Рабочая программа специальности 100700. Промышленная теплоэнергетика (ПТ) направления 650800. Теплоэнергетика испециальности 330100. Безопасность жизнедеятельности в техносфере (бжт) направления
Вид материала | Рабочая программа |
- Рабочая программа для студентов VI курса специальности, 350.79kb.
- Рабочая программа для студентов Vкурса специальности 290800. Промышленная теплоэнергетика, 63.46kb.
- Рабочая программа учебной дисциплины сд. 13 Информационные технологии в управлении, 340.61kb.
- Чурикова Екатерина Валериевна рабочая программа, 322.31kb.
- Рабочая программа и задание на курсовую работу с методическими указаниями для студентов, 1673.35kb.
- Рабочая программа для студентов II курса специальности 280101 «Безопасность жизнедеятельности, 279.42kb.
- Рабочая программа учебной дисциплины «промышленная экология региона», 229.54kb.
- К ф. н., доцент Латышева, 547.01kb.
- Рабочая программа для студентов IV курса специальности 100700 промышленная теплоэнергетика, 243.31kb.
- Рабочая программа и задание на контрольную работу с методическими указаниями для студентов, 1598.02kb.
МПС РОССИИ
РОССИЙСКИЙ ГОСУДАРСТВЕННЫЙ ОТКРЫТЫЙ ТЕХНИЧЕСКИЙ УНИВЕРСИТЕТ ПУТЕЙ СООБЩЕНИЯ

16/3/1
Одобрено кафедрой «Теоретическая и прикладная механика»
Утверждено деканом факультета «Транспортные средства»
МЕХАНИКА
(ПРИКЛАДНАЯ МЕХАНИКА)
Рабочая программа
специальности
100700. ПРОМЫШЛЕННАЯ ТЕПЛОЭНЕРГЕТИКА (ПТ)
направления
650800. ТЕПЛОЭНЕРГЕТИКА И специальности
330100. БЕЗОПАСНОСТЬ ЖИЗНЕДЕЯТЕЛЬНОСТИ В ТЕХНОСФЕРЕ (БЖТ)
направления
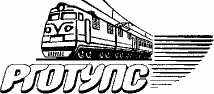
Москва - 2007
656500. БЕЗОПАСНОСТЬ ЖИЗНЕДЕЯТЕЛЬНОСТИ
Разработана на основании примерных учебных программ данных дисциплин, составленной в соответствии с государственными требованиями к минимуму содержания и уровню подготовки инженера по специальностям: 100700 и 330100.
Составители — проф. В.Г. МИЦКЕВИЧ, проф. Г.П. НОСКОВ, проф. B.C. СЕМЕНОЖЕНКОВ, доц. А.В. ВАСИЛЬЕВ
© Российский государственный открытый технический университет путей сообщения, 2002
1. ЦЕЛИ И ЗАДАЧИ ДИСЦИПЛИНЫ
1.1. Цели изучения дисциплины — овладеть знаниями, умениями и навыками, необходимыми для дальнейшего изучения специальных инженерных дисциплин и последующей деятельности в условиях производства.
"Механика" (прикладная механика) — дисциплина, представляющая собой основу общетехнической подготовки инженеров.
В курсе "Механика" в полной мере используются сведения, полученные студентами при изучении общенаучных и инженерных дисциплин, таких как "Высшая математика", "Физика", "Инженерная графика", "Вычислительная математика", "Теоретическая механика" и др.
Будучи комплексной дисциплиной, "Механика" включает в себя в том или ином объеме основные положения курсов "Сопротивление материалов", "Теория механизмов и машин", "Детали машин и основы конструирования". При этом соответствующие разделы вводятся как логически обусловленные и связанные между собой темы единой дисциплины.
1.2. Задачи изучения дисциплины
Изучив дисциплину, студент должен:
1.2.1. Иметь представление об общих принципах проектирования и конструирования, построения моделей и алгоритмов расчетов типовых изделий машиностроения с учетом их главных критериев работоспособности, что необходимо при создании нового или модернизации и надежной эксплуатации действующего оборудования отрасли.
- Знать и уметь использовать основные положения сопротивления материалов, теории механизмов и машин, деталей машин.
- Иметь опыт правильного выбора расчетной модели и выполнения необходимых расчетов в процессе проектирования и оценки работоспособности изделий машиностроения.
