Хранилищ газа и нефти
Вид материала | Методические указания |
СодержаниеМетодические указания Методические указания Вопросы для самоконтроля Методические указания Методические указания |
- Правила создания и эксплуатации подземных хранилищ газа в пористых пластах*1 пб 08-621-03, 484.04kb.
- Разработка технологии и методов регулирования хранения попутного газа в пластах-коллекторах, 402.61kb.
- Правила создания и эксплуатации подземных хранилищ газа в пористых пластах I. Область, 575.4kb.
- Правила создания и эксплуатации подземных хранилищ газа в пористых пластах Настоящим, 537.31kb.
- Положение о научно-образовательном центре «Нефтегазовое дело», 89.57kb.
- История кафедры геологии нефти и газа, 289.6kb.
- Цифровые инженерно-геологические картографические модели планирования подземных хранилищ, 237.94kb.
- Рабочая программа учебной дисциплины ен. Р. 02 Математическое моделирование процессов, 353.5kb.
- Геохимические методы поисков месторождений нефти и газа содержание учебной дисциплины, 74.47kb.
- «Об административной ответственности за правонарушения в сфере использования нефти, 9.48kb.
Студент должен:
з н а т ь: правила эксплуатации сливо-наливных устройств;
уметь: производить отбор проб нефтепродуктов.
Правила технической эксплуатации оборудования систем слива-налива железнодорожных маршрутов и цистерн, нефтеналивных судов. Назначение и отбор проб нефтепродуктов, правила их хранения.
Методические указания
Для проведения операций по сливу и наливу железнодорожных цистерн на нефтебазах оборудуются сливо-наливные эстакады, оборудованные сливо-наливными устройствами, подводящими трубопроводами с коллекторами, насосами и другим оборудованием, позволяющим принимать цистерны всех типов.
Нефтегрузовые операции на эстакадах могут проводиться одновременно с несколькими или одиночными цистернами, причем часто применять закрытый и открытый способы слива и налива цистерн.
К закрытому способу слива и налива нефтепродуктов относится такой способ, который применяют только при полной герметизации технологического оборудования и приборов, соединяющих цистерны с приемораздаточными трубопроводами. При такой системе герметизации исключается возможность контакта струи перекачиваемого нефтепродукта с атмосферным воздухом. Достоинством такого способа является и то, что сокращаются или даже исключаются потери нефтепродуктов от испарения и проливов, а также снижается пожароопасность.
К открытому способу слива и налива цистерн относится способ, при котором отсутствует полная герметизация оборудования и наблюдается разбрызгивание нефтепродукта.
В связи с требованиями противопожарной безопасности слив и налив нефтепродуктов с температурой вспышки до 61°С (т.е. легковоспламеняющиеся нефтепродукты) должен осуществляться закрытым способом. Мазуты, масла и высоковязкие нефтепродукты допускается сливать и наливать открытым способом.
При эксплуатации нефтебазового хозяйства используются, в основном, следующие способы слива и налива нефтепродуктов: слив нефтепродуктов из железнодорожных цистерн через горловину цистерн (верхний слив цистерны); слив нефтепродуктов через нижние сливные приборы (нижний слив); налив нефтепродуктов в ж.д. цистерны через горловины (верхний слив); слив нефтепродуктов из ж.д. цистерн через нижние сливные приборы в желоб или емкость, расположенные непосредственно под рельсами или вдоль них (межрельсовый слив цистерн).
Верхний слив применяется в тех случаях, когда цистерны не оборудованы приборами нижнего слива, или если приборы находятся в неисправном состоянии и их нельзя открывать при наличии нефтепродуктов в цистерне. В связи с этим на всех действующих и вновь строящихся железнодорожных сливо-наливных установках должны быть предусмотрены устройства для обеспечения как нижнего, так и верхнего слива, с учетом того, что в парке действующих железнодорожных цистерн все еще находится значительная часть цистерн, не оборудованных нижними сливными приборами, отвечающими современным требованиям.
