Тема Основные категории, понятия и показатели качества
Вид материала | Закон |
- Наименование и краткое содержание лекций №№ п/п Тема лекции, краткая аннотация Кол-во, 44.79kb.
- Темы и краткое содержание Тема Молодежь как половозрастная группа и ее основные характеристики, 145.8kb.
- 1 Основные понятия и показатели теории надежности, 163.45kb.
- Тема: Основные понятия и определения, 164.71kb.
- Тема: Основные понятия и определения, 121.92kb.
- План урока: Орг момент. Повторение изученного. Объявление темы. Изучение нового материала., 66.27kb.
- Сущность, показатели и основные методы управления качеством продукции, 45.54kb.
- Вопросы для подготовки к экзамену по дисциплине «Инновационный менеджмент», 40.57kb.
- 1. Понятия качества и конкурентоспособности, 901.75kb.
- Конспект лекций Раздел Культура речи: аспекты и критерии Тема, 430.83kb.
Тема 1. Основные категории, понятия и показатели качества.
1. Роль качества продукции в рыночной экономике
Повышение качества продукции – объективная закономерность развития предприятия
Проблема повышения качества продукции актуальна для любого предприятия, особенно на современном этапе, когда в повышении производства все большее значение играет фактор «качество продукции», обеспечивающий ее конкурентоспособность. Проблема качества зародилась и проявилась с развитием общественного производства. На первых порах промышленной революции предметы труда создавались отдельными лицами или небольшими группами людей, которые знали запросы немногочисленных потребителей. С развитием промышленного производства и разделения труда перечень работ возрос настолько, что рабочий потерял из виду конечный продукт труда. В результате резко возросла проблема качества.
Можно отметить следующие аспекты качества.
Национальный аспект. Он проявляется присущим той или иной нации образом мышления в области качества. Так, если американский практицизм ориентирует фирмы на управление качеством с целевой функцией максимальной прибыли, то для японских фирм характерны установки на увеличение доли фирмы на рынке, даже если это будет связано с первоначальными потерями части возможной прибыли.
Политический аспект. Поскольку качество определяет конкурентоспособность фирм, и, в конечном счете, стран, оно, естественно, влияет на уровень доходов населения, уровень безработицы и, следовательно, на политическую ситуацию внутри страны, на международный политический статус государств.
Технический аспект. Уровень развития техники и качество создаваемых человеком объектов – взаимосвязанные характеристики. С одной стороны, научно-технический прогресс, приводящий к совершенствованию техники, создает мощную основу для совершенствования качества продуктов. С другой стороны, более высокого качества продукция, услуги, системы информационных и транспортных коммуникаций и других компонентов качества жизнедеятельности создают лучшие предпосылки для ускорения научно-технического прогресса.
Социальный аспект. Данный аспект также следует рассматривать с двух позиций. Высокое качество как компонент потребностей, повышая уровень образованности, интеллектуального развития, благосостояния нации, разумеется, влияет на социальную среду, социальный статус государства. Как правило, понятие «развитая страна» отождествляется с ее возможностями производить конкурентоспособную продукцию и высоким среднестатистическим уровнем нации. В то же время социальный уровень человека влияет на качество его труда. Уровень культуры производителей – это показатель их потенциальных возможностей в области качества. Можно утверждать, что высококачественные продукты человеческого труда есть творения высокой культуры. Неспроста японцы считают, что высококачественный продукт, созданный трудом человека, своего рода произведение искусства.
Экономический аспект. Качество напрямую связано с экономикой. Повысить качество – это значит, из того же количества сырья и материалов сделать большее количество продукции. Практически все решения в области качества, программы повышения качества, мероприятия по управлению качеством связаны с экономическими затратами и имеют смысл, если приводят к приемлемому для предприятия экономическому эффекту. Поэтому качество должно рассматриваться, прежде всего, как экономическая категория.
Моральный аспект. Американский ученый Джозеф М. Джуран считает, что любое предприятие включает в себя два: первое – полезное, которое выпускает качественную продукцию, приобретаемую потребителями, и второе – впустую расходующее все виды ресурсов и выпускающее брак («второй завод Джурана»). Если учесть, что некачественный труд приводит к излишним затратам ресурсов, энергии, к неудовлетворенности и материальным потерям клиентов, то можно сделать вывод о том, что такой труд аморален.
Рассмотренные аспекты качества показывают сложность проблемы управления качеством и важность их решения в комплексе.
Эффект от повышения качества продукции
Для изготовителей продукции:
- Лучше используются ресурсы
- Сокращаются потери от брака и рекламаций
- Увеличиваются доходы от реализации продукции повышенного качества
- Увеличиваются фонды экономического стимулирования за счет роста прибыли
- Моральное удовлетворение коллектива предприятия.
Для потребителей продукции:
- Спрос удовлетворяется меньшим количеством изделий повышенного качества
- Расширяется и обновляется ассортимент изделий
- Сокращаются затраты в процессе эксплуатации продукции
- Создаются более благоприятные условия труда в сфере потребления
- Более полно удовлетворяются потребности населения
- Для государства:
- Расширяются экспортные возможности и валютные потребления
- Увеличивается народно-хозяйственный эффект на единицу затрат
- Ускоряется НТП в промышленности
2. Основные категории и понятия.
В среде специалистов существует большое число определений качества. Понятие качества развивалось исторически.