Тематика практических занятий и номера лабораторных работ из приведенного в данной программе перечня утверждены решением кафедры в зависимости от специальности студента,
2. СОДЕРЖАНИЕ ДИСЦИПЛИНЫ
Введение
Прикладная механика как научно-теоретическая основа механизации и автоматизации производства. Её связь с другими науками. Роль отечественных ученых в создании научных школ. Структура курса и его связь с другими дисциплинами [1, c.2 -4; 2, c.3- 6].
2.1. ТЕОРИЯ МЕХАНИЗМОВ И МАШИН
2.1.1. Общие сведения
Основные понятия и определения: изделие машиностроения, оборудование, машина, аппарат, установка, прибор, механизм, сборочная единица, деталь. Механизм как кинематическая основа технологических, энергетических, транспортных, информационных и других машин [1, c.4-6; 2, c.4-5].
2.1.2. Структура механизмов
Звенья и их связи. Кинематические пары, их виды и свойства. Кинематические цепи. Число степеней свободы механизма. Структурные формулы. Классификация плоских шарнирно-рычажных механизмов [1, c.6-11; 2, c.7-17].
2.1.3. Анализ механизмов
Задачи и методы кинематического анализа механизмов. Кинематические диаграммы. Планы скоростей и ускорений. Задачи и методы динамического анализа механизмов. Силы, действующие на звенья механизмов. Кинетостатика плоского рычажного механизма. Уравновешивающая сила (момент). Приведенные массы, силы, моменты. Динамическая модель механизма. Уравнение движения механизма. Неравномерность движения машинного агрегата. Балансировка вращающихся тел. Трение в кинематических парах. КПД механизмов [1, c.12-17; 2, c.203-215, 326-333; 5, c.18-36].
2.1.4. Синтез механизмов
Кинематический синтез. Динамический синтез. Основная теорема зацепления. Цилиндрическая зубчатая передача. Эвольвента окружности. Эвольвентное зацепление, его параметры и свойства. Построение внешнего эвольвентного зацепления прямозубых цилиндрических колес. Способы изготовления цилиндрических зубчатых колес. Косозубые колеса. Пространственные передачи зацеплением: прямозубая комическая передача, червячная передача.
Виды кулачковых механизмов. Определение профиля кулачка по заданной функции движения ведомого звена (толкателя) [1,c. 47-89; 2, c.143-158, 225-232, 320-323].
2.2. СОПРОТИВЛЕНИЕ МАТЕРИАЛОВ
2.2.1 .Общие сведения
Понятия, допущения и определения. Прочность, жесткость и устойчивость. Схематизированные объекты изучения: брус, пластинка, оболочка и массив. Сплошность, однородность и изотропность материала. Внешние силы и их классификация. Деформации и перемещения. Метод сечений. Внутренние силы. Напряжение (полное, нормальное и касательное) с.87 - 128; 2, c.27-34].
2.2.2. Растяжение и сжатие
Осевое (центральное) растяжение и сжатие. Напряжения.. Уравнение совместности деформации.
Теоретический и эффективный коэффициенты концентрации. Контакты двух шаров. Контакты двух цилиндров. Общий случай контакта двух тел. Предельные состояния. Коэффициент запаса прочности. Условия прочности при растяжении (сжатии). Расчет по допускаемым напряжениям и допускаемым нагрузкам [1, c.123-167; 2, c.35-52].
2.2.3. Геометрические характеристики сечений
Площадь. Статический момент. Осевые или экваториальные моменты инерции. Полярный момент инерции. Центробежный момент инерции. Зависимость между моментами инерции относительно параллельных осей. Моменты инерции простых и сложных сечений. Главные оси инерции и главные моменты инерции [1, c. 143-148; 2, c.75-79].
2.2.4. Сдвиг. Кручение
Напряженное состояние и деформации при сдвиге. Чистый сдвиг, 3акон Гука при сдвиге. Модуль сдвига. Практические расчеты на сдвиг.
Кручение круглого прямого вала. Момент сопротивления и напряжения при кручении. Угол закручивания и жесткость вала. Построение крутящих моментов и углов закручивания. Определение диаметра вала из условия прочности и жесткости при кручении. Напряжения в брусе прямоугольного сечения при кручении [1, c.156-186; 2, c.52- 59].
