Наносимые электрохимическими методами на поверхность детали в результате осаждения компонентов в виде ионов из электролита при пропускании электрического тока
Вид материала | Документы |
СодержаниеКатодными металлическими покрытиями Анодными металлическими Химическое никелирование |
- Электролиз введение, 421.2kb.
- Реферат по физике на тему: Дережинского Сергея «а» класс, 410.05kb.
- Тема «Электрический ток в металлах. Действия электрического тока.», 113.8kb.
- Peugeot/citroen (полный список) Группы и подгруппы компонентов, 1088.71kb.
- Программа курса лекций, 68.05kb.
- Стандартов безопасности труда, 50.74kb.
- Приказ от 20 г.№ Инструкция по оказание помощи пострадавшему от электрического тока, 32.86kb.
- Электроснабжения. Основные параметры, 59.82kb.
- «Резонанс в электрической цепи переменного тока» Урок физики в 11 классе с применением, 22.08kb.
- Определение ионов меди в природных водах Павловского района, 162.37kb.
«Покрытия для деталей машиностроения»
4. ЭЛЕКТРОХИМИЧЕСКИЕ И ХИМИЧЕСКИЕ ПОКРЫТИЯ
Электрохимическими называются покрытия, наносимые электрохимическими методами на поверхность детали в результате осаждения компонентов в виде ионов из электролита при пропускании электрического тока.
Химическими называются покрытия, наносимые химическими методами за счет восстановления металлов из растворов их соединений или осаждения их из газовой среды без подведения электрического тока от внешнего источника.
Толщина электрохимических покрытий в зависимости от предъявляемых к ним требований может изменяться в широких пределах (от долей микрона до десятых долей миллиметра). Толщина химических покрытий обычно не превышает 10 мкм.
Преимуществами указанных методов являются возможность получения покрытия без нагрева до высоких температур, из одного и того же метала с различной структурой и свойствами, возможность создания покрытий из сплавов металлов путем их совместного осаждения.
Рассматриваемые покрытия условно делят на три группы: защитные (используемые в целях защиты от коррозии), защитнодекоративные и специальные, придающие поверхностному слою детали требуемые свойства (твердость, износостойкость, паяемость и др.).
4.1. Электрохимические покрытия
Электрохимические металлические покрытия по механизму защиты подразделяются на катодные и анодные.
Катодными металлическими покрытиями называются такие покрытия, металл которых имеет более положительный электродный потенциал, чем защищаемый материал. Например, для деталей из углеродистой, низко- и среднелегированной стали в атмосферных условиях это - золото, серебро, медь, никель, хром, свинец.
Катодные покрытия защищают металл детали, изолируя его от окружающей среды. Основное требование к катодным покрытиям — беспористость. В местах несплошностей покрытия будет протекать коррозия с образованием продуктов коррозии, распространяясь под покрытием, что может привести к его отслаиванию.
Анодными металлическими покрытиями называются такие покрытия, металл которых в атмосферных условиях имеет более отрицательный электродный потенциал, чем защищаемый материал (например, цинк, кадмий, титан, алюминий и другие для углеродистой и среднелегированной стали).
Анодные покрытия защищают металл не только изолируя его от воздействия с внешней средой, но и электрохимически, за счет протекторного1 действия покрытия.
Общую схему нанесения электрохимических покрытий обычно рассматривают на примере цинкования. Цинковое покрытие является анодным. В кислый электролит 1 (раствор сернокислого цинка ZnSO4 погружают анодные пластинки из цинка, которые подключаются к положительному полюсу генератора 2 (рис. 9). Обрабатываемая деталь К (катод) погружается в электролит между анодными пластинами (А) и подключается к отрицательному полюсу электрической цепи.
Сернокислый цинк в электролите диссоциирует: ZnSO4 ↔ Zn+ + SO4−.
При этом катионы цинка начинают перемещаться к катоду, разряжаются (принимая на себя два избыточных электрона с катода) и цинк осаждается на поверхности детали. Анионы SО4− перемещаются к аноду (цинковым пластинам). Поэтому концентрация анионов SО4− и катионов Zn+ в растворе электролита поддерживается практически постоянной и процесс осаждения цинка на детали-катоде продолжается.
В процессе электролиза в электролите частично происходит диссоциация воды (Н2О ↔ Н+ + ОН−) и может иметь место нежелательное наводораживание покрываемого материала. Для устранения этого в электролит добавляют специальные вещества (Na2SO4, NaCl и др.).