- Аристотель (Ш в. до н. э.): Различие между предметами; дифференциация по признаку «хороший – плохой»;
- Гегель (XIX в. н. э.): Качество есть в первую очередь тождественная с бытием определенность, так что нечто перестает быть тем, что оно есть, когда оно теряет свое качество;
- Уолтер Шухарт (1931 год): качество имеет два аспекта: объективные физические характеристики и субъективную сторону (насколько вещь хороша);
- Каору Исикава (1950 год): Качество – свойство, реально удовлетворяющее потребителей;
- Дж. Джуран (1979 год): Пригодность для использования (соответствие назначению). Субъективная сторона – степень удовлетворения потребителя;
- ГОСТ 15467 – 79: Качество продукции – совокупность свойств продукции, обуславливающих ее способность удовлетворять определенные потребности в соответствии с ее назначением;
- Международный стандарт ИСО-8402-94: Качество продукции – совокупность свойств и характеристик объекта, относящихся к его способности удовлетворять обусловленные или предполагаемые потребности.
Под свойством продукции понимается ее объективная особенность, проявляющаяся при производстве, эксплуатации или потреблении.
Различают производственные и потребительские свойства продукции. К производственным свойствам относится вся совокупность свойств, создаваемых в процессе производства. Она представляет собой потенциальное качество.
Потребительские свойства продукции характеризуют лишь ту совокупность показателей, которая относится к числу наиболее важных и значимых для потребителя. Это реальное качество продукции.
Количественная характеристика свойств называется показателем качества продукции.
№ | Признак классификации | Типы показателей |
1 | Отношение к свойствам продукции | 1.1 Назначения 1.2 Надежности 1.3. Технологичности 1.4 Эргономические 1.5. Эстетические 1.6. Стандартизации 1.7. Патентно-правовые 1.8. Экономические |
2 | Количество отражаемых свойств | 2.1 Единичные 2.2 Комплексные 2.3. Интегральные |
3 | Метод определения | 3.1 Инструментальные 3.2 Расчетные 3.3 Статистические 3.4 Органолептические 3.5 Экспертные 3.6 Социологические 3.7 Комбинированные |
4 | Стадия определения | 4.1 Проектные 4.2 Производственные 4.3 Эксплуатационные 4.4 Прогнозируемые |
5 | Размерность отражаемых величин | 5.1 Абсолютные 5.2. Приведенные 5.3 Безразмерные |
6. | Значимость при оценке качества | 6.1 Основные 6.2 Дополнительные |
В практической деятельности термин «объект» обычно заменяется термином «продукция».
Продукция представляет собой результат процесса (процессов) или какой-либо деятельности. Она может быть материальной (товары) и нематериальной (услуги).
Обеспечение качества – планируемые и систематически выполняемые организацией-производителем действия, создающие уверенность в том, что качество продукции будет соответствовать предъявляемым требованиям.
Сертификация – процедура, дающая письменную гарантию соответствия продукции установленным требованиям (стандартам).
3. Основные показатели качества
По количеству характеризуемых свойств все показатели качества делятся на единичные, комплексные, определяющие и интегральные.
Единичные показатели качества характеризуют одно свойство продукции (например, скорость, потребляемая мощность и др.)
Комплексные показатели качества характеризуют совокупность нескольких свойств продукции (например, надежность: безотказность, долговечность, ремонтопригодность, сохраняемость).
Таблица 1.1
Интегральные показатели качества – выражаются через соответствующую сумму экономических и технических показателей (например, общий полезный эффект от эксплуатации продукции, общие затраты на создание и эксплуатацию изделия и др.).
Разновидностью комплексного показателя качества является интегральный показатель качества. Это комплексный показатель качества, отражающий отношение полезного суммарного эффекта от использования объекта по назначению (П) к затратам на создание (Зс) и затраты на эксплуатацию (Зэ).
П
И = --------------
Зс + Зэ
Показатели качества весьма разнообразны, поэтому для каждого вида продукции должна быть выбрана соответствующая номенклатура показателей, наиболее полно характеризующая ее качество.
Примером комплексного показателя качества может служить коэффициент готовности, который позволяет одновременно характеризовать и безотказность, и ремонтопригодность изделия. Он определяется по формуле:
Т
Кг = -----------,
Т + Тв
где Т – средняя наработка на отказ;
Тв – среднее время восстановления.
Пример: Пусть циклы работы изделия распределены во времени, как показано на рисунке.






Рис. 1.2. Циклы работы изделия
При этом: Т1 = 10 ч, Т2 = 12 ч, Т3 = 20 ч – периоды использования изделия по назначению, а Тв1 = 1 ч, Тв2 = 2 ч, Тв3 = 3 ч – периоды восстановления его работоспособности. Тогда:
Т1 + Т2 + Т3 42
Средняя наработка на отказ: Т = --------------------- = ------ = 14 ч;
3 3
Тв1 + Тв2 + Тв3 6
Среднее время восстановления: Тв = -------------------- = ---- = 2 ч;
3 3
следовательно, 14
Кг = ---------- = 0,875
14 + 2
Комплексный показатель Кг = это вероятность готовности изделия в нужный момент.
4. Комплексная оценка уровня качества объекта
Уровень качества объекта – это мера соответствия качества оцениваемого объекта качеству базового объекта.
Базовый показатель качества – показатель качества объекта, принятого за эталон при сравнительных оценках качества.
1. Определение цели оценки.
Целью оценки уровня качества может быть аттестация, оптимизация, техническое задание, решение о покупке и т.д.
2. Выбор номенклатуры единичных показателей качества.
3. Определение значений единичных показателей качества базового и оцениваемого объекта.
За базовые значения единичных показателей качества могут быть приняты показатели, представляющие национальный или мировой уровень качества.
4. Определение относительных единичных показателей. Относительный единичный показатель качества определяется по формуле:
Pi
qi = ------ , где:
Piб
qi - относительный единичный показатель качества;
Pi - численное значение i - го единичного показателя качества оцениваемого объекта;
Piб - численное значение i – го показателя качества базового объекта.
5. Определение весовых коэффициентов.
Различные свойства объекта по-разному влияют на его качество в целом. Например, точность хода часов, значительно важнее с точки зрения их качества, чем чистота полировки поверхности. Следовательно, и показатели качества, и относительные показатели качества должны учитываться при определении комплексного уровня качества объекта с определенными поправками – так называемыми весовыми коэффициентами аi.
