Физический факультет
Вид материала | Документы |
- Н. Г. Чернышевского Физический факультет утверждаю " " 20 г. Рабочая программа, 277.23kb.
- Инженерно- физический факультет высоких технологий Инженерно-физический факультет высоких, 561.11kb.
- Н. Г. Чернышевского Физический факультет утверждаю " " 2011 г. Рабочая программа, 125.38kb.
- Т. В. Лаптинская Физический факультет мгу им. М. В. Ломоносова Тема доклад, 6.35kb.
- Мордовский государственный университет. Физический факультет. Башлыков н. А. Материалы, 107.43kb.
- Программа курса занятий по подготовке менеджеров (авторская разработка Шатилло В. В.),, 26.19kb.
- А. А. Криволуцкий Центральная аэрологическая обсерватория, 620.15kb.
- И. Н. Карташов, М. В. Кузелев Физический факультет мгу им. М. В. Ломоносова, 11.5kb.
- Боровский Валитова Татьяна Александровна программа, 151.55kb.
- М. В. Ломоносова физический факультет кафедра физики элементарных частиц расписание, 41.66kb.
БЕЛОРУССКИЙ ГОСУДАРСТВЕННЫЙ УНИВЕРСИТЕТ
ФИЗИЧЕСКИЙ ФАКУЛЬТЕТ
КАФЕДРА ФИЗИКИ ТВЕРДОГО ТЕЛА
Методы получения защитных покрытий.
Работа студента 4-го курса
Эйзнера А.Б.
Минск 2002 г.
Оглавление.
1. Введение. 3
2. Методы химического осаждения покрытий. 3
2.1. Физические основы. 3
- Принципиальная схема установки и характеристики метода. 3
- Влияние режимов нанесения на структурные характеристики
покрытий. 4
3. Получение пленок распылением материала ионной бомбардировкой. 5
3.1. Физические основы. 5
3.2. Ионно-лучевое распыление. 6
3.2.1. Принципиальная схема установки и характеристики метода. 7
3.3.1. Влияние режимов нанесения на структурные характеристики
покрытий. 7
3.3. Ионно-плазменное распыление. 7
3.3.1. Катодное распыление. 7
3.3.1.1. Принципиальная схема установки и характеристики
метода. 7
3.3.1. Диодное распыление. 8
3.3.2. Магнетронное распыление. 8
3.3.3.1. Принципиальная схема установки и характеристики
метода 8
3.3.3.2. Влияние магнетронной системы на свойства покрытий. 10
4. Методы генерации потока, осажденного вещества термическим
испарением. 10
- Физические основы. 10
- Способы термического вакуумного напыления и их принципиальные схемы. 12
4.2.1. Резистивное испарение. 12
4.2.2. Электронно-лучевое испарение. 13
4.2.2.1. Схема установки. 13
4.2.2.2. Характеристики метода. 14
- Способы активации испаренных потоков вещества с помощью
электрического разряда. 14
4.2.3.1. Схема установки и характеристики метода. 14
- Влияние режимов нанесения на структурные
характеристики покрытий. 16
4.2.4. Способы испарения материалов в вакууме с помощью
электрического разряда. 16
4. Преимущества метода генерации потока частиц
термическим испарением. 18
5. Сравнительные характеристики различных методов получения тонких
пленок. 18
6. Список литературы. 19
1. Введение.
Процесс нанесения покрытия на поверхность режущего инструмента определяется как свойствами материала покрытия и инструмента, так и спецификой протекания процессов формирования покрытия. Исходя из выше сказанного, все методы нанесения покрытий можно разделить на две группы.
В первую группу входят методы химического осаждения покрытий из парогазовой фазы (ХОП). Вторая группа – это методы физического осаждения покрытий (ФОП). К этим методам относятся: метод получения тонких пленок распылением материалов ионной бомбардировкой (РИБ); метод генерации потока осаждаемого вещества термическим испарением (МТИ).
2. Методы химического осаждения покрытий (ХОП).
2.1. Физические основы.
Метод ХОП основан на гетерогенных химических реакциях в парогазовой среде, окружающих инструмент, в результате которых образуются покрытия. Исходными продуктами служат газообразные галогенойды, при взаимодействии которых с другими составляющими смесей (водородом, аммиаком, окисью углерода и т.д.) образуется покрытие. Разложение галогенойда происходит вследствие термической химической реакции (Т = 1000…1100 С)[6]. Уравнения химических реакций процессов ХОП с образованием карбидов, нитридов и оксидов в общем виде имеют следующий вид:
реакция образования карбидов
МеГ + Н2 + СnHm МеС + НГ + Н2; (1)
реакция образования нитридов
МеГ + Н2 + N2 MeN + HГ + Н2; (2)
реакция образования оксидов
МеГ + Н2 + СО2 МеОm + НГ + СО, (3)
где Ме – металл; Г – галоген; m,n – целые числа.
Для случая получения нитрида титана формула (2) приобретает вид
TiCl4 + N2 + 2H2 TiN + 4HCl; (4)
2.2. Принципиальная схема установки и характеристики метода.
Принципиальная схема установки представлена на рисунке 1[6].
