Анализ состояния 1 Стратегия развития редкометалльной отрасли в условиях глобализации минерально-сырьевого комплекса
Вид материала | Документы |
- Отчёт о научно-исследовательской работе по теме, 1297.9kb.
- Об утверждении Программы по развитию минерально-сырьевого комплекса в Республике Казахстан, 985.23kb.
- Дальневосточный федеральный округ объединяет 9 субъектов рф, занимает площадь 6,5 млн, 231.11kb.
- Стратегия развития росиии в условиях мировой глобализации, 39.95kb.
- Iii международная научно-практическая конференция молодых ученых и студентов «стратегия, 75.29kb.
- Концепция развития в условиях сельской школы. Стратегия и тактика перевода школы, 558.01kb.
- План развития отрасли (стратегия развития отрасли) цели, задачи и перспективы развития, 1546.26kb.
- Учебная программа " Энергоэффективность и энергосбережение на предприятиях минерально-сырьевого, 177.62kb.
- Проблемы экономической оценки минерально-сырьевого потенциала красноярского края, 19.62kb.
- Глобализация и ее влияние на банковскую систему России, 236.02kb.
Водоупорные
Фильтрующие
Расход водоносных горизонтов >фильтрационных потерь




Расход водоносных горизонтов ≈ фильтрационным потерям
Гидродинамические последствия



Проявление фильтрацион-ных потерь на поверхности
Изменение структуры потока незначительно
Формирование конусов репрессии






Гидрохимические загрязнения
Водоносных горизонтов в форме ореолов рассеяния
Водоносных горизонтов в форме объемов растекания
Поверхности земли и поверхностных вод




В УкрНИИЭП при участии Мариупольского металлургического комбината им Ильича проведены исследования, разработана и опробована в промышленных условиях на опытном заводе УкрНИИЭП малоотходная эколого-экономически елесообразная технология утилизации Zn, Pb и Fe из пылей и шламов газоочисток сталеплавильных и доменных производств ряда заводов черной металлургии России, Украины, Молдавии и Германии /1-3/.
Разработанная технология защищена патентами Украины. В стадии оформления находится российский патент.
При переработке 110 тыс.т/год исходного цинксодержащего шлама, содержащего 1-2,5% цинка обеспечиваются:
- получение 1-2,45 тыс. т/год дефицитного дорогостоящего высокосортного цинкового концентрата, используемого для получения металлического цинка и производства оцинкованного проката, и 107-108,5 тыс. т/год частично металлизованных железорудных окатышей, возвращаемых в агло-доменное производство поставщика исходного сырья;
- доходы от продажи цинкового концентрата ($640/т) и частично металлизованных окатышей ($20-25/т) - до $ 1,3 млн/год;
- решение крупных социально-экологических проблем: высвобождение земельных площадей, уменьшение степени загрязнения окружающей среды, создание новых рабочих мест, сокращение затрат предприятия на плату за размещение и хранение отходов, аренды земель, штрафов за превышение лимитов на образование и размещение отходов и др.;
Ориентировочная стоимость проекта ($ тыс.) до 740
в том числе:
- предпроектные и проектные работы 40
- закупка оборудования до 550
- строительно-монтажные работы 125
- пуско-наладочные работы с авторским надзором 25
Предполагаемые сроки реализации проекта (мес.)
- разработка проектной документации 6-9
- закупка и поставка оборудования 3
- монтаж оборудования, пуско-наладочные работы 4
- выход на проектную мощность 3
Установка комплектуется серийным отечественным оборудованием, надежна в эксплуатации, автоматизирована.
Окупаемость установки – до 2,5 лет после выхода на проектную мощность.
При наличии на предприятии пустующих зданий и простаивающего оборудования затраты могут быть значительно сокращены.
Расходные коэффициенты для установки производительностью 110 тыс. т/год по исходному сырью приведены в табл.2.