2.2.5. Изгиб
Общие понятия о деформации изгиба. Чистый изгиб. Прямой изгиб. Поперечный изгиб. Опоры и опорные реакции балок. Изгибающий момент и поперечная сила. Зависимость между изгибающим моментом, поперечной силой и интенсивностью распределенной нагрузки. Построение эпюр изгибающих моментов и поперечных сил. Нормальные напряжения при изгибе. Осевые моменты сопротивления. Условие прочности по нормальным напряжениям.
Касательные напряжения при изгибе. Главные напряжения. Расчет на прочность по допускаемым напряжениям. Расчет по предельным состояниям и допускаемым нагрузкам.
Линейные и угловые перемещения три изгибе. Дифференциальное уравнение изогнутой оси балки. Универсальное уравнение [1, c.201-223; 2, c.67-71,79-82].
2.2.6. Сложное сопротивление. Теории, прочности
Виды сложного сопротивления. Основные теории прочности. Косой изгиб. Внецентренное растяжение (сжатие). Изгиб с кручением [1, c.205-237; 2, c.85-88,63-67].
2.2.7. Устойчивость сжатых стержней
Понятие устойчивости. Продольный изгиб. Формула Эйлера для критической силы. Влияние способа закрепления концов стержня на величину критической силы. Пределы применимости формулы Эйлера. Формула Ясинского. Практический метод расчета на устойчивость [1, c.234-245; 2, c.90-94].
2.2.8. Переменные напряжения
Усталость материалов. Предел выносливости. Влияние состояния поверхности и концентраторов напряжений на прочность. Масштабный фактор. Выносливость при совместном действии изгиба и кручения. Параметры циклов переменных напряжении. Определение коэффициента запаса прочности. Практические меры повышения усталостной прочности [1, c.211-2264; 2, c.94-101].
2.2.9. Упругие колебания и удар
Собственные и вынужденные упругие колебания систем с одной степенью свободы. Резонанс при колебаниях. Приближенные, методы определения частот собственных колебаний. Напряжения при ударе. Ударная прочность. Динамические коэффициенты при ударных нагрузках [1, c. 259-273; 2, c.333-344].
2.3. ДЕТАЛИ МАШИН
2.3.1. Общие сведения
Детали машин общего назначения. Критерии работоспособности. Надежность и долговечность. Выбор материалов. Стандартизация. Допуски и посадки. Единая система конструкторской документации [1, c.297- 316; 2, c. 110-122].
2.3.2. Соединения
Основные виды соединений. Сварные соединения. Способы сварки. Основные схемы нагружения. Резьбовые соединения. Область применения. Виды и геометрические параметры резьб. Стандартные крепежные детали. Способы стопорения резьбовых соединений. Силовые соотношения в винтовой паре. Самоторможение. Расчет резьбовых соединений на прочность [1, c. 325-341; 2, c.278-304].
2.3.3. Механические передачи
Общие сведения. Классификация, устройство и назначение передач. Силовые и кинематические соотношения в передачах.
Зубчатые передачи. Область применения. Достоинства и недостатки, классификация. Параметры зубчатых передач. Конструкции и материалы зубчатых колес. Точность изготовления. Критерии работоспособности зубчатых передач. Расчет цилиндрических прямозубых передач на контактную и изгибную прочность.
Особенности конструкций и расчета цилиндрических косозубых и конических прямозубых передач. Передачи с зацеплением Новикова.
Редукторы, мультипликаторы и коробки передач. Планетарные и дифференциальные передачи. Смазка зубчатых передач.
Червячные передачи. Общие сведения, достоинства и недостатки. Основные параметры и их выбор. Критерии работоспособности. Материалы червяков и колес. Силы, действующие в зацеплении. Расчеты передачи на контактную и изгибную прочность. Червячные редукторы. Тепловой расчет и смазка.
Цепные передачи. Виды и область применения. Приводные цепи. Звездочки. Основные параметры и соотношения. Основы расчета.
Ременные передачи. Общие сведения, достоинства, недостатки и область применения. Конструкции и материалы. Сиди, действующие в ременной передаче, и критерии ее работоспособности. Основы расчета плоско- и клиноременных передач.
Фрикционные передачи. Общие сведения. Классификация, достоинства, недостатки и область применения. Материалы. Критерии работоспособности. Расчет на прочность и рекомендации по конструированию.
