3 Допуски и посадки деталей машин и механизмов
Вид материала | Лекция |
СодержаниеПримеры применения посадок с натягом Система допусков и посадок для подшипников качения |
- Программа вступительного экзамена в аспирантуру по специальной дисциплине 05. 02., 266.3kb.
- Программа учебной дисциплины "Допуски, посадки и технические измерения " предназначена, 164.04kb.
- Лекции Лабораторные, 56.23kb.
- Допуски и посадки, 955.44kb.
- Является воздействие на потерпевших движущихся, разлетающихся, вращающихся предметов,, 56.73kb.
- Лекция 21 Точность обработки деталей Допуски и посадки, 160.03kb.
- Памятка для студентов группы пкм- по изучению дисциплины " Теория механизмов и машин, 72.92kb.
- Разработка и исследование аналитических моделей динамики механизмов с зазорами в сопряжениях, 718.37kb.
- Рабочей программы дисциплины Теория механизмов и машин по направлению подготовки 190600, 39.8kb.
- Программа дисциплины по кафедре Детали машин детали машин и механизмов, 575.22kb.
Тема 3 Допуски и посадки деталей машин и механизмов
Лекция 7 Выбор системы посадок, квалитетов и вида посадок
Примерные области применения некоторых рекомендуемых посадок с зазором (на примере посадок в системе отверстия). Посадки H/h (Smin = 0 и Smax = TD + Td) назначают преимущественно для пар с точным центрированием и направлением, в которых допускается проворачивание и продольное перемещение деталей при регулировке, а иногда и при работе.
Эти посадки можно использовать вместо переходных (в том числе для сменных частей). Для вращающихся деталей их применяют только при малых скоростях и нагрузках.
Посадка H6/h5 — для точного центрирования (например, пиноли в корпусе задней бабки токарного станка, измерительных зубчатых колес на Шпинделях зубоизмерительных приборов). Посадка H7/h6 (предпочтительная) — при менее жестких требованиях к точности центрирования (например, для сменных зубчатых колес в станках, корпусов под подшипники качения в станках, автомобилях и других машинах, поршня в пневмати- ческих инструментах, сменных кондукторных втулок и т. п.). Посадка H8/h7 (предпочтительная) — для центрирующих поверхностей в тех случаях, когда можно расширить допуски на изготовление при несколько пониженных требованиях к соосности.
ЕСДП СЭВ допускает применение посадок H/h 9-12-го квалитетов для соединений при низких требованиях к точности центрирования (например, для посадки шкивов, зубчатых колес, муфт и других деталей на вал с креплением шпонкой при передаче вращательного движения, при невысоких требованиях к точности механизма в целом и при небольших нагрузках).
Посадки H5/g4, H6/g5 и H7/g6 (предпочтительная) имеют самый наименьший гарантированный зазор из всех посадок с зазором. Они применяются для точных подвижных соединений, требующих гарантированного, но небольшого зазора для обеспечения точного центрирования (например, золотник в пневматической сверлильной машине, шпиндель в опорах делительной головки, в плунжерных парах и т. п.).
Из всех подвижных наиболее распространены посадки H7/f7 (предпочтительная), H8/f8 и другие им подобные 6, 8 и 9-го квалитетов. Например, посадку H7/f7 применяют в подшипниках скольжения малых и средних по мощности электродвигателей, поршневых компрессорах, в коробках скоростей станков, в центробежных насосах, в двигателях внутреннего сгорания и других машинах.
Посадки H7/e8 H8/e8 (предпочтительные), H7/e7 и другие им подобные 8 и 9-го квалитетов обеспечивают легкоподвижное соединение при жидкостном трении; их применяют для быстровращающихся валов больших машин. Например, первые две посадки применяют в турбогенераторах и электромоторах, работающих с большими нагрузками. Посадку H9/e9 применяют для крупных подшипников в тяжелом машиностроении, свободно вращающихся на валах зубчатых колес и других деталей, включаемых муфтами сцепления, для центрирования крышек цилиндров. Чтобы увеличить долговечность и надежность машин, эту посадку следует заменять аналогичной посадкой 8-го квалитета.
