Исследование гидрометаллургических процессов в многокомпонентных системах производства вторичных цветных металлов
Вид материала | Исследование |
Основное содержание диссертации опубликовано в работах, в том числе |
- Гост 1639-78: лом и отходы цветных металлов и сплавов общие технические условия, 1661.44kb.
- Разработка экологически чистых технологий комплексного извлечения благородных и цветных, 759.54kb.
- «производство отливок из сплавов цветных металлов», 38.25kb.
- Московский Государственный Институт Стали и Сплавов (Технологический Университет) Кафедра, 461.38kb.
- Темы рефератов по дисциплине «Материаловедение», 19.05kb.
- Исследование переходных процессов в замкнутых нелинейных системах управления 111, 347.96kb.
- Правительства Российской Федерации от 23 июля 2002 г. # 552 "Об утверждении Положения, 136.41kb.
- Извлечение цветных и редких металлов из отходов металлургического производства и нетрадиционных, 531.33kb.
- Гост 1639-93 Лом и отходы цветных металл. Общие технические условия, 1007.65kb.
- А. Б. Коростелев, А. В. Тарасов, Парецкий, 208.73kb.
а. Переплавку сырья осуществляют с целью усреднения состава получающегося сплава, для чего, разумеется, необходима предварительная черновая разборка поступающих ломов и отходов на виды (по содержанию меди и основных примесей) с целью наиболее рациональной шихтовки. В качестве плавильного агрегата может быть использована индукционная (тигельная или канальная) или другая электрическая печь. Добавка покровных флюсов – минимальная, обеспечивающая защиту зеркала ванны от окисления. Рационально использование современных поворотных анодных печей типа МЕРЦ, хорошо зарекомендовавших себя при переработке вторичного медного сырья. На переплавку также поступает анодный скрап после отмывки шлама и предварительной подсушки, а также цементный осадок операции электроцементации после отмывки конденсатной водой. Процесс ведут при температуре расплава 1420-1470 К, при необходимости, с перемешиванием ванны после загрузки инертным газом.
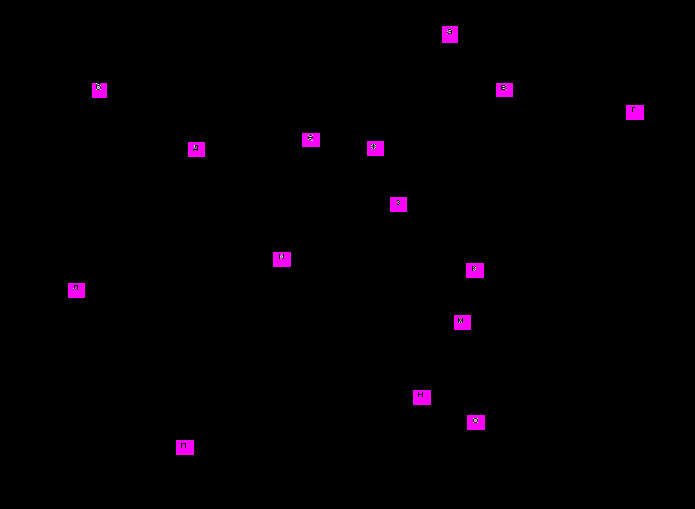
Рис. 13 Технологическая схема переработки низкокачественных вторичных медных сплавов
Около 15% от общей массы расплава подвергают воздушному распылению для последующего химического растворения, осуществляемого с целью нейтрализации серной кислоты, образующейся на стадии электроэкстракции меди (блок «ж» технологической схемы).
Цинксодержащие возгоны (35-40% Zn), образующиеся при переплавке сырья, направляют на операцию очистки цинкового электролита от железа и мышьяка (блок «к») после стадии анодного окисления железа.
б. Растворение гранул медных сплавов ведут в аппаратах перколяционного типа с чередованием продувки горячим (до 100оС) воздухом и прокачки кислых растворов. На выщелачивание подают отработанный электролит после электроэкстрации цинка (г/дм3: 20-25 Zn, 150-180 H2SO4), маточник после выпарки всех промвод (блок «п») технологической схемы (г/дм3: 10-20 Zn, 5-10 Cu); при необходимости объединенный раствор для выщелачивания подкрепляют концентрированной серной кислотой. Шлам после растворения гранул, содержащий, %: 8-10 Cu, 5-8 Zn, 22-25 Sn, 12-15 Pb, объединяют со шламом электролиза вторичных медных сплавов и после промывки (блок «д») направляют в специальную переработку, варианты которой описаны ниже.