Принципиальная технологическая схема основных процессов приведена на рис.2, основные зависимости технологических параметров – на рис. 3, 4, экономические показатели – на рис.5,6.
Таблица 2.
Расходные коэффициенты установки
Наименование | Ед. измерения | Количество |
Фильтр-ткань | кв. м/год | 1600 |
Вода | куб. м/год | 1000 |
Природный газ | тыс. куб. м/год | 4000 |
Электроэнергия | тыс. кВтч/год | 4000 |
Особое внимание следует обратить на возможность экономически выгодного снабжения отечественной промышленности дорогостоящими и дефицитными соединениями Zn и Pb из техногенных месторождений этих элементов (шламонакопители) заводов черной металлургии.
Анализ спроса и мировых цен на Zn, Pb и их соединения показывает тенденцию постоянного устойчивого спроса и цен на них в размере 1-5 % в год.
Наиболее перспективным способом утилизации пылей и шламов является пирометаллургический с использованием одного из вариантов вельц-процесса или избирательной дистилляции Zn и Pb. В настоящее время углерод является единственным практически применяемым восстановителем оксида цинка.
Нами были проведены работы по оптимизации параметров процесса избирательной дистилляции цинка в условиях углетермического восстановления с
учетом которых разработан малоотходный способ извлечения Zn, Pb, Fe.. В качестве восстановителя использовали отсевы кокса (фракции - до 5 мм).
Во время исследования разработанной технологии твердые продукты анализировали на содержание Fe, Zn, Pb, Ca, Si, S, Cu и др. по стандартным методикам. Наибольшее содержание Zn (79%) отмечено в продукте, уловленном в зоне высокотемпературной возгонки вельц-печи, табл. 3.
Таблица 3
Химический состав цинкового концентрата по зонам вельц-печи
Место отбора проб | Состав цинкового концентрата (% масс.) | ||||||
Zn | PbO | Fe | Ca | Si | C1- | S | |
Зона возгонки (по длине) | 49,4 75,1 79,0 | 1,07 1,09 1,20 | 1,0 0,2 0,05 | 0,3 0,09 - | 1,14 - 0,5 | 0,18 - 0,23 | 0,2-0,3 0,2-0,3 0,2-0,3 |
Общий газоход | 60-65 | 8,7 | 1,7 | 0,5 | 0.9-1,1 | 0,1-0,2 | 0,2-0,3 |
Основную массу в полученном цинковом концентрате составляют высокодисперсные кристаллы оксида цинка (габитус частиц - шестигранные призмы).
Полученный цинковый концентрат по содержанию цинка на 10-17% превосходит отечественный концентрат марки КЦ-0, выпускавшийся заводом "Укрцинк" (в настоящее время ЗАО «Цинк»,Украина), и превышает лучшие мировые образцы (конкурентоспособен на внутреннем и внешнем рынках), табл. 4.
Частично металлизованные обесцинкованные окатыши имеют прочность до 40 кг/окатыш, содержат более 57% железа и могут служить сырьем в металлургическом производстве.
Разработанная технология является практически безотходной.
Полученные в ходе исследований данные использованы в качестве исходных при проектировании и испытаниях опытно-промышленной установки переработки пылей (шламов) газоочисток сталеплавильных производств разработанной безотходной технологии.
Таблица 4.
Сравнительный анализ цинкового концентрата (новая технология).
Сырье завода | Компоненты полученного концентрата, % масс. | ||||||||
Zn | PbО | Cu | Cd | S | Сd | Fe | Cl- | SiO2 | |
ММК им. Ильича, НЛМК | 68-79 | 4-7 | 0,4-0,8 | 0,25-0,5 | 2,2-3,2 | 0,04-0,07 | 1,5-3,5 | 0,01-0,2 | 2-3 |
Концентрат КЦ-0 стандартный | 61-62,5 | 1-2 | 0,4-0,8 | 0,3-0,65 | 2-3 | 0,02-0,06 | 1,2-3,4 | 0,02-0,2 | 2-2,5 |
Для обеспечения установки по переработке цинксодержащих шламов сырьем стабильного состава необходимы мероприятия по упорядочению процесса их складирования с исключением возможности совместного транспортирования и хранения данного вида сырья с отходами других производственных процессов.