Верхний слив нефтепродуктов обладает целым рядом недостатков по сравнению с нижним: часто имеют место значительные потери от испарения; невозможно осуществлять нижний слив; частые срывы насосов при сливе продуктов с высоким значением давления насыщенных паров; применение вакуумных насосов для заполнения всасывающих коммуникаций; применение вакуумных насосов для заполнения всасывающих коммуникаций.
Верхний налив применяется в настоящее время и используется значительно чаще вследствие большей простоты, хотя также обладает большими недостатками (повышенное испарение, пожарная опасность и т.д.)
Существующие способы слива и налива цистерн характеризуются технологическими схемами слива и налива железнодорожных цистерн.
При определении длины рукава учитывают возможные отклонения оси колпака цистерны относительно оси наливного стояка с таким расчетом, чтобы конец рукава доходил до нижней образующей цистерны. В начальный момент, налива наблюдается разбрызгивание нефтепродукта и смешение паров с атмосферным воздухом, а затем прекращается, т. к. струя нефтепродукта находится в затопленном состоянии.
Более совершенной следует считать схему, где показан закрытый прямоточный слив нефтепродуктов в межрельсовый желоб с боковой емкостью или емкостью, расположенной непосредственно под рельсами.
Сливной желоб круглого или прямоугольного сечения делается из листовой стали или железобетона. Желоб обычно укладывают с уклоном ко дну равным 0,005÷0,007 к отводным трубам. Отводные трубы укладываются с уклоном не менее 0,02 к приемным резервуарам и оборудуются гидрозатвором. Нулевой резервуар и желоб, предназначенные для слива нефти и нефтепродуктов, выполняют те же функции, что и обычные резервуары, т.е. прием нефти, ее хранение и последующую откачку. В нулевом резервуаре происходят те же большие и малые дыхания, как во всех наземных резервуарах. Потому все нулевые резервуары оборудуют отводными газо-воздушными трубопроводами, в конце которых устанавливают дыхательную арматуру.
Сливо-наливные операции на эстакадах могут производиться одновременно с несколькими или одиночными цистернами. Количество эстакад n в общем случае определяется в зависимости от числа прибывающих за сутки маршрутов.
Принудительный слив нефтепродуктов может осуществляться, например, с помощью погружных насосов или за счет создания в цистерне избыточного давления. Для осуществления сифонного слива необходимо предварительно заполнить нефтепродуктом сливной стояк. Для этого обычно используются вакуум-насосы, которые при сливе одиночных цистерн устанавливаются прямо на стояке. При маршрутном сливе верхнюю часть стояка подсоединяют к вакуум-коллектору.
При верхнем сливе цистерн центробежными насосами или самотеком установка дополнительно поршневого вакуум-насоса необходима не только для заполнения стояка и всасывающих трубопроводов. Практика показывает, что в процессе слива, когда уровень взлива в цистерне становится низким и сливаемая жидкость не успевает подтекать к приемному рукаву, у его конца образуется воздушная воронка. Воздух из нее прос
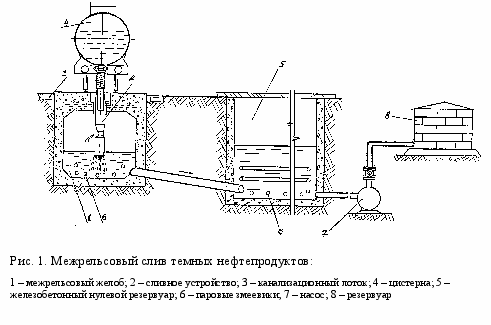
кальзывает во всасывающий трубопровод и в нем образуется воздушная пробка, приводящая к разрыву сплошности потока жидкости и срыву работы насоса. Это означает окончание «газовой» операции и переход на операцию зачистки-удалению остатков груза. Зачистка цистерн наиболее эффективна поршневыми насосами.
