Лекция 17. Свариваемость металлов и сплавов
Вид материала | Лекция |
- Строение и кристаллизация металлов и сплавов лекция 3 Строение металлов и сплавов, 66.78kb.
- «производство отливок из сплавов цветных металлов», 38.25kb.
- Примерная программа дисциплины механические свойства металлов, 122.33kb.
- Литейные свойства металлов и сплавов, 213.86kb.
- Ться с методикой определения электропроводности металлов, экспериментальным и расчетным, 109.79kb.
- Гост 1639-78: лом и отходы цветных металлов и сплавов общие технические условия, 1661.44kb.
- 3 Технические требования, 688.9kb.
- Междунаро дная научно-техническая конференция «Технологии термической и химико-термической, 357.66kb.
- Гост 1639-93 Лом и отходы цветных металл. Общие технические условия, 1007.65kb.
- Жаропрочность платины, палладия и их сплавов, 427.22kb.
Лекция 17. Свариваемость металлов и сплавов
Под свариваемостью понимают способность металлов и сплавов образовывать неразъемные соединения с помощью того или иного метода сварки. Эти соединения не должны иметь трещин, пор, неметаллических включений.
Свариваемость металлов зависит от содержания в металле углерода и легирующих добавок. С увеличением содержания углерода и легирующих элементов в сталях свариваемость их ухудшается.
Для оценки свариваемости применяют различные пробы и испытания. Наиболее распространенными пробами на свариваемость являются:
1. Проба на стойкость металла шва против образования кристаллизационных трещин.
П
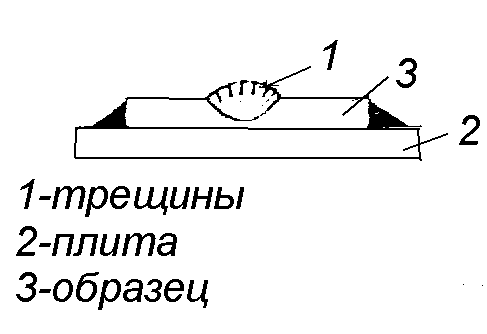
2. Проба на стойкость металла околошовной зоны против образования закалочных структур и трещин.
Для определения свариваемости стали определяют эквивалентное содержание углерода (Сэкв) по формуле

Символы элементов означают их процентное содержание в стали. Если Сэкв будет меньше 0,45, то трещин в околошовной зоне не будет. Если Сэкв будет больше 0,45, то для предупреждения закалки и появления трещин в околошовной зоне следует применить предварительный подогрев металла перед сваркой (
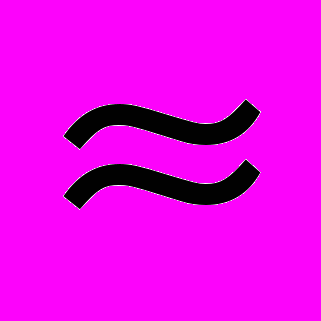
3. Проба на межкристаллитную коррозию (МКК).
Этому испытанию подвергаются нержавеющие и кислотостойкие стали, у которых в результате нагрева в процессе сварки может произойти изменение микроструктуры металла шва, околошовной зоны (выпадение карбидов хрома), что делает их склонными к межкристаллитной коррозии. Чем больше содержание углерода в стали, тем больше вероятность появления межкристаллитной коррозии.
Испытания выполняют путем кипячения сваренных образцов в агрессивной среде:
- метод А – кипячение в растворе серной кислоты или сернокислой меди в течение 24-74 часов;
- метод АМ – то же, но с добавлением медной стружки, кипячение в течение 144 часов.
П
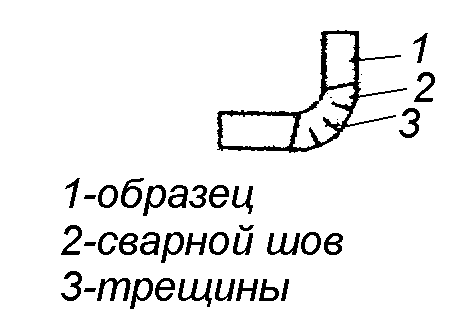
Дефекты сварного шва
При сварке могут образовываться горячие и холодные трещины.