Рис. 2. Технологическая схема процесса получения товарного цинкового концентрата из пылей (шламов)газоочисток металлургического производства.
И
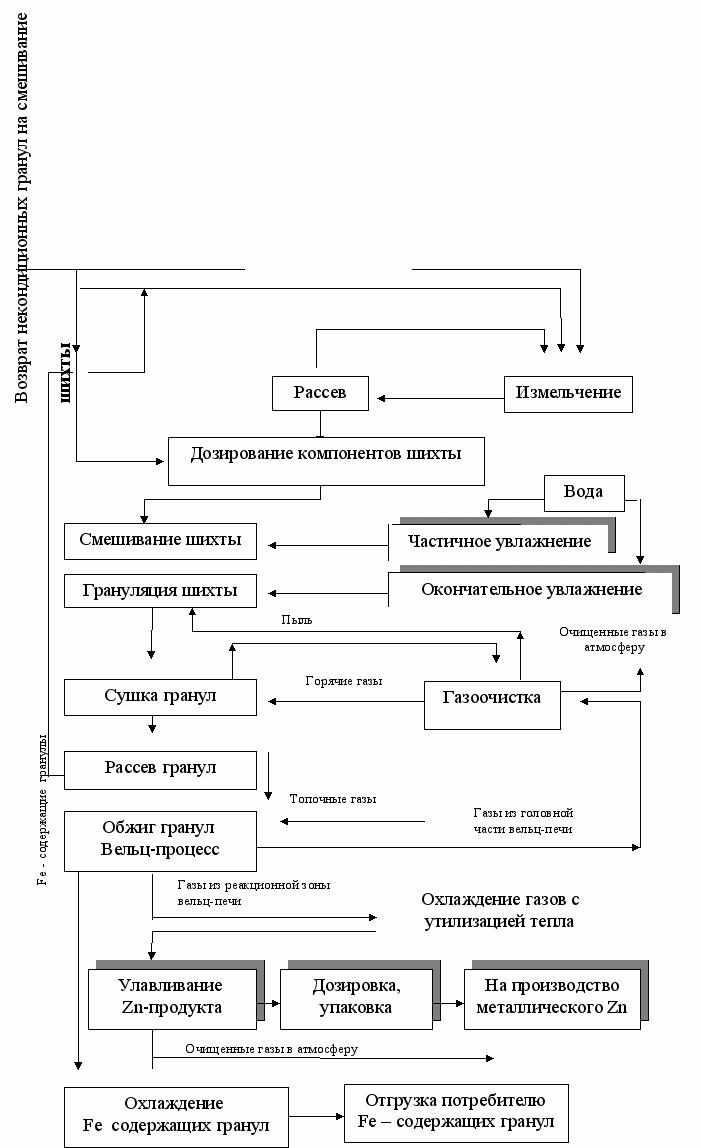
3.2 Технологическая и аппаратурно-технологическая схемы опытно-промышленной установки
Технологическая и аппаратурно-технологическая схемы процесса переработки шламов приведены на рис.2.11 и 2.12, соответственно.
Отделение приема и складирования исходного сырья (ОПСС). В зависимости от взаимного расположения шламонакопителя, участков складирования шламов и пылей газоочисток сталеплавильного и доменного производств, а также предполагаемых помещений опытно-промышленной установки по переработке цинксодержащих отходов доставку шламов и отсевов кокса в ОПСС осуществляют железнодорожным или автотранспортом (поз. 1). Операции перегрузки осуществляют с помощью грейферного крана (поз. 2) через закрома (поз. 22).
