Десятые академические чтения раасн, 2006 г
Вид материала | Документы |
СодержаниеСПИСОК литературЫ Получение строительного гипса путем использования СПИСОК литературЫ Гибридные связующие нового поколения |
- Десятые академические чтения раасн, 2006, 1266.3kb.
- Десятые академические чтения раасн, 2006, 1519.63kb.
- Концепция устойчивого развития в стратегии градостроительства франции 05. 23. 22 Градостроительство,, 332.07kb.
- Резолюция районной детской экологической конференции Десятые Басарукинские чтения, 39.32kb.
- План организационно-педагогической деятельности с детьми, имеющими ярко-выраженные, 77.33kb.
- Новосибирский государственный педагогический университет, 43.06kb.
- Академические программы и экзаменационные курсы в австралии международные центры Embassy, 146.35kb.
- Экология человек общество, 371.15kb.
- Министерство образования и науки российской федерации московский государственный областной, 2810.15kb.
- Рассказывайте детям о ценности чтения. Показывайте связь чтения с их успехами в учебе, 97.26kb.
СПИСОК литературЫ
1. Баженов Ю. М. Строительные композиты гидратационного твердения // Вестник отделения строительных наук РААСН. – 1999. – № 2. – С. 27-31.
2. Рыбьев И. А. Строительное материаловедение. – М.: Высшая школа, 2002. – 700 с.
3. Баженов Ю. М. Многокомпонентные мелкозернистые бетоны // Строительные материалы, оборудование, технологии 21 в.. 2001. – № 10. – С. 24.
4. Каприелов С. С., Батраков В. Г., Шейнфельд А. В. Модифицированные бетоны нового поколения: реальность и перспектива // Бетон и железобетон. – 1999. – № 6. – С. 6-10.
5. Кинетическая модель процесса флоккуляции в маловязких дисперсных системах / А. П. Прошин, А. М. Данилов, Е. В. Королёв, В. А. Смирнов // Изв. ВУЗов. Строительство. – 2003. – № 4. – С. 53-57.
6. Батраков В. Г. Модифицированные бетоны. – М.: СИ, 1998. – 768 с.
7. Демьянова B. C., Калашников В. И. Быстротвердеющие высокопрочные бетоны с органоминеральными модификаторами. – Пенза: ПГУАС, 2003. – 195 с.
8. Баженов Ю. М. Технология бетона. – М.: Изд. АСВ, 2003. – 500 с.
УДК 666.914
Спасибухов Ю.Н., аспирант
Воронежский государственный архитектурно-строительный университет
ПОЛУЧЕНИЕ СТРОИТЕЛЬНОГО ГИПСА ПУТЕМ ИСПОЛЬЗОВАНИЯ
ТЕХНОГЕННЫХ ПРОДУКТОВ ОТ НЕЙТРАЛИЗАЦИИ СЕРНИСТЫХ ВЫБРОСОВ
ПРОМЫШЛЕННЫХ УСТАНОВОК
В настоящее время производство гипсовых вяжущих материалов осуществляется в основном за счет использования природного гипсового сырья. В то же время мощным потенциальным источником гипсового сырья являются попутные продукты таких отраслей промышленности, как энергетика, металлургия, химическая, пищевая, содержащие в своем составе сульфат кальция. В настоящее время насчитывается более 50 видов гипсосодержащих попутных продуктов и отходов. Их использование имеет не только экономическое, но и экологическое значение, так как шламонакопители отходов часто занимают плодородные земли, загрязняют грунтовые воды, а также являются источниками пыли и вредных выделений.
Наибольший интерес и для исследователей, и для практики, представляют технологии получения техногенного гипсового сырья из отходящих газов ряда промышленных установок, основанные на нейтрализации сернистого ангидрида (SO2) известняковыми суспензиями. Отходящие газы, содержащие SO2, получаются главным образом на предприятиях черной и цветной металлургии (выплавка меди, цинка, никеля и др.), на тепловых электрических станциях, работающих на каменном угле, мазуте.