Горячие трещины образуются в сварном шве высоколегированных сталей, алюминиевых и медных сплавов в процессе кристаллизации, когда металл шва находится в твердо-жидком состоянии. Горячие трещины образуются в результате усадочных явлений. Сварной шов при остывании стремится уменьшиться на величину усадки (для стали
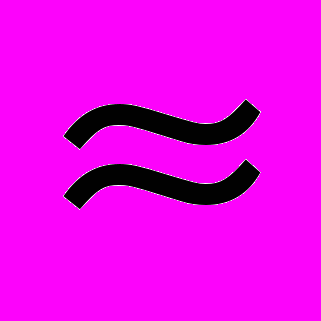
Холодные трещины чаще всего возникают после полного затвердевания металла сварного шва или появляются в металле, охлажденном до комнатной температуры. Причинами их образования являются: склонность к закалке, собственные напряжения в результате усадки, а также структурные превращения в зоне термического влияния. Наиболее часто они располагаются в основном металле в непосредственной близости к сварному шву – в зоне термического влияния. Этот дефект сварки характерен для деталей из высокоуглеродистых и легированных сталей, образующих закалочные структуры в околошовной зоне.
Трещины, возникающие при температуре металла ниже 1200оС условно принято называть «холодными», а выше этой температуры – «горячими».
Помимо трещин к дефектам сварного шва относятся поры. Поры – это заполненные газами полости. Основная причина их возникновения – выделение водорода, азота и окиси углерода, которые интенсивно растворяются в жидком металле шва. При охлаждении шва растворимость газов резко уменьшается и, если их выделение происходит в период затвердевания, пузырьки газа не всегда успевают всплыть и остаются в металле в виде пор. Для борьбы с пористостью следует тщательно очищать свариваемые кромки от загрязнений, ржавчины, а также улучшают защиту металла шва от контакта с окружающей средой. Применяют режимы сварки и специальные приемы, обуславливающие замедление процесса кристаллизации сварочной ванны.
Неметаллические включения: оксидные FeO,SiO2,MnO –снижают ударную вязкость и хладностойкость сталей; сульфидные MnS, FeS и фосфорсодержащие существенно способствуют образованию горячих трещин.
Технологические особенности сварки различных металлов и сплавов
- Сварка углеродистых и низколегированных сталей
Стали с содержанием углерода до 0,25% относятся к низкоуглеродистым. Они хорошо свариваются всеми известными способами сварки. Стали, содержащие углерода 0,25–0,45%, относятся к среднеуглеродистым. Они обладают удовлетворительной свариваемостью. Их сваривают с предварительным подогревом, а после сварки подвергают термообработке – отжигу или нормализации. Стали, которые содержат углерода 0,45–0,75% относятся к высокоуглеродистым. Они плохо свариваются, поэтому их не применяют для сварки.
К низколегированным относятся стали, в которых содержание одного легирующего элемента не превышает 2%, а суммарное содержание всех легирующих элементов менее 2,5–5%.
Так как повышение содержания углерода в сталях ухудшает их свариваемость, то в низколегированных сталях, применяемых в сварных конструкциях, количество углерода ограничивают 0,23%. Этим достигается хорошая или удовлетворительная свариваемость сталей. Влияние легирующих элементов учитывается различным образом, в том числе определением эквивалентного содержания углерода
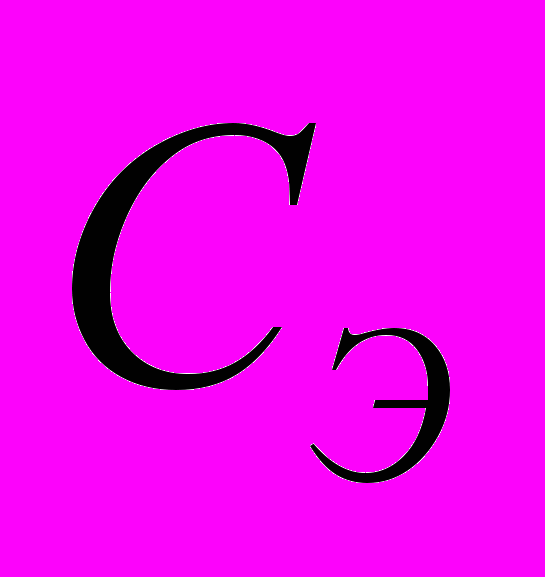
При СЭ >0,45 они имеют повышенную склонность к закалке и образованию холодных трещин в зоне термического влияния. Для предупреждения образования холодных трещин рекомендуется:
- производить подогрев изделий до 100–300оС
- применять многослойную сварку
- перед сваркой производить прокалку электродов до 400–450оС
- производить медленное охлаждение заготовки после сварки
- при контактной сварке применять мягкие режимы (медленный нагрев и медленное остывание)
Для повышения стойкости металла к образованию кристаллизационных трещин, стремятся понизить содержание углерода в металле шва (не более 0,15%). Это достигается применением электродной проволоки с небольшим содержанием углерода. Правда, это несколько снижает прочность металла шва, но компенсируется дополнительным легированием металла шва элементами, повышающими прочность (Сr, Mn, Тi).