Передачи винт-гайка. Область применения. Основные схемы. Резьбы. Передаточное отношение. КПД Расчеты силовых передач [1, c.242-323; 2, c126-143,163-202].
2.3.4. Валы, подшипники, муфты
Валы. Основные типы валов и их конструкции. Материалы. Критерии работоспособности. Расчетные схемы. Приближенный расчет валов. Расчет на выносливость и жесткость.
Подшипники качания. Классификация. Основные типы, устройство и маркировка. Критерии работоспособности. Расчет (подбор) подшипников качения по динамической и статической грузоподъемностям. Смазка, монтаж и демонтаж подшипников.
Подшипники скольжения. Общие сведения. Режимы трения. Конструкции подшипниковых узлов. Материалы вкладышей. Условный расчет. Смазка. Муфты. Общие сведения, назначение и классификация [1, c.377-396; 2, c232-273].
3. ВИДЫ РАБОТ С РАСПРЕДЕЛЕНИЕМ ВРЕМЕНИ
Курс (семестры) | III |
Всего часов | 150 |
Аудиторные занятия | 20 ч |
Лекционные занятия | 8 ч |
Лабораторные занятия | 12 ч |
Контрольные работы (количество) | 3 |
Самостоятельная работа | 130 ч |
Зачеты (количество) | 1 |
Экзамены (количество) | 1 |
4. ПЕРЕЧЕНЬ ТЕМ ЛЕКЦИОННЫХ ЗАНЯТИЙ
Раздел 1. Основные виды механизмов. Структурный анализ и синтез механизмов – 2 ч.
Раздел 2. Основные понятия; метод сечений; центральное растяжение сжатие; сдвиг; прямой поперечный изгиб; кручение – 3 ч.
Раздел 3. Основы проектирования передач: зубчатых, червячных, ременных, цепных, фрикционных. Критерии работоспособности – 3 ч.
ПЕРЕЧЕНЬ ТЕМ ДЛЯ САМОСТОЯТЕЛЬНОЙ ПРОРАБОТКИ СТУДЕНТОМ
Раздел 1
- Динамическая модель механизма.
- Линейные и нелинейные уравнения движения в механизмах. Трение в кинематических парах.
Раздел 2
- Обобщенный закон Гука. Понятие о статически неопреде
лимых задачах.
- Моменты инерции простых и сложных сечений. Главные
оси инерции и главные моменты инерции.
- Виды сложного сопротивления. Основные теории прочности. Косой изгиб. Внецентренное растяжение (сжатие).
Изгиб с кручением.
Раздел 3
- Соединения. Основные виды. Схемы нагружения и расчета.
- Валы. Основные типы валов. Расчетные схемы.
- Подшипники качения. Критерии работоспособности. Расчет (подбор) подшипников.
3.4. Муфта. Назначение. Конструкции. Расчет.
5. ЛАБОРАТОРНЫЕ ЗАНЯТИЯ
5.1 .Определение элементов и параметров эвольвентных цилиндрических колес — 2 ч.
5.2.Построение эвольвентных профилей зубьев цилиндрических зубчатых колес методом обкатки — 2 ч.
- Испытание стального стержня на растяжение — 2 ч.
- Испытание стального стержня на кручение — 2 ч.
- Определение напряжений и деформаций при изгибе — 2 ч.
- Зубчатый редуктор. Изучение конструкций — 2 ч.
6. СОДЕРЖАНИЕ КОНТРОЛЬНЫХ РАБОТ
Контрольная работа № 1
- Структурный и кинематический анализ рычажного механизма.
- Расчет и построение эвольвентного зацепления прямозубых цилиндрических колес.
Контрольная работа № 2
Расчет прямых стержней на растяжение (сжатие), кручение, изгиб и циклическую прочность.
Контрольная работа № 3
Расчет одноступенчатого редуктора общего назначения.
7. МЕТОДИЧЕСКИЕ УКАЗАНИЯ
Настоящие методические указания составлены в соответствии с программой, содержат обзор основных разделов курса и вводят в круг понятий, определений и терминологии, необходимых как при первом знакомстве с предметом, так и при его последующем углубленном изучении.
В них даны рекомендации по приемам и методам самостоятельного изучения теоретической части курса, а также выполнения контрольных и лабораторных работ, приведены контрольные вопросы для самопроверки.
К экзамену студент допускается после выполнения всех контрольных и лабораторных работ. Экзаменационный билет содержит обычно два вопроса по теории и одну типовую задачу.
7.1.ТЕОРИЯ МЕХАНИЗМОВ ИМАШИН
7.1.1. Общие сведения
"Теория механизмов и машин" является научно-теоретической основой механизации и автоматизации производства. Она тесно связана с математикой, физикой, теоретической механикой, техническим черчением. "Теория механизмов и машин" - наука, изучающая структуру, кинематику и динамику механизмов и машин. Её основные проблемы - исследование существующих механизмов (анализ) и проектирование новых по заданным условиям (синтез).
Одной из важнейших задач при изучении настоящего раздела является усвоение специальной терминологии, определений и основных положений. На их базе строятся все последующие исследования и выводы.
Прежде всего, надо знать, что называют механизмом и машиной.
Механизмом называют механическую систему тел, предназначенную для преобразования движения одного или нескольких из них в требуемое движение других тел. Комплекс механизмов, состоящий из двигателей, передач, рабочих органов и контрольно-регулирующих устройств, выполняющий работу по преобразованию энергии, материалов, информации или перемещению грузов, называют машиной.
По структурно-конструктивным признакам механизмы делятся на семь следующих видов: рычажные, зубчатые, винтовые, кулачковые, фрикционные, механизмы с гибкими связями и прочие, в том числе комбинированные.
В данном разделе прикладной механики основное внимание уделяется изучению рычажных и зубчатых механизмов.
7.1.2. Структура механизмов
В этой теме также вводится ряд понятий из классической теории механизмов и машин, которые следует запомнить.
Механизм и, следовательно, машину собирают из отдельных "частей" - деталей. Деталью называют изделие, изготовленное из монолитного материала без применения сборочных операций. Одна или несколько деталей, образующих жесткую систему тел, предназначенные для выполнения определенной функции в составе механизма, называют звеном. Звено может быть подвижным и неподвижным. Неподвижное звено называют стойкой.
Под кинематической парой понимают подвижное соединение двух звеньев, допускающее их относительное движение. Места контакта каждого из двух звеньев называют элементами кинематической пары. Элементы низших пар - поверхности, высших - линии или точки.
На относительное движение каждого звена элементы кинематической пары налагают ограничения, называемые связями. В зависимости от числа налагаемых связей кинематические пары разделяют на пять классов. Под кинематической цепью понимают связанную систему звеньев, образующих между собой кинематические пары. Цепи различают открытые и замкнутые, простые и сложные, плоские и пространственные.
Число степеней свободы плоских механизмов W определяют по формуле Чебышева (1869 г.): W = 3n - 2p5 - p4, где n - количество подвижных звеньев; p5 - количество кинематических пар 5 класса (низших пар) и p4 - количество кинематических пар 4 класса (высших пар).
Любой механизм имеет одно или несколько ведущих звеньев, количество которых соответствует значению W.
Ведущее звено, образующее со стойкой вращательную или поступательную кинематическую пару, относят к механизмам 1 класса. Более сложные механизмы можно получить, если последовательно присоединять к одному или нескольким ведущим звеньям и стойке так называемые структурные группы Ассура (1914) - такие кинематические цепи, которые получают нулевую подвижность после присоединения концевых пар к стойке. В состав этих групп входят только низшие кинематические пары. Структурные группы Ассура не изменяют числа степеней свободы механизмов. Их подразделяют на классы и порядки. Разложение кинематической цепи механизма на структурные группы называют структурным анализом. При структурном анализе определяют количество звеньев, количество и класс кинематических пар, число степеней свободы, класс и порядок структурных групп. По Артоболевскому (1905-1977 гг.) класс и порядок механизма соответствует наивысшему классу и порядку входящих в него структурных групп.
В процессе изучения материала по пособиям [1...6] следует научиться самостоятельно решать задачи по структурному анализу различных видов механизмов.
Вопросы
1. Что называют кинематической цепью, механизмом, деталью, звеном механизма?
2. По каким признакам классифицируют кинематические пары и цепи
- Что называют числом степеней свободы механизма и как его определить?
- Какие кинематические цепи называют структурными группами Ассура?
- Объясните принцип структурной классификации плоских механизмов по Артоболевскому.
- В какой последовательности выполняется структурный анализ механизмов?