6. Выбор метода свертывания относительных единичных показателей.
Свертывание показателей качества (комплексирование) – их объединение (агрегирование), осуществляемое по тому или иному закону.
Q = f (n, qi, аi),
Где Q – комплексный обобщенный показатель, характеризующий качество продукции;
n – число оцениваемых показателей качества;
qi – относительный i – й показатель качества изделия;
аi – коэффициент весомости i-го единичного показателя качества Pi;
f (...) – применяемая функция.
7. Оценка уровня качества.
После выбора метода свертывания, переходят к вычислениям комплексного показателя уровня качества Q.
8. Принятие решения.
Это заключительный этап, логически вытекающий из цели оценки. Если результат не соответствует техническому заданию, то принимаются меры по проведению дополнительных НИОКР, затем повторная оценка.
Пример. Для оценки технического уровня качества часов используется оценочное число Q, которое вычисляется по формуле:
Q = a1q1 + a2q2 + a3q3, где
q1 – относительный показатель изохронной погрешности P1 (определение точности хода при различной величине завода часов);
q2 – относительный показатель позиционной погрешности Р2 (определение точности хода при различном пространственном положении часов);
q3 – относительный показатель температурной погрешности;
а1, а2, а3 – весовые коэффициенты, определенные экспертным методом и равные 0,12; 0,08 и 0,8 соответственно;
Пусть у оцениваемого изделия: Р1 = 0,12 с/сут.; Р2 = 0,15 с/сут.; Р3 = 0,3 с/сут., а у базового образца: Р1б = 0,18 с/сут.; Р2б = 0,17 с/сут.; Р3б = 0,28 с/сут.
Р1 0,12
Тогда: q1 = -------- = ----------- = 0, 66;
Р1б 0,18
Р2 0,15
q2 = -------- = ----------- = 0, 88;
Р2б 0,17
Р3 0,3
q3 = -------- = ----------- = 1,07.
Р3б 0,28
Определим комплексный показатель, характеризующий технический уровень оцениваемых часов: Q = а1q1 + a2q2 + a3q3 = 0,12 x 0, 66 + 0,08 x 0,88 + 0,8 x 1,07 = 0,08 + 0,07 + 0,9 = 1,05, т.е. технический уровень оцениваемых часов выше технического уровня базового образца.
Обеспечение качества – это совокупность способов, методов и действий, направленных на создание уверенности в том, что продукция или услуга, удовлетворяет опредделенным требованиям к качеству.
Управление качеством – действия, использующие методы и виды деятельности оперативного характера в целях удовлетворения требований к качеству.
Принципы управления качеством: принцип целенаправленности, принцип системности и принцип непрерывности.
Политика в области качества – основные направления, цели и задачи в области качества. .
Тема 2. Основные методы управления качеством
Для наиболее полного представления методов и средств управления качеством применяемые в методической и учебной литературе подходы к систематизации могут быть объединены и дополнены (рис. 1, 2). К средствам управления качеством отнесены орудия, предметы, совокупность приспособлений для осуществления менеджмента качества: оргтехника, банки нормативной документации, средства связи и метрологии и т.д., а также управленческие отношения — отношения субординации и координации.
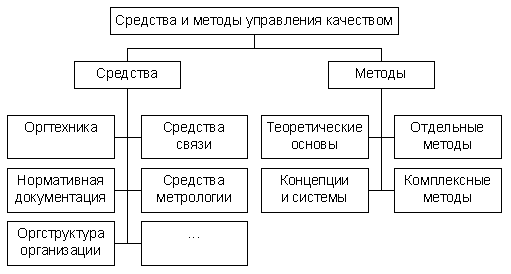
Классификация средств и методов управления качеством
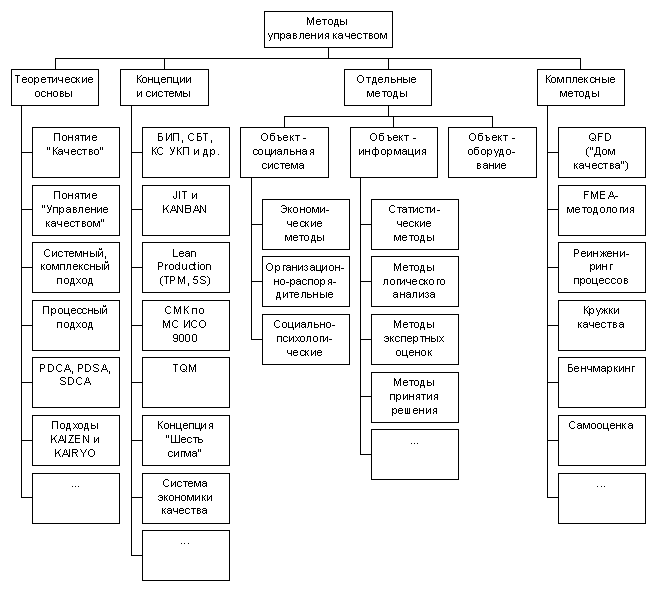
Классификация методов управления качеством
Методы управления качеством — способы и приемы, с помощью которых субъекты (органы) управления воздействуют на организацию и элементы производственного процесса для достижения поставленных целей в области качества. Наряду с отдельными методами выделены представляющие их комбинации комплексные методы, а также теоретические основы, концепции и системы. В отличие от комплексных методов, концепции и системы предполагают не только применение определенного набора методов, но и реформирование подхода к управлению организацией.
Отдельные методы полезно классифицировать по объекту воздействия: информация, социальные системы, оборудование. Последние связаны с особенностями конкретного производственного процесса, включают методы измерений, настройки и др. Управление социальными системами, как правило, подразделяется на экономические, организационно-распорядительные и социально-психологические методы.
