мелкие резьбы у термообрабатываемых валов получают сразу на резьбошлифовальных станках.
Внутренние резьбы нарезают машинными метчиками на сверлильных, револьверных и резьбонарезных станках в зависимости от типа производства.
Наружные резьбы нарезают:
– в единичном и мелкосерийном производствах на токарно-винторезных
станках плашками, резьбовыми резцами или гребенками;
– в мелкосерийном и серийном производствах резьбы не выше 7-ой степени точности нарезают плашками, а резьбы 6-ой степени точности - резьбонарезными головками на револьверных и болторезных станках;
– в крупносерийном и массовом производствах - гребенчатой фрезой на
резьбофрезерных станках или накатыванием.
Термическая.
Закалка объемная или местная согласно чертежу детали.
Токарная. (Центрошлифовальная).
Исправление центровых отверстий (центрошлифовальная). Перед шлифованием шеек вала центровые отверстия, которые являются технологической базой, подвергают исправлению путем шлифования конусным кругом на центрошлифовальном станке за два установа или притираются на токарных станках.
Шлифовальная.
Шейки вала шлифуют на круглошлифовальных или бесцентрово-шлифовальных станках.
Шлицешлифовальная.
Шлицы шлифуются в зависимости от центрирования:
– при центрировании по наружной поверхности – наружное шлифование
на круглошлифовальных станках и шлифование боковых поверхностей
на шлицешлифовальном полуавтомате с делением;
– при центрировании по поверхности внутреннего диаметра – шлифование
боковых поверхностей шлицев и шлифование внутренних поверхностей
по диаметру профильным кругом.
Моечная.
Контрольная.
Нанесение антикоррозионного покрытия.
Операционные эскизы маршрутного технологического процесса изготовления валов представлен в табл. 40, 41.
Таблица 40
Маршрутный технологический процесс изготовления вала длиной до 120 мм
Операция | |||
П/п | Наименование | Содержание | Операционный эскиз |
000 | Заготовительная | Прокат | ![]() |
005 | Токарная | Обтачивание с припуском под шлифование, снятие фасок и отрезка в размер по длине. | ![]() |
010 | Шлифовальная | Шлифование шеек вала (черновое) | ![]() |
015 | Фрезерная | Фрезерование шпоночных канавок | ![]() |
020 | Сверлиль- ная | Сверление продольных (осевых) и поперечных (радиальных) отверстий | ![]() |
025 | Термическая | | |
030 | Шлифовальная | Окончательное шлифование шеек вала. | ![]() |
035 | Контрольная | |
Таблица 41
Маршрутный технологический процесс изготовления валов диаметром 30 0 80 мм и длиной от 120 до 500 мм
Операция | |||
П/п | Наименование | Содержание | Операционный эскиз |
000 | Заготови- тельная | Штамповка. (Прокат) | |
005 | Фрезерно-центровальная | Фрезерование торцов и центрование | ![]() |
010 | Токарная | Черновая обработка поверхностей (два установа) | ![]() |
015 | Токарная | Чистовая обработка поверхностей (два установа) | ![]() |
020 | Накатная | Накатывание рифлений | ![]() |
025 | Круглошлифовальная | Шлифование предварительное | ![]() |
030 | Фрезерная | Фрезерование шпоночных канавок | ![]() |
035 | Шлицефре зерная (Фрезерная) | Нарезание шлицев | ![]() |
040 | Зубофрезерная | Нарезание зубьев | ![]() |
045 | Зубозакругляющая | Закругление зубьев | ![]() |
050 | Токарная (Резьбофрезерная) | Нарезание резьбы | ![]() |
055 | Химико-термическая | | |
060 | Шевинго- вальная | Шевингова- ние зубьев | ![]() |
065 | | Калибровка резьбы | |
070 | Термичес кая | Закалка Закалка ТВЧ | |
075 | Токарная (Центро- шлифовальная) | Притирка (шлифование центров) | ![]() |
080 | Обкаточная | Обкатка зубьев | ![]() |
085 | Круглошлифовальная | Шлифование шеек вала | ![]() |
090 | Шлицешлифовальная | Шлифование шлицев | ![]() |
095 | Контрольная | |
4.7.1.2. Типовой технологический процесс изготовления втулок
К втулкам относят детали, образованные наружными и внутренними поверхностями вращения, имеющими одну общую прямолинейную ось при отношении длины цилиндрической части к наибольшему наружному диаметру более 0,5 и менее или равное 2 (рис. 23).
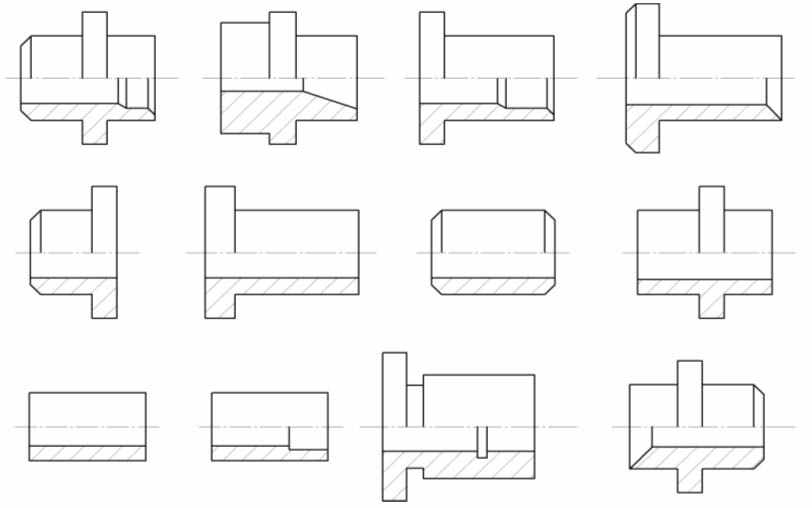
Рис. 23. Типичные детали класса втулки
Основные технологические задачи:
– обеспечение точности и концентричности наружных поверхностей относительно отверстия (точность 7–9 квалитет; шероховатость поверхности отверстия Ra 1,25…0,32 мкм: наружной - Ra 2,5…0,63 мкм);
– обеспечение перпендикулярности торцов к оси отверстия (0,015-0,020 мм на диаметре 100 мм);
– достижение точности взаимного расположения поверхностей (радиальное биение 0,01–0,03) и точности формы (отклонение от круглости и профиля продольного сечении в пределах допуска на размер).