Складирование цинксодержащих шламов и углеродистого восстановителя -кокса, осуществляют в бетонные закрома (поз. 22) под железнодорожной эстакадой и далее грейферным краном - в приемные бункера (поз. 4, 3, соответственно). Разгрузка бункеров производится весовыми дозаторами (поз. 6,7) для передачи сырьевых материалов в отделение подготовки и грануляции шихты. Бункера снабжены вибраторами (поз 5). Передача сырья осуществляется по конвейерной галерее в отделение подготовки и грануляции шихты.
Разгрузка бункеров производится на ленточные желобчатые конвейеры (поз.8), подающие шламы и кокс в бункера-накопители (поз. 10) отделения подготовки и грануляции шихты (ОПГШ) и далее ленточными весовыми дозаторами (поз.11) и в размольно-смесительные бегуны (поз. 9) для размола компонентов до фракции 200-300 мкм и смешивания с исходным шламом.
Смешивание компонентов шихты в размольно-смесительных бегунах производят при массовом соотношении кокс: шлам =1:1 при общей производительности 2 т/ч для исключения возможности возгорания размалываемых отсевовкокса. Затем шихту направляют в двухвальный лопастной смеситель (поз. 12), где проводят окончательное смешивание компонентов с добавлением оставшегося цинксодержащего шлама через ленточный весовой дозатор (поз. 11) и частичное увлажнение шихты.
На всех предыдущих операциях возможна также пневмотранспортная подача материалов.
Все участки перегрузки компонентов шихты и их обработки должны быть снабжены аспирационными системами с общей или раздельной двухступенча1 той газоочисткой с тягодутьевыми устройствами, возвратом уловленной пыли и трубами выброса очищенного воздуха в атмосферу.
Полученная смесь поступает на тарельчатый гранулятор (поз. 13).
На тарель гранулятора в подобранные опытным путем точки распыляется вода для обеспечения влажности получающихся гранул в пределах 14 %. Оптимальный диаметр гранул — 2 - 8мм. Точки установки съемного ножа и подачи
распыляемой воды подбираются опытным путем.
Сформованные гранулы поступают в ленточную сушилку (поз. 14) для сушки при температуре 250-300°С в течение 1 часа с использованием тепла топочных газов выносной топки (поз. 15) и (или) физического тепла газов, отводимых от холодного конца обжиговой печи (поз. 17) до остаточной влажности
5-6% и далее на трехситный грохот (поз. 16) для выделения целевой фракции (2-
8мм).
Некондиционные гранулы других фракций возвращают на размалывание в бегуны (поз. 9) через бункера-накопители (поз. 3, 4) для подшихтовки исходной шихтовой смеси.
На всех участках приготовления, грануляции и сушки шихты устанавливают аспирационные и 2-хступенчатые газоочистные системы. Уловленную пыль возвращают на подшихтовку в бункер-накопитель (поз. 4).
Кондиционная фракция сухих гранул (2-8 мм) поступает в отделение обжига гранул и улавливания цинкового концентрата ЮОУК).
Отделение обжига гранул и улавливания цинкового концентрата. Вельцевание (обжиг) гранулированной шихты проводят для дистилляции цинка в противоточной вращающейся обжиговой вельц-печи при температуре в реакционной
зоне 950-1100°С в течение 1-2 часов с отводом пылегазовой смеси из холодного
конца обжиговой печи с использованием установки отбора цинкового концентрата. Атмосфера газовой фазы печи - слабо-окислительная.
- Из вельц-печи пылегазовая смесь поступает с использованием тягодутьевого агрегата через котел-утилизатор, в рукавный тканевый фильтр типа ФРИР при температуре до 138 °С. Для изготовления тканевых рукавов используют
ткани типа лавсан или оксалон с сопротивлением ткани 600-700 мм вод. столба.