Экономические методы управления подразумевают создание экономических условий, побуждающих работников и коллективы предприятий, отделов систематически повышать и обеспечивать необходимый уровень качества. Развитие рыночных отношений требует более широкого использования экономических методов управления качеством. К таким методам могут быть отнесены:
- финансирование деятельности в области управления качеством;
- хозяйственный расчет в подразделениях системы управления качеством;
- экономическое стимулирование производства;
- ценообразование на продукцию и услуги с учетом их уровня качества;
- применение системы оплаты труда и материального поощрения;
- использование экономических мер воздействия на поставщиков;
- бизнес-планирование создания новых и модернизированных видов продукции и услуг.
Организационно-распорядительные методы осуществляются посредством обязательных для исполнения директив, приказов, указаний руководства и других предписаний, направленных на повышение и обеспечение необходимого уровня качества:
- регламентирование (функциональное, должностное, структурное);
- стандартизация;
- нормирование;
- инструктирование (объяснения, разъяснения);
- распорядительное воздействие (на основе приказов, распоряжений, указаний, постановлений и др.).
Социально-психологические методы влияют на социально-психологические процессы, протекающие в трудовых коллективах, для достижения целей в области качества. В области менеджмента качества к ним могут быть отнесены:
- моральное стимулирование высокого качества результатов труда;
- приемы улучшения в коллективе психологического климата (ликвидация конфликтов, подбор и обеспечение психологической совместимости сотрудников);
- учет психологических особенностей членов трудовых коллективов;
- формирование мотивов трудовой деятельности персонала, направленных на достижение требуемого качества;
- сохранение и развитие традиций предприятия по обеспечению необходимого качества;
- способы повышения самодисциплины, ответственности, инициативы и творческой активности каждого члена коллектива.
«Семь основных инструментов контроля качества» гистограмма, стратификация (расслаивание), диаграмма Парето, диаграмма рассеивания (разброса) и контрольные карты предназначены для анализа количественной информации.
1) Лист сбора данных (ЛСД) предназначен для регистрации возникающих событий, т.е. для сбора данных для последующего анализа.
Внешне ЛСД представляет собой таблицу, заполнение которой сводится к простому добавлению в соответствующую ячейку вертикального штриха при наступлении того или иного события. Первые четыре события отмечаются вертикальными штрихами, а каждое пятое - горизонтальной чертой, пересекающей первые четыре штриха. Таким образом, каждая <связка> черточек обозначает 5 событий.
Заполнение листа сбора данных - это наиболее простой из инструментов качества - нет ничего проще, чем поставить штрих в нужной ячейке. Подсчет результатов также осуществляется довольно легко.
На рисунке приведен пример листа сбора данных, в котором регистрировались жалобы покупателей молочной продукции на отдельные виды несоответствий в разные дни недели.
![]() |
Лист сбора данных (ЛСД)
2) Гистограмма - это диаграмма в виде столбцов, на которой графически показано изменение какой-либо величины с учетом частоты распределения.
Например, в таблице 1 приведены данные о росте студентов-юношей в отдельно выбранной студенческой группе.
На основании этих данных можно построить гистограмму, отражающую частоту появления того или иного значения в выборке, а также диапазон рассеивания значений (в данном случае - значений роста юношей).
Таблица 1
Исходные данные для построения гистограммы.
Студент | Рост, см |
1 | 170 |
2 | 163 |
3 | 162 |
4 | 183 |
5 | 173 |
6 | 171 |
7 | 180 |
8 | 172 |
9 | 185 |
10 | 177 |
11 | 179 |
12 | 176 |
13 | 179 |
14 | 172 |
15 | 169 |
16 | 190 |
Для построения гистограммы нужно определить следующие параметры:
Граничные точки.
- В нашем случае граничными точками будут значения 162 и 190 (минимальное и максимальное значения в выборке)
- Количество классов гистограммы, определяется как корень квадратный из объема выборки.
В нашем случае объем выборки равен шестнадцати, т.е. количество классов: sqrt (16) = 4
- Ширина одного класса: расстояние между граничными точками нужно разделить на количество классов.
В нашем случае ширина одного класса вычисляется как (190-162) / 4 =7
Теперь нужно определить границы каждого класса:
1-й класс: 162-168
2-й класс: 169-175
3-й класс: 176-182
4-й класс: 183-190
После того, как мы нанесли <сетку> гистограммы на систему координат, нужно отметить количество событий из нашей выборки, попадающих в тот или иной класс.
![]() |
Гистограмма
На гистограмме видно, насколько часто в нашей выборке встречается то или иное значение.
3) Потоковая диаграмма - графическое отображение последовательности операций в рамках отдельного процесса, с указанием альтернативных путей развития событий в случае выполнения или невыполнения определенных условий.
Фрагмент диаграммы <Прием продукции на склад>.
4) Схема Исикавы (причинно-следственная диаграмма) показанная на рис. 5, позволяет формализовать и структурировать причины возникновения того или иного события, например, - появления несоответствия, а также устанавливать причинно-следственные связи.
Все возможные причины классифицируются по принципу <5М>:
Man (Человек) - причины, связанные с человеческим фактором
- Machines (Машины, оборудование) - причины, связанные с оборудованием
- Materials (Материалы) - причины, связанные с материалами
- Methods (Методы) - причины, связанные с технологией работы, с организацией процессов
- Measurements (Измерения) - причины, связанные с методами измерения.
Исследуемое событие изображается в правой части схемы, символизируя корень древовидной диаграммы, которая строится справа от обозначения события. Горизонтально, от корня диаграммы до левого края листа, наносится центральная ось диаграммы, похожая на ствол дерева. К центральной оси диаграммы К. Исикавы примыкают пять ветвей, каждая из которых соответствует своему классу причин, или своему <М>.