В результате растворения гранул получают раствор, содержащий, г/дм3: 35-38 Cu, 20-25 Zn, 0,3-0,5 Ni, 8-12 H2SO4, который используют при электролизе анодов, полученных при переплавке исходного сырья.
в. Процесс электролиза проводят в ваннах ящичного типа, аналогичных по конструкции ваннам электрорафинирования меди, но с конусным днищем, необходимым для сбора и удаления накапливающегося анодного шлама. Средняя масса анода стандартной формы – 190 кг. Используют катодные матрицы из титана или нержавеющей стали. Катодная плотность тока 200-220 А/м2. Выход анодного шлама 9-12 %, катодный выход по току 93-95%.
Катоды после сдирки и отмывки (блок «г») являются товарной продукцией (качество катодной меди не хуже М1), а шлам после фильтрации направляют на отмывку совместно со шламом от растворения гранулированного сплава.
При накоплении примесей цинка (выше 60-70 г/дм3) и никеля (выше 20 г/дм3) часть электролита выводят из общей схемы циркуляции электролизных ванн на электроэкстракцию (блок «ж»), пополняя недостаток раствором с операции выщелачивания гранул (блок «б»). Анодный скрап (выход 15-18%) возвращают на переплавку.
г. Отмывку катодов проводят по стандартной схеме в воде и стабилизирующих растворах; промводы направляют на упаривание (блок «п»).
д. Шлам для промывки от остатков электролита репульпируют водой (Т:Ж=1:3), пульпу фильтруют, фильтрат направляют на выпарку, а кек влажностью 15-18% - на отдельную переработку.
е. Анодный скрап подвергают струйной отмывке водой, шлам направляют на фильтрацию (блок «д»), а отмытый скрап подсушивают и возвращают на переплавку (блок «а»).
ж. Электроэкстракцию меди проводят в ваннах с нерастворимыми анодами (Pb+1%Ag) до остаточной концентрации 2-4 г/дм3 Cu при катодной плотности тока 130-150 А/м2. Катодные листы после отмывки и сдирки с матриц являются конечной продукцией, а электролит (до 90 г/дм3 Zn, кислотность 25-30 г/дм3 H2SO4) поступает на операцию анодного окисления железа в многокамерный электролизер (блок «з»).
з. Многокамерный электролизер в предлагаемой технологической схеме выполняет две функции:
- в катодных камерах при прохождении раствора происходит электроцементационная очистка цинковых растворов от меди, кадмия и основного количества никеля; исходным электролитом в них служит раствор после фильтрации железо-мышьякового кека (блок «к»). Очищенный раствор после стадии контрольной цементации (блок «и») подают на электроэкстракцию цинка. Отфильтрованный и промытый (блок «л») цементный осадок возвращают на плавку в голову процесса.
- в анодной камере происходит количественное окисление железа до Fe(III) и удаление хлора, после чего полученный раствор подвергают гидролитической очистке от железа и мышьяка (блок «к») и направляют в катодные камеры того же электролизера на электроцементационную очистку.
и. Контрольную цементацию ведут с целью очистки цинковых растворов от остаточного количества примесей, что обусловливает минимальный расход цинкового порошка. Цементный осадок после фильтрации и промывки возвращают на плавку (блок «а»), очищенный раствор направляют на электроэкстракцию цинка (блок «н»), а промводы упаривают (блок «п»).
к. Очистку полученных после анодного окисления железа растворов ведут методом гидролитического осаждения при рН около 2,8-3, нейтрализуя избыточную кислоту цинковыми возгонами, образующимися при переплавке исходного сырья. После фильтрации пульпы железо-мышьяковый кек подлежит захоронению или может быть направлен в специальную переработку, а очищенный раствор подвергают электроцементационной очистке в катодной камере многокамерного электролизера (блок «з»).
л. Отмывку цементных осадков (как и все промывки кеков в технологической схеме) проводят конденсатом, полученным при выпарке промывных растворов (блок «п»). Цементную медь, содержащую 18-20% Zn и 0,5-0,8% Ni, позвращают на плавку в голову процесса.