Для сварки низколегированных сталей рекомендуется сварка в защитных газах, ручная дуговая, под флюсом, электрошлаковая, контактная.
- Сварка теплоустойчивых сталей (стали типа М, МХ,ХМФ,Х5МФ)
Теплоустойчивые стали используются для изготовления химических аппаратов, работающих при повышенных температурах.
Специфика работы конструкций из теплоустойчивых сталей способствует протеканию диффузионных процессов, приводящих к перераспределению углерода и других легирующих элементов между металлом шва и металлом околошовной зоны. Например, углерод будет диффундировать из основного металла в металл шва, если содержание его в металле шва будет меньше. Это приводит к снижению прочностных свойств сварного соединения.
Поэтому необходимо использовать для сварки такие сварочные материалы, которые позволят получить химический состав металла шва близкий к основному металлу.
Обычно сварку теплоустойчивых сталей производят вручную, короткой дугой, по тщательно очищенной поверхности. Возможны сварка в защитных газах, под флюсом, электрошлаковая, контактная.
Теплоустойчивые стали в процессе сварки склонны к образованию холодных трещин. Поэтому их сварку необходимо вести быстро, без перерывов, не допуская при этом как перегрева, так и чрезмерно быстрого охлаждения. Кроме того, применяют предварительный или сопутствующий подогрев деталей и последующую термическую обработку.
- Сварка среднелегированных сталей
К среднелегированным относят стали, в которых содержание одного легирующего элемента не превышает 2–5%, а суммарное содержание всех элементов 5–10%. Они характеризуются высокими механическими свойствами (предел прочности 600–1200МПа).
Комплексное легирование сталей несколькими элементами, позволяющее получить высокопрочные стали, одновременно затрудняет их сварку. При сварке среднелегированных сталей возможно:
1) образование холодных трещин в металле шва и околошовной зоне вследствие восприимчивости сталей к закалке; жесткого крепления деталей под сварку; выделения атомарного водорода в микропустоты и шлаковые включения в металле шва.
2) образование кристаллизационных трещин.
Для получения качественных сварных соединений применяют технологические приемы:
1. Использование электродных материалов с пониженным содержанием углерода, серы и других элементов, приводящих к образованию в металле шва легкоплавких соединений, способствующих появлению «горячих» трещин.
2. Применение сварочных материалов, исключающих образование в металле шлаковых включений, в которых может скопиться водород.
3. Выполнение сварки на постоянном токе, что позволяет уменьшить содержание водорода в металле шва.
4. Незамедлительная термообработка деталей после сварки.
5.Для предупреждения образования «холодных» трещин необходим предварительный или сопутствующий подогрев (350–450оС).
Сварные соединения из среднелегированных сталей после сварки могут подвергаться полной термообработке, совсем не подвергаться термообработке или подвергаться высокому или низкому отпуску.
Полная термообработка (закалка с последующим отпуском) сваренных деталей производиться в случаях, если химический состав основного металла и металла шва одинаков. Предупреждение появления кристаллизационных трещин производится легированием металла шва алюминием или титаном, способствующими измельчению зерен металла шва.
Если сварные соединения после сварки не будут подвергаться термообработке, то в этом случае появление кристаллизационных трещин устраняется только измельчением зерна металла шва за счет легирования его титаном, алюминием.
Если изделие не подвергается термообработке, то его сварку можно произвести аустенитными электродами (ЭА-1а), но при этом микроструктура металла шва и основного металла будут резко отличаться между собой.
Наконец, сварные соединения из среднелегированных сталей могут подвергаться только высокому или низкому отпуску. Это делается в случае, если изделие, ввиду его крупных габаритов, нельзя подвергнуть полной термической обработке.
Отпуск применяется для снятия остаточных напряжений, устранения закалки шва и околошовной зоны.
Основными методами сварки среднелегированных сталей являются сварка в углекислом газе, аргоне, сварка под флюсом, ручная сварка, электрошлаковая, электронно-лучевая, плазменная.