Причинно-следственная диаграмма К. Исикавы
Далее, на каждой ветви отдельно, как на оси, строятся дополнительные <веточки>, каждая из которых представляет отдельную причину в своем классе. К каждой такой <веточке>, в свою очередь, подводятся побеги-причины более высокого уровня, детализирующие ее. Продолжая таким образом, мы получаем разветвленное дерево, связывающее причины наступления того или иного события, находящиеся на разном уровне детализации. Таким образом, мы можем установить причинно-следственную связь между частными отклонениями от нормы (первичными причинами) и их влиянием на вероятность наступления конкретного события.
Для эффективности применения данного метода и достоверности полученных результатов построение диаграммы К. Исикавы должны выполнять профессионалы. Из-за своей структуры диаграмма К. Исикавы также носит название <рыбья кость>.
5) Диаграмма Парето, или ABC-анализ, позволяет выявить основные причины, оказывающие наибольшее влияние на возникновение той или иной ситуации. Принцип Парето гласит, что 20% причин порождает 80% следствий. Другими словами, из всех возможных причин всего лишь 20% являются особенно значимыми, так как они влияют на результаты, которые составляют 80% от всего количества.
Принцип Парето еще носит название <Правило 20-80>. Этот принцип назван так в честь итальянского экономиста Вильфредо Парето, который в конце XIX-го века обратил внимание на тот факт, что 80% итальянского капитала сосредоточено в руках 20% населения Италии. Позднее справедливость этого правила была подтверждена наблюдениями и последующими подсчетами результатов в различных отраслях жизни. Так, устранение 20-ти процентов из общего числа возникающих несоответствий отвлекает на себя 80% от общей суммы затрат на устранение всех возможных несоответствий; для компании-поставщика 20% из общего числа заказчиков формируют 80% прибыли, и так далее. Таким образом, сосредоточив свое воздействие на 20% причин, мы оказываем влияние на 80% последствий. Следующие 30% причин порождают, как ни странно, только 15% следствий и, наконец, оставшиеся 50% влияют всего лишь на 5% следствий (рис. 6). Таким образом, мы можем распределять свое внимание и воздействие, исходя из значимости и эффективности результатов.
Например, если взять произвольный текст и посчитать, сколько раз в нем встречается каждая буква, то с большой долей вероятности окажется, что буквы, составляющие 20% алфавита, образуют около 80% всего текста.
Диаграмма В. Парето
6) Диаграмма корреляции (диаграмма рассеивания) - графическое отображение отношения между переменными величинами, связанными между собой. Слово «корреляция» (correlation) означает соотношение, соответствие. Связь, проявляющаяся при большом числе наблюдений в виде определенной зависимости между средним значением результативного признака и признаками-факторами, называется корреляционной.
Диаграмма корреляции призвана обнаружить принцип, по которому изменяется условно зависимая переменная величина при изменении значения независимой переменной. Например, на рисунке показано, как изменяется объем продажи газированных напитков при изменении погодных условий. Налицо сильная положительная корреляция.
Диаграмма рассеивания
Коэффициент Фехнера (коэффициент корреляции знаков) – простейший показатель тесноты связи. Он основан на сравнении поведения отклонения индивидуальных значений каждого признака (X и Y) от своей средней величины. При этом во внимание принимаются не величины отклонений (Xi – X) и (Yi – Y), а их знаки («+» или «-»). Определив знаки отклонения от средней величины в каждом ряду, рассматривают все пары знаков и подсчитывают число их совпадений и несовпадений. Если совпадение знаков обозначить символом C, а несовпадений – H, то коэффициент Фехнера можно записать как отношение разности чисел пар совпадений и несовпадений знаков к их сумме, т.е. к общему числу наблюдаемых единиц:
∑C - ∑H
K ф = ------------- ,
∑C + ∑H
Очевидно, что если знаки всех отклонений по каждому признаку совпадут, то ∑H = 0 и тогда K ф = 1. Это характеризует наличие прямой связи. Если все знаки не совпадут, то ∑C = 0 и тогда K ф = - 1 (обратная связь). Если же ∑C = ∑H, то K ф = 0, связь отсутствует. Итак, как и любой показатель тесноты связи, коэффициент Фехнера может принимать значения от 0 до ± 1. При этом, чем ближе значение к 1, тем больше (сильнее) теснота зависимости между X и Y. Для приведенного примера K ф = 0,8.
Параллельное рассмотрение X и Y у n единиц
Для этого единицы наблюдения располагают по возрастанию значений факторного признака X и затем сравнивают с ним поведение значений результативного признака Y.
Месяц | Объем выпуска продукции Xi | Стоимость нереализованной продукции Yi | Знаки отклонений от средней величины | |
Xi – Xср | Yi – Yср | |||
1 2 3 4 5 6 7 8 9 10 | 12 16 25 38 43 55 60 80 91 100 | 28 40 38 65 80 101 95 125 183 245 | - - - - - + + + + + | - - - - - + - + + + |
∑ | 520 | 1000 | | |
7) Контрольные карты Шухарта
В процессе статистического регулирования технологического процесса периодически проверяют небольшое количество изготовляемой продукции на конкретной операции, рассчитывают статистический параметр качества и сопоставляют его с номинальным значением, что дает возможность своевременно сигнализировать об отклонении и тем самым предупреждать возникновение дефектов и брака, обеспечивая заданный уровень качества продукции. Для реализации процесса статистического регулирования по одному показателю качества используют контрольные карты Шухарта. В верхней части карты отмечаются точками значения средних арифметических показателей качества х. Здесь нанесены четыре границы: две внешние, ограничивающие поле допуска – Тв (верхний технический допуск) и Тн (нижний технический допуск), за пределами которых находится зона брака, и две внутренние – Рв (верхний предупредительный допуск) и Рн (нижний предупредительный допуск), между которыми находится номинальный размер контролируемого параметра Рном.