Кафедрой технологии строительных изделий и конструкций Воронежского государственного архитектурно-строительного университета, совместно с ООО «Спецстрой-Холдинг», выполнены обширные исследования по улавливанию и нейтрализации сернистых выбросов, с переводом полученного продукта в строительный гипс.
В основе известнякового метода очистки газов от диоксида серы лежит процесс поглощения SO2 водой с последующей нейтрализацией образовавшейся сернистой кислоты известняком. По имеющимся данным /1/, в результате поглощения SO2 известняком образуется шлам, состоящий из полугидрата сульфита кальция CaSO3.0,5H2O(30…70%), часть которого (15…40%) в ходе процесса окисляется в дигидрат сульфата кальция CaSO4.2H2O; в шламе также содержится неиспользованный известняк CaCO3(30…60%) и разного рода примеси (до 10%). Такой состав шлама, практически не пригоден для получения строительного гипса. К тому же, процесс окисления идет очень медленно (порядка 60 часов). Между тем, из других источников/2,3/, нам стало известно, что процесс окисления CaSO3.0,5H2O можно значительно интенсифицировать. Установлено, что присутствие в растворе соединений ионов металлов переменной валентности: марганца, меди, железа и других, существенно увеличивает скорость реакции окисления CaSO3.0,5H2O.
Цель нашей работы состояла в том, чтобы, одновременно повышая эффективность очистки дымовых газов от SO2, оптимизировать процесс окисления CaSO3.0,5H2O, получить в качестве отходов сероулавливания преимущественно техногенное гипсовое сырье, пригодное для получения гипсового вяжущего. Отработать практические приемы перевода CaSO4.2H2O в строительный гипс, определить оптимальный состав водостойкого гипсового вяжущего специального назначения.
Для решения поставленных задач нами создана опытная полупромышленная установка, представленная на рисунке. Установка состоит из абсорбера с подвижной шаровой насадкой, сборников-нейтрализаторов, циркуляционного насоса и дымососа. Сущность эксперимента заключалась в моделировании двухступенчатой схемы очистки дымовых газов. Исследования проводили в абсорбере диаметром 0,225м, высотой 2м, с двумя слоями насадки из пластмассовых шаров диаметром 23мм, объемной плотностью 260кг/м3. Доля свободного сечения опорно-распредилительной решетки составляла 0,4, высота статического слоя насадки- 150мм.
В ходе эксперимента в абсорбере производительностью по газу 250м3/ч, подвергали очистке газ, полученный от сжигания сернистого угля и содержащий 0,1…0,3% об. SO2. Температура газа составляла 150…250 оС, скорость газа в абсорбере-2,0…2,5м/с. Орошение абсорбера производили по замкнутому циклу, поглотительной суспензией, содержащей 100г/л CaCO3. Для увеличения коэффициента использования известняка, водородный показатель суспензии первой ступени орошения поддерживали на уровне рН=6,0…6,5, второй ступени орошения - на уровне рН=4,5. Температура суспензии составляла 35…40 оС, плотность орошения - 12…30 м3/м2.ч. В качестве катализаторов использовались следующие неорганические соли: MnSO4, CuSO4, NiSO4, FeSO4. Концентрация катализаторов в орошающей суспензии изменялась от 0,5.10-3 до 2.10-3 моль/л.
В процессе проведения эксперимента, степень очистки дымовых газов от SO2 составляла 90…96%. Установлено, что каталитический эффект при окислении сульфита кальция в сульфат кальция проявляют все использовавшиеся в опытах неорганические соли в большей или меньшей степени. Удалось подобрать наиболее эффективный вид катализатора, и определить его оптимальную массовую составляющую, получить шлам, в основном состоящий из CaSO4.2H2O(60…85%).
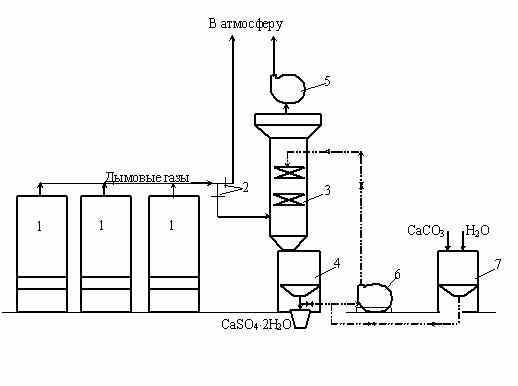
Рис. Схема опытной установки для нейтрализации сернистых выбросов.