Метод ХОП применяется при нанесении покрытий на основе карбидов, нитридов, карбонитридов титана, оксида алюминия. Он реализуется при температурах 1000-1100 оС, этот факт исключает возможность нанесения покрытий данным методом на инструменты из быстрорежущих сталей, которые были подвергнуты термической обработке. Средняя скорость роста толщины покрытия варьируется в пределах 10 – 15 мкм/ч. Толщины покрытий, наносимых данным методом, составляют порядка 10мкм.
Существует ряд недостатков метода ХОП:
- взрывоопасность и токсичность водорода, как газа-носителя
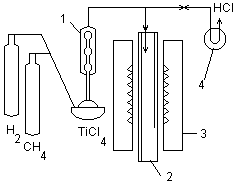
Рис. 1 Принципиальная схема установки для нанесения высокотемпературным методом ХОП:
1 – газосмеситель; 2 – реактор; 3- печь; 4 – устройство для удаления остатков реакции.
- наличие большего количества непрореагировавших компонентов
- сложность технологического оборудования
- внутреннее напряжение в слое покрытия
- невозможность нанесения покрытия на инструмент, имеющий острые режущие кромки
2.3. Влияние режимов нанесения на структурные характеристики
покрытий.
Качество, свойства и структура покрытия в значительной степени зависят от параметров газофазового осаждения. Наиболее существенную роль играет температура на границе раздела конденсата и инструментального материала. От температуры зависят структура покрытия, прочность его адгезии с твердым сплавом. Кроме того, взаимная диффузия повышает прочность сцепления покрытия и твердого сплава и, в свою очередь, зависит от кристаллохимического сродства осаждаемого покрытия и твердого сплава. Однако если на границе покрытие – твердый сплав за счет экстракции элемента из твердого сплава (углерод, кислород и др.) образуются устойчивые хрупкие соединения типа W3CO3C (-фаза), прочность сцепления покрытия и твердость сплава снижаются:
(x 1) Ti + x WC + y Co (x 2) TiC + W3CO3C. (5)
Рост -фазы происходит в основном в начальной стадии осаждения покрытия и заканчивается одновременно с завершением зародышеобразования, поэтому по мере уменьшения минимальной толщины покрытия, при которой образуется его полная сплошность , снижается и общая толщина -фазы.
Композиции твердый сплав – покрытие имеют низкопеременные значения остаточных напряжений в объеме покрытия. Наличие переходный зоны (-фазы) благоприятно сказывается на характере изменения остаточного напряжения на границе раздела твердый сплав – покрытие, так как снижается градиент напряжений и наблюдается достаточно плавный переход напряжения на границе.
На свойства и параметры покрытия (микротвердость, толщину, фазовый состав, структуру) оказывает влияние концентрация реагентов газовой смеси, давление смеси и скорость ее подачи, исходная чистота компонентов смеси. Особенно вредно присутствие вредных реагентов типа O2, H2O, N2, которые приводят к охрупчиванию покрытия, снижают прочности адгезии с твердым сплавом, резкому изменению физико-химических и теплофизических свойств покрытий. Поэтому к чистоте компонентов газовой смеси предъявляются повышенные требования [6].
- Получение тонких пленок распылением материалов ионной бомбардировкой (РИБ).
3.1. Физические основы.
Ионное распыление (ИР) – метод вакуумного напыления, в котором осаждаемый атомарный поток получают в результате бомбардировки ускоренными ионами поверхности исходного напыляемого материала и последующей инжекции распыленных атомов в паровую фазу.
Характер взаимодействия бомбардирующих ионов с поверхностью твердого тела определяется их энергией. При энергиях меньших 5 эВ, взаимодействие ограничивается физически и химически адсорбированными слоями, вызывая их десорбцию и обуславливая протекание различных химических реакций. При кинетических энергиях, превышающих энергию связи атомов в кристаллической решетке, бомбардировка вызывает разрушение приповерхностного слоя и выброс атомов в паровую фазу (распыление). Минимальная энергия ионов, приводящая к выбиванию атомов с поверхности, называется пороговой энергией распыления. Значение ее находится в интервале энергий от 15 до 30 эВ.
Характеристикой процесса ИР служит коэффициент распыления, определяемый количеством атомов, выбитых с бомбардируемой поверхности падающим ионом. При возрастании энергии бомбардирующих ионов свыше 100 эВ коэффициент распыления резко увеличивается и в области 5-10 кэВ выходит на насыщение. Дальнейшее повышение кинетической энергии свыше 100 кэВ приводит к снижению распыления, вызванному радиационными эффектами и внедрениями ионов в кристаллическую решетку. Диапазон энергий бомбардирующих ионов, представляющих интерес при получении покрытий, находится в пределах от 300 до 5000 эВ. Распыление вызывается, в основном, передачей импульса энергии от бомбардирующей частицы атомам кристаллической решетки в результате серии последовательных столкновений. Передача импульса от падающих ионов происходит в первых атомных слоях решетки, например, при бомбардировке поверхности поликристаллической меди ионами аргона с энергией 1000 эВ глубина проникновения равнялась трем атомным слоям.
Энергия распыления атомов значительно превышает кинетическую энергию испаренных атомов и составляет 0,1-100 эВ. Распыление сопровождается эмиссией вторичных электронов, которые ускоряются в электрическом поле, вызывая дополнительную ионизацию.
Коэффициент распыления определяется энергией и направлением падения ионов, природой взаимодействующих материалов, кристаллографической структурой и атомным строением бомбардируемой поверхности.