Слив под избыточным давлением применяют для сокращения времени слива. При этом способе в котле вагона-цистерны под поверхностью нефтепродукта создают давление, не превышающее 0,05 МПа. Люк колпака цистерны закрывают герметичной специальной крышкой со штуцером для подачи сжатого воздуха. Данный способ слива характеризуется более низким значением потерь нефтепродуктов от испарения.
Вопросы для самоконтроля
- Способы слива-налива нефтепродуктов
- Технологические схемы слива и налива железнодорожных цистерн
- Принудительный слив нефтепродуктов
Тема 2.3 Эксплуатация трубопроводов перекачивающих станций и нефтебаз
Студент должен:
з н а т ь: правила эксплуатации трубопроводов перекачивающих станций и нефтебаз; правила эксплуатации трубопроводов перекачивающих станций (ПС) и нефтебаз.
Методические указания
В период эксплуатации трубопроводов следует осуществлять постоянный контроль за состоянием трубопроводов и их элементов (сварных швов, фланцевых соединений, арматуры), антикоррозионной защиты и изоляции, дренажных устройств, компенсаторов, опорных конструкций и т.д. с записями результатов в эксплуатационном журнале.
При периодическом контроле следует проверять:
техническое состояние трубопроводов наружным осмотром и, при необходимости, неразрушающим контролем в местах повышенного коррозионного и эрозионного износа, нагруженных сечений и т.п..
Трубопроводы, подверженные вибрации, а также фундаменты под опорами и эстакадами для этих трубопроводов в период эксплуатации должны тщательно осматриваться с применением приборного контроля за амплитудой и частотой вибрации. Сроки осмотров в зависимости от конкретных условий и состояния трубопроводов устанавливаются в документации, но не реже одного раза в 3 месяца.
Если при наружном осмотре обнаружены неплотности разъемных соединений, давление в трубопроводе должно быть снижено до атмосферного, температура горячих трубопроводов - до плюс 60°С, а дефекты устранены с соблюдением необходимых мер безопасности.
При обнаружении дефектов, устранение которых связано с огневыми работами, трубопровод должен быть остановлен, подготовлен к проведению ремонтных работ в соответствии с нормативно-технической документацией по промышленной безопасности.
Основным методом контроля за надежной и безопасной эксплуатацией технологических трубопроводов является периодическая ревизия, которая проводится в установленном порядке.
Результаты ревизии служат основанием для оценки состояния трубопровода и возможности его дальнейшей эксплуатации.
Продление сроков службы трубопроводов и его элементов проводится в установленном порядке.
При проведении ревизии внимание следует уделять участкам, работающим в особо сложных условиях, где наиболее вероятен максимальный износ трубопровода вследствие коррозии, эрозии, вибрации и других причин. К таким относятся участки, где изменяется направление потока (колена, тройники, врезки, дренажные устройства, а также участки трубопроводов перед арматурой и после нее) и где возможно скопление влаги, веществ, вызывающих коррозию (тупиковые и временно неработающие участки).
При ревизии трубопроводов с давлением до 10 МПа (100 кгс/см2) следует:
а) провести наружный осмотр трубопровода;
б) измерить толщину стенки трубопровода приборами неразрушающего контроля, а в необходимых случаях - сквозной засверловкой с последующей заваркой отверстия.
Количество участков для проведения толщинометрии и число точек замера для каждого участка определяется в соответствии с документацией и в зависимости от конкретных условий эксплуатации.
Во всех случаях контроль толщины стенки в каждом месте следует производить в 3 - 4 точках по периметру, а на отводах - не менее чем в 4 - 6 точках по выпуклой и вогнутой частям.
Внутренний осмотр участков трубопроводов проводится с помощью ламп, приборов, луп, эндоскопа или других средств.
Внутренняя поверхность должна быть очищена от грязи и отложений, а при необходимости - протравлена. При этом следует выбирать участок, эксплуатируемый в наиболее неблагоприятных условиях (где возможна коррозия и эрозия, гидравлические удары, вибрация, изменение направления потока, застойные зоны). Демонтаж дефектного участка трубопровода при наличии разъемных соединений проводится путем их разборки, а на цельносварном трубопроводе этот участок вырезают.