Обозначено: 1 – угольные топки; 2 – шибер; 3 – абсорбер; 4 – сборник-нейтрализатор; 5 – дымосос; 6 – циркуляционный насос; 7 – бак суспензии.
Так, при использовании CuSO4 в качестве катализатора жидкофазного окисления, в процессе очистки дымового газа был получен шлам влажностью 60…80%, содержащий до 85% CaSO4.2H2O в твердой фазе. Согласно ГОСТ 4013-82 «Камень гипсовый и гипсоангидритовый для производства гипсовых вяжущих материалов», продукт сероочистки соответствует сырью 3,4 сорта.
Полученные партии гипсосодержащего шлама подвергали сушке до постоянной массы при температуре 50…60 оС. Высушенный материал представляет собой порошок желто-серого цвета. Плотность порошка в рыхлом состоянии 950…1050кг/м3, в уплотненном состоянии 1200…1300кг/м3, размер кристаллов двуводного гипса составляет 150…200мкм. Согласно результатам химического и рентгенофазового анализов (таблица 1), продукт сероочистки в основном состоит из CaSO4.2H2O (75…84%) и небольшого количества примесей.
Таблица 1
Химический состав шлама, образующегося при очистке дымовых газов от SO2 суспензией известняка.
Характеристика шлама | Содержание оксидов по результатам химического анализа, % | Минералогический состав шлама,% | |||||||||
CaO | SO3 | MgO | CO2 | Al2O3 Fe2O3 | SiO2 | H2O | CaSO4.2H2O | CaSO3.0,5H2O | CaCO3 | MgCO3 | |
Шлам, полученный при очистке дымовых газов от SO2 известняковыми суспензиями без использования катализаторов. | 43,89…44,09 | 25,18....31,42 | 0,17....0,18 | 17,45....23,68 | 0,7 | 0,5 | 5,67....7,07 | 18,02…39,39 | 21,13…27,09 | 39,18…53,31 | 0,36…0,38 |
Шлам, полученный при очистке дымовых газов от SO2 известняковыми суспензиями с использованием CuSO4 в качестве катализатора жидкофазного окисления. | 32,08....33,87 | 39,60....42,02 | 0,19....0,20 | 2,46....5,07 | 0,70....0,95 | 4,09....4,65 | 16,34....17,80 | 75,85…83,46 | 5,16…7,88 | 5,11…11,01 | 0,40…0,42 |
На основе трех партий техногенного гипсового сырья было получено гипсовое вяжущее β–модификации и водостойкое гипсоцементнозольное вяжущее. Дегидратацию техногенного гипсового сырья проводили в сушильном шкафу, при температуре 140…155оС, время дегидратации составляло 4,0…4,5 часа. Строительно-технические свойства строительного гипса приведены в таблице 2.
Полученный строительный гипс, портландцемент марки М500Д0 использовали для создания водостойкого гипсоцементнозольного вяжущего. В качестве активной минеральной добавки использовали золу гидроудаления Воронежской ТЭЦ №1. Выбор оптимального состава гипсоцементнозольного вяжущего проводили по методике разработанной в МГСУ им. Куйбышева /4/. Пользуясь этой методикой, по показаниям концентрации гидрооксида кальция в водных суспензиях сульфата кальция, портландцемента и золы, устанавливали необходимое количество золы и цемента. Золу вводили для связывания гидрооксида кальция и предотвращения образования разрушающего структуру цементного камня эттрингита. На основе полученных результатов был определен оптимальный состав гипсоцементнозольного вяжущего:
строительный гипс – 50%;
портландцемент М500Д0 – 19%;
зола Воронежской ТЭЦ №1 – 31%.
Строительно-технические свойства гипсоцементнозольного вяжущего приведены в таблице 2.
Таким образом, проведенные исследования показали возможность получения строительного гипса и водостойких вяжущих на основе техногенного гипсового сырья, с хорошими строительно-техническими свойствами.