В тканевом фильтре улавливается высокосортный цинковый концентрат, который затем поступает из бункеров фильтра в бункер-накопитель и далее черезвесовой дозатор в упаковочную машину для заполнения полиэтиленовых или краф г-мешков, а затем с помощью автопогрузчика - на склад готовой продук-ции. 1 (огрузочно-разгрузочные операции осуществляются тельфером г/п 1 т.
Очищенный от пыли газ удаляется в атмосферу через дымовую трубу, а уловленная пыль используется для подшихтовки компонентов шихты, поступающих на грануляцию. Тепловой баланс процессов сушки и обжига шихты проведен в приложении 12.
Контроль качества получаемого цинкового концентрата осуществляет ЦЗЛ комбината в соответствии с требованиями стандартов (ГОСТ, ТУ) и потребителя.
Обесцинкованные частично восстановленные железорудные окатыши (гранулы) из вельц-печи поступают в барабанный вращающийся или шахтный холодильник, расположенный под ней, охлаждаются до температуры 90-100°С, затем поступают через элеватор в бункер-накопитель, откуда лопастным питателем перегружаются в контейнеры или подаются на склад готовой продукции и далее транспортируются стороннему потребителю ж/д транспортом или в собственное аглодоменное производство основного предприятия.
Контроль качества обесцинкованных частично металлизованных железорудных окатышей (гранул) осуществляет ЦЗЛ комбината в соответствии с требованиями стандартов (ГОСТ, ТУ) и потребителя.
Все участки пересыпок и переработки продукции должны быть снабжены аспирационными системами с двухступенчатой газоочисткой. Избыточное тепло процессов сушки сырьевых материалов, сушки и обжига гранул используется в котле-утилизаторе с получением пара. В качестве топлива в тепловых агрегатах можно использовать природный, доменный, коксовый и другие горючие газы или их смеси с применением воздушного дутья. Вид используемого топлива устанавливает ОАО «ММК им. Ильича».
3.3 Опытно-промышленные испытания разработанной технологии на сырье ОАО «ММК им. Ильича»
Для испытаний использовали сухой шлам газоочисток доменного и сталеплавильного производств комбината и отсевы кокса, доставленные по договору с разработчиком на Харьковский опытный цементный завод в количестве около 6000 кт и 300 кг, соответственно.
Общий вид технологического оборудования, использованного при опытно-промышленных испытаниях технологии на Харьковском опытном цементном заводе приведен на рис. 2.13., 2.14.
Во время проведения испытаний были отработаны оптимальные парамет-
ры основных технологических процессов.
Исходные и конечные продукты анализировали на содержание Zn, Pb, Са, Si, S, Fe, С по стандартным методикам. Анализы проведены параллельно Исполнителем и независимым исследователем «Институтом монокристаллов» НАН Украины. Отходящие газы анализировали на содержание оксидов серы, азота, углерода, паров воды, по стандартным методикам. Результаты анализов приведены в таблицах 2.10, 2.11, 2.12, 2.13.
Результаты химического анализа проб Zn-содержащих шламов доменного и конвертерного производств приведены в таблицах 2.10, 2.11.
Таблица 2.10
Zn-содержащий шлам газоочисток доменного цеха
1 | Feo6m % | до спекания | после спекания |
47,5 | 55,6 | ||
2 | Fe2O3 % | 43,1 | 64,8 |
3 | FeO % | 8,3 | 0,35 |
4 | FeMeT % | 0,91 | - |
5 | Zn% | 0,86 | 0,08 |
6 | Cu% | 0,025 | 0,014 |
7 | Pb% | 0,049 | 0,011 |
Zn-содержащий шлам газоочисток ККЦ и МП
Таблица 2.11
| | до спекания | после спекания |
1 | Feo6lll % | 56,8 | 56,3 |
2 | Fe2O3 % | 45,2 | 65,8 • |
3 | FeO % | 40,8 | 0,35 |
4 | FeMeT % | 4,5 | - |
5 | Zn% | 0,79 | 0,075 |
6 | Cu% | 0,041 | 0,04 |
■7 | Pb% | 0,22 | 0,073 |