Наибольшее распространение в качестве источника бомбардирующих ионов получил инертный газ аргон, имеющий массу, достаточную для распыления, и характеризующийся относительно малой стоимостью.
Влияние температурных условий незначительно. Распыление металлов в твердом и расплавленном состояниях практически не различается. Исключение составляет область температур, при которых переход атомов в паровую фазу путем испарения становится существенным и превышает распыление. С увеличением угла падения ионов (относительно нормали к поверхности) эффективность распыления возрастает.
В установках ВН поток распыленных атомов создается либо в результате бомбардировки ионами плазмы разряда поверхности исходного напыляемого материала, находящегося под отрицательным потенциалом или являющегося катодом тлеющего разряда (ионно-плазменное распыление, разновидностями которого являются катодное, магнетронное распыления), либо за счет бомбардировки ускоренными ионами, эмитированных автономным источником (ионно-лучевое распыление). В зависимости от схемы распылительного устройства напыление при давлении остаточных газов от 10 до 10-2 Па [5].
3.2. Ионно-лучевое распыление.
3.2.1. Принципиальная схема установки и характеристики метода.
В данном методе для распыления используется пучок частиц высокой энергии. Для создания таких потоков частиц с контролируемой энергией разработаны системы ионных пушек (рис.2)[5].
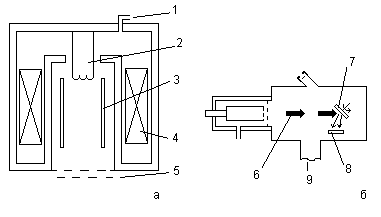
Рис. 2 Ионно-лучевое распыление:
1 – напуск рабочего газа; 2 – термоэлектронный катод; 3 – анод; 4 – магнитная
система; 5 – ускоряющий электрод; 6 – пучок ионов; 7 – распыляемый материал;
8 – подложкодержатель; 9 – присоединение к вакуумной системе; а – ионная
пушка; б – схема напыления.
Низковольтный разряд (40-80 В) возбуждается в среде аргона. Наличие термоэлектронного катода обеспечивает стабильность разряда в широком интервале давлений от 100 до 10-1 Па. Магнитное поле, создаваемое в области цилиндрического анода, изменяет траекторию электронов, увеличивая вероятность столкновения с молекулами газа. Система фокусировки и ускорения позволяет получать практически моноэнергетические пучки ионов с энергией от 100 до 3000 эВ и плотностью тока от 0,1 до 20 мА/см2. Есть сведенья о получении пучков аргона с плотностью тока до 26 мА/см2 при ускоряющем напряжении 1000 В. Получение пучков низкоэнергетических ионов с высокой плотностью тока ограничено. Для нейтрализации потока ионов, с целью распыления диэлектрических материалов, в пушку устанавливают источник низкоэнергетических электронов [5].
3.2.2. Влияние режимов нанесения на характеристики покрытий.
Покрытие TiCN было нанесено по средствам ионно-лучивого распыления. Период решетки данного покрытия зависит от соотношения между количеством азота и углеводородной смеси в реакционном газе. Из рис.3 видно, что период решетки максимален и равен 4.325 Å, когда реактивный газ содержит только углеводородную смесь, и минимальный период – 4.261 Å, когда реактивный газ содержит только азот [7].
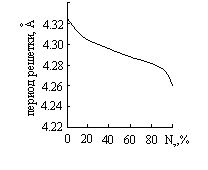
Рис. 3 Изменение периода решетки фазы TiCN в зависимости от объемной концентрации азота в реактивной газовой смеси в процессе конденсации.
3.3. Ионно-плазменное распыление.
3.3.1. Катодное распыление.
3.3.1.1. Принципиальная схема установки и характеристики метода.
Принципиальная схема установки приведена на рисунке 4 [4].
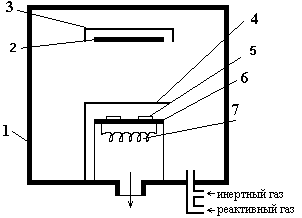
Рис.4 Схема установки для нанесения покрытий катодным распылением:
1 – камера; 2 – катод; 3 – заземленный экран; 4 – заслонка; 5 – подложка;
6 – заземленный анод; 7 – резистивный нагреватель подложки.
Метод осуществляется следующим образом. Вакуумный объем, содержащий анод и катод, откачивают до давления 10-4 Па, после чего производят напуск инертного газа (обычно это Ar при давлении 1-10 Па). Для зажигания тлеющего разряда между катодом и анодом подается высокое напряжение 1-10 кВ. Положительные ионы инертного газа, источником которого является плазма тлеющего разряда, ускоряются в электрическом поле и бомбардируют катод, вызывая его распыление. Распыленные атомы попадают на подложку и оседают в виде тонкой пленки [5].
Преимущества метода катодного распыления в следующем:
- безынерционность процесса
- низкие температуры процесса
- возможность получения пленок тугоплавких металлов и сплавов (в том числе и многокомпонентных)
- сохранение стехиометрического исходного материала при напылении
- возможность получения равномерных по толщине пленок
Метод имеет недостатки:
- низкая скорость осаждения (0.3-1 нм/с)
- загрязнение пленок рабочим газом вследствие проведения процесса при высоких давлениях
- низкая степень ионизации осаждаемого вещества
Данный метод может быть осуществлен и по другой схеме – диодная схема распыления.
3.3.2. Диодное распыление.