Таблица 2
Строительно-технические свойства строительного гипса и водостойкого гипсоцементнозольного вяжущего.
№ п/п | Характеристика Вяжущего | Нормальная густота,% | Сроки схватывания, мин. | Водопоглощение по массе,% | Предел прочности при сжатии образцов кубиков 2х2х2см, мПа | Коэффициент размягчения | ||||
начало | конец | 2 часа | 1 сутки | 28 суток | При постоянной массе | |||||
1 | Партии полученного техногенного гипса β– модификации | 60 | 5 | 8 | 21,70 | 2,35 | - | - | 6,42 | 0,28 |
2 | 60 | 5 | 8 | 17,16 | 3,10 | - | - | 7,67 | 0,32 | |
3 | 65 | 5 | 8 | 19,70 | 2,29 | - | - | 6,50 | 0,29 | |
4 | Гипсоцементнозольное вяжущее | 53 | 5 | 10 | 15,12 | 2,80 | 6,88 | 13,20 | 16,30 | 0,66 |
Наиболее перспективные направления использования полученного строительного гипса в строительстве:
-производство внутренних гипсобетонных перегородок, декоративных и акустических гипсовых плит;
-производство поризованных блоков из пеногипса;
-производство шпатлевок, сухих смесей для отделочных, штукатурных, реставрационных, ремонтных работ.
Перспективные направления использования водостойкого гипсоцементнозольного вяжущего на основе строительного гипса:
-производство наружных ограждающих конструкций (камни, блоки, панели), внутренних перегородок, объемных элементов (санитарно-технические кабины, вентиляционные блоки, шахты лифтов);
-устройство стяжек и оснований наливных полов.
СПИСОК литературЫ
1. Крыленко В.И., Белоконь С.М., Потоцкий В.П. Влияние состава известняковой суспензии на эффективность очистки агломерационных газов от сернистого ангидрида./Химическая промышленность.-1973.-№11.-с.45-50.
2. Вилесов Н.Г. Очистка выбросных газов. - Киев, 1971.-197с.
3. Терни Т. Механизмы реакций окисления-восстановления. - М., 1968.-238с.
4. Гипсовые материалы и изделия (производство и применение). Справочник. Под общей ред. А.В. Ферронской.-М.:Издательство АСВ, 2004.-488с.
УДК 691.175-405.8
Старовойтова И.А., аспирант, Абдрахманова Л.А., д-р техн. наук, профессор,
Хозин В.Г., д-р техн. наук, профессор, Солдатов Д.А., канд.техн.наук, доцент
Казанский государственный архитектурно-строительный университет
ГИБРИДНЫЕ СВЯЗУЮЩИЕ НОВОГО ПОКОЛЕНИЯ
ДЛЯ ПОЛИМЕРНЫХ КОМПОЗИЦИОННЫХ МАТЕРИАЛОВ
Прогресс современного и будущего материаловедения безусловно базируется на совершенствовании композиционных материалов, основные синергические эффекты в которых связаны с взаимодействием на границе раздела фаз, появлением межфазных слоёв различной протяжённости и градиентом. В армированных, каркасных и матричных композитах, материалах типа взаимопроникающих структур наибольшие возможности позитивного изменения свойств заложены в модификации самих связующих.
Необходимость значительного улучшения технологических, физико-механических, теплофизических и других свойств полимерных композиционных материалов (ПКМ) требует качественно нового подхода к созданию связующих, образующих матрицу композита. Связующие нового поколения сами должны представлять собой ПКМ.
Связующие способны переходить из вязко-пластического состояния с хорошим смачиванием поверхности второго компонента, обеспечивающего переработку и формование систем в изделия, в твёрдую матрицу с комплексом заданных механических, теплофизических и физико-химических свойств, среди которых прочность и долговечность сыграют доминирующую роль. Эволюция развития связующих привела к тому, что они сами становятся композитами, с уменьшающимся масштабным уровнем гетерогенности, вплоть до наноуровня, когда понятие фазы теряет смысл (нанокомпозиты, нанотехнологии).