м. Железо-мышьяковый кек промывают репульпацией при Т:Ж=1:3; промводы отправляют на выпарку (блок «п»).
н. Электроэкстракцию цинка проводят по известной технологии, используя применяемое на цинковых предприятиях оборудование [600]. Катоды после отмывки (блок «о») могут быть переплавлены в марочный чушковый металл. Отработанный электролит (г/дм3: 20-25 Zn, 150-180 H2SO4) направляют на выщелачивание гранул распыленного сплава (блок «б»). Показатели электроэкстракции цинка аналогичны получаемым на современных цинкэлектролитных заводах.
о. Отмывку и сдирку катодного цинка осуществляют также стандартными методами, промводы перекачивают на операцию выпарки (блок «п»).
п. Выпарку промвод проводят в вакуум-выпарных аппаратах, используя тепло, получаемое при переплавке исходного сырья. Конденсат используют на стадиях промывки кеков и цементных осадков, а маточный раствор направляют на стадию выщелачивания распыленного сплава.
ЗАКЛЮЧЕНИЕ
1. Гидрометаллургические процессы перспективны при переработке низкосортного полиметаллического вторичного сырья, которое не удается эффективно переработать классическими пирометаллургическими методами. Для обоснования нового экологически выдержанного гидрометаллургического производства актуальны исследования, направленные на интенсификацию операций выщелачивания, очистки растворов и выделения металлов. Разработаны научные основы альтернативных технологий извлечения меди, цинка, свинца, никеля и других ценных компонентов из многокомпонентных медных сплавов, полученных переплавкой лома и отходов сложного состава.
2. Комплексная переработка поликомпонентного вторичного медного сырья возможна при условии организации комбинированной технологии, основными элементами которой являются:
- восстановительная плавка вторсырья с получением минимального количества шлаков; разливка сплава в аноды;
- электролиз с селективным выделением олова и свинца в шлам, а цинка, никеля и железа - в раствор. Вывод основного количества меди из процесса в виде катодов;
- утилизация отработанного электролита по схеме:
- электроэкстракция меди до минимально возможной концентрации в электролите;
- химическое растворение распыленных сплавов для компенсации снижения концентрации меди и повышения кислотности электролита (с возвратом полученных растворов в голову процесса);
- гидролитическая очистка с получением кека, аккумулирующего железо;
- электроцементация с получением цементного осадка с высоким содержанием меди, никеля;
- получение сульфата цинка или электролита, пригодного для переработки на катодный цинк;
- утилизация твердых промпродуктов и сточных вод и организация замкнутого по технологическим растворам цикла.
Для формирования технологической схемы переработки сложного сырья разработаны единые теоретические основы химического и анодного растворения сплавов, очистки многокомпонентных растворов цементационными и гидролитическими методами, получения качественных продуктов, содержащих ценные компоненты.
3. Анализ фазовых диаграмм состояния гетерогенных металлических систем и микроструктурные исследования позволили прогнозировать анодный процесс с возможностью развития пассивации при растворении сплавов.
4. Установленные теоретические зависимости скорости растворения компонентов бинарных сплавов от температуры и интенсивности перемешивания характерны для протекания процесса в диффузионной области. Проведенные исследования позволили сформулировать особенности растворения бинарных сплавов на медной основе.
5. Установлено, что избирательное растворение электроположительного компонента в начальный период и непрерывная диффузия этого компонента через обедненный им слой в стационарных условиях приводит к тому, что атомы меди, находящиеся на поверхности сплава, характеризуются повышенной энергией. Их активность на границе раздела фаз становится больше единицы, т.е. выше активности не только меди в объеме сплава, но и чистого металла.
6. При анодном растворении гомогенных сплавов возникает поверхностный слой, т.е. метастабильная система, способная к дальнейшему самопроизвольному превращению в термодинамически устойчивую фазу. С увеличением доли электроотрицательного компонента до определенного предела склонность гомогенного сплава к селективному растворению изменяется незначительно, после чего следует ее быстрое возрастание.
7. Анодное растворение сплавов осложняется образованием нерастворимых пленок оксидов, гидроксидов, солей, которые тормозят процесс, причем механизм их образования и фазовый состав существенно отличается от шламовых фаз, полученных при химическом растворении. Интерпретированы процессы псевдоселективного растворения и растворения с фазовым превращением с единых кинетических позиций. Установлены условия протекания селективного растворения, определены основные параметры образования собственной фазы электрохимически положительного компонента.