Посадки H8/d9, H9/d9 (предпочтительные) и другие им подобные 7, 10, 11-го квалитетов применяют сравнительно реже. Например, посадку H7/d8 применяют при больших скоростях вращения и относительно малых давлениях в крупных подшипниках, а также для сопряжений поршень - цилиндр в компрессорах, посадку H9/d9 — при невысокой точности механизмов.
Посадки H7/c8 и H8/c8 имеют большие гарантированные зазоры; их используют для соединений с невысокими требованиями к точности центрирования. Наиболее часто эти посадки используют в соединениях деталей (особенно с неодинаковым коэффициентом линейного расширения), работающих при повышенных рабочих температурах (паровые турбины, двигатели, турбокомпрессоры, турбовозы и другие машины, у которых в рабочем состоянии зазоры значительно уменьшаются). Уменьшение зазора в этом случае является следствием того, что вал нагревается и расширяется больше, чем вкладыш подшипника.
выбор переходных посадок. Переходные посадки H/Js, H/k, H/m, H/n используют в неподвижных разъемных соединениях для центрирования деталей, которые при необходимости могут сдвигаться вдоль вала или быть сменными. Эти посадки характеризуются малыми зазорами и натягами, что, как правило, позволяет собирать детали при небольших усилиях (вручную или с помощью молотка). Для гарантии неподвижности одной детали относительно другой их дополнительно крепят шпонками, стопорными винтами и другими крепежными средствами.
Сочетание высокой точности центрирования с относительной легкостью сборки и разборки соединения при постоянстве небольших усилий возможно лишь при небольших изменениях натяга и зазора. Вследствие этого переходные посадки предусмотрены только в 4 —8-м квалитетах. В них точность вала на один квалитет выше точности отверстия.
В переходных посадках при сочетании наибольшего предельного размера вала и наименьшего предельного размера отверстия всегда получается наибольший натяг, при сочетании наибольшего предельного размера отверстия и наименьшего предельного размера вала — наибольший зазо1
Выбор переходных посадок определяется требуемыми точностью центрирования и легкостью сборки и разборки соединения. Точность центрирования определяется величиной F радиального биения втулки на валу (или вала во втулке), возникающего при зазоре и одностороннем смещении вала в отверстии. Погрешности формы и расположения поверхностей сопрягаемых деталей, смятие неровностей, а также износ деталей при повторных сборках и разборках будут увеличивать радиальное биение.
Легкость сборки и разборки соединений с переходными посадками, так же как и характер этих посадок, определяется вероятностью получения в них зазоров и натягов.
выбор посадок с натягом. Посадки с натягом предназначены для получения неподвижных неразъемных соединений без дополнительного крепления деталей, хотя иногда и в этом случае используют шпоночные, штифтовые и другие средства крепления (например, маховика на коническом конце коленчатого вала двигателя). Относительная неподвижность деталей обеспечивается за счет сил сцепления (трения), возникающих на контактирующих поверхностях вследствие их деформации, создаваемой натягом при сборке соединения. Благодаря надежности и простоте конструкции деталей и сборки соединений эти посадки применяют во всех отраслях машиностроения (например, при сборке осей с колесами на железнодорожном транспорте, венцов со ступицами червячных колес, втулок с валами, составных коленчатых валов, вкладышей подшипников скольжения с корпусами и т.д.).
Примеры применения посадок с натягом (в порядке возрастания гарантированного натяга):
H7/p6 (предпочтительная) — для соединений тонкостенных деталей и при воздействии небольших нагрузок;
H7/r6 (предпочтительная) — для соединения кондукторных втулок с корпусом кондуктора; шатунных втулок с шатуном дизеля;
H7/s6 (предпочтительная) — для соединения центральной колонны крана с основанием;
H7/u6 —для соединения ступицы и венца червячного колеса; втулок подшипников скольжения в изделиях тяжелого машиностроения;
H8/x8, H8/z8 — имеют самые большие гарантированные натяги и применяются при больших нагрузках.