Диодная установка для напыления состоит из двух плоских электродов, расположенных параллельно и отстоящих друг от друга на расстоянии 5-15 см. Катод изготавливают из напыляемого материала. Он электрически изолирован и соединен с отрицательным полюсом высоковольтного выпрямителя. Анод, он же и подложкодержатель, обычно находится под потенциалом земли. Камера предварительно вакуумируется до 10-3 Па и на катод подается потенциал 3-5 кВ. При определенном напряжении, которое зависит от геометрии электродов, расстояния между ними и давления газа, происходит пробой и возбуждается в аргоне тлеющий разряд постоянного тока. Положительные ионы, ускоренные в прикатодной области, бомбардируют и распыляют поверхность катода напыляемого материала. Поток распыленных атомов осаждается на подложке в виде тонких пленок. Незначительные скорости осаждения (0,01 мкм/мин), обусловлены низкой плотностью ионного тока на катоде и невысокий вакуум ограничивают применение метода. Кроме того, эмитированные катодом и ускоренные в электрическом поле (2-5 кэВ) электроны интенсивно бомбардируют анод и размещенные на нем подложки, вызывая их перегрев и радиационные дефекты в структуре [5].
3.3.3. Магнетронное распыление.
3.3.3.1. Принципиальная схема установки и характеристики метода.
Схема магнетронной распылительной системы приведена на рисунке 9.
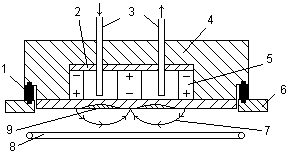
Рис. 5 Схема магнетронной системы ионного распыления с плоским катодом:
1 – изолятор; 2 – магнитопровод; 3 – система водоохлаждения; 4 – корпус
катодного узла; 5 – постоянный магнит; 6 – стенка вакуумной камеры;
7 – силовые линии магнитного поля; 8 – кольцевой водоохлаждаемый анод;
9 – зона эрозии распыляемого катода.
Основными элементами являются плоский катод, изготовленный из напыляемого материала, анод, устанавливаемый по периметру катода, магнитная система, обычно на основе постоянных магнитов, и система водоохлождения. Силовые линии магнитного поля, замыкаясь между полюсами, пересекаются с линиями электрического поля. Принцип действия установки основан на торможении электронов в скрещенных электроических и магнитных полях.
Известно, что на заряд, движущийся в электромагнитном поле, действует сила Лоренца, направление которой, по правилу сложения сил, зависит от направления ее составляющих. При этом, часть силы Лоренца, обусловленная действием магнитного поля, не совершает работы, а лишь искривляет траекторию движения частицы, заставляя ее двигаться по окружности в плоскости, перпендикулярной V и B.
Таким образом, в магнетронных устройствах при одновременном действии электрических и магнитных полей изменяется траектория движения электрона. Электроны, эмитированные катодом, и образующиеся в результате ионизации, под действием замкнутого магнитного поля локализуются непосредственно над поверхностью распыляемого материала. Они как бы попадают в ловушку, образуемую, с одной стороны, действием магнитного поля, заставляющего двигаться электроны по циклоидальной траектории вблизи поверхности, с другой – отталкиванием их электрическим полем катода в направлении к аноду. Вероятность и количество столкновения электронов с молекулами аргона и их ионизация резко возрастают. Из-за неоднородности действия электрических и магнитных полей в прикатодной зоне интенсивность ионизации в различных участках различна. Максимальное значение наблюдается в области, где линии индукции магнитного поля перпендикулярны вектору напряженности электрического поля, минимальное – где их направление совпадает.
Локализация плазмы в прикатодном пространстве позволила получить значительно большую плотность ионного тока при меньших рабочих давлениях, и, соответственно, обеспечить высокие скорости распыления.
Магнетронные устройства относятся к низковольтным системам ионного распыления. Напряжение источника питания постоянного тока не превышает 1000-1500 В. При подаче отрицательного потенциала на катод, между электродами возбуждается аномальный тлеющий разряд в среде аргона. Наличие магнитной ловушки обеспечивает при одних и тех же давлениях газа возникновение разряда при более низких напряжениях по сравнению с диодными системами. Напряжение разряда составляет 300-700 В.
Магнетрон может работать в диапазонах давления рабочего газа от 10-2 до 1 Па и выше. Давление газа и индукция магнитного поля оказывают значительные влияния на характеристики разряда. Понижение давления обуславливает повышение рабочих напряжений. В то же время для каждой магнетронной системы существует некоторый интервал значений, обычно 10-1 – 1 Па, в котором колебание давления не оказывает существенного влияния на изменение параметров разряда. Воздействие магнитного поля аналогично действию газовой среды. Поэтому низкие рабочие давления в магнетронах обеспечивают увеличение индукции магнитного поля, величина которой у поверхности катода составляет 0,03-0,1 Тл. Повышение удельной мощности способствует стабилизации разряда в области низких давлений [5].
Преимущества метода [4]:
- высокая скорость распыления при низких рабочих напряжениях (600-800 В) и при небольших давлениях рабочего газа (510-1 -10 Па)
- отсутствие перегрева подложки
- малая степень загрязнения пленок
- возможность получения равномерных по толщине пленок на большей площади подложек
3.3.3.2. Влияние магнетронной системы на свойства покрытий.