8. Проведенные теоретические расчеты позволяют предсказать допустимые концентрации примесей в электролите при получении меди заданной чистоты для данных условий электролиза многокомпонентных растворов, подобрать оптимальные условия электролиза.
9. Установлено влияние условий электрохимического окисления и других факторов на состав и структуру гидролитических осадков железа, на скорость гидролитического осаждения Fe(III) из сульфатных медьсодержащих цинковых растворов, что позволило построить математическую модель и определить оптимальные условия процесса.
10. Показано, что при электроцементации образуются сплавы и твердые растворы; активность каждого из компонентов в твердой фазе определяется равновесным потенциалом реакции восстановления. Одновременно снижается энергия активации процесса разряда. Установлено, что твердые растворы, получаемые при совместной кристаллизации, в отдельных микрообъемах имеют неравновесный состав. Методом построения диаграмм E-pH в программной среде HSC 4.0, определены области существование соединений меди, никеля и цинка в зависимости от их концентраций в растворе. При анализе диаграмм установлен фазовый состав пассивирующих оксидных, гидроксидных и оксисульфатных пленок при подщелачивании прикатодного слоя. Рассчитано изменение активности ионов в электролите и спрогнозировано смещение равновесных потенциалов при образовании твердых растворов и интерметаллидов при катодном осаждении. Выведены уравнения, позволяющие определить потенциал ионизации образующейся твердой фазы при изменении условий электроцементационной очистки растворов. Установлено влияние состава раствора и других факторов на скорость протекания реакций электроосаждения и цементации.
11. Методами хроноамперометрии и обратного растворения фаз, образующихся при катодном осаждении, подтверждено предположение о фазовом составе осадков, механизме их образования и влиянии на механизм электроосаждения и кинетику реакции контактного вытеснения.
12. Разработанная технология основана на экологически выдержанных производственных операциях, использует современные энергетические источники, предполагае комплексное и селективное извлечение ценных компонентов и организацию замкнутых по растворам технологических циклов. Основные операции технологической схемы прошли опытно-промышленную проверку; подтверждена их экономическая эффективность.
Основное содержание диссертации опубликовано в работах, в том числе:
Отдельные издания:
- Процессы и аппараты цветной металлургии: Учебник для вузов / Набойченко С.С., Агеев Н.Г., Дорошкевич А.П., Жуков В.П., Елисеев Е.И., Карелов С.В., Мамяченков С.В. Екатеринбург, УрО РАН, 2005. 700 с.
- Набойченко С.С., Карелов С.В., Мамяченков С.В. Переработка медьсодержащих лома и отходов с комплексным извлечением цветных металлов. М., ЦНИИЦМЭИ, 1990. 27 с.
- Карелов С.В., Мамяченков С.В., Ранский О.Б. Переработка шлаков медеплавильного производства. М., ЦНИИЦМЭИ, 1994. 25 с.
- Карелов С.В., Мамяченков С.В., Набойченко С.С., Якорнов С.А., Усов С.П. Комплексная переработка цинк- и свинецсодержащих пылей предприятий цветной металлургии. М., ЦНИИЦМЭИ, 1996. 41 с.
5. Набойченко С.С., Мамяченков С.В., Карелов С.В. Мышьяк в цветной металлургии. Монография. Екатеринбург, УрО РАН, 2004. .240/100.
Статьи:
6. Худяков И.Ф.,Мамяченков С.В., Карелов С.В. К вопросу электрохимического разделения меди и олова из вторичных сплавов на медной основе // Цветные металлы. 1989, № 4, С. 44-47.
7. Заузолков И.В., Карелов С.В., Мамяченков С.В., Худяков И.Ф., Волкова Н.В., Артемьева А.Г. Анодное поведение сплавов на основе меди в сернокислых электролитах // Известия вузов. Цветная металлургия. 1989, № 6, С. 24-28.
8. Мамяченков С.В., Карелов С.В., Набойченко С.С. О макроструктуре катодных осадков при электрохимической переработке вторичных бронз // Известия вузов. Цветная металлургия. 1990, № 2, С. 69-74.
9. Пузаков В.В., Заузолков И.В., Щеглова Р.С., Кудряшов Ю.Е., Мамяченков С.В. Особенности электролитического рафинирования никельсодержащей меди // Известия ВУЗов. Цветная металлургия. 1990, № 2, С.120-122.