Предупредительные границы Рв и Рн устанавливаются таким образом, чтобы выход тех или иных значений за предел этих границ под влиянием погрешностей, нарушающих нормальный ход процесса, еще не означал появления брака, а лишь сигнализировал о возможности его возникновения, если эти погрешности не будут немедленно устранены.
Технологический процесс протекает удовлетворительно, если средние арифметические значения х выборок не выходят за границы регулирования Рв и Рн, а размахи R не выходят за свою границу Тв.R. В этом случае вся партия, произведенная между текущей выборкой и предыдущей выборкой, считается годной и убирается с рабочего места. Если же в выборке обнаружен брак или статистический анализ показывает на возможность его появления при данном состоянии технологического процесса, вся накопившаяся у станка за последний период времени продукция подлежит разбраковке, а станок останавливается для переналадки.
![]() |
Контрольная карта У. Шухарта
«Семь новых инструментов управления качеством» преимущественно работают с логическими и ассоциативными связями, систематизацией факторов и направлений решения проблем. Это диаграммы сродства и связей, диаграммы древовидная, матричная, стрелочная и диаграмма процесса осуществления программы.
Диаграмма сродства - инструмент, позволяющий выявлять основные нарушения процесса путем обобщения и анализа близких устных данных.
- Диаграмма связей - инструмент, позволяющий выявлять логические связи между основной идеей, проблемой и различными факторами влияния.
- Диаграмма дерева - инструмент стимулирования процесса творческого мышления, способствующий систематическому поиску наиболее подходящих и эффективных средств решения проблем.
- Матричная диаграмма - инструмент, позволяющий выявлять важность различных неочевидных (скрытых) связей. Обычно используются двумерные матрицы в виде таблиц со строками и столбцами a1, a2,., b1, b2. - компоненты исследуемых объектов.
- Матрица приоритетов - инструмент, для обработки большого количества числовых данных, полученных при построении матричных диаграмм, с целью выявления приоритетных данных. Этот анализ часто рассматривается как факультативный.
- Блок-схема процесса принятия решения - это инструмент, который помогает запустить механизм непрерывного планирования. Его использование способствует уменьшению риска практически в любом деле. Планирует каждый мыслимый случай, который может произойти, перемещаясь от утверждения проблемы до возможных решений.
- Стрелочная диаграмма - инструмент, позволяющий планировать оптимальные сроки выполнения всех необходимых работ для реализации поставленной цели и эффективно их контролировать.
Тема 3. Комплексный подход к повышению качества продукции
Применение методов управления качеством для снижения потерь фирмы от брака и уменьшения себестоимости продукции.
Цель достигается в несколько этапов:
1. Сбор информации о потерях фирмы, связанных с отклонениями качества на стадии эксплуатации от возврата продукции, брака на стадии производства из-за отклонений качества за определенный период. Указанные данные берутся в службе сервиса (потери на бесплатный гарантийный ремонт и замену продукции), в службе технического контроля качества (потери на брак в производстве), в службе управления качеством (потери от рекламаций, судебных исков и претензий потребителей) и т.д. Итоговые результаты формируются в таблицу (№ отклонения, вид дефекта, сумма потерь от данного дефекта) и ранжируются по степени убывания величины потерь.
2. Построение столбчатого графика. По оси абсцисс откладываются виды брака, а по оси ординат – финансовые потери. При этом слева направо откладываются виды отклонений от качества соответственно уменьшению финансовых потерь от них.
3. Построение диаграммы Парето, каждое следующее значение ординаты равно сумме значений предыдущих ординат.
4. Анализ АВС. Определение группы дефектов А, приводящих примерно к 80% потерь, и группы С – группу самых малозначительных потерь, составляющих примерно 10% от общих потерь.
5. Анализ причин, приводящих к главному виду брака. Построение причинно-следственной диаграммы К. Исикавы.
На диаграмме Исикавы представляются все возможные причинные факторы, которые могут привести к главному виду брака.
6. Проведение корреляционного анализа связи между случайными величинами – каждым выявленным причинным фактором и анализируемым следствием (главным видом брака). При этом могут быть установлены несколько возможных причин появления главного вида брака.
7. Для выявления основного фактора из нескольких установленных, вновь строится диаграмма Парето.
8. Исследование основной причины появления главного дефекта (Например, низкого качества комплектующего изделия).
9. Разработка и реализация специальной программы качества, включающего следующие возможные элементы:
- пересмотр контракта с поставщиком данного комплектующего изделия;
- ужесточение требований к разбросу параметров в стандарте на данное комплектующее изделие;
- внедрение у поставщика автоматической установки контроля качества данного комплектующего.
10. После проведения в жизнь данной программы качества, вновь (за такой же период, как и при исходном анализе, по указанным выше каналам) собираются статистические данные о финансовых потерях фирмы, связанных с качеством и проводится сравнение финансовых потерь за предыдущий и последующий периоды по формуле:
∆П = П1 – П2
и определение, на сколько приведенные меры позволили сократить потери, связанные с браком.
Работа по сокращению потерь должна вестись постоянно, циклично, т.е. вновь строятся столбчатый график, диаграмма Парето, диаграмма Исикавы, проводится анализ причинно-следственных связей и т.д. до приемлемого уровня потерь.
Тема 4. Эволюция систем управления качеством
Модель управления качеством А. Фейгенбаума
Развитие систем управления качеством включает несколько этапов.
Первый этап – акцент на техническом контроле конечного продукта.
С. Кольт – идея стандартного качества.
Г. Форд – создал независимую службу контроля.
Ф. Тейлор, А. Файоль, М. Вебер – научная, классическая школы менеджмента, системный подход.