Во время осмотра проверяют наличие коррозии, трещин, уменьшения толщины стенки труб и деталей трубопроводов;
При необходимости проводится радиографический или ультразвуковой контроль сварных стыков и металлографические и механические испытания;
После проведения ревизии составляются акты, к которым прикладываются все протоколы и заключения о проведенных проверках. Результаты ревизии заносятся в паспорт трубопровода. Акты и остальные документы прикладываются к паспорту.
Периодические испытания трубопроводов на прочность и плотность проводят, как правило, во время проведения ревизии трубопровода.
Сроки проведения испытания для трубопроводов с давлением до 10 МПа (100 кгс/см2) принимается равным удвоенной периодичности проведения ревизии, но не реже одного раза в 8 лет.
Вопросы для самоконтроля
- Организация периодического контроля состояния технологических трубопроводов
- Порядок проведения периодической ревизии технологических трубопроводов
Тема 2.4. Эксплуатация оборудования баз сжиженного газа
Студент должен:
з н а т ь: правила технической эксплуатации баз сжиженного газа (БСГ),
умет ь: выполнять проверочные расчеты оборудования БСГ
Правила технической эксплуатации баз сжиженного газа. Характерные неисправности и их устранение. Проверочные расчеты оборудования БСГ (насосов, компрессоров, ТП).
Методические указания
Сжиженные углеводородные газы поставляются на БСГ в специальных железнодорожных цистернах или по трубопроводам, проложенным от заводов-поставщиков.
Внешние отличительные признаки железнодорожных цистерн для перевозки сжиженных газов: резервуар цистерны окрашен в светло-серый цвет; низ корпуса резервуара цистерны окрашен в черный цвет; вдоль оси резервуара цистерны нанесена красная полоса с надписями «Пропан — бутан», «Огнеопасно».
Железнодорожная цистерна для перевозки сжиженных газов имеет следующую арматуру: два угловых вентиля для слива и налива жидкой фазы газа (окрашены в коричневый цвет с желтыми поперечными по лосами); один угловой вентиль для паровой фазы газа (окрашен в коричневый цвет); сигнальный вентиль для контроля уровня наполнения цистерны (окрашен в красный цвет); г) вентиль контроля максимального наполнения (окрашен в зеленый цвет); д)вентиль контроля опорожнения цистерны; вентиль для слива воды; пружинный предохранительный клапан; узел манометродержателя.
Вся арматура, кроме узла манометродержателя, располагается на крышке люка, закрывающегося защитным колпаком.
Прибывшие на КБ железнодорожные цистерны с сжиженным газом должны быть немедленно приняты, осмотрены и подготовлены к сливу газа.
Операции по подготовке к сливу и слив сжиженного газа должны выполняться только после удаления паровоза (тепловоза) с территории КБ на расстояние не менее 20 м от границы КБ и после окончания маневровых работ по установке железнодорожных цистерн на соответствующие места у сливной эстакады.
Слив сжиженных газов из железнодорожных цистерн в условиях КБ может осуществляться одним из следующих методов: созданием необходимого перепада давления между цистерной и резервуаром путем нагнетания компрессором паров сжиженных газов из наполняемого резервуара в железнодорожную цистерну; перекачиванием сжиженных газов специальными насосами; самотеком, когда наполняемые резервуары расположены ниже железнодорожной цистерны (например, подземные резервуары).
Категорически запрещается создавать перепад давления между цистерной и резервуаром путем выпуска в атмосферу паровой фазы газа из наполняемого резервуара.
Давление паровой фазы, нагнетаемой компрессором в железнодорожную цистерну при сливе, не должно превышать рабочего давления, указанного на табличке цистерны.
При повышении давления в железнодорожной цистерне выше рабочего компрессор должен быть немедленно остановлен.