10. Набойченко С.С., Мамяченков С.В., Карелов С.В., Лаптев В.М., Артемьев Н.И. Переработка анодных шламов электролитического рафинирования вторичных бронз // Цветные металлы. 1992, № 2. С. 23-26.
11. Карелов С.В., Мамяченков С.В., Набойченко С.С., Артемьева А.Г. Испытания электрохимической технологии переработки вторичных бронз // Цветная металлургия. 1994, № 2, С. 22-24.
12. Карелов С.В., Мамяченков С.В., Набойченко С.С., Артющик В.А., Артющик Л.В. Комплексная переработка свинцово-оловянных кеков // Цветная металлургия. 1994, № 2, с. 17-20.
13. Карелов С.В., Мамяченков С.В., Набойченко С.С., Артемьева А.Г. Комплексная переработка анодных шламов электролиза вторичных бронз // Цветные металлы. 1994, № 7, с. 17-19.
14. Карелов С.В., Мамяченков С.В., Набойченко С.С. Электрохимическая технология переработки вторичных медных сплавов // Цветная металлургия. 1996, № 1, с. 17-21.
15. Карелов С.В., Набойченко С.С., Усов С.П., Мамяченков С.В. Электроцементационная очистка цинковых растворов // Цветная металлургия. 1996, № 7, с.23-25.
16. Naboichenko S.S., Karelov S.V., Mamyachenkov S.V., Yakornov S.A. Processing of lead cakes with recovery of commercial products / Modelling Advanced Process Technology, Expert and Control System of Heat and Mass Transfer Phenomena. Ekaterinburg: Ural State Technical University. 1996. Р. 71-73.
17. Naboichenko S.S., Karelov S.V., Usov S.P., Mamyachenkov S.V. Technological features of electrocementation cleaming zinc solutions / Modelling Advanced Process Technology, Expert and Control System of Heat and Mass Transfer Phenomena. Ekaterinburg: Ural State Technical University. 1996. p. 70-71.
18. Карелов С.В., Набойченко С.С., Мамяченков С.В., Стенина Л.Э., Брайнина Х.З. Использование диметилглиоксима для очистки цинковых растворов от никеля // Цветная металлургия. 1997, № 7, С. 35-37.
19. Набойченко С.С., Карелов С.В., Мамяченков С.В., Якорнов С.А. Комплексная переработка свинецсодержащих техногенных отходов медеплавильных предприятий Урала // Ивестия ВУЗов. Горный журнал, 1997, № 11-12, С. 252-257.
20. Карелов С.В., Набойченко С.С., Мамяченков С.В. Комплексная переработка вторичных медных сплавов гидроэлектрометаллургическим методом // Цветные металлы. 1997, № 5, С. 29-32.
21. Карелов С.В., Мамяченков С.В., Набойченко С.С. Анодная поляризация медных сплавов // Цветные металлы. 1997, № 9, С. 21-24.
22. Карелов С.В., Якорнов С.А., Мамяченков С.В., Набойченко С.С., Самойленко В.Н. Особенности анодного растворения олова, свинца и их сплавов // Цветная металлургия. 1998, № 2-3, С. 17-22.
23. Карелов С.В., Якорнов С.А., Мамяченков С.В., Набойченко С.С. Переработка свинцово-оловянных кеков медеплавильного производства // Цветная металлургия. 1998, № 2-3, С. 29-34.
24. Karelov S.V., Mamyachenkov S.V., Naboichenko S.S., Yakornov S.A., Goriaeva O.Yu., Verhaege M. Processing of Zinc and Lead bearing Dusts from Non-ferrous Metallurgical Plants in Russia / 4-th ASM International Conference and Exhibition on the Recycling of Metals 17-18 June 1999 The Forum Hotel Vienna, Vienna, Austria Book of Proceeding. Р.77.
25. Набойченко С.С., Карелов С.В., Захарова Е.А., Мамяченков С.В., Дедюхина Т.Л. Исследования по созданию экологически безопасной технологии в цветной металлургии / 4-th ASM International Conference and Exhibition on the Recycling of Metals 17-18 June 1999 The Forum Hotel Vienna, Vienna, Austria Book of Proceeding. Р. 176-188.