В зависимости от параметров процесса при магнетронном распылении покрытие TiNx (x меняется от 1 до 0.6) может иметь микротвердость от 1400 до 4000 кгс/мм2 (при температуре подложки 300-330 оС).
Зависимость микротвердости TiN от парциального давления азота имеет явно выраженный максимум (рис.6).
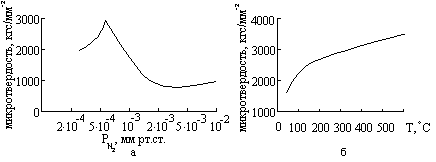
Рис. 6 Зависимость микротвердости покрытия TiN при магнетронном распылении от парциального давления азота (а) и температуры подложки (б).
На рис.7 показана зависимость микротвердости покрытий TiNx от расхода азота при магнетронном распылении, при величине полезной мощности равной 2 кВт [3].
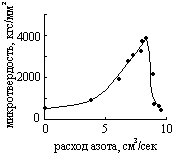
Рис.7 Зависимость микротвердости пленки TiNx от расхода азота.
4. Метод генерации потока осаждаемого вещества термическим испарением (МТИ).
4.1. Физические основы.
Метод МТИ заключен в нагреве исходных материалов с помощью какого-либо источника энергии (резистивный нагрев, электронный луч, электрический разряд и т.п.) до температуры испарения, испарения и конденсации паров на поверхности твердого тела в виде тонких пленок и покрытий.
В результате испарения или сублимации вещества переходят в паровую фазу. Пар, находящийся в термодинамическом равновесии с жидкостью или твердым телом, называется насыщенным. Испарение обусловлено тем, что кинетическая энергия молекул или атомов в поверхностном слое твердого тела или жидкости настолько превышает их среднюю в объеме при данной температуре, что они отрываются и распространяются в свободное пространство. Энергия атомов определяется температурой испарителя и составляет 0,1-0,3 эВ.
Движущей силой переноса частиц является различие давлений насыщенных паров над поверхностью испарения и вблизи поверхности конденсации. С повышением температуры нагрева испарение интенсифицируется. Зависимость давления насыщенных паров от температуры однокомпонентной системы выражается уравнением Клайперона-Клаузиса:
dP Hисп
= , (6)
dT T( Vп Vж)
где dP – изменение равновесного давления пара вследствие малого изменения температуры dT; Hисп – теплота испарения вещества; Vп, Vж – молярные объемы соответственно пара и жидкости.
Предполагая, что Vп Vж , и допуская, что пар подчиняется законам идеального газа, т.е. VпP = RT, уравнение (6) после соответствующих преобразований будет иметь вид:
lgP = Hисп/ RT + const , (7)
где R – универсальная газовая постоянная.
Уравнение (7) справедливо в узком интервале температур, так как не учитывает зависимости теплоты испарения от температуры. С учетом изменения теплофизических характеристик в справочниках приводится уравнение, позволяющее получить более точные значения давления для широкого интервала температур:
lgP = A/T + BlgT + CT + D. (8)
При одной и той же температуре различные металлы характеризуются различными значениями давления насыщенного пара, что значительно ограничивает применение МТИ при получении покрытий из сплавов.
Разработаны технологические приемы, обеспечивающие получение покрытий стехиометрического состава путем изменения исходного состава с целью компенсации разницы в упругостях пара, испарение дозированных количеств вещества, взрывообразное испарение и испарение из нескольких тиглей.
Упругость паров практически не зависит от давления окружающего газа. Оно определяет диффузию пара из пограничного слоя над испарителем и, соответственно, скорость испарения. При малых давлениях в камере (P 10-2 Па), когда средняя длинна свободного пробега молекул превышает ее характерные размеры, влиянием остаточного газа можно пренебречь и тогда, согласно кинетической теории газов и уравнению Герца-Кнудсена, скорость испарения по массе будет определяться с помощью уравнения Ленгмюра:
W = 7,78(M/T)1/2 P, (9)
где W – скорость испарения, гсм-2с-1; М – молярная масса вещества, г/моль; Т – температура испарения, К; Р – давление насыщенных паров, Па.
Давление остаточных газов в рабочем пространстве оказывает значительное влияние на характер распределения потоков атомов. Столкновение с молекулами газа изменяет их начальную энергию и траекторию. При молекулярном течении газа, когда столкновение между самими молекулами и атомами исключается, распределение испаренных атомов описывается законами Ламберта-Кнудсена.
Согласно первому закону, интенсивность потока пара в направлении , угла между нормалью к поверхности испарения и направлением испаренных атомов, пропорциональна косинусу этого угла. Преимущественное испарение происходит в направлениях, близких к нормали к испаряемой поверхности, т.е. там, где cos имеет наибольшую величину. Неравномерность распределения потока пара обуславливает в свою очередь неравномерность покрытия по толщине. Количество осаждаемого вещества обратно пропорционально квадрату расстояния от испарителя до поверхности напыления (второй закон).
Полученные зависимости для точечных испарителей могут быть использованы при оценке зон осаждений покрытий, равномерных по толщине. При этом реальные испарители рассматриваются как набор точечных. Расширение зон осаждения равномерных по толщине покрытий на практике достигается увеличением расстояния испаритель-подложка, применением большей поверхности испарителя и разработкой специальной внутрикамерной оснастки, обеспечивающей перемещение и вращение детали в процессе напыления [5].
4.2. Способы термического вакуумного напыления и их принципиальные схемы.