4.Сварка высоколегированных сталей
К высоколегированным относят стали, содержащие более 10% легирующих элементов. Из этой группы наибольшее распространение имеют нержавеющие хромистые и хромоникелевые стали. Главными легирующими элементами в этих сталях являются хром, никель, углерод (0,02–0,14%С), придающие этим сталям высокую коррозионную стойкость. Для улучшения свойств этих сталей в них дополнительно могут быть введены молибден, тантал, ниобий, марганец, азот.
Значительная литейная усадка, большой коэффициент линейного расширения, а также многокомпонентное легирование, присущее этим сталям, приводят при сварке к возникновению трещин в металле шва и околошовной зоне и межкристаллитной коррозии.
Сварка хромоникелевых сталей (стали типа 12Х18Н9, 17Х18Н9, 04Х18Н10Т, 12Х18Н10Т). Эти стали свариваются всеми способами. При их сварке могут образовываться горячие трещины, поэтому для улучшения свариваемости сталей в шов вводят легирующие добавки для измельчения зерен или создания в шве аустенитно-ферритной структуры. Другой особенностью сварки является то, что при температуре 500–800 оС образуется и выпадает по границам зерен карбид хрома, при этом основной металл у границ зерен обедняется хромом и теряет коррозионную стойкость. В процессе эксплуатации этих сталей может наблюдать межкристаллитная коррозия. Для предупреждения такой коррозии в сварных швах необходимо:
- по возможности уменьшать в этих сталях и сварочной проволоке количество углерода
- применять пониженные значения тока
- вводить в сталь карбидообразующие элементы (титан или ниобий)
- производить отжиг после сварки (выдержка 2–3 часа при 850–900 оС) для выравнивания содержания хрома в местах сварки.
Сварка хромистых сталей ферритного класса может выполняться вручную, автоматами под слоем флюса, а также с помощью электрической сварки в среде защитных газов. Сварка производится на постоянном токе с использованием высоколегированной проволоки и флюсов на основе соединения CaF2. Для предупреждения появления «холодных» трещин, все хромистые стали сваривают с предварительным подогревом (150–450 оС), а после сварки необходим отпуск при 680–780 оС.
При сварке ферритных сталей Х17, Х25 в околошовной зоне наблюдается весьма интенсивный рост зерен металла, не устраняемый никакой термообработкой. И кроме того, в этой же зоне металл подвержен межкристаллитной коррозии.
Отпуск после сварки восстанавливает пластичность сварных соединений и служит средством увеличения коррозионной стойкости металла околошовной зоны.
5. Алюминиевые сплавы.
Основными факторами, затрудняющими сварку алюминия, являются:
-алюминий легко окисляется с образованием тугоплавкого оксида алюминия Al2O3, имеющего температуру плавления 2050оС, что значительно превышает температуру плавления алюминия 658оС. Оксидная пленка препятствует сплавлению кромок, поэтому ее следует перед сваркой удалять и не допускать образования в процессе сварки;
-алюминий в жидком состоянии хорошо растворяет водород. При понижении температуры растворимость водорода в алюминии падает и он выделяется из металла в виде мельчайших пузырьков, что снижает прочность шва и нарушает герметичность соединения;
- при затвердевании алюминий и его сплавы дают большую усадку, вследствие чего вблизи шва могут образоваться трещины;
-большой коэффициент линейного расширения, что вызывает существенные деформации;
-высокая тепло- и электропроводность, приводящие к необходимости увеличения мощности источника энергии для их сварки.
Для улучшения свариваемости алюминия и его сплавов применяют следующие мероприятия:
- перед сваркой кромки изделия и присадочные прутки очищают щеткой от грязи, обезжиривают и подвергают травлению, после чего промывают водой, т.е. ведется тщательная подготовка поверхностей к сварке;
- для удаления оксидной пленки из варочной ванны применяют порошкообразные флюсы или специальные пасты, а также электродные покрытия, в состав которых входят фтористые и хлористые соединения лития, калия, натрия и других элементов. Под действием флюсов Al2O3 переходит в летучий AlCl3, самовозгоняющийся при температуре 183оС.
Алюминий можно сваривать почти всеми рассмотренными способами сварки. Наиболее часто применяют сварку ацетиленокислородным пламене м, автоматическую под слоем флюса, аргоно-дуговую, электрошлаковую, на контактных машинах, электронным лучом в вакууме.