26. Карелов С.В., Мамяченков С.В., Набойченко Е.С., Захарова Е.А. Экологическая опасность медеплавильного производства на Среднем Урале // Вестник УГТУ-УПИ. Екатеринбург, 2000, № 1 (9), С. 50-53.
27. Выварец А.Д., Дистергефт Л.В., Карелов С.В., Мамяченков С.В., Набойченко Е.С. Экономическое стимулирование переработки техногенных образований // Цветные металлы, 2000, N 3, с.4-6.
28. Карелов С.В., Мамяченков С.В., Набойченко Е.С. Техногенные отходы медеплавильного производства и перспективы их переработки // Цветные металлы. № 9, 2000, С. 47-49.
29. Karelov S.V., Naboichenko E.S., Mamyachenkov S.V., Khilay V.V. Prospects of complex prosessing of lead-bearing semi-products of copper industry / Metallurgy of nonferrous and rare metals. Prosessing of Russian-Indian Symposium. Moscow. 2002. P. 56-60.
30. Карелов С.В., Выварец А.Д., Дистергефт Л.В., Мамяченков С.В., Хилай В.В., Набойченко Е.С. Оценка эколого-экономической эффективности переработки вторичного сырья и техногенных отходов // Известия вузов. Горный журнал. 2002. № 4. С. 94-104.
31. Карелов С.В., Мамяченков С.В., Хилай В.В., Кирпиков А.С., Анисимова О.С. Исследование анодной поляризации медных сплавов // Вестник УГТУ-УПИ, 2002, № 5(20). С. 117-121.
32. Хилай В.В., Карелов С.В., Мамяченков С.В., Кирпиков А.С. Способ расчета материальных балансов сложных технологических схем с учетом оборотных материалов // Известия вузов. Цветная металлургия, 2003, № 6, С. 78-80.3/1.
33. Карелов С.В., Мамяченков С.В., Кирпиков А.С., Анисимова О.С. Разработка технологии очистки оборотных и сточных вод металлургических предприятий от мышьяка // Записки горного института. С.-Петербург, 2003. Т. 154. С. 179-182 .
34. Мамяченков С.В., Анисимова О.С., Орлов Е.Г., Кирпиков А.С., Хилай В.В. Переработка мышьяксодержащих растворов отделения мокрой очистки газов сернокислотного производства // Известия вузов. Цветная металлургия, 2004, № 1, С. 11-15.
35. Карелов С.В., Выварец А.Д., Мамяченков С.В., Хилай В.В., Набойченко Е.С. Оценка эколого-экономической эффективности переработки вторичного сырья и техногенных отходов / Ресурсосберегающие технологии. Сб. М.: РАН, Министерство промышленности, науки и технологий РФ, Экспресс-информация. 2004. Вып. 8, С. 18-29 .
36. Карелов С.В., Мамяченков С.В., Анисимова О.С., Хилай В.В., Кирпиков А.С. Опытно-промышленные испытания технологии электроцементационной очистки сульфатных цинковых растворов // Цветные металлы. 2004, №2. С. 16-18.
37. Мамяченков С.В., Анисимова О.С., Орлов Е.Г., Кирпиков А.С., Хилай В.В. Переработка мышьяксодержащих растворов отделения мокрой очистки газов сернокислотного производства //Известия вузов. Цветная металлургия, 2004, № 1, С. 11-15.
38. Набойченко С.С., Карелов С.В., Мамяченков С.В., Кирпиков А.С. Исследование электролитического рафинирования свинцово-оловянных сплавов во фтористоводородных электролитах // Цветные металлы. 2004. № 4. С. 41-46.
39. Мамяченков С.В., Анисимова О.С., Орлов Е.Г., Кирпиков А.С., Хилай В.В. Переработка мышьяксодержащих растворов отделения мокрой очистки газов сернокислотного производства // Известия вузов, Цветная металлургия, 2004. № 1. С. 11-15.
40. Karelov S.V., Mamyachenkov S.V., Anisimova O.S., Khilay V.V., Kirpikov A.S. Experimental-Industrial Tests of Zink-Sulfate Solutions Electrocementing Treatment Technology // Non-Ferrous Metals. 2004. № 2. P. 13-16.
41. Нурмагамбетова А.М., Малышев В.П., Мамяченков С.В. Энергетические аспекты распределения Больцмана // Вестник УГТУ-УПИ, 2004, №5(35), С. 215-218.