Выбор способа формирования соединения (под прессом с нагревом охватывающей или охлаждением охватываемой детали и др.) зависит от конструкций деталей и их размеров, величины требуемого натяга и т. д. Прочность соединений с натягом может быть повышена путем нанесения на детали гальванопокрытий, правильного выбора конструктивных форм деталей, стабилизации технологических факторов при сборке и др.
Надежность посадок с натягом зависит от механических свойств материалов соединяемых деталей, шероховатости и отклонений формы их поверхностей, конструктивных факторов, величины натяга, метода сборки соединения, условий эксплуатации и т. д. Многие из указанных факторов трудно нормализовать, и они не могут быть учтены при расчете, поэтому рекомендуется в ответственных случаях выбранную посадку проверять экспериментально. Посадка считается годной, если при наименьшем натяге гарантируется неподвижность соединения, а при наибольшем — прочность соединяемых деталей. При этих условиях соединение будет передавать заданный крутящий момент или осевую силу, а детали будут выдерживать без разрушения напряжения, вызванные натягом и другими факторами.
СИСТЕМА ДОПУСКОВ И ПОСАДОК ДЛЯ ПОДШИПНИКОВ КАЧЕНИЯ
Подшипники качения являются наиболее распространенными стандартными узлами, изготовляемыми на специализированных заводах. Они обладают полной внешней взаимозаменяемостью по присоединительным поверхностям, определяемым наружным диаметром D наружного и внутренним диаметром d внутреннего колец, и неполной внутренней взаимозаменяемостью между телами качения и кольцами. Вследствие малых допусков зазоров и малой допустимой разноразмерности комплекта шариков тела качения и кольца подшипников подбирают селективным методом. Полная взаимозаменяемость по присоединительным поверхностям позволяет быстро оптировать, а также заменять изношенные подшипники качения при сохранении хорошего качества узлов; при несоблюдении полной взаимозаменяемости качество подшипниковых узлов ухудшается.
Классы точности подшипников качения. Качество подшипников при прочих равных условиях определяется: 1) точностью присоединительных размеров d, D, ширины колец В, а для роликовых радиально-упорных подшипников еще и точностью монтажной высоты Т; точностью формы и взаимного расположения поверхностей колец подшипников и их шероховатостью; точностью формы и размеров тел качения в одном подшипнике и шероховатостью их поверхностей; 2) точностью вращения, характеризуемой радиальным и осевым биением дорожек качения и торцов колец.
В зависимости от указанных показателей точности по СТ СЭВ 774 — 77 установлено пять классов точности подшипников, обозначаемых (в порядке повышения точности) 0; 6; 5; 4; 2. Для иллюстрации различий в требованиях к точности радиальных и радиально-упорных подшипников d = 80-120 мм укажем, например, что допустимое радиальное биение дорожки качения внутренних колец 2-го класса и биение торца этих колец относительно отверстий в 10 раз меньше, чем для подшипников нулевого класса (соответственно 2,5 и 25 мкм). ГОСТ 520 — 71 регламентированы методы контроля точности отдельных колец и собранных подшипников, а также показатели величины обязательного ресурса, который у серийно выпускаемых подшипников подлежал периодической выборочной проверке изготовителем на стендах.
Класс точности подшипника выбирают исходя из требований, предъявляемых к точности вращения и условиям работы механизма. Для большинства механизмов общего назначения применяют подшипники класса точности О (нормального). Подшипники более высоких классов точности применяют при больших частотах вращения и в тех случаях, когда требуется высокая точность вращения вала (например, для шпинделей шлифованных и других прецизионных станков, для авиационных двигателей и приборов и т. п.). Класс точности указывается через тире перед условным обозначением подшипника; например, 6 — 205. Здесь цифра 6 — класс точности подшипника. Для гироскопических и других прецизионных приборов и машин используются подшипники класса 2 и точнее.