Как известно, наибольшие успехи в разработке и практическом применении композиционных материалов, связаны с органическими полимерными связующими и композитами. Относительно новым поколением этих связующих Ю.С.Липатов назвал гибридные [1] (по природе – полимер-полимерные). К ним он отнёс следующие их типы: 1).смеси двух или более линейных полимеров – термопластичные связующие или матрицы; 2).смеси линейных и сетчатых полимеров – так называемые полувзаимопроникающие полимерные сетки (полу-ВПС); 3).сетчатые полиблочные полимеры; 4).взаимопроникающие полимерные сетки (ВПС); 5).сегрегированные, или взаимосвязанные сетки.
Общим признаком таких систем является возникновение термодинамической несовместимости компонентов (в ходе их отверждения или протекания реакций поперечного сшивания и формирования фрагментов сетки), следствием которой является незавершённое микрофазовое разделение системы. В результате формируется сегрегированная структура с появлением у неё специфического комплекса свойств (наличие областей, различающихся по плотности, механическим свойствам, возникновение внутренних межфазных границ и пр.). Гибридная полимерная матрица, в которой произошло выделение микрообъёмов составляющих компонентов вследствие незавершённого микрофазового разделения, может рассматриваться как самоармированная (наполненная) дисперсно-упрочнённая система, в которой размер, свойства и распределение областей микрофазового разделения является функцией термодинамической несовместимости компонентов и определяется фазовой диаграммой.
Таким образом, по своей структуре гибридные матрицы действительно могут рассматриваться как самостоятельные ПКМ со всеми особенностями их физико-химического и механического поведения и определяющей ролью межфазных слоёв в свойствах самой матрицы (по аналогии с наполненными полимерами).
Однако, органические полимеры, в т.ч. и элементорганические, уступают неорганическим материалам по целому ряду технических свойств, в первую очередь, связанных с температурным воздействием. Полимерам свойственна горючесть, низкая тепло- и термостойкость, склонность к термодеструкции и атмосферному старению. Они имеют меньшие твёрдость и модуль упругости (кроме волокон), склонны к ползучести при статических нагрузках.
Поэтому ныне взоры многих исследователей обращены к получению «второго поколения» гибридных связующих и матриц – полимернеорганических композитов, в том числе и нанокомпозитов [3].
При этом особый интерес представляют полимер-неорганические нанокомпозиты, в которых эти компоненты (органические и неорганические) связаны сильными ковалентными или ионными химическими связями. Пока таких попыток известно немного, но возможности привлечения золь-гель-синтеза полимер-неорганических связующих, открывают, безусловно, новые перспективы для материаловедения и технологии получения композиционных материалов с заданными свойствами.
Безусловно, что к этим системам, образующимся из заведомо «чуждых» друг к другу по химической природе исходных реагирующих компонентов, применимы общие признаки термодинамической несовместимости полимер-полимерных гибридных связующих, которые имел в виду Липатов Ю.С.[1].
Достаточно часто на все процессы микросегрегирования в органо-неорганичеких отверждающихся связующих накладывается их химическое взаимодействие с появлением новых продуктов реакции. И, скорее всего, именно эта новая фаза с разной дисперсностью и структурным типом будет определять свойства образующегося гибридного материала.
Целью нашей работы является изучение гибридных связующих как самостоятельных материалов на основе органических и неорганических олигомеров. В качестве органических олигомеров в работе были использованы изоцианаты, а в качестве неорганических – силикаты и полисиликаты натрия. После этого станет возможным, зная требования, предъявляемые к конкретному композиционному материалу, создать матрицу с необходимым комплексом свойств. В ряде же случаев появится возможность использовать одно и то же связующее как основу для ряда материалов принципиально различного функционального назначения.
Получаемые и исследуемые нами гибридные связующие имеют ряд принципиальных отличий от связующих, для которых Липатов ввёл понятие гибридных. Во-первых, в области исследуемых составов и с учётом условий получения связующих термодинамическая несовместимость возникает уже на стадии смешения компонентов. Во-вторых, один из компонентов имеет органическую природу (полиизоцианат), а второй – неорганическую (силикат и полисиликат натрия). В-третьих, при получении связующих образуются химические связи (Si-O-C) между органической и неорганической составляющими связующего.