В зависимости от температуры испарения материал нагревают резистивным способом, воздействием высокочастотного электромагнитного поля, бомбардировкой ускоренными электронами, лучем лазера и с помощью электрического разряда.
4.2.1. Резистивное испарение.
Нагрев резистивным способом обеспечивается за счет тепла, выделяемого при прохождении электрического тока непосредственно через напыляемый материал или через испаритель, в котором он помещается. Конструктивно резистивные испарители подразделяются на проволочные, ленточные и тигельные. Первые изготавливают из проволоки тугоплавких металлов (вольфрам, молибден, ниобий) диаметром 0,5-1,5 мм путем придания ей формы, способом удержания металла в расплавленном состоянии. При изготовлении ленточных используют тонкие листы тугоплавких металлов толщиной 0,1-0,5 м, которых создают специальные углубления для размещения испаряемых металлов. Для испарения больших количеств материалов разработаны тигельные испарители. Тигель изготавливают из тугоплавких металлов, керамических материалов и графита. Материалы испарителя должны удовлетворять следующим требованиям:
- давление пара материала при температуре испарения должно быть пренебрежимо мало по сравнению с упругостью пара напыляемого вещества
- материал испарителя должен хороше смачиваться расплавленным напыляемым металлом с целью обеспечения хорошего теплового контакта и равномерного потока пара
- химическое взаимодействие между контактирующими материалами, обуславливающее загрязнение покрытий и разрушение испарителей, должно отсутствовать
Способ применяется при испарении материалов, температура нагрева которых не превышает 1500 С [5].
4.2.2. Электронно-лучевое испарение.
4.2.2.1. Принципиальная схема установки.
Принципиальная схема электронно-лучевого испарения в вакууме дана на рис.8.
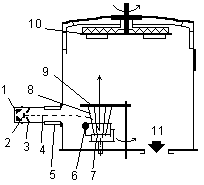
Рис. 8 Принципиальная схема применения электронно-лучевого нагрева при вакуумном напылении:
1 – прикатодный, формирующий электрод; 2 – термоэлектронный катод;
3 – анод; 4 – поток электронов; 5 – система магнитной фокусировки;
6 – узел электромагнитного пучка на 90; 7 – водоохлажденный тигель;
8 – поток пара; 9 – заслонка; 10 – подложкодержатель;
11 – система вакуумирования
Ускоренный пучок электронов с помощью отклоняющей системы непосредственно направляется на поверхность испаряемого материала. При столкновении с частицами окружающей среды электроны могут терять свою энергию и изменять направление движения. Число столкновений определяется концентрацией частиц, протяженностью электронного потока и его сечением. Для исключения газовыделений в процессе нагрева необходимо применять высокочистые исходные материалы.
Электронная пушка – устройство для создания, ускорения и фокусировки пучка электронов – состоит из катодного узла и системы фокусировки, обеспечивающей направленность потока (рис.9). Последняя, включает прикатодный фокусирующий электрод, ускоряющий анод и устройство магнитной фокусировки [5].
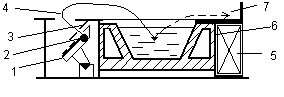
Рис.9 Схема плоско-лучевой электронной пушки:
1 – катодный узел; 2 – проволочный термоэлектронный катод; 3 – анод;
4 – ускоренный пучок электронов; 5 – устройство магнитного поворота
электронов; 6 – водоохлаждаемый медный тигель; 7 – охлаждаемая ловушка
для отраженных электронов.
4.2.2.2. Характеристики метода.
Метод осуществляется при величине остаточного давления в камере не превышающей 10-2 – 10-3 Па.
Степень объемного заряда в электронном пучке оценивается по средствам величины коэффициента пространственного заряда ( Р), определяемого уравнением:
P = I/ U 3/2. (10)
Если Р 10-8 А/В3/2 , то влияние пространственного заряда не учитывают. Это типично для пушек с током 10-3 А. Для мощных же генераторов электронов, с токами до 4 А и ускоряющими напряжениями 10-30 кэВ, формирование пучка в значительной мере определяется величиной объемного пространственного заряда.
В электронно-лучевых испарителях электроны ускоряются в электрическом поле до энергий 5-30 кэВ, и поэтому возможно возбуждение мягкого тормозного и характеристического рентгеновского излучения.
Анализ расходов энергии электронов показывает, что при удельной мощности 103-105 Вт/см2 30-40% расходуется на плавление и испарение (2-10% на испарение, 30-35% на плавление).Остальная мощность расходуется на теплообмен путем теплопроводности, излучения и уносится электронами, эмитируемыми из зоны нагрева. Последнее зависит как от испаряемого материала, так и от параметров электронного луча. При этом основная доля электронов уносится упруго и неупруго отраженными электронами, количество которых и энергия определяется, в первую очередь природой материала, и углом падения пучка и достигает, например, для стали 25%, для вольфрама 38% [5].
4.2.3. Способ активации испаряемых потоков веществ с помощью электрического разряда
4.2.3.1. Принципиальная схема установки и характеристики метода.
Принципиальная схема “ионного осаждения” представлена на рисунке 10.