Во избежание больших потерь сжиженного газа в виде «возврата» следует отсасывать пары из железнодорожных цистерн при их разгрузке до давления 0,5—0,7 кгс/см2.
Следует иметь в виду, что во время отсоса паров из цистерны происходит испарение неслитого сжиженного газа (находящегося ниже уровня сливных труб) и жидкость охлаждается до температуры точки кипения при данном давлении в цистерне, при этом давление падает.
Запрещается подтягивать соединения гибких, шлангов сливо-наливной эстакады, находящихся под давлением, отсоединять шланги разрешается только убедившись, что цистерна отключена и давление в шлангах полностью сброшено.
По окончании слива угловые и контрольные вентили на железнодорожной цистерне должны быть заглушены пробками проверены на герметичность мыльной эмульсией.
Отсоединять цистерну от заземляющего устройства разрешается только по окончании слива (или налива) и установки заглушек на штуцеры вентилей цистерны.
Трубопроводы слива газа из железнодорожных цистерн, имеющие участки из резинотканевых рукавов, должны быть оборудованы обратными, клапанами, установленными в непосредственной близости от рукавов.
Вопросы для самоконтроля
- Способы поставки сжиженного газа на БСГ
- Оборудование цистерн для перевозки сжиженного газа
- Методы слива сжиженного газа из цистерн
- Меры безопасности при производстве сливо-наливных операций
Тема 2.5. Эксплуатация станции подземного хранения газа
Студент д о л ж е н:
з н а т ь: правила эксплуатации оборудования станций подземного хранения газа (СПХГ).
Правила технической эксплуатации оборудования станций подземного хранения газа: компрессорного цеха, установки очистки, осушки газа, промысловой части.
Методические указания
Подземное хранение газа и жидкостей проектируется в естественных пористых и проницаемых коллекторах, а также в непористых и непроницаемых горных породах.
Подземные хранилища газа обеспечивают в основном следующее: покрытие сезонной неравномерности газопотребления, связанной с отопительной нагрузкой в зимнее время; уменьшение капитальных вложений в магистральный газопровод и компрессорные станции; создание условий для ритмичной работы источников газа и сооружений магистральных газопроводов; создание государственных запасов газа (топлива и сырья для химических заводов) в необходимых районах страны; сохранение нефтяного газа в новых нефтедобывающих районах и углеводородного конденсата при .временной невозможности его использования; увеличение коэффициента нефтеотдачи в старых нефтедобывающих районах в случае создания ПХГ в выработанных нефтяных месторождениях.
Общий объем газа в подземном хранилище делится на две части: активный (рабочий) и буферный (остаточный). Активный газ — объем, ежегодно закачиваемый и отбираемый из ПХГ. Буферный газ — объем, который постоянно находится в ПХГ во время его эксплуатации.
Буферный газ предназначен для создания в хранилище определенного давления в конце отбора, при котором обеспечивается необходимый дебит газа, получаемого из хранилища. Чем больше объем буферного газа, тем больше давление в хранилище и дебит отдельных скважин, меньше общее число скважин для отбора газа из хранилища и степень сжатия газа на КС подземного хранилища при подаче его потребителю.
Объем буферного газа в подземном хранилище зависит от глубины залегания ловушки, физико-геологических параметров пласта-коллектора, толщины пласта и угла наклона структуры, режима эксплуатации хранилища, технологического режима эксплуатации скважин и давления газа на головке скважин в конце периода отбора газа.
Объем буферного газа составляет от 60 до 140 % рабочего газа. Затраты на буферный газ и его закачку в ПХГ эквивалентны капитальным вложениям при сооружении ПХГ. Объем буферного газа, число эксплуатационных скважин и мощность КС взаимосвязаны.
Газ, закачиваемый в подземное хранилище, сжимается компрессорами до необходимого давления. В процессе сжатия газ нагревается и загрязняется парами компрессорного масла.