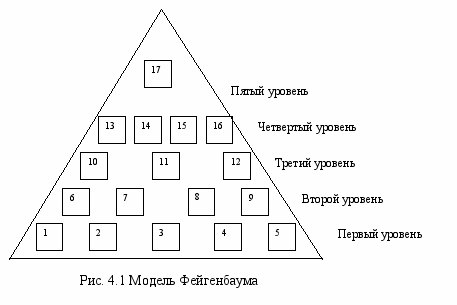
Итог первого этапа развития систем управления качеством может характеризоваться моделью Фейгенбаума.
Первый уровень (подготовка к проектированию)
выбор методов контроля качества
- оценка качества продукции различных поставщиков
- разработка планов приема материалов и оборудования
- контроль измерительных приборов
- предварительная оптимизация на качество
- Второй уровень (проектирование системы обеспечения качества)
- планирование системы обеспечения качества
- испытание прототипов изделий, определение уровня их надежности
- оценка эффективности различных методов контроля
- анализ стоимости затрат на обеспечение качества
- Третий уровень (этап активизации системы)
- разработка технологии контроля качества
- обратная связь и контроль качества
- разработка системы информации о качестве продукции
- Четвертый уровень (этап реализации системы по стадиям)
- контроль новых проектов
- входной контроль материалов и комплектующих проектов
- контроль качества производственных процессов
- анализ и улучшение производственных процессов
- Пятый уровень (конечный)
- комплексный контроль качества
Как видно из рассмотренной модели, ее итогом на первом этапе явился тотальный контроль качества.
Основу концепции обеспечения качества первого этапа можно сформулировать так:
- потребитель должен получать только годные изделия;
- основные усилия должны быть направлены на итоговый контроль качества.
Проблема «Стоимость – эффективность» в управлении качеством
Воплощение в жизнь этой концепции привело к резкому возрастанию затрат на контроль качества (в высокотехнологичных отраслях численность контролеров составила 30 – 40% от численности производственных рабочих), т.е. в рамках этой концепции повышение качества всегда сопровождается ростом затрат на его обеспечение. Иначе говоря, цели повышения эффективности производства и повышения качества изделий вступили в противоречие (смотри рисунок).
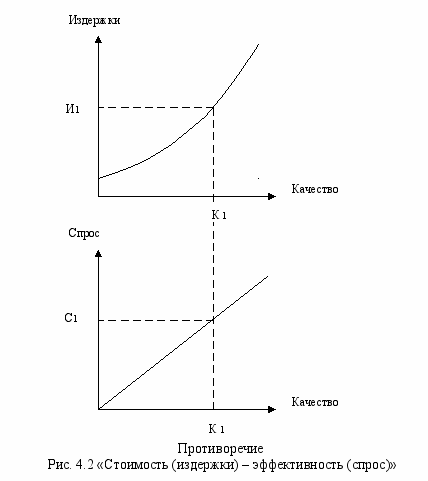
Модель системы управления качеством Эттингера - Ситтига
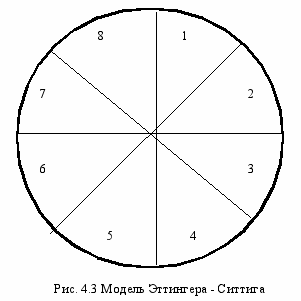
С 20-х годов 20-го века начались попытки если не разрешить, то хотя бы ослабить указанное противоречие первого этапа. В мае 1924 г. сотрудник фирмы «Вестерн Электрик» (США) доктор Шухарт предложил контрольные карты и соответствующие статистические методы, которые позволили сосредоточить усилия не на конечном контроле качества, а на контроле техпроцессов.
В это же время росло понимание того, что каждый производственный процесс имеет определенный процент выхода годных изделий, который определяется всей совокупностью деятельности предприятия, организации труда, управления. Учитывая это обстоятельство, а также усиление конкуренции ведущие предприятия в 50-х годах начали применять концепцию непрерывного управления качеством.
Итог второго этапа развития систем качества может характеризоваться моделью Эттингера – Ситтига, которая графически изображается кругом, разделенным на восемь секторов. В восьми секторах указаны специальные функции управления предприятием (изучение спроса, формулирование целей, конструирование изделий, планирование производственных процессов, производство, распределение, послепродажное обслуживание потребителей, эксплуатация изделий).
Модель системы управления качеством Д. Джурана.
Дальнейшее развитие модели систем управления качеством продукции получили в трудах американского специалиста Д. Джурана.
Его модель представляет собой восходящую спираль, а не замкнутый треугольник или круг. Такая спираль отображает непрерывное формирование и улучшение качества продукции. Модель Джурана включает в себя четырнадцать этапов:
обследование рынка;
- составление проектных заданий;
- проектно-конструкторские работы;
- разработка ТУ на производственные процессы;
- разработка техпроцессов и подготовка производства;
- приобретение сырья, материалов, комплектующих изделий, инструмента и установление связи с поставщиками;
- изготовление инструмента, приспособлений, КИП и А;
- производство изделий;
- технический контроль в процессе производства;
- технический контроль готовых изделий;
- испытание изделий;
- сбыт;
- техобслуживание в процессе использования;
- обследование рынка.
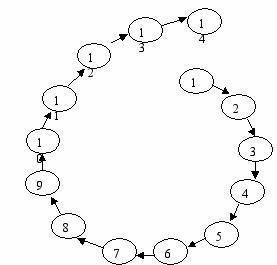
Рис. 4.4 Модель Д. Джурана
14 принципов совершенствования качества Э. Деминга
В 30-е годы в менеджменте возникла «школа человеческих отношений», которая немедленно была воплощена и в управление качеством. Эдвардс Деминг предложил для менеджеров следующие 14 принципов совершенствования качества:
Соблюдайте постоянство целей.
- Примите новую философию: откажитесь от низкого качества во всем.
- Откажитесь от повсеместного контроля.