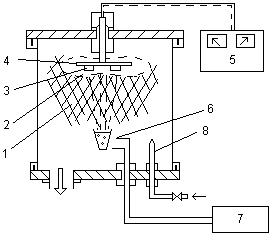
Рис. 10 Схема установки “ионного осаждения”:
1 – тлеющий разряд; 2 – катодная зона; 3 – подложки;
4 – подложкодержатель, отрицательное напряжение смещения 1-5 кВ;
5 – высоковольтный выпрямитель; 6 – тигель; 7 – испаритель;
8 – напуск аргона.
Анодом тлеющего разряда служит тигель с испаряемым материалом, который обычно находится под потенциалом земли. Процесс выполняется следующим образом. Камера предварительно вакуумируется до давления не выше 10-4 Па. При закрытой заслонке напыляемый материал расплавляется и производится его дегазация. Затем испаритель отключается, на подложку подается отрицательный потенциал смещения 2-5 кВ, и в камеру напускают рабочий газ аргон. При давлении 10-1-1 Па, в зависимости от геометрии устройства и межэлектродных расстояний, между подложкой и испаряемым материалом возбуждается тлеющий разряд. Поверхность подложки в результате бомбардировки ускоренными ионами и возбужденными атомами аргона распыляется. В некоторых случаях, с целью повышения эффективности удаления примесей, в состав аргона вводят химически активный газ, образующий с ними летучие соединения. Производится очистка поверхности подложки от оксидных соединений.
При достижении равновесного минимального тока на подложке, не отключая тлеющий разряд, начинается напыление. Испарение ведется в условиях тлеющего разряда. На поверхности подложки протекают два конкурирующих процесса: распыление и осаждение. На начальных стадиях, когда подложка находится под высоким потенциалом (3-5 кВ), скорость распыления выше. Затем потенциал уменьшается и идет осаждение покрытия при бомбардировке растущего слоя энергетическими частицами. Напыление возможно, как в тлеющем разряде, так и в отсутствии. В последнем случае напуск аргона прекращается, и процесс ведется аналогично классическому способу термовакуумного напыления. При напылении покрытий на диэлектрические материалы используют высокочастотный разряд, либо при разряде в постоянном токе вблизи них устанавливается сетка, изготавливаемая из напыляемого или другого инертного материала., на которую подается высокий отрицательный потенциал.
На начальных стадиях роста поверхность подложки и растущий слой подвергаются интенсивной бомбардировке ионами, ускоренными в темном катодном пространстве, и возбужденными частицами. Основной вклад при этом вносится возбужденными нейтральными частицами, составляющими 90% всей энергии потока. Энергия частиц колеблется от значений, определяемых ее температурой нагрева, до энергий ионов, ускоренных в поле подложки.
Воздействие энергетических частиц обуславливает десорбцию газов, распыление приповерхностного слоя, рост дефектов кристаллической решетки, изменение морфологии поверхности и структур роста тонких пленок и покрытий. Все это обуславливает напыление высокочастотных прочносцепленных покрытий. Кроме того покрытия, осажденные данным способом, характеризуются достаточно высокой равномерностью по толщине при напылении на поверхности со сложной геометрией [5].
4.2.3.2. Влияние режимов нанесения на структурные характеристики
покрытий.
Улучшая свойства покрытий, способ ионного осаждения сохраняет преимущества в условиях газового рассеяния; обеспечивает получение слоев, равномерных по толщине, на поверхностях сложной формы. На рисунке 11 приведены зависимости скоростей осаждения различных материалов на переднюю и обратную поверхность подложки от давления аргона.
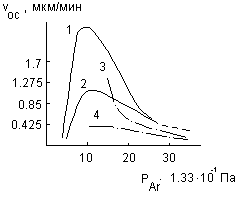
Рис. 11 Влияние давления аргона (РAr) на скорости “ионного осаждения” (Voc)
золота (сплошная линия) и коррозионностойкой стали (пунктирная линия)
на переднюю (1,3) и обратную (2,4) поверхности плоской подложки.
С повышением давления рабочих газов скорость напыления снижается, длинна свободного давления уменьшается, возрастает число столкновений, растет эффект рассеяния и при давлении 3,3-4,6 Па значения скорости осаждения на обеих поверхностях сравниваются. По аналогии с процессом испарения в газах это должно свойства покрытий из-за попадания газа и снижения энергии осаждающих атомов. При ионном осаждении это компенсируется высокой энергией потока пороговой смеси [5].
4.2.4. Способ испарения материалов в вакууме с помощью электрического разряда.
4.2.4.1. Принципиальная схема установки и характеристики метода.
В основу разрядного устройства была положена конструкция электронно-лучевой пушки с кольцевым термоэлектронным катодом – наличие электрического ускоряющего поля в зоне испарения и небольшое давление пара для возбуждения разряда (рис.12).
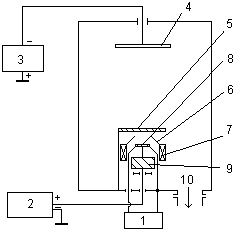
Рис. 12 Схема установки вакуумного напыления с применением разрядного испарителя анодной формы:
1 – источник накала катода; 2 – источник питания разряда; 3 – высоковольтный
выпрямитель; 4 – подложка; 5 – заслонка; 6 – система электростатической
фокусировки; 7 – магнит; 8 – термоэлектронный катод; 9 – тигель с испаряемым
материалом; 10 – система вакуумирования.