Допуски и посадки подшипников качения (по СТ СЭВ 774 — 77 «Подшипники качения. Технические требования»). Для сокращения номенклатуры подшипники изготовляют с отклонениями размеров внутреннего и наружного диаметров, не зависящими от посадки, по которой их будут Монтировать. Для всех классов верхнее отклонение присоединительных диаметров принято равным нулю. Таким образом, диаметры наружного Dm и внутреннего dn колец приняты соответственно за Диаметры основного вала и основного отверстия, а следовательно, посадки наружного кольца с корпусом осуществляют по системе вала, а посадки внутреннего кольца с валом — по системе отверстия. Однако поле допуска на диаметр отверстия внутреннего кольца расположено в «минус» от минимального размера, а не в «плюс», как у обычного основного отверстия т. е. не «в тело» кольца, а вниз от нулевой линии (рис, 8.13). '
При таком перевернутом расположении поля допуска отверстия внутреннего кольца для получения соединений колец с валами с небольшим натягом не нужно прибегать к специальным посадкам, а можно получать
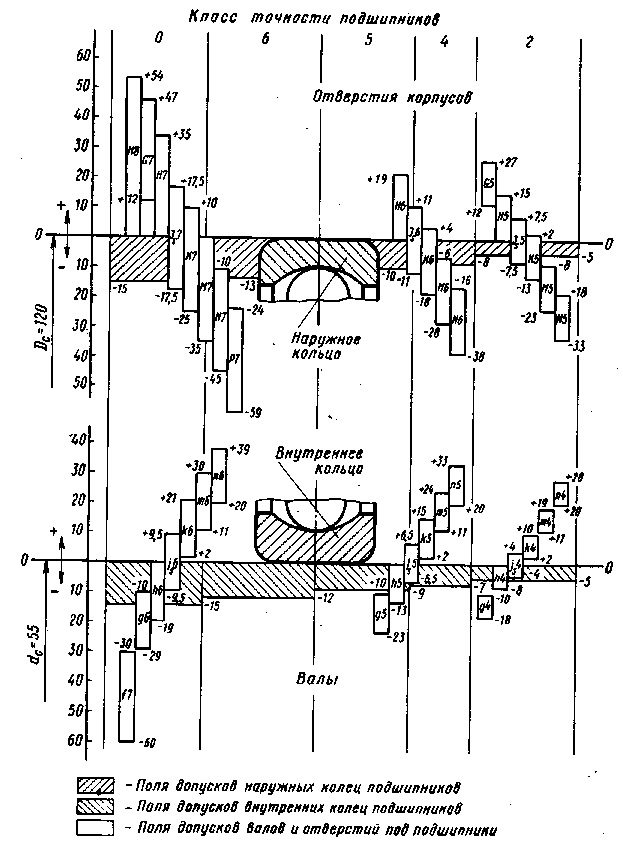
Рис. Схема расположения полдей допусков колец подшипников качения, валов и отверстий в корпусах (отклонения в мкм).
используя для валов поля допусков n6, m6, k6, js6или те же поля -го и 4-го квалитетов. Соединение вала, имеющего одно из указанных полей (кроме js6, js5 и js4), с внутренним кольцом подшипника даст посадку с небольшим гарантированным натягом. Посадки с большими натягами не применяют из-за тонкостенной конструкции колец подшипников и трудности получения в них требуемых рабочих зазоров.
Для обеспечения высокого качества подшипниковых узлов непостоянство диаметра (овальность) и средняя конусообразность отверстия и наружной цилиндрической поверхности колец шариковых и роликовых радиально-упорных подшипников 5 —2-го классов точности не должны быть более 50% допуска на Dm (dm). Допустимая овальность присоединительных (посадочных) поверхностей колец подшипника в свободном состоянии может быть больше 50% допуска на размер диаметра. Но при сборке подшипника и его монтаже кольца выправляются. Вследствие овальности, конусообразности и других отклонений при измерении могут быть получены различные значения диаметра колец подшипника в разных сечениях.