Процессы цинкования осуществляются при температурах 15…40°С. Время процесса, в зависимости от толщины покрытия, составляет от одной минуты до двух и более часов.
Нанесение электрохимических покрытий на основе других металлов отличается от цинкования составом электролита, выбором металла анода и другими параметрами процесса. Общая схема аналогична цинкованию.
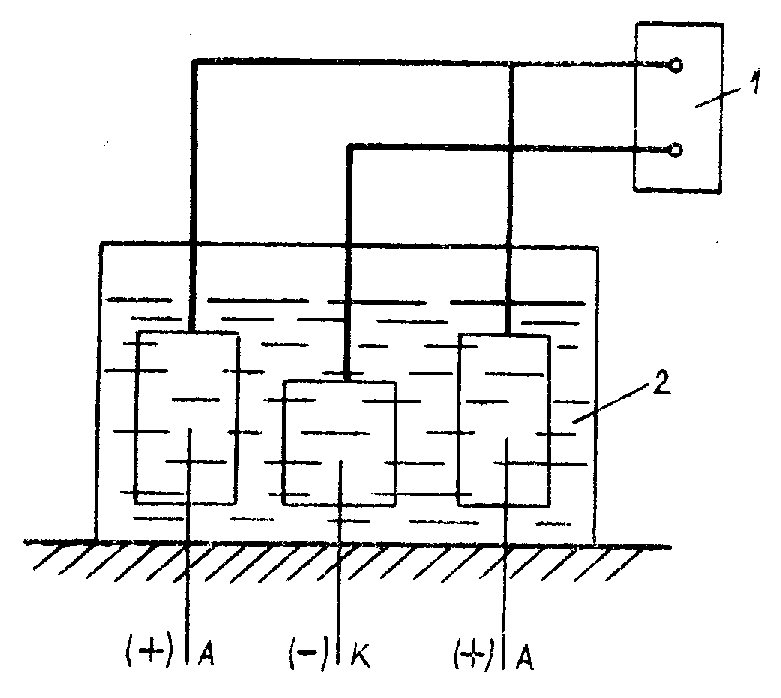
Рис. 9. Схема электрохимического процесса
нанесения металлических покрытий
Примером катодного покрытия по отношению к сплавам на железной основе (в условиях атмосферной коррозии) является хромирование. Процесс осаждения хрома производится при температурах 35…70 °С. Катодом является деталь (изделие). В качестве анода обычно применяют свинцовые пластины, которые не растворяются в применяемом для хромирования электролите состава: хромовый ангидрид (СrО3) и серная кислота (Н2SО4).
В результате хромирования могут быть получены покрытия, различающиеся по твердости и хрупкости, в зависимости от температуры и плотности тока. При этом различают мягкое покрытие (легко полируется и имеет наименьшую хрупкость), твердое (толщиной от 5 мкм до 1 мм, с сильно развитой сеткой трещин), а также наиболее твердое и хрупкое (с сильно развитой сеткой трещин, поэтому применяется ограниченно).
Технологический процесс нанесения всех электрохимических покрытий включает три основные стадии: подготовительные операции, нанесение покрытий и заключительные, отделочные операции.
Качество таких покрытий зависит от многих факторов, главные из которых качество подготовки поверхности детали под покрытие, состав электролита и режим электрохимического осаждения, форма детали и анода и другие.
Недостатком указанных покрытий является небольшая прочность их сцепления с основным металлом и резкий переход по составу в зоне соединения. Постепенного перехода по составу от металла покрытия к основному металлу можно добиться только путем специальной термообработки изделия совместно с покрытием. Можно также указать и на возможную неравномерность покрытия на деталях сложного профиля, трудности нанесения покрытия на детали из разнородных металлов.
К числу других способов нанесения электрохимических покрытий относится электронатирание. Этот способ также заключается в осаждении металла при пропускании тока между катодом (деталью) и анодом, к которому присоединяют мягкую «подушечку» или иглу, смоченные в соответствующем растворе, содержащем металл покрытия. При приложении напряжения (~6 В) «подушечку» перемещают по поверхности обрабатываемой детали (при периодическом обновлении раствора) до образования покрытия требуемой толщины. Таким образом, в частности, наносят покрытия на сталь и медные сплавы. В качестве металлов покрытий наиболее широко применяют никель, хром, олово, медь, цинк, кадмий, золото и серебро. Обычно используют растворы высокой концентрации, за исключением растворов для нанесения драгоценных металлов (в связи с их большой стоимостью) и случаев осаждения цинка и кадмия из цианидных растворов (поскольку при этом применяют растворимые аноды). Покрытия, нанесенные способом электронатирания, имеют матовую или слегка блестящую поверхность. Электронатирание используется, в основном, для нанесения покрытий на дорогостоящие агрегаты, разборка которых неосуществима
Или обходится слишком дорого, а также для восстановления изношенных участков покрытий.