Композиции на основе изоцианатных компонентов и водных растворов силикатов щелочных металлов с точки зрения химии процессов изучались в ИХВС НАН Украины достаточно подробно [4,5]. Составы, полученные на основе жидкого стекла и изоцианатов могут быть классифицированы как полимерсиликатные, представляющие собой продукты с взаимопроникающими химически связанными матрицами (органической и неорганической). Данные электронной микроскопии свидетельствуют о том, что матрица дисперсионной среды имеет глобулярную структуру, содержащую в основном структурные элементы с двумя характерными размерами. Размеры этих структурных элементов составляют от 0,07 до 0,4 мкм в зависимости от содержания неорганического компонента в композиции. Таким образом, данные системы могут быть отнесены и к объектам нанотехнологии. В системах на основе жидких стёкол и изоцианатов протекает целый ряд химических реакций, в результате которых композиции содержат: дизамещённые мочевины, уретаноподобные продукты, изоцианураты, амины, поликремниевую кислоту и натриевые соли угольной и органических кислот. Степень протекания реакций и количество образующихся в результате веществ зависит от многих факторов, и, в первую очередь, от природы силиката и изоцианата.
В качестве неорганического компонента нами было выбрано натриевое жидкое стекло и полисиликаты натрия в связи с их доступностью, более низкой стоимостью и возможностью протекания в их присутствии тримеризации изоцианатов с образованием изоциануратов, обладающих повышенными прочностными характеристиками, тепло- и термостойкостью.
В качестве органического компонента в работе мы использовали полиизоцианат (ПИЦ) и дифенилметандиизоцианат (МДИ). Однако, для получения и изучения свойств связующего МДИ оказался непригодным, так как в связи с высокой активностью при его совмещении с силикатом натрия происходило достаточно быстрое вспучивание и отверждение композиции. В то же время для получения вспененных (теплоизоляционных) материалов МДИ в совокупности с силикатом натрия вполне пригодны.
В работе было установлено влияние модуля жидкого стекла и полисиликатов натрия на оптимальные соотношения компонентов и эксплуатационные свойства исследуемых композитов. Диапазон применяемых силикатных модулей составил 2,8-4,5. К жидким стёклам относятся компоненты с силикатным модулем (СМ) 2,8-4,0, а к полисиликатам – 4,0-4,5 [6].
За оптимальное соотношение компонентов принималось соотношение, при котором отверждённые композиции не имели градиента структуры по высоте образца (по данным оптической микроскопии). Косвенно это подтверждалось испытанием на твёрдость по Бринеллю, Шору и микротвёрдость на микротвердомере ПМТ-3. У образцов с оптимальным соотношением компонентов твёрдость и микротвёрдость практически не изменялись по высоте образца. Образцы для испытания на твёрдость и микротвёрдость представляли собой пластины диаметром 20 мм и толщиной 3 мм.
Установлено, что при изменении СМ от 2,8 до 4,5 оптимальное содержание силиката натрия в композиции снижается с 50-55% до 20-25%.
Для изучения влияния СМ на физико-механические и другие эксплуатационные свойства образцов отверждённых связующих сравнивались показатели образцов композиции при оптимальных соотношениях.
Повышение СМ приводит к росту модуля упругости композита, повышению водостойкости и термо- и теплостойкости. Однако, в то же время при увеличении СМ, хотя скорость достижения максимальной прочности на сжатие увеличивается, абсолютные её значения снижаются. Это вполне закономерно и связано с изменением соотношения разных продуктов реакций ПИЦ и жидкого стекла. Для композитов, включающих стёкла с более низким модулем характерна повышенная концентрация Na+, которая способствует образованию изоциануратных структур, характеризующихся повышенной прочностью по сравнению с полимочевинами и уретаноподобными продуктами, образующихся в большем количестве при использовании ЖС с большим СМ.
Таким образом, при изучении связующих на основе изоцианатов и силикатов натрия было установлено, что изменяя природу изоцианата и СМ силиката натрия можно получить разные материалы с эксплуатационными свойствами, изменяющимися в широких пределах.