- Откажитесь от партнерства, основанного только на цене продукции; установите долгосрочные партнерские отношения; уменьшите количество поставщиков.
- Постоянно совершенствуете систему производства и обслуживания.
- Практикуйте в организации наставничество и обучение.
- Внедрите современные методы руководства: функции управления должны смещаться от контроля количественных показателей к качественным.
- Устраните страх: способствуйте тому, чтобы сотрудники высказывались открыто.
- Устраните барьеры между подразделениями и сотрудниками организации.
- Откажитесь от лозунгов, транспарантов и наставлений для рабочих.
- Откажитесь от количественных оценок работы.
- Поддерживайте чувство профессиональной гордости в сотрудниках.
- Внедрите в организации систему образования и самосовершенствования сотрудников.
- Добейтесь приверженности руководства организации приверженности идее качества.
10 составляющих повышение качества Д. Джурана
Д. Джураном были сформулированы 10 составляющих повышения качества:
Формирование осознанной потребности в качественной работе и создание возможностей для улучшения качества.
- Установление целей для постоянного совершенствования деятельности.
- Создание организации, способной эффективно работать над достижением целей, сформировав команды и выбрав координаторов.
- Предоставление возможности обучения всем сотрудникам организации.
- Выполнение проектов для решения проблем.
- Информирование сотрудников организации о достигнутых успехах.
- Выражение признания сотрудникам, внесшим наибольший вклад в улучшение качества.
- Информирование о результатах.
- Регистрация достижений.
- Внедрение и закрепление достижений, которых удалось добиться за год, системы и процессы, постоянно функционирующие в организации.
Многие из перечисленных выше принципов легли в основу современной концепции управления качеством TQM (Total gualiti management).
Роль японских «кружков качества» в повышении качества продукции
Кружки качества - добровольные объединения работников организации различного уровня и разных областей деятельности, собирающиеся в свободное от работы время с целью поиска мероприятий по совершенствованию качества.
Кружки действуют на основе следующих принципов:
- Добровольности участия;
- Регулярности собраний;
- Конкретности решаемых проблем;
- Выявления, изучения и оценки проблем качества в ходе обсуждения.
Кружки качества обеспечили:
- Проведение причинно-следственного анализа
- Укрепление связей между сотрудниками фирмы
- Выявление мероприятий по сокращению затрат
- Самообучение членов кружка
О популярности кружков качества говорят следующие данные: первый кружок был зарегистрирован в 1962 г., к началу 1965 г. в Японии было 3700 кружков, а в настоящее время их насчитывается более 300 тысяч.
Система предложений. Одним из главных способов использования опыта и знаний всех сотрудников является стимулирование внесения ими предложений по усовершенствованию. В наиболее успешных японских компаниях большинство всех сотрудников активно занимается работой по усовершенствованию качества, например через системы предложений. Примером может служить компания Toyota, которая в начале 1950-х годов организовала систему предложений среди своих сотрудников. Первое время система не работала как следует, но в 1970-80-е годы система предложений стала очень продуктивной: если в 1951 году (год начала действия этой системы) было подано 789 предложений, число вовлеченных сотрудников составило 8 %, а число использованных предложений 23 %, то в 1986 году эти показатели приняли следующие значения: 2 648 710, 95 %, 96 %. Основными причинами эффективности этой системы в компании Toyota являются следующие.
1. Каждое предложение получает ответ в течение 2 часов.
2. Лучшие предложения награждаются медалью, деньгами или приемом в «Клуб хороших идей», каждое предложение оплачивается.
3. Управленческий персонал очень серьезно относится ко всем предложениям, и подавляющее большинство из них в той или иной форме используется.
Подсчитали, что в 1986 году японские компании получили около 40 млн предложений от своих работников, в то время как работники компаний США представили на рассмотрение лишь около 1 млн предложений по усовершенствованию.
В некоторых компаниях число поданных на рассмотрение предложений от различных подразделений вывешивается на досках объявлений. Это приводит к соревнованию между различными подразделениями.
«Семь инструментов» японского управления качеством
Сегодня всем хорошо известны «семь инструментов» японского управления качеством:
Вовлечение в процесс обеспечения качества каждого сотрудника фирмы;
- Использование статистических методов контроля качества;
- Создание системы мотивации;
- Поощрение обучения, повышения квалификации;
- Организация кружков качества;
- Создание команд (временных коллективов) из специалистов, заинтересованных в решении конкретной проблемы;
- Превращение проблемы обеспечения качества в общенациональную задачу.
Японская программа повышения качества «пять нулей»
Японская система управления качеством ориентирована на профилактику, предотвращение брака. Большую популярность на японских предприятиях завоевала программа «пяти нулей», суть которой сводится к тому, что работник не должен делать.
Принимать дефектную продукцию с предыдущей операции;
- Создавать условия для появления брака;
- Передавать дефектную продукцию на следующую операцию;
- Вносить изменения в технологию;
- Повторять ошибки.
Японская модель иерархии качества
Японская система управления качеством установила четырехуровневую иерархию качества.
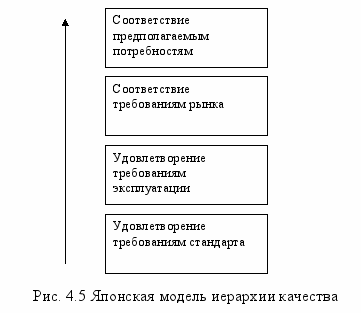
После 1970 г. японский опыт изучается во всем мире. Однако необходимо при этом учитывать национальные особенности и традиции японцев.
Модель системы управления качеством «Петля качества». ИСО 9000.
Положительный опыт ведущих стран мира по управлению качеством нашел отражение в международных стандартах ИСО серии 9000, устанавливающих требования к системам качества, разработанные Международной организацией по стандартизации ИСО