Развитие электрохимического метода нанесения покрытий определяют композиционные электрохимические покрытия. Они отличаются от обычных гальванических тем, что содержат включения частиц другого вещества с размерами 0,1…10 мкм: оксидов, карбидов, органических полимеров, боридов, нитридов, алмаза, графита и других, обладающих высокой химической инертностью, твердостью и термостойкостью, смазывающими и другими характеристиками.
К числу перспективных относится и способ электрополимеризации, с применением которого можно покрыть поверхность металлических материалов тонким слоем пластмассы.
4.2. Химические покрытия
Химические покрытия создаются на основе металлов и неметаллов.
К химическим методам нанесения покрытий относятся: оксидирование, фосфатирование, пассивирование, никелирование, меднение и др.
В отличие от электрохимического химическим методом можно наносить равномерные по толщине покрытия на детали сложной формы с внутренними поверхностями.
Оксидированием называется процесс образования на поверхности детали оксидной пленки обрабатываемого материала. Химическое оксидирование связано с обработкой детали в растворах, содержащих окислители.
Оксидирование стали (называемое «воронением») ведется при температуре 135…145 °С в течение 1,5…2,5 ч в зависимости от состава стали. Детали погружают в горячий раствор, состоящий из едкой щелочи и окислителя - азотнокислого или азотистокислого натрия или обоих вместе. Толщина оксидной пленки не превышает 2 мкм, поэтому размеры деталей практически не увеличиваются.
Оксидная пленка имеет черный цвет с различными оттенками: синим, фиолетовым, коричневым в зависимости от химического состава стали. Поэтому оксидирование применяется в декоративных целях (для придания черного цвета оптическим приборам, резьбовым и крепежным деталям, пружинам и др.).
Химическому оксидированию подвергаются также детали из алюминия, цинка, магния, меди и их сплавов. При оксидировании алюминия чаще применяется электрохимический способ, называемый анодированием.
Фосфатированием называется процесс образования на поверхности металлических изделий мелкокристаллической пленки из нерастворимых в воде фосфорнокислых солей различных металлов (марганца, железа, цинка). Для фосфатирования применяют сложные растворы фосфатов марганца, железа и цинка, нитратов и других активных веществ. Наибольшее распространение получило горячее фосфатирование, при температурах 96…98 °С. Толщина фосфатных покрытий может составить от 1 до 14 мкм. Цвет покрытия - от серого до черного. Фосфатированию подвергаются стали, чугуны, цветные металлы и их сплавы. Фосфатирование в сочетании с последующим нанесением лакокрасочных покрытий, масла, воска или пластмассы применяют для защиты деталей от коррозии. Фосфатные покрытия используют также при холодной обработке давлением для повышения технологичности процесса.
Пассивированием называется процесс создания на поверхности детали тонкой защитной пленки. Пассивирование применяется как для защиты детали от коррозии, так и для повышения сопротивления коррозии других видов покрытий (цинковых, кадмиевых и др.). Пассивированию подвергают стали, латуни, алюминиевые сплавы и др. Разновидностью пассивирования является хроматирование - обработка деталей в водных растворах, содержащих соединения трех- и шестивалентного хрома, а также различные анионы и катионы (выполняющие специфические функции, например активирование поверхности металла, получение определенного окрашивания и др.).
Указанные виды химических неметаллических покрытий часто сочетаются в практике в одном или последовательных процессах, что обеспечивает получение более качественных покрытий. Например, после оксидирования может быть выполнено хроматирование.
Химическое никелирование применяется во многих отраслях машиностроения и приборостроения: для покрытия металлических изделий сложного профиля (с глубокими каналами и глухими отверстиями); для увеличения износостойкости трущихся поверхностей деталей машин; для повышения коррозионной стойкости в среде кипящей щелочи и перегретого пара; для замены хромового покрытия (с последующей термической обработкой химического никеля), чтобы использовать вместо коррозионно-стойкой стали более дешевую, покрытую химическим никелем; для никелирования крупногабаритной аппаратуры; для покрытия непроводящих материалов, пластмасс, стекла, керамики и т. п. Покрытия химического никеля, получаемые из кислых растворов, имеют гладкую блестящую поверхность, а из щелочных - менее блестящую.