Получаемые и исследуемые нами гибридные связующие оказались пригодными для ряда строительных материалов различного назначения:
1).Теплоизоляционные материалы, в том числе пенопласты;
2). Стекло- и базальтопластики;
3). Антикоррозионные покрытия.
Естественно, в зависимости от вида получаемого материала будет меняться как соотношение и природа компонентов связующего, так и перечень добавок, способствующих получению требуемого материала.
Возможность получения некоторых из перечисленных нами материалов подтверждена опытной проверкой.
На разработанном связующем с применением жидкого стекла с модулем 2,8-2,9 нами был получен модифицированный пенополиуретан (ППУ) [7-9], свойства которого представлены в таблице 1. Кроме компонентов гибридного связующего в состав композиции для получения ППУ вошли: простой олигоэфир, пеностабилизатор - смесь ОП-7 и ОП-10, а также специально подобранный смесевой катализатор.
Таблица 1
Свойства модифицированного ППУ
Содер-жание силиката натрия, масс.% | Крат-ность вспени-вания | Время вспенива-ния, с | Плот-ность, кг/м3 | Прочность на сжатие при 10%-ной дефо-рмации, МПа | Сорбционное увлажнение, % за 24 часа | Время самосто-ятельного горения, с |
0 | 12 | 40 | 90 | 0,38 | 1,8 | горит |
4 | 12 | 45 | 100 | 0,37 | 1,8 | 20 |
7 | 11 | 50 | 105 | 0,36 | 1,9 | 16 |
10 | 10,5 | 55 | 110 | 0,33 | 1,9 | 14 |
Разработанные связующие были использованы в качестве связующих для получения теплоизоляционных материалов с использованием волокнистых наполнителей (рубленая солома и древесная стружка) [10].
Время отверждения полученных теплоизоляционных материалов и основные эксплуатационные характеристики приведены в таблице 2.
Таблица 2
Время отверждения и основные эксплуатационные характеристики теплоизоляционных материалов на основе гибридных связующих и волокнистых наполнителей
| Эксплуатационные характеристики | |||||
Плотность, кг/м3 | Время отверждения при t=200С, мин | Прочность при 10% деформации, МПа | Тепплопро-водность, Вт/м.К | Водоп-поглощение за 30 сут, об.% | Горю-честь | |
Теплоизо-ляционный материал | 320-500 | 15 | 0,65-2,6 | 0,056-0,067 | 13,0-22,0 | ТГ |
Также разработанные связующие использовались нами для получения базальтопластиков, а именно базальтопластиковой арматуры (БПА), свойства которой, а также сравнительный анализ с промышленными аналогами представлен в таблице 3.
БПА на разработанном связующем имеет более высокие показатели по химстойкости, особенно в щелочной среде, и наибольшую степень сохранения прочности после выдержки в агрессивных средах.
Лучшие показатели при испытании на огнестойкость у БПА на гибридных связующих обусловлены их сравнительно высокой теплостойкостью (до 3000С), что связано со значительным содержанием неорганического компонента в составе связующего (теплостойкость применяемых в настоящее время для стекло- и базальтопластиков связующих составляет всего 100-1200С).
Таблица 3
Сравнительный анализ характеристик БПА на разработанном связующем с промышленными аналогами
Наименование показателя | Значение показателя для | ||
БПА на разрабо-танном связующем оптимального состава | БПА фирмы “Гален” (г.Чебо-ксары) | CПА завода стекло-пластиков (г.Бийск) | |
Плотность, кг/м3 | 2200 | 2040 | 2490 |
Изменение массы БПА (%) после кипячения в течение 3-х часов в средах: H2O 2н NaOH 2н HCl | 0,6 -2,3 -0,7 | 0,5 -14 0,52 | 0,5 -4 -0,4 |
Степень сохранения прочности (в % по отношению к исходной) после выдержки в агрессивных средах: H2O 2н NaOH 2н HCl | 112 81 88 | 54 35 38 | 51 16 68 |
Время начала горения при испытании на горючесть, сек | 15 | 8 | 15 |
Потеря массы при горении в течение 2 мин, % | 3 | 14 | 10 |