Под действием электрического поля ускоренный поток электронов бомбардирует поверхность исходного напыляемого металла, находящегося под потенциалом анода, обеспечивая нагрев его и испарение. С увеличением мощности давление паров в межэлектродном пространстве растет. Одновременно в результате столкновений с электронами происходит возбуждение и ионизация испаренных атомов. При некоторой скорости испарения, значение которой определяется природой напыляемого материала и конструктивными параметрами устройства, между катодом и анодом возбуждается разряд. Возникновение разряда сопровождается ярким свечением вытекающего потока пара с характерным цветом для каждого испаряемого металла. Разряд является несамостоятельным, так как термоэлектронная эмиссия катода достигается за счет накала его от дополнительного источника. Регулируемый ток термоэлектронов значительно облегчает управление процессом испарения. Устойчивость разряда и его параметры зависят как от физических условий горения, так и от характеристики источника питания.
При испарении металлов используют высоковольтный (напряжение 200-700 В, ток от 1 до 10 А) и низковольтный (напряжение 30-70 В, ток до 100 А) разряды. Степень ионизации осажденных атомов , в зависимости от режима разряда, в первом случае изменяется в интервале от 2 до 30%, во втором – приближается к 100%. Возбуждение низковольтного дугового разряда обеспечивается напуском аргона в пространство между электродами и начальным возникновением разряда в среде газа. По мере нагрева и испарения напыляемого материала натекание аргона постепенно перекрывается, и разряд горит только в парах металла. Вакуум при напылении с помощью разрядов анодной формы не хуже 10-3 Па.
Испарение металлов с помощью данного разряда обусловило значительное повышение энергии осажденных атомов и таким образом позволило активно влиять на процессы зарождения и роста покрытий. Поток пара, ускоренный в электрическом поле подложки, не только очищает ее поверхность, удаляя адсорбированные слои газа, но и изменяет кристаллографическую структуру приповерхностного слоя, производя его распыление. Стабильность разряда и возможности широкого и тонкого регулирования энергией и плотностью потока осаждающихся атомов позволяют использовать этот способ не только при получении металлических покрытий и покрытий из соединений, но и при диффузионном насыщении [5].
4.3. Преимущества метода генерации потока осаждаемого вещества термическим испарением.
Основные преимущества МТИ в следующем [4]:
- возможность нанесения пленок металлов (в том числе тугоплавких), сплавов, полупроводниковых соединений и диэлектрических пленок
- простота реализации
- высокая скорость испарения вещества и возможность регулирования ее в широких пределах за счет изменения подводимой к испарению мощности
- возможность получения покрытий, практически свободных от загрязнения
5. Сравнительные характеристики различных методов получения тонких пленок.
Характеристики покрытий зависят от метод их нанесения на рабочую поверхность (табл.1,2) [1].
Таблица 1
Твердость некоторых карбидовых покрытий, полученных различными способами.
-
Соединение
Метод
Микротвердость, кгс/мм 2
TiC
МТИ
2500-3000
3000-5500
РИБ
2400
ХОП
3350-3600
4500
Cr7C3
МТИ
2200
ХОП
1900-2200
Таблица 2
Твердость некоторых нитридных покрытий, полученных осаждением из паровой и газовой фазы.
-
Соединение
Метод
Микротвердость, кгс/мм2
TiN
МТИ
1900-2800
РИБ
1400-4000
1900
ХОП
1900-2400
CrN
РИБ
3500
- Список литературы.
- Волин Э.М. Ионно-плазменные методы получения износостойких покрытий (Обзор зарубежной литературы за 1979-1983 гг.) // Технология легких сплавов.№ 10.1984.
- Мацевитый В.М., Борушко М.С., Береснев В.М., Романова Л.М., Удовенко
Е.С. Структура и механические свойства вакуумно-плазменных покрытий
ТiCN // Известия высших учебных заведений. Черная металлургия.– № 3. –
1984.
- Заявка 20935 Англия. Механические свойства пленок нитрида титана.
Плазменное осаждение пленок нитрида титана / Мюзил Дж., Вискожид Дж.,
Баснер Р., Уэллер Ф. Опубл. 1985.
- Белый А.В., Карпенко Г.Д., Мышкин Н.К. Структура и методы формирования износостойких поверхностных слоев. – Москва: Машиностроение, 1991.
- Никитин М.М. Технология и оборудование вакуумного напыления. Москва: Металлургия, 1992.
- Верещака А.С. Работоспособность режущего инструмента с износостойкими покрытиям.Москва: Машмностроение,1993.
- Гнесин Г.Г., Фоменко С.Н. Износостойкие покрытия на инструментальных материалах (обзор) // Порошковая металлургия. – 1996. – № 9-10. С.1726.
- Житомерский В.И., Гримбегр И., Жозэф М.К. и др. Вакуумно-дуговое осаждение металл/керамических покрытий на полимерную одложку.// Поверхность и технология нанесения покрытий. 1998. № 108-109. – С. 160-165.
- Гримбегр И., Житомерский В.И. и др. Многокомпонентные покрытия (Ti,Zr)N и (Ti,Nb)N, нанесенные вакуумно-дуговым методом.// Поверхность и технология нанесения покрытий. 1998. № 108-109. – С. 154-159.
- Бохман Р.Л., Житомерский В.И., Гримбегр И. и др. Структура и твердость многослойных нитридных покрытий Ti, Zr и Nb осажденных вакуумно-дуговым методом.// Поверхность и технология нанесения покрытий. 2000. № 125. – С. 257-262.