Сконденсированные на забое скважины пары масла обволакивают зерна песка, уменьшают сечение поровых каналов и фазовую проницаемость для закачиваемого газа. Это в свою очередь способствует уменьшению расхода закачиваемого газа и повышению давления нагнетания. Поэтому нагретый газ перед закачкой в скважину охлаждают с целью уменьшения дополнительных температурных напряжений в фонтанной арматуре, обсадной колонне, цементном камне за колонной, избежания отрыва цементного камня от колонны и образования трещин в нем, т. е. для сохранения герметичности скважин.
В процессе хранения газ обогащается парами воды. При отборе с его потоком выносятся взвеси (песчинки, частицы глины, цементного камня и т. д.). Поэтому во многих случаях извлекаемый из хранилища газ очищается от твердых взвесей и осушается от влаги.
К поверхностному оборудованию ПХГ предъявляются следующие требования: 1) обработка отбираемого из ПХ газа до товарных кондиций в течение полного цикла отбора газа и подачи его в магистральный газопровод; 2) использование давления газа для получения товарных кондиций отбираемого газа из хранилища; 3) дистанционное управление и контроль (эксплуатация без участия обслуживающего персонала); 4) отвечать требованиям законов об охране окружающей среды.
Для замера количества газа, закачиваемого и отбираемого из скважин, удаления влаги из газа при отборе, регулирования давления закачки и отбора построены газораспределительные пункты, на которых установлены на открытой площадке сепараторы, отключающая арматура и здания, где находятся регулирующие клапаны и расходомеры для каждой скважины.
Закачка газа. По газопроводу-отводу диаметром 500 мм под давлением 2,5—3,6 МПа газ, предварительно очищенный от взвешенных твердых частиц и капельной влаги в вертикальных масляных пылеуловителях, направляется на прием газомоторных компрессоров типа 10ГК для компримирования в две ступени Затем он поступает на установку очистки от компрессорного масла, где последовательно проходит через четыре ступени очистки- циклонные сепараторы (горячий газ); циклонные сепараторы (охлажденный газ); угольные адсорберы и керамические фильтры.
В сепараторах улавливаются крупные частицы масла (20— 30 мкм), а более мелкие — в угольных адсорберах. Сорбентом служит активированный уголь в форме цилиндриков диаметром 3—4 мм и высотой 8 мм. Насыщенный маслом сорбент регенерируют при помощи пара.
Самая тонкая очистка от мелкодисперсных масляных частиц осуществляется в керамических фильтрах, имеющих определенные коэффициенты проницаемости и пористости. Керамический фильтр состоит из трубок, изготовленных из фильтрующего материала, один конец которых наглухо закрыт. Трубки помещены группами в прочный корпус. Показатель загрязнения трубок — увеличение перепада давления на входе и выходе фильтра свыше 0,027 МПа. Регенерацию фильтрующих трубок осуществляют путем обратной продувки, промывки растворителями твердых и жидких частиц..
Пройдя эти аппараты, охлажденный и очищенный от масла газ поступает по газосборному коллектору на ГРП, где его поток разделяется по скважинам и замеряется количество газа, закачиваемого в каждую скважину.
Отбор газа. При отборе газ из скважин поступает на ГРП по индивидуальным шлейфам. С газом, извлекаемым из хранилища, может выноситься песок даже при очень небольших депрессиях (0,03—0,04 МПа). Для предотвращения выноса песка из пласта в скважину забой ее оборудуют специальными фильтрами или призабойную зону укрепляют вяжущими веществами.
Влага, улавливаемая на ГРП, автоматически сбрасывается в специальные замерные емкости.
Далее по газосборному коллектору газ поступает на установку осушки, откуда при точке росы —2° попадает в магистральный газопровод. Для осушки газа используют диэтилен-гликоль (ДЭГ).
Очистку газа осуществляют в газовых сепараторах, которые устанавливают на открытых площадках.
Вопросы для самоконтроля
- Задачи возлагаемые на подземные хранилища газа
- Понятие о буферном объеме газа
- Подготовка газа перед закачкой в пласт
- Подготовка газа перед закачкой в магистральный газопровод