Химически осажденный никель обладает более высокими защитными свойствами из-за меньшей пористости, чем электрохимически осажденный, а также потому, что осадки, содержащие в своем химическом составе фосфор, более стойки к агрессивным средам, чем чистый никель. Помимо фазы твердого раствора фосфора никель может содержать ряд химических соединений: Ni3Р, Ni5Р2 и Ni2Р. Химически восстановленный никель имеет аморфную структуру, а при нагревании аморфный осадок переходит в кристаллическое состояние. Прочность сцепления никель-фосфорного покрытия с основой непосредственно после осаждения невелика. При термообработке никелированных деталей повышается сцепление покрытия с основой вследствие диффузии никеля и фосфора в основной металл с образованием переходного диффузионного слоя.
Основной характеристикой, определяющей защитные свойства катодных покрытий, является их пористость. Установлено, что химические Ni-Р покрытия менее пористые, чем покрытия той же толщины, но полученные электрохимическим способом. По антифрикционным свойствам никель-фосфорные химические покрытия превышают хромовые. Химически восстановленный никель может быть использован для покрытия деталей, работающих на износ. По износостойкости никелевые покрытия сравнимы с хромовыми. При трении в паре с бронзой БрС-30 износостойкость покрытий почти вдвое выше, чем у закаленной стали. Химическому никелированию подвергаются сталь, медные, алюминиевые и магниевые сплавы, титан, цинк, сплавы типа инвар. С целью повышения прочности сцепления с основным металлом никелированные детали подвергают термической обработке.
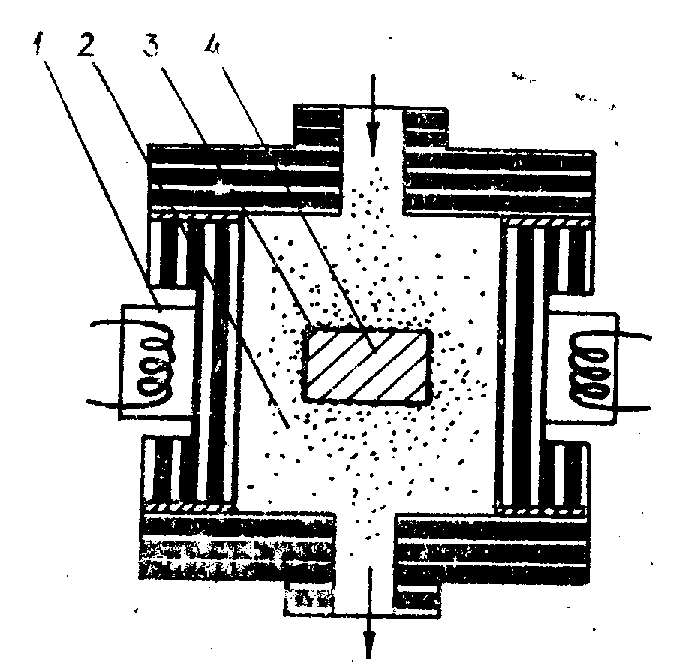
Рис. 10. Схема процесса термохимического осаждения карбида титана:
1 - нагреватель; 2 - зона реакции; 3 - термохимическое осаждение;
4 - покрываемая деталь
Химическим способом наносят покрытия также на основе металлов: меди, олова, хрома, свинца и др. Получили практическое применение химическое кобальтирование и осаждение некоторых драгоценных металлов (золочение, серебрение и т. п.). Защитной пленке оксидов обязана своей химической стойкостью и коррозионно-стойкая (нержавеющая) сталь.
Титанирование можно провести путем термохимического процесса (рис. 10). Газовую реакционную смесь (например, тетрахлорид титана и метан) подводят к предварительно на-гретой до 1000…1100 °С поверхности детали из сплавов железа. Газообразные реакционные компоненты связываются на поверхности детали. При этом одновременно протекают процессы диффузии и кристаллизации. Образующийся в результат е этих реакций защитный слой толщиной до 0,01 мм состоит из карбида титана, обладающего особенно высоким сопротивлением износу.
1 В гальванической паре защищаемым металлический материал в местах нарушения сплошности покрытия становится катодом и не разрушается до тех пор, пока весь металл покрытия не будет разрушен.